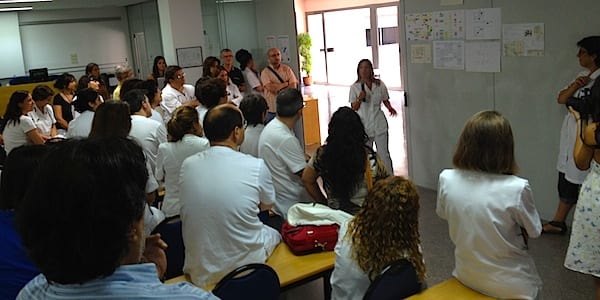
Surviving the economic crisis working with lean healthcare
CASE STUDY - In the past two years, the Consorci Sanitari del Garraf near Barcelona experienced a lean turnaround. The author gives us an overview of the key building blocks of this transformation.
Words: Cristina Fortcuberta Adalid, Instituto Lean Management
Corsorci Sanitari del Garraf has a long tradition of focus on patient care and of good working practices, and there is no doubt this pre-existing culture helped the organization to embrace lean thinking so successfully in the past couple of years.
In both 2012 and 2013, CSG made the Top 20 list of the best-managed hospitals in Spain, and in January it was awarded the Abedis Donabedian recognition for hospital quality excellence. Both are extremely sought-after accolades here in Spain. So how did the organization achieve such great results? To understand this, we can analyze CSG's journey using the Lean Transformation Model as a framework.
Scroll down and you will be able to see an A3 I drew - it will give you an overview of the transformation. Further below there are short explanations of each of the building blocks of a lean transformation as they took shape at Consorci Sanitari del Garraf.
But first, some background information:
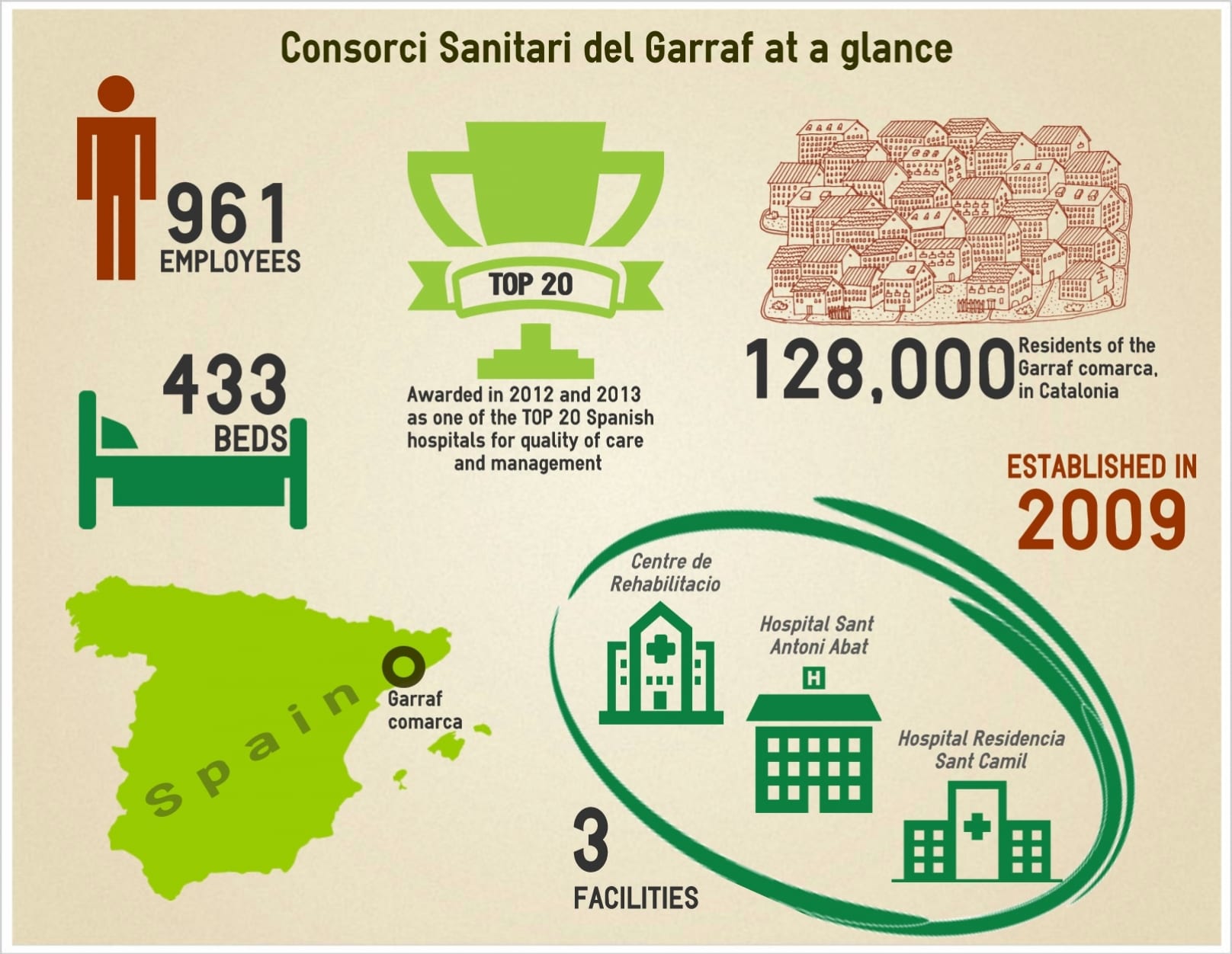
Now that we have made introductions, let's get into the lean transformation. Here's my A3 of the Corsorci's transformation, looked at from the perspective of the Lean Transformation Model (each section is available in a larger format below).
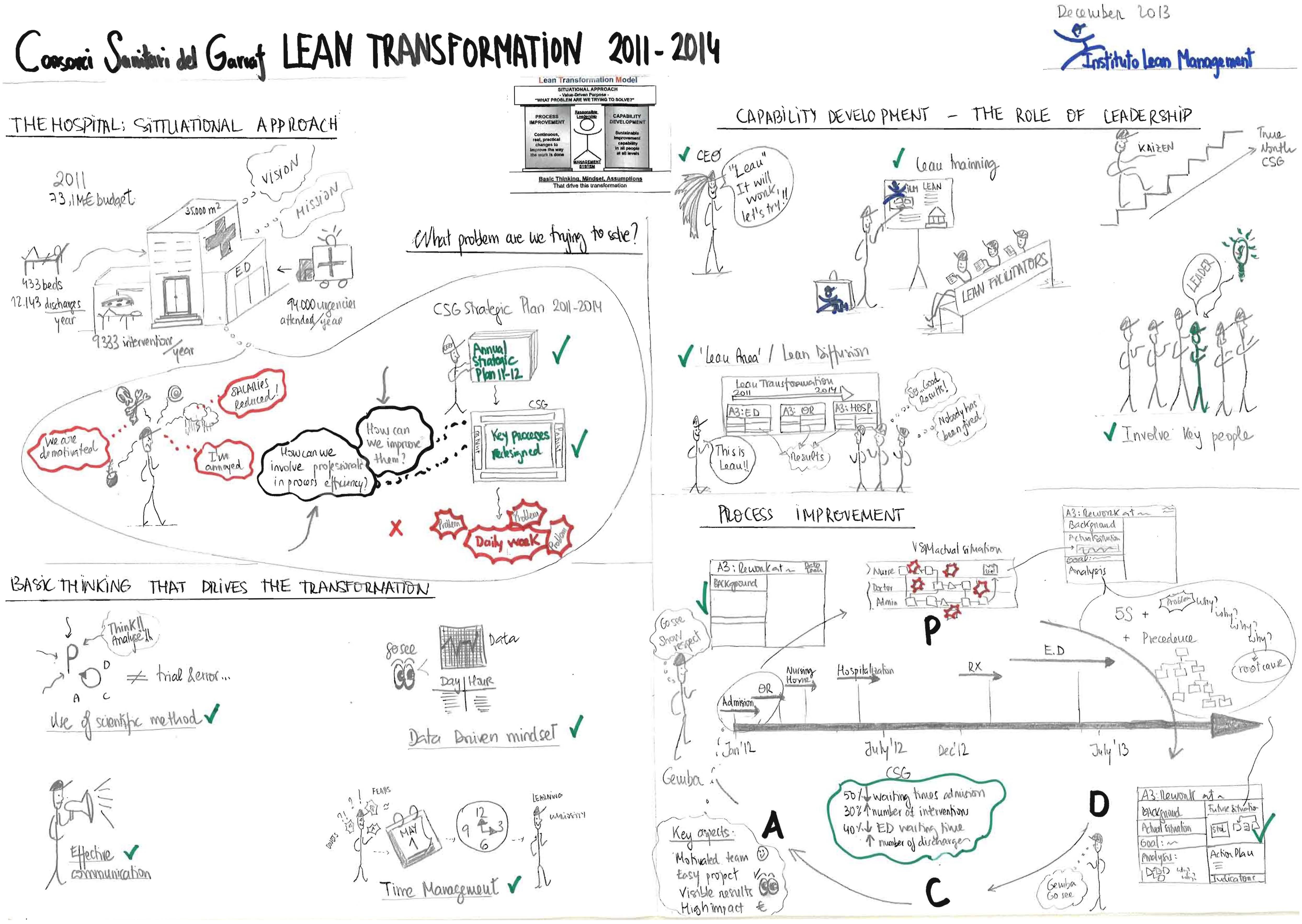
- Situational Approach
- The problem CSG was trying to solve: In mid-2011, the organization had just finishedredesigning the map of its key processes. From that point onwards, it felt it needed to improve them on a daily basis and involve its professionals in process improvement. After reviewing different existing methodologies, it decided lean management was the best option. Why? Mainly, because of its "respect for people" philosophy.
- The challenge: lean was a completely unknown methodology at CSG. Those who had heard of it thought it was only applicable to car manufacturing. Initial resistance was evident.
- The opportunity: earlier in 2011, the CEO had attended a public workshop organized by ILM and was really enthusiastic about it. He was convinced lean could help his organization to improve the delivery of patient care and, at the same time, increase the engagement of professionals.
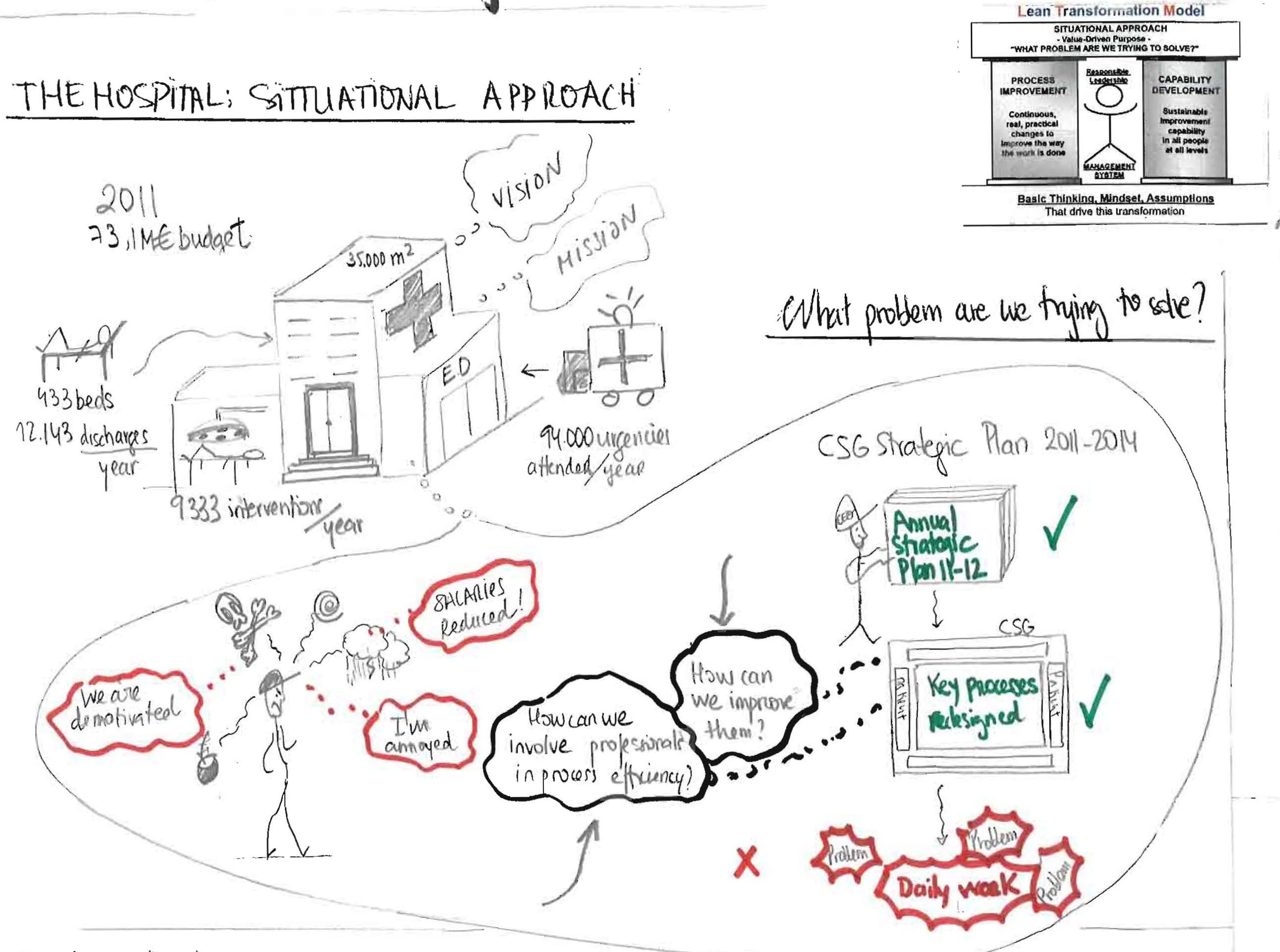
- Basic thinking driving the transformation
The implementation of lean thinking at CSG is based on the following key aspects:
- Effective communication to achieve people involvement.
- Use of the scientific method and PDCA without losing momentum, in order to rapidly increase knowledge.
- Data-driven mindset: any action is based on data extracted from the gemba instead of guessing and perceptions.
- Time management: give people the time to adapt to new situations.
Here's what Lean Manager, Rosa Maria Simón, said: "One of the major objectives for CSG is to transform processes so that they can create value, provide high quality care and give optimal accessibility to our patients. Achieving this while in tough economic times is impossible without the participation of every person involved in the value chain. People are the number one source of value in our organization."
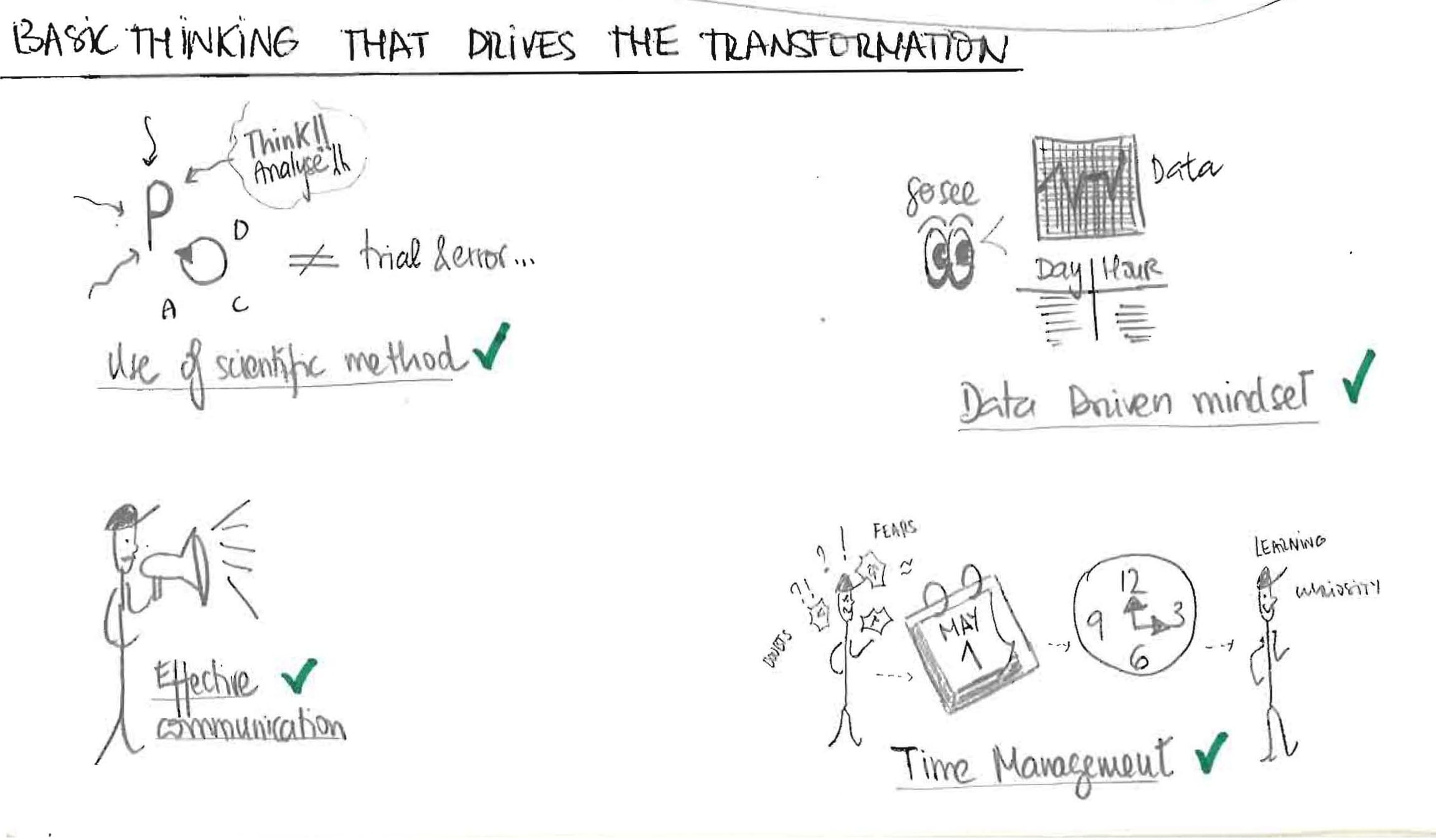
- Capability development & the role of leadership
When you are deploying lean management techniques and principles, developing the capabilities of people is one of the things you can never go without. CSG was aware of this from the very beginning and knew that people development would contribute greatly to overcoming resistance.
- Training a group of people was one of the first things CSG did. Facilitators were asked to participate in a lean workshop that lasted several days. They are a group of 20 people from different management levels in the organization.
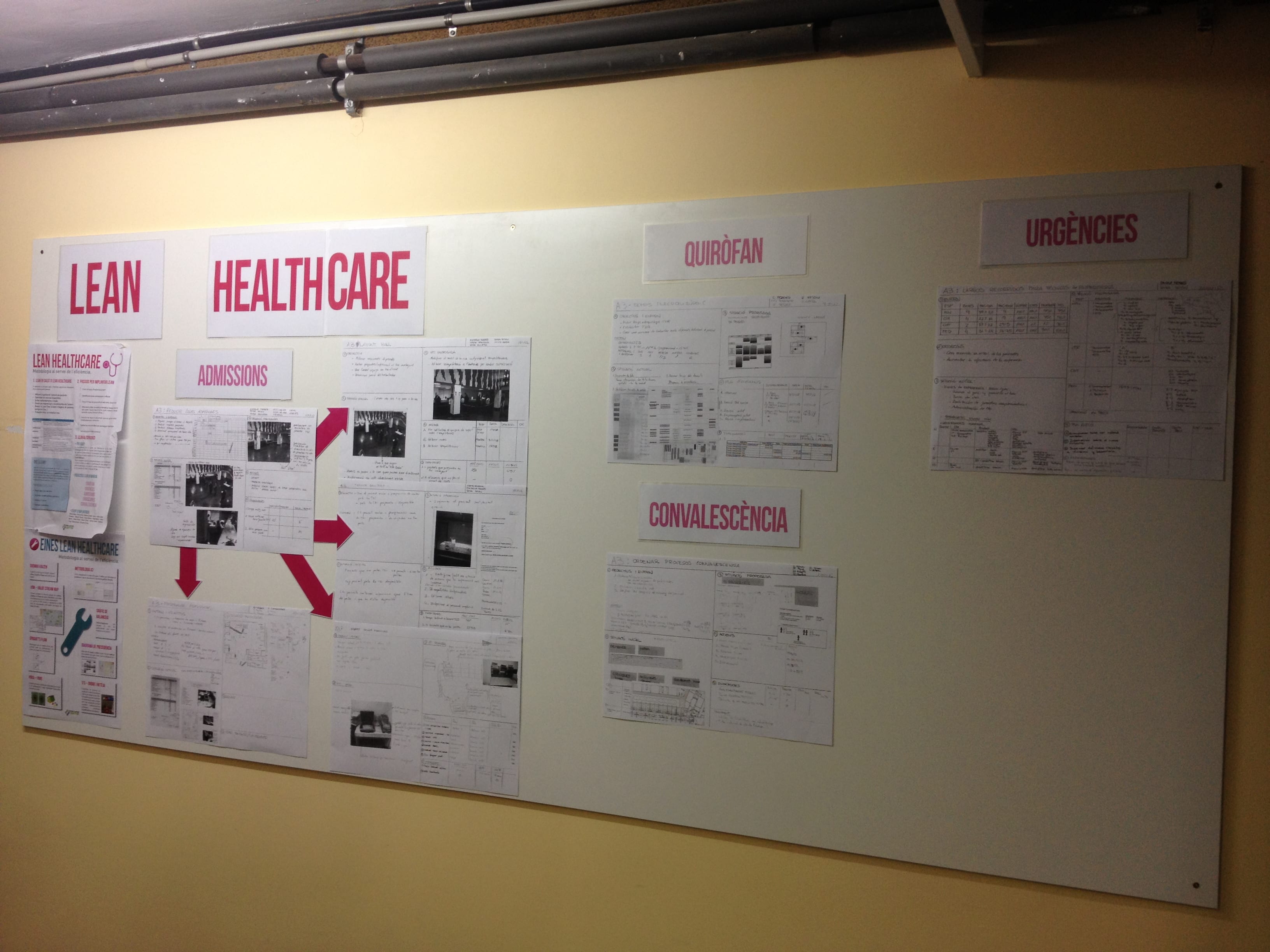
They didn’t necessary have to be the ones who would directly use lean tools, but those who would lead the entire project. After the workshop, the person responsible for training in the entire hospital became the main lean leader, and since then she has participated in every project and acted as a channel between professionals and the management team.
- Working on small, contained projects each time also helped people to rapidly implement improvements (this was “learning by doing”).
- After the implementation of the first three projects, a “lean diffusion” session was organized so that everyone interested (participation was not mandatory) could see with their eyes what was going on, the steps that were being followed and the results that were being achieved. The final goal of this session was keeping people informed.
- Aligned with this last point, a “lean diffusion” area was created. The A3s that were developed were hung to a wall in a busy location within the organization.
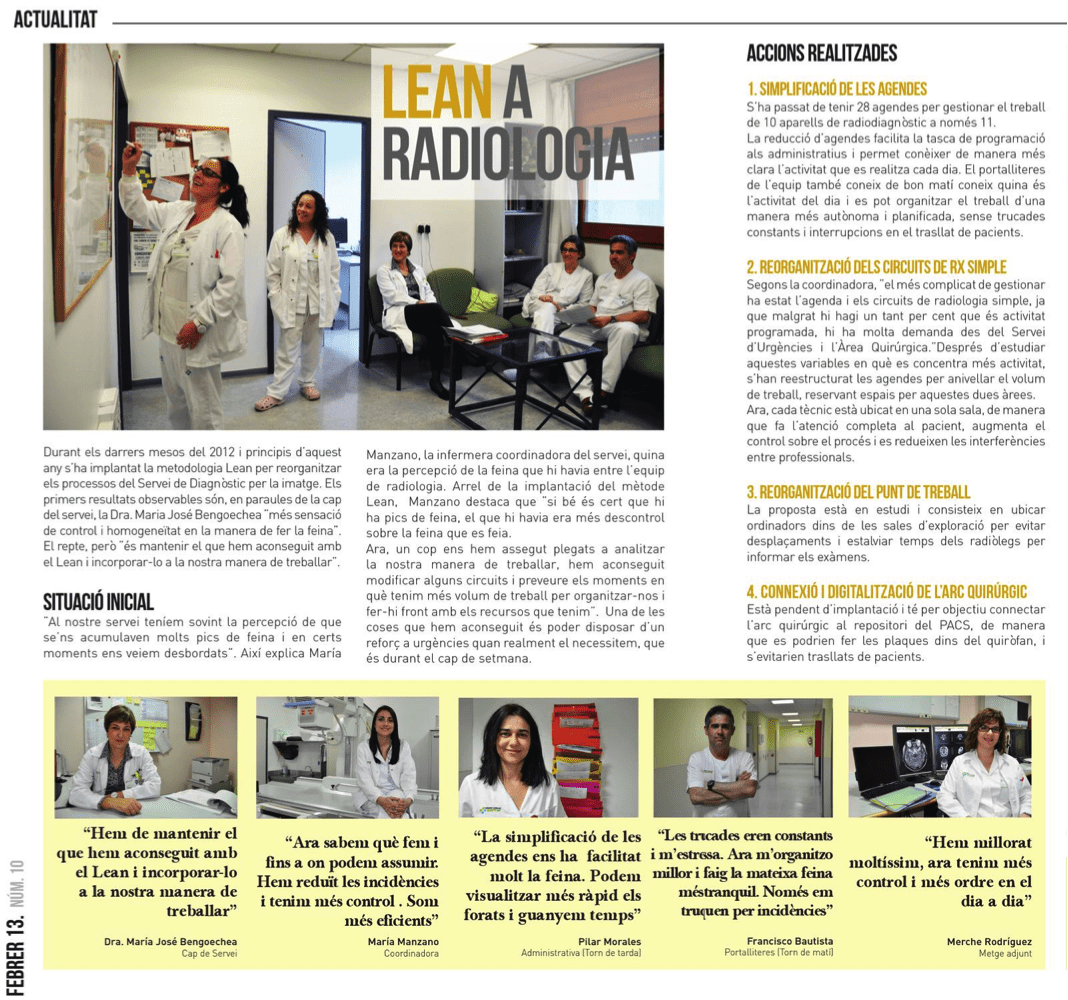
After a few months, staff behavior started to change as everyone began to understand what lean was about (and maybe, more importantly, what it wasn’t about). The picture on the left shows a page from the organization’s internal monthly magazine. In the article shown on the page, the Diagnosis Service team talks about their experience using lean principles and tools and share their point of view and how the changes directly affected them.
Over the entire course of the transformation, the active role of leadership has contributed to the achievement of good results. The project has been supported enthusiastically, down to the level of every decision and implementation of changes. On certain occasions, meetings on CSG’s lean work happened in the presence of some members of the management team.
The organization knows it has a long way to go in its lean implementation, but it’s also encouraged by the great start it experienced.
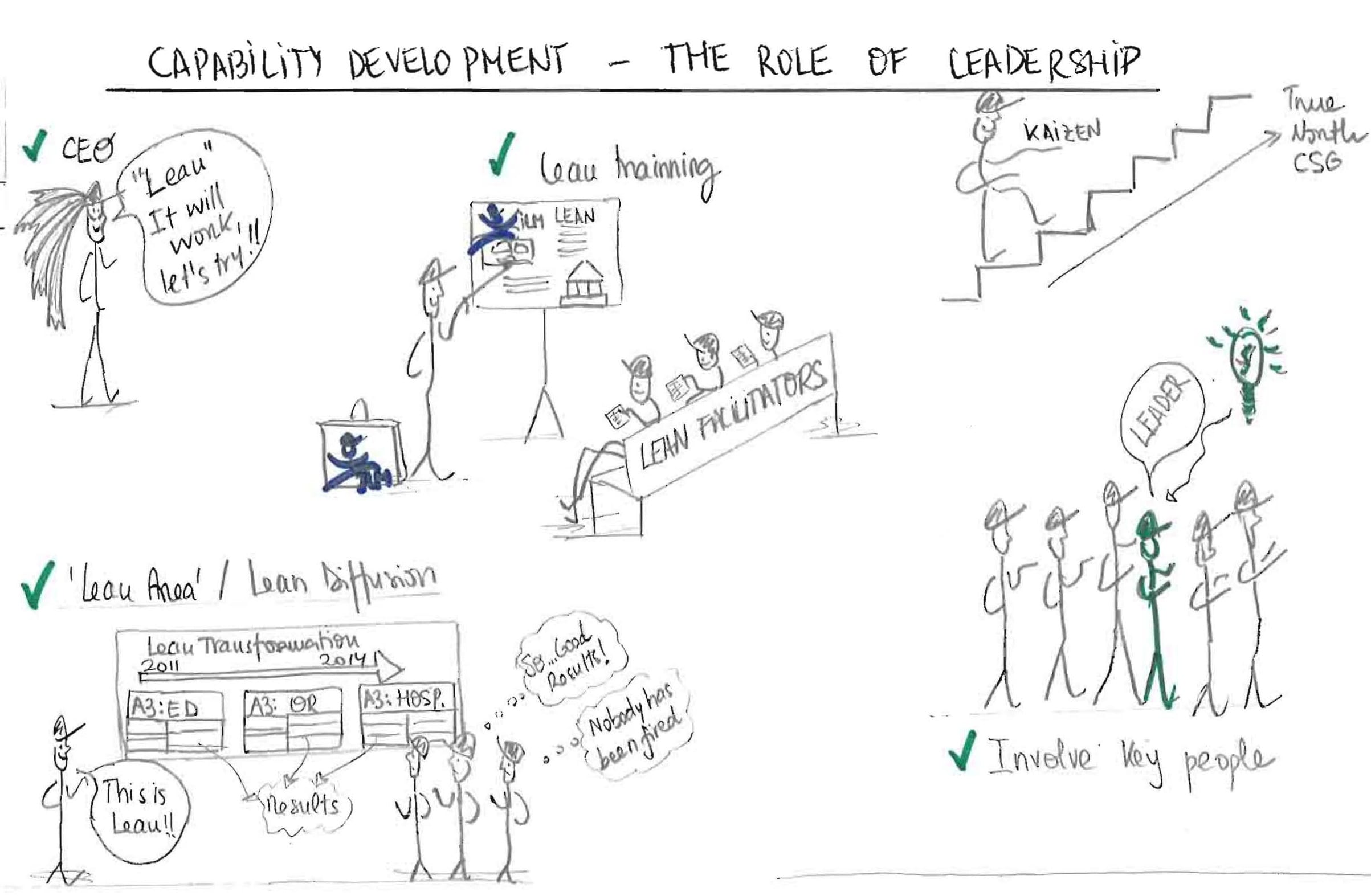
- Process improvement
Process improvement at CSG follows the PDCA philosophy and is supported by the use of lean tools, such as A3s, value stream mapping, 5S, standardization or precedence diagrams.
The criteria used to select the first project (which had to be small, visible, easy to complete, assigned to a highly motivated team, etc.) were critical to its success, as it represented the early gains that gave the organization the traction it needed to expand the reach of its lean implementation.
The steps are the same in each project. Here they are:
- The PLAN phase consists, first of all, in starting the A3 of the project. The background and the available resources are written down, in the ‘Current Situation’ section. In order to fully describe and understand the situation and to detect opportunities for improvement, the team must go to the gemba. A value stream map is also included in the A3. Then, the overarching goal of the project is added to the A3, and the team starts to analyze each improvement opportunity and tries to reach its root cause. Once the analysis is complete, the team can start to think about countermeasures.
- The DO phase consists in determining the actions that will lead the team to the future situation.
- The CHECK phase sees the monitoring of the indicators included in the A3. Generally, this happens several weeks after actions are implemented.
- The ACT or ADJUST phase entails the standardization or the adjustment (through a new PDCA cycle) of the actions, depending on the results achieved.
The A3 is a tool that guides the development of the entire project.
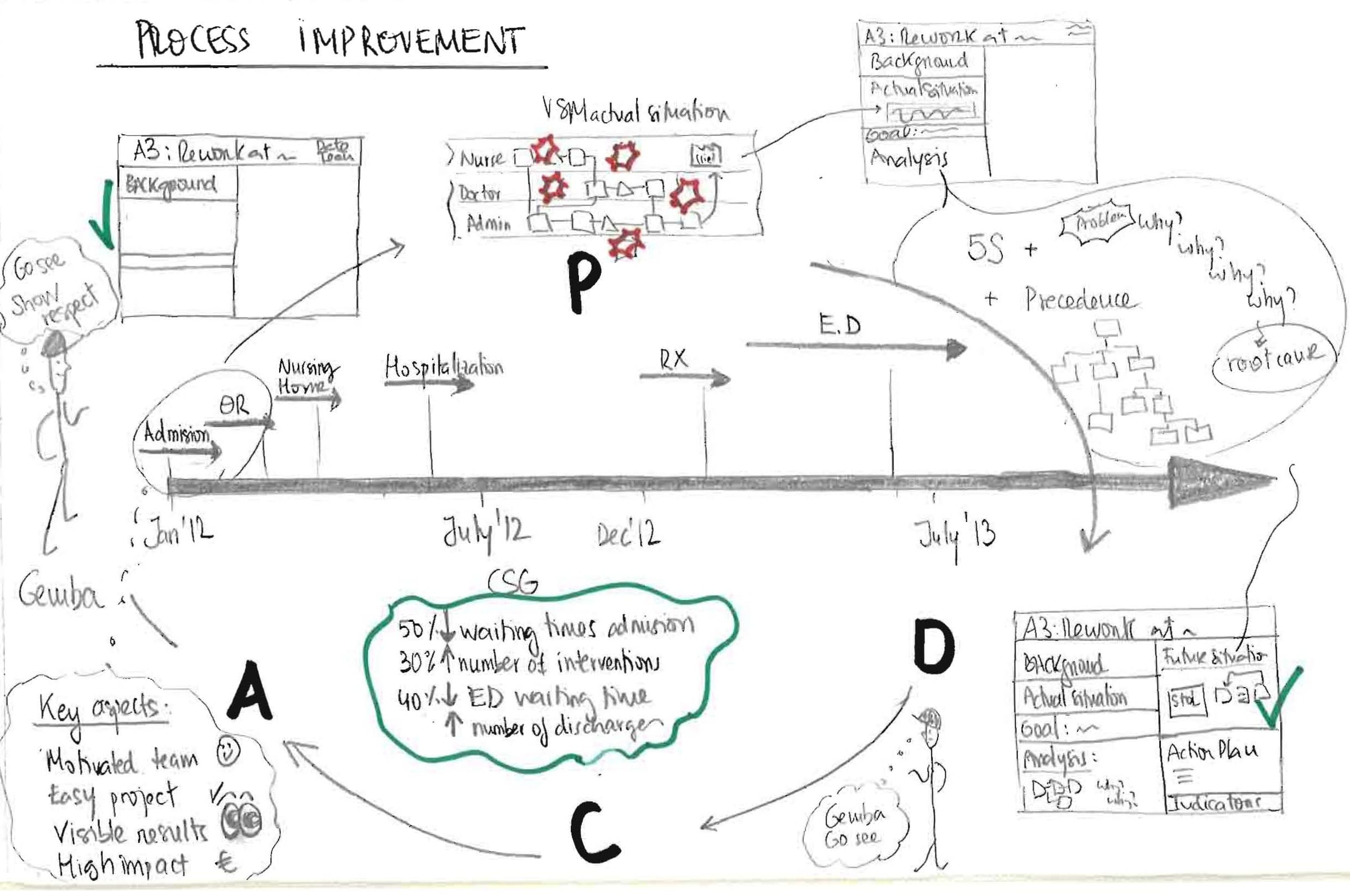
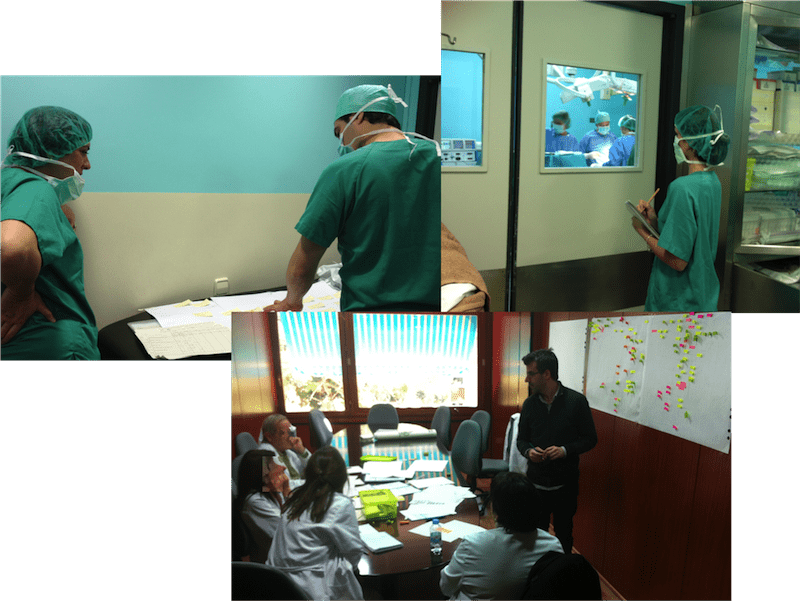
Applying a Lean approach to a Surgical Service at Consorci Sanitari del Garraf (CSG)
Background
For the past few months, CSG has had a long waiting list for its surgeries together with cuts to the surgical activities performed in the afternoons. This situation highlighted the need to increase the number of procedures completed in the mornings in each of the three operating rooms.
Current situation and problems
Before starting the project, a multidisciplinary team was selected. The first phase of the project, and one of the most important ones, was spending several days at the gemba in order to understand and describe the initial situation (see picture 1). Essentially, the service analyzed was a general surgery.
After the observation phase, an A3 was “opened”. The A3 is a powerful lean tool in which the PDCA (Plan, Do, Check, Act) phases are reflected upon in seven sections. It helps to bring order to problem solving.
In the A3, the team described the background so that everyone could understand the reason for starting the project, and the initial situation. To paint this picture they used value stream mapping, which described the process as well as information and material flow of all surgical activities, and reflected on the opportunities for improvement identified during the observation. Among others, the team highlighted a high volume of duplicated activities, rework, professionals’ downtime and a lot of motion, between seven surgeries. This last one was visualized through a spaghetti diagram, to effectively “see” the number of movements professionals had to perform to do their work.
Objectives
Everything confirmed that 30% of the total turnaround time (TAT, time between procedures) was not value added. Lowering this figure by optimizing all the activities carried out between surgeries became the main goal.
The TAT was defined as the time between the last sanitary bandage applied on patient zero and the first incision on patient one.
Analysis
According to the opportunities detected, the team conducted a 5 Why exercise through which it was able to get to the root cause of the problems. The 5 Why methodology consists in asking ‘why’ five times (as an approximate number) for each of the problems detected, until you reach their root cause.
The issues identified were mainly due to a lack of coordination between professionals and to a failure to assign tasks. A precedence diagram was used to analyze the order and sequence in which activities were carried out, and then redefine them, together with the time of each activity and the total time.
Process bottlenecks were of course identified. The more horizontal the optimized process is, the smaller the lead-time will be. The result was a better-organized and more efficient process. This was achieved using the SMED approach.
Countermeasures & Proposed Situation
From this point onwards, the team continued to work on the potential countermeasures, which meant starting to fill in the right side of the A3. As far as the future state goes, a new way of doing TAT activities was proposed. After a number of days in which PDCA was carried out, a new working standard was tried by the professionals, and then adjusted and improved using their feedback.
A 5S implementation was also conducted inside the operating rooms. Having a clean and well-organized workplace prevents waste and variation from appearing. In other words, it transforms the workplace in another tool that supports the completion of daily work.
Action Plan
Once all team members agreed on the future state, the dates in which each action would have to be accomplished by were included in the A3’s ‘Action plan’ section. For example, they planned for a few communication meetings that would be used to explain to all staff the new standard work.
Indicators and follow-up
The TAT was used as the main indicator, which was periodically reviewed.
The result of this project was a 30% reduction of the NVA time between procedures, which helped to move more of the activity to the mornings.
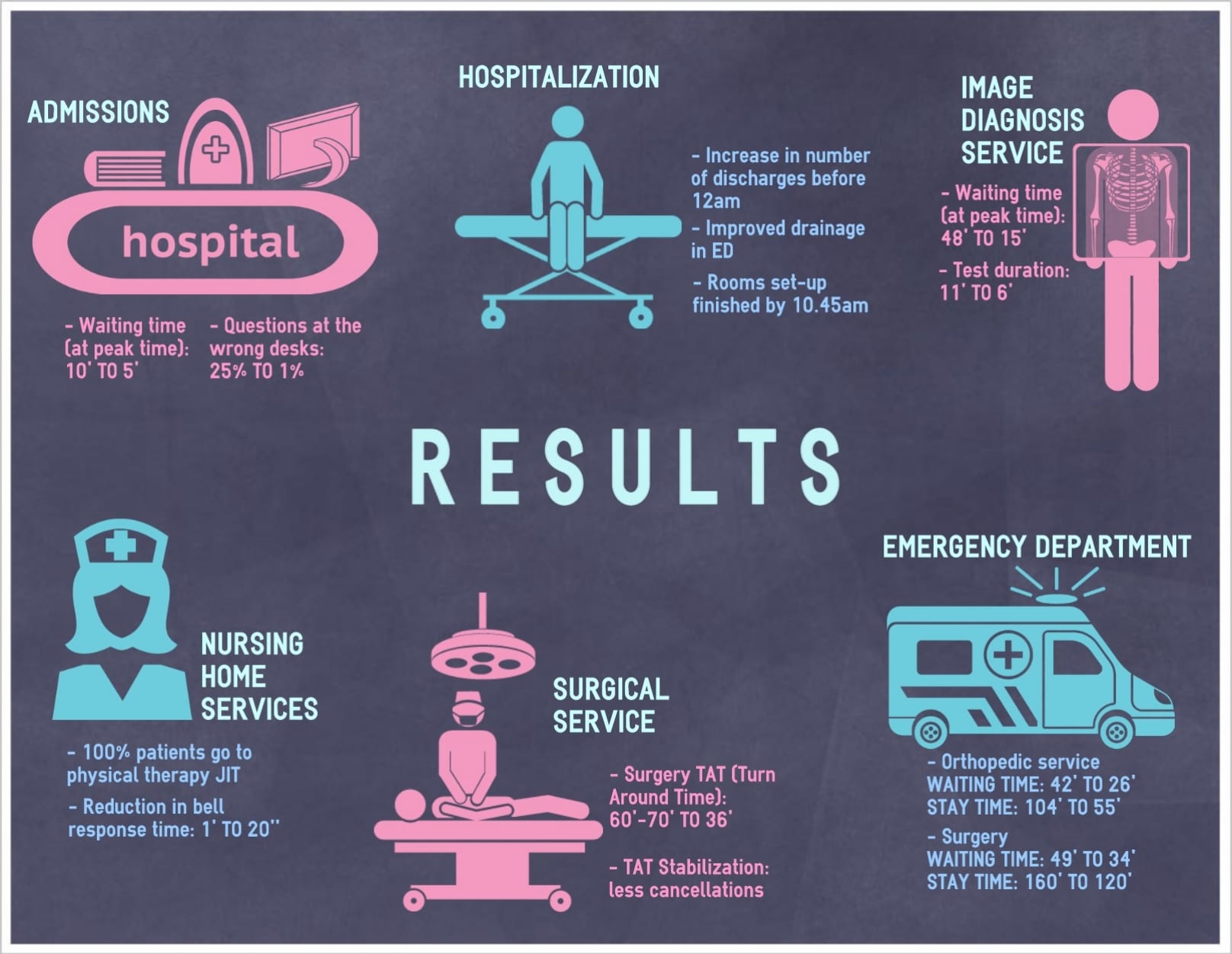
THE AUTHOR
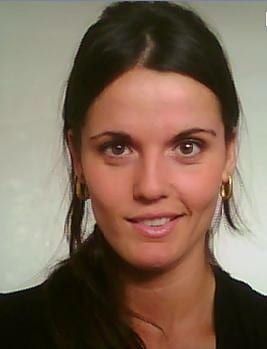
Read more
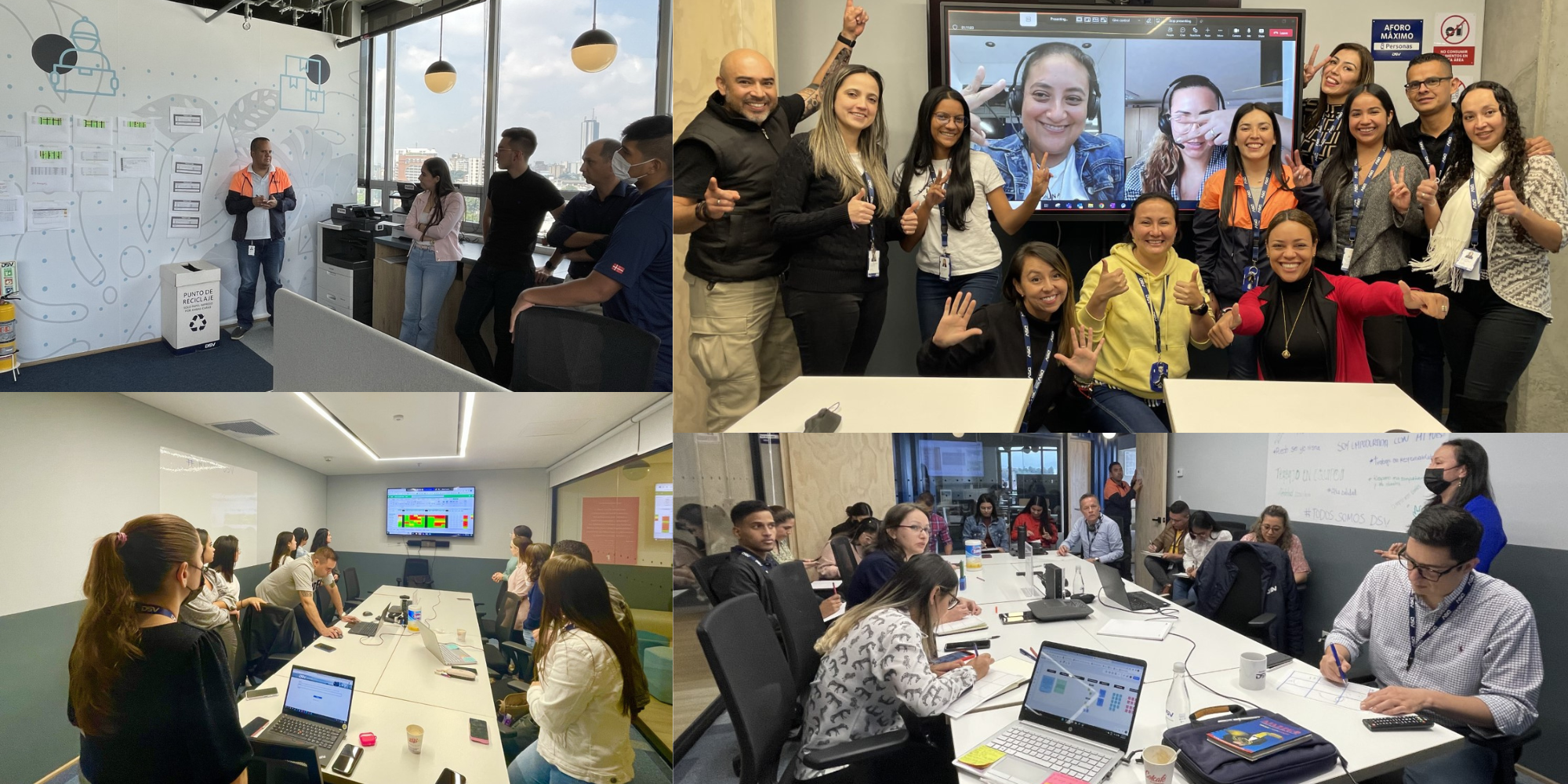
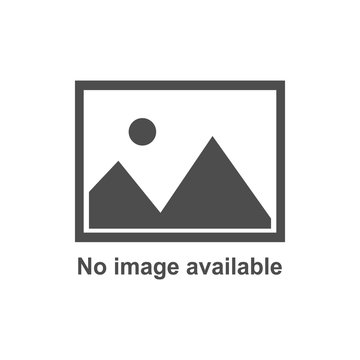
CASE STUDY – This transport and logistics company in Colombia has turned to Lean Thinking to become more adaptive and ensure an easier post-acquisition integration of new cultures.
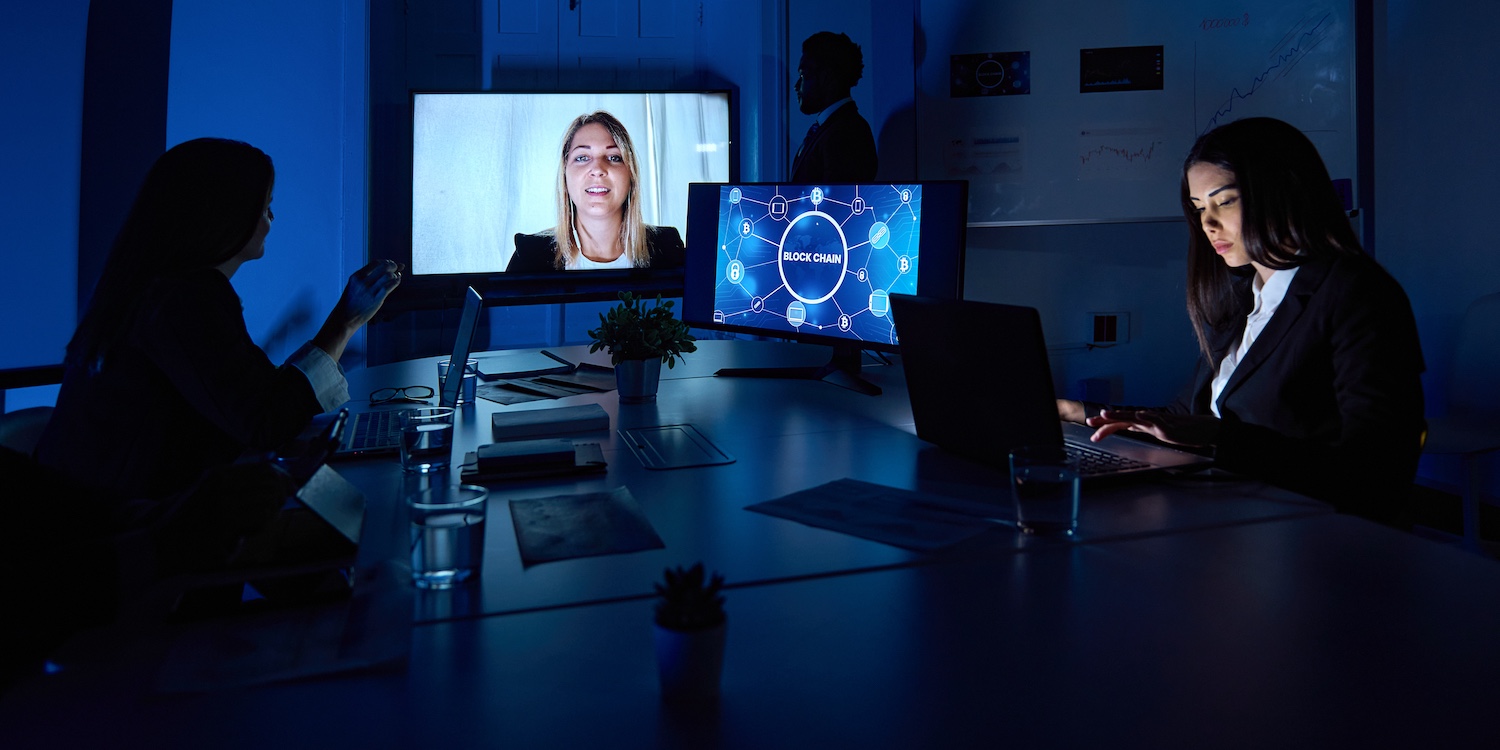
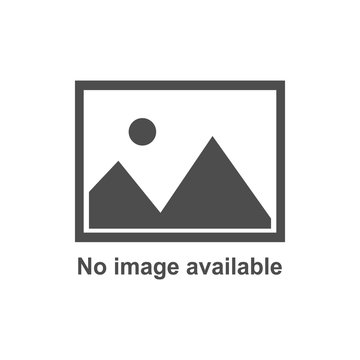
FEATURE – This article explores the integration of lean leadership behaviors with digital tools to achieve sustainable performance improvement in modern organizations.
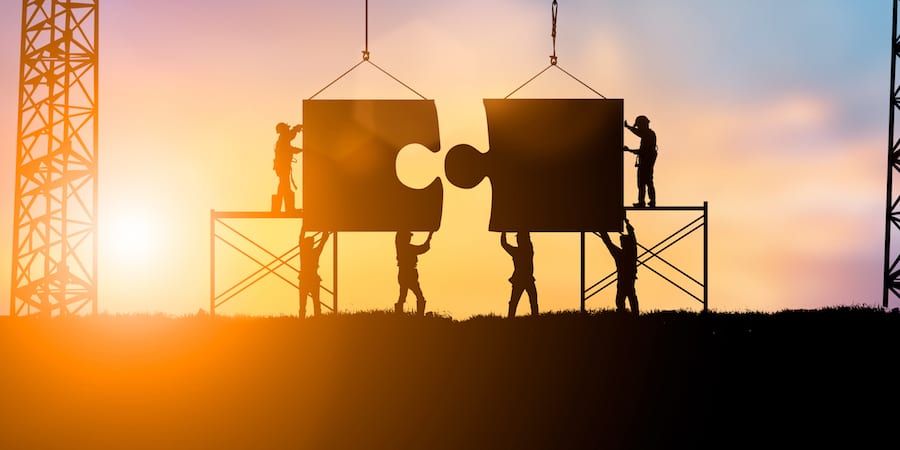
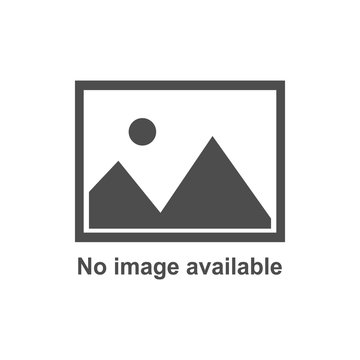
FEATURE – Using Carol Dweck’s distinction between fixed and growth mindsets, the author discusses how leaders should think and act to make lean possible. Looks like no fixed mindset is beyond saving.
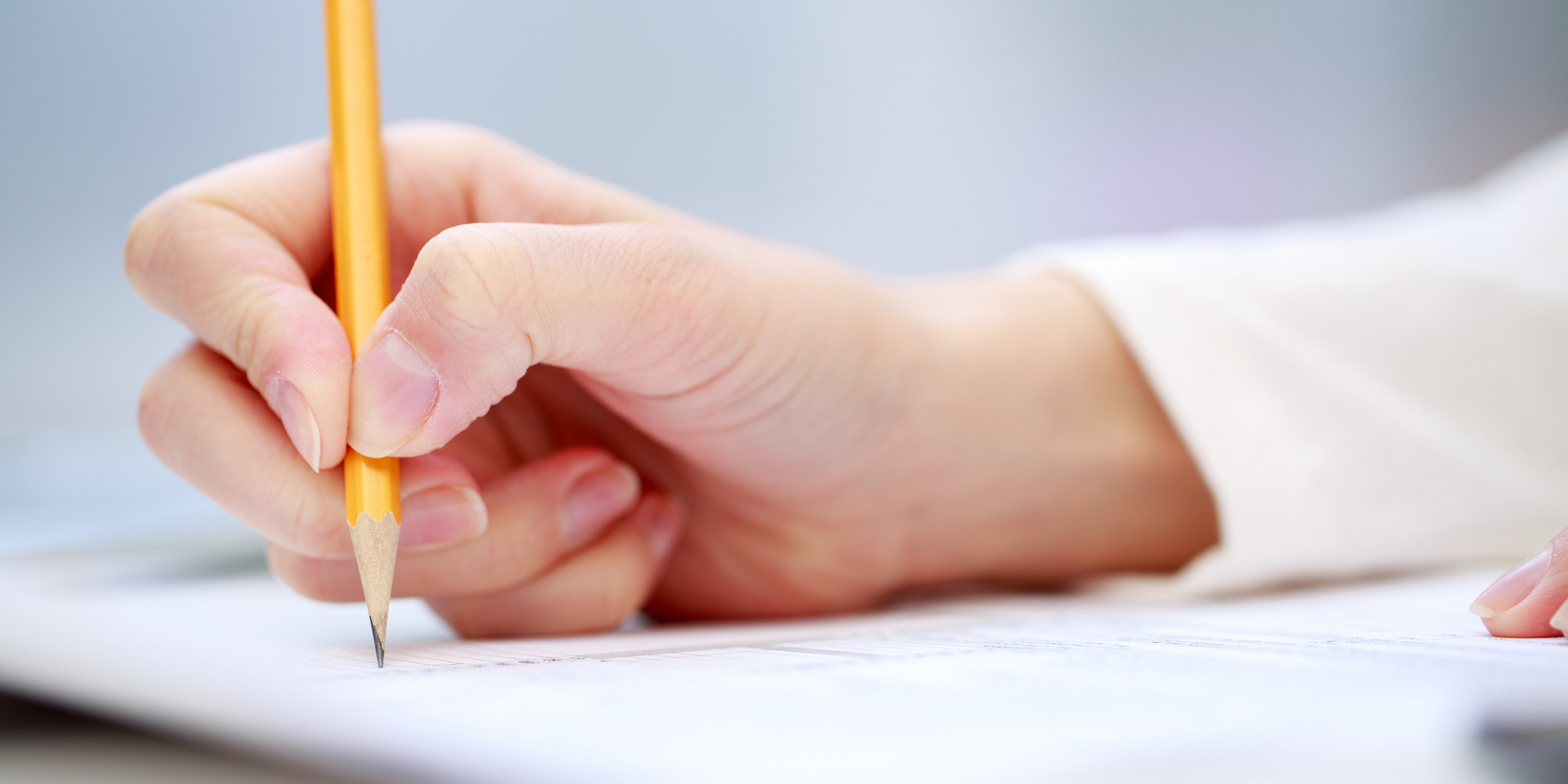
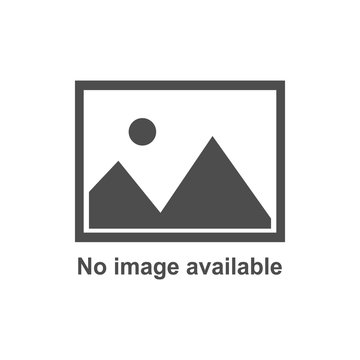
FEATURE – Problem solving is a fundamental part of being a leader, which is what led this medical school in the United States to include A3 thinking in its curriculum.