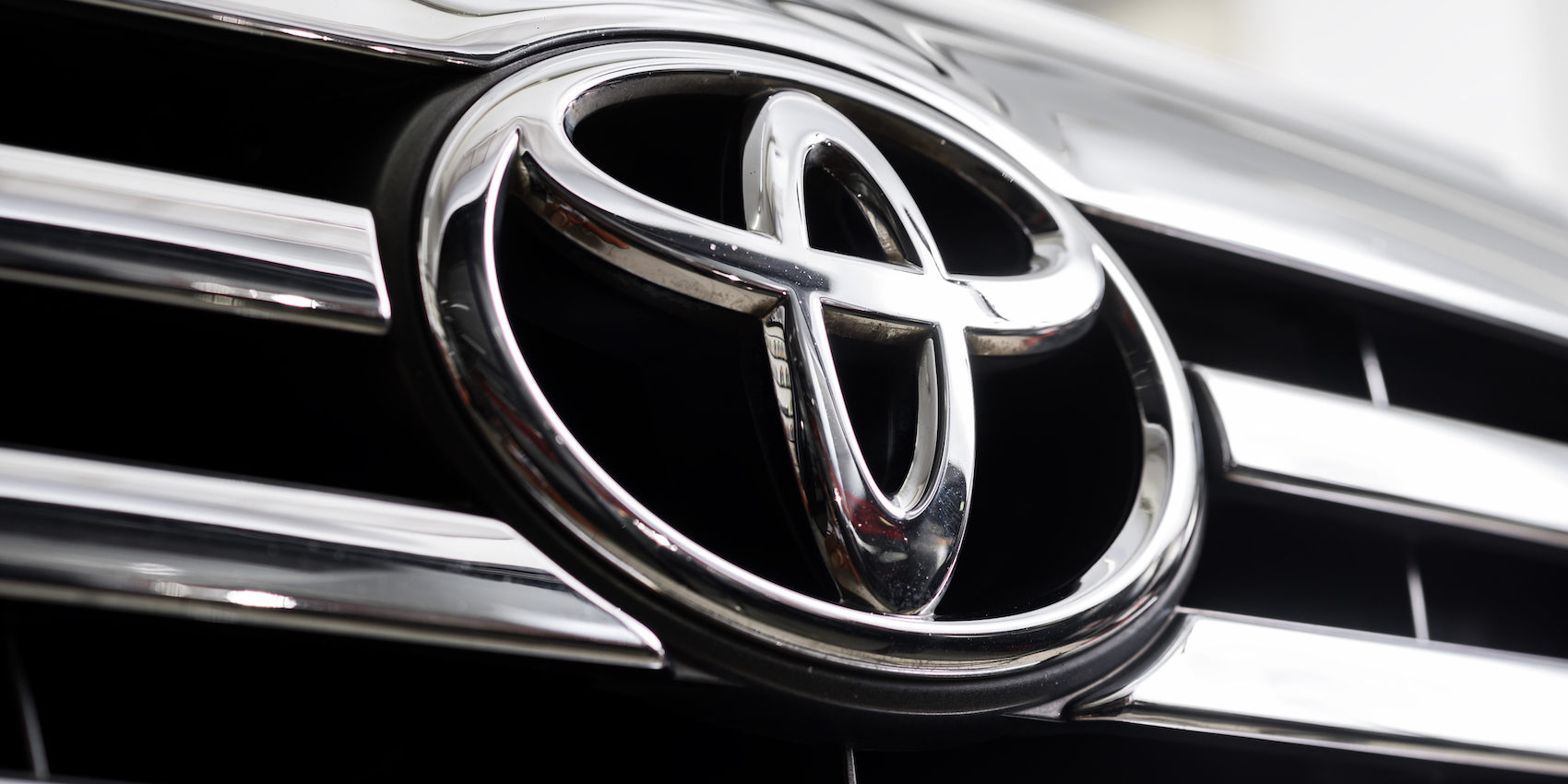
What does learning look like at Toyota?
INTERVIEW – Toyota’s approach to developing capabilities and its focus on life-long learning are inspirational. But how do people at Toyota actually learn?
Interviewees: Martyn Hayward, Lean Consultant, and Yian Baty, Section Manager at Toyota Motor Manufacturing UK.
Planet Lean: How does learning happen at Toyota Deeside?
Yian Baty: At Deeside, the development of our people (which we consider directly related to our ability to manage the process effectively) is led by Group Leaders and line managers on the shop floor. HR also plays a very important role in ensuring each of our employees is on a path of continuous learning. It does so through development maps, but also by looking at our strategic needs as outlined in our Hoshin. This means we don’t aim to only teach people skills they will need here and now, but look at their long-term development instead.
Martyn Hayward: We believe in on-the-job learning. Therefore, upon reflecting on how we recruit, we have introduced an initiative called A Day at Work: we invite potential employees into the plant to observe certain tasks. This exercise is designed to show them how we operate as an organization here at Deeside. When we hire new people, we don’t necessarily expect them to already have experience on the assembly line. We believe we can coach, develop and train people from any walk of life and give them the skills they require to perform their day-to-day tasks.
PL: What tools and techniques do you use in your people development activities?
MH: We rely heavily on training dojos. This are particularly powerful when training new members, to equip them with the fundamental skills they will need out on the floor. To assist us with that, our trainers need to be certified in Japan to deliver Toyota’s Job Instructions training.
We, of course, have standards for our operations and our members are expected to follow them to ensure safety and quality. For this to happen consistently, there are regular observation of the members’ work to ensure adherence. Part of the daily checks our leaders have to perform focus specifically on whether members are using the standardized work. This can involve videoing our team members at work and then sitting them down to review the process with them. It’s a great learning tool.
PL: What about the material you use?
MH: When it comes to assisting the teaching of the fundamental skills our members require, we use visual manuals created by Toyota Motor Corporation. These ensure a standardized approach to training globally. No matter where you are, we know we are training members in the exact same way.
PL: What does learning at Toyota look like?
YB: We use a program called Core Job Role to provide a picture of what makes a good team member, team leader or group leader. This gives them an idea of where we expect them to go – beyond just quality or kaizen. In this sense, the program is also a coaching tool for leaders to develop their members.
We don’t set a standard target of where people should be in their development, because Toyota believes in life-long learning. It is not enough for people to learn the skills they need in the short-term. It’s where a team member takes what we teach them that really matters! So, to assess their level of learning, we don’t just measure their understanding and knowledge, but more holistically look at their skill, will and belief.
MH: In addition, we have a development map for our shop floor members that sets out possible progress of an individual from when they start to when they can become a Senior Manager.
PL: How much of the learning takes place in a classroom and how much at the gemba?
MH: We provide some classroom-based training, with our development maps setting out a number of courses and workshops that will support members in their future progress. At Toyota, on-the-job development is constant and goes hand in hand with the coaching and mentoring members receive from their supervisors and managers.
YB: We have a number of programs that teach people practical skills, but also behaviors. This is critical for our people in the longer term, especially if they are moving position from one occupational classification to another. They need to understand what behaviors they need to make that transition. It’s important to understand that technical skills are not everything: having the behaviors is just as important, especially when you are managing people. With the andon, for example, it’s essential we coach our supervisors to ensure they respond in the appropriate manner to a member raising a problem.
PL: How do you take into account each person’s unique learning path?
YB: Because everybody learns at a different pace, our development map isn’t linear and allows for deviation – based on a team member’s interests (they can request training) and the skills the supervisors need in their group in order to fill a specific gap. Even though we set clear expectations from the outset, a person’s development within Toyota can take different paths from what was originally foreseen.
PL: What does it mean for Toyota to be a learning organization? And why is it so important?
MH: For us, learning is fundamental because we know that developing our people is the only way to develop our organization. We recognize the value of human development: flexible, motivated people lie at the center of Toyota Production System. It is our very culture that helps us to create an effective learning environment. Indeed, our development efforts are informed and guided by the Toyota Way and are very much seen as a critical part of our long-term strategy.
Some organizations don’t pay enough attention to people development. To them, it looks like a detour, when it is actually the best shortcut. This is why we aim to cement understanding by giving organizations the unique opportunity to study these techniques as part of the Toyota Lean Management Centre learning package.
YB: Our Hoshin simply can’t be achieved by the management team alone. It needs the active and full participation of team members, because they are the ones who really instigate change at all levels. That’s why continuous learning is a vital part of what we do: developing the right skill and behaviors in our people will help us to achieve what we set out to achieve as a business.
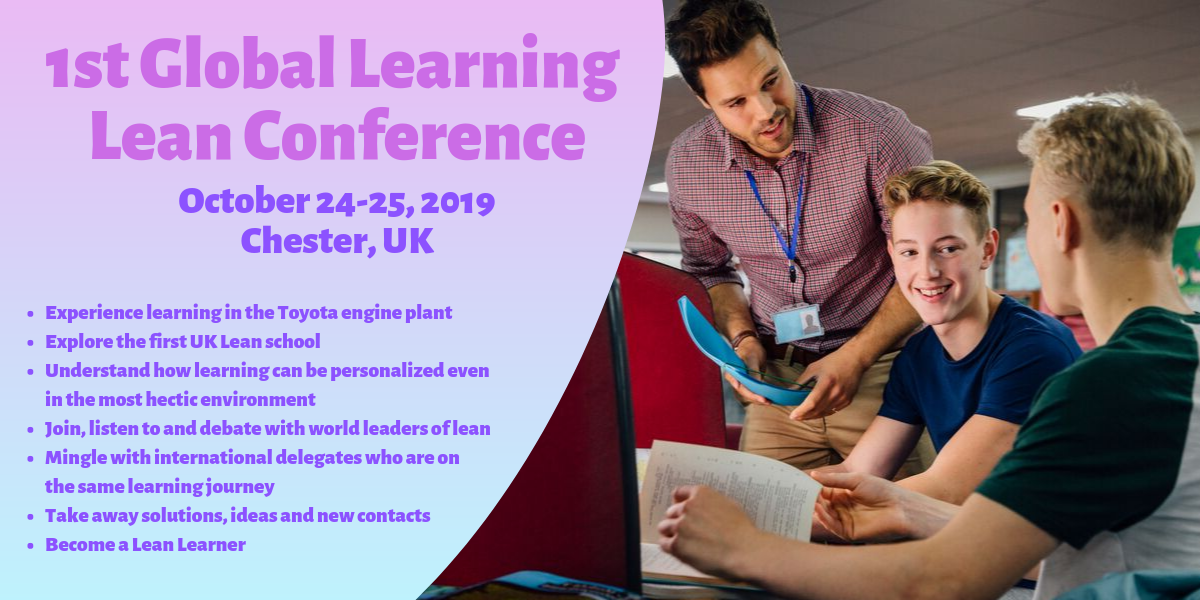
THE INTERVIEWEES
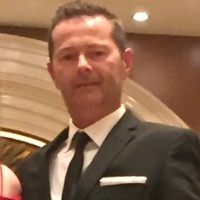
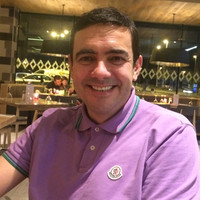
Read more
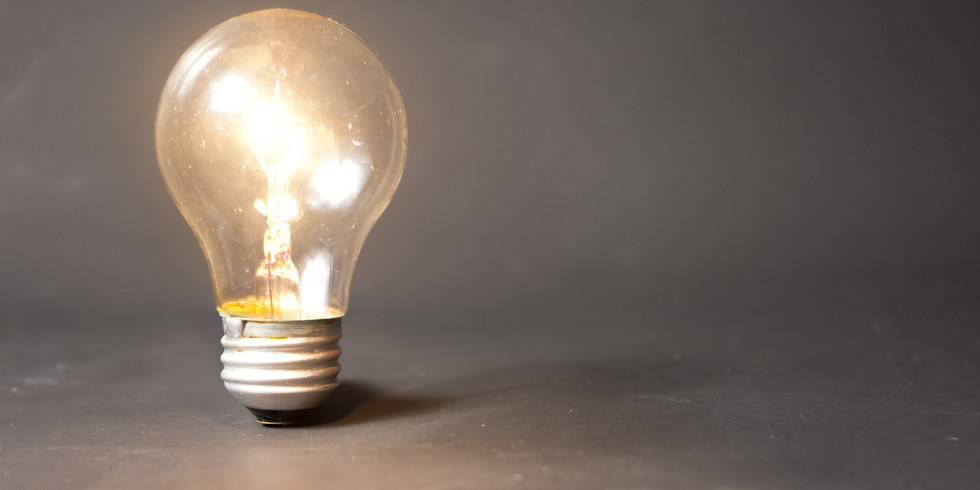
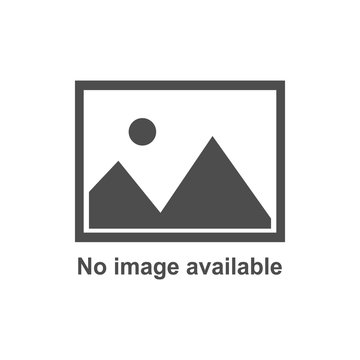
FEATURE – In this call to arms, the author encourages us to fight to prove the relevance of Lean Thinking in such difficult times and explains why only mastering it can truly address our problems.
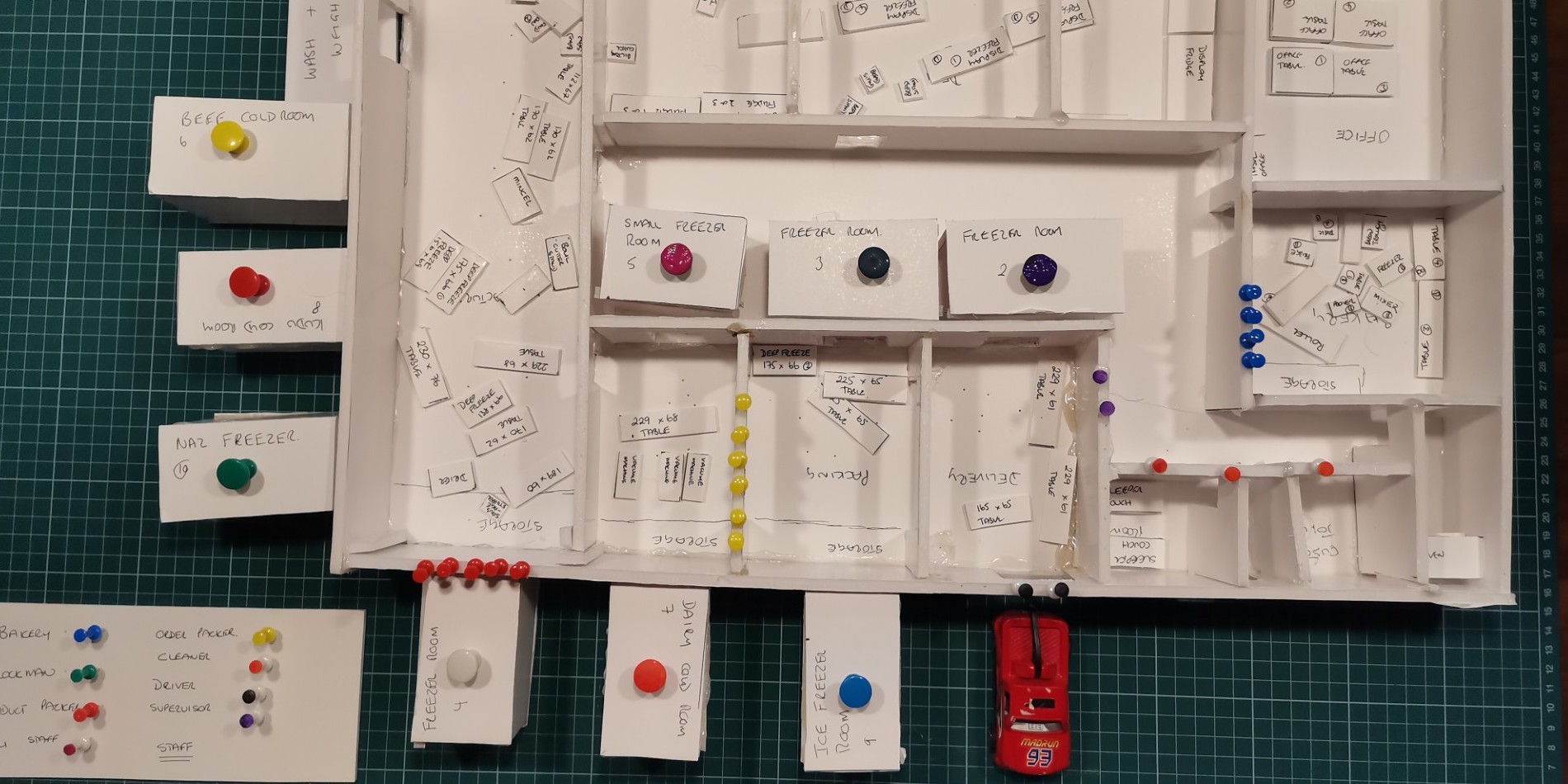
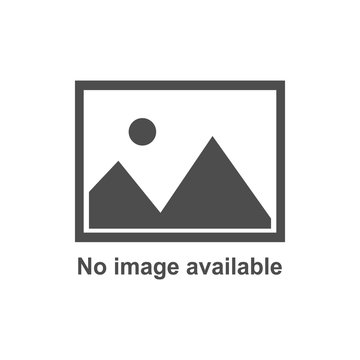
FEATURE - Looking back to her experience coaching teams in Africa, the author encourages us to introduce play in our work, as a way of teaching people and of unlocking creativity.
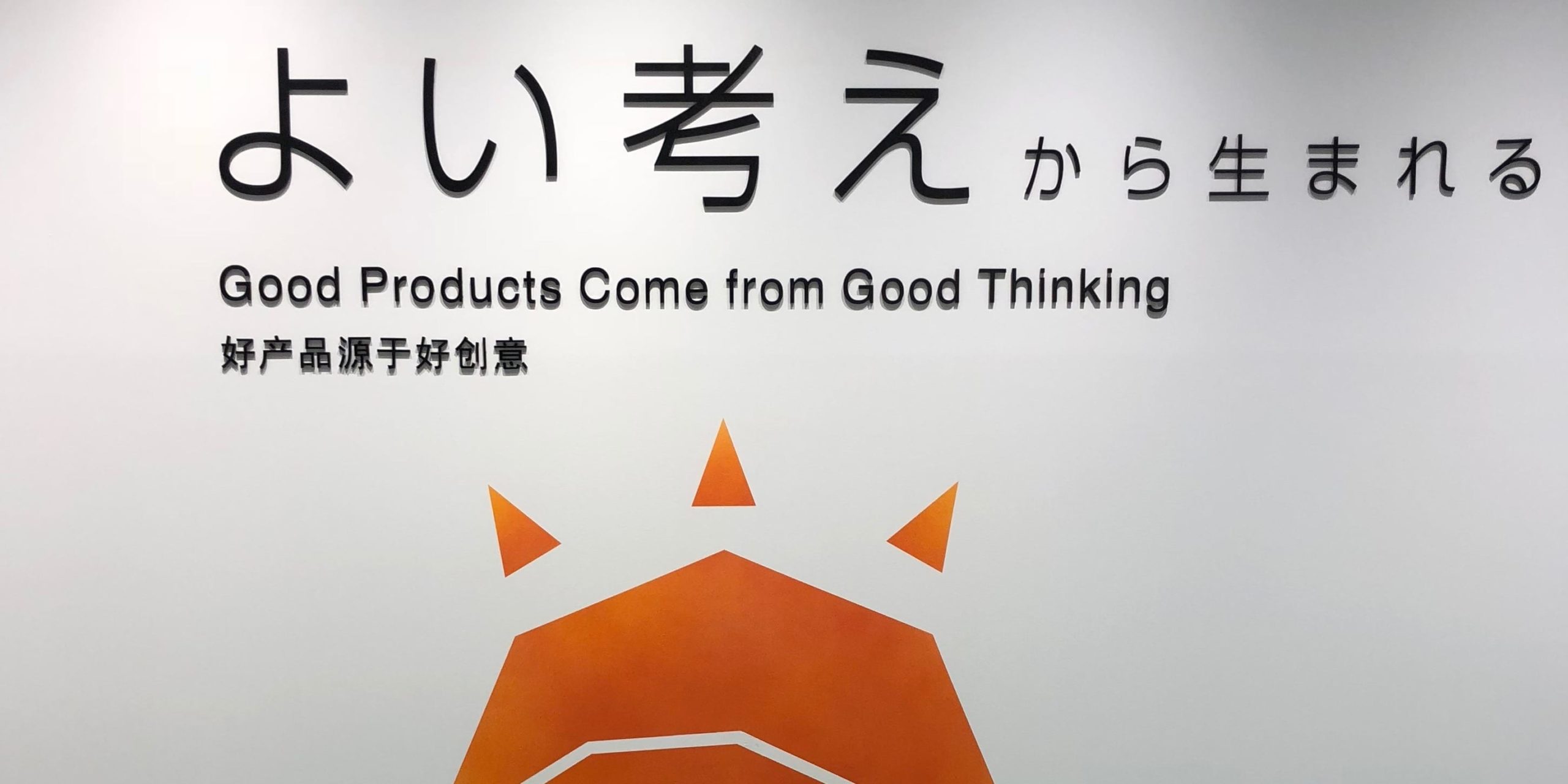
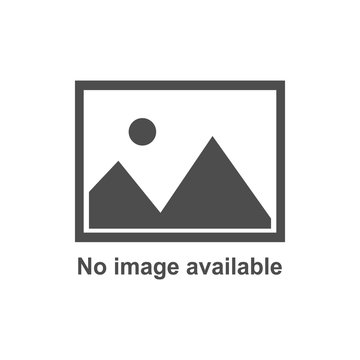
FEATURE – Following a recent visit to Toyota, the authors strive to challenge popular beliefs and shed a light on the underlying philosophy that has made TPS a success for over half a century.
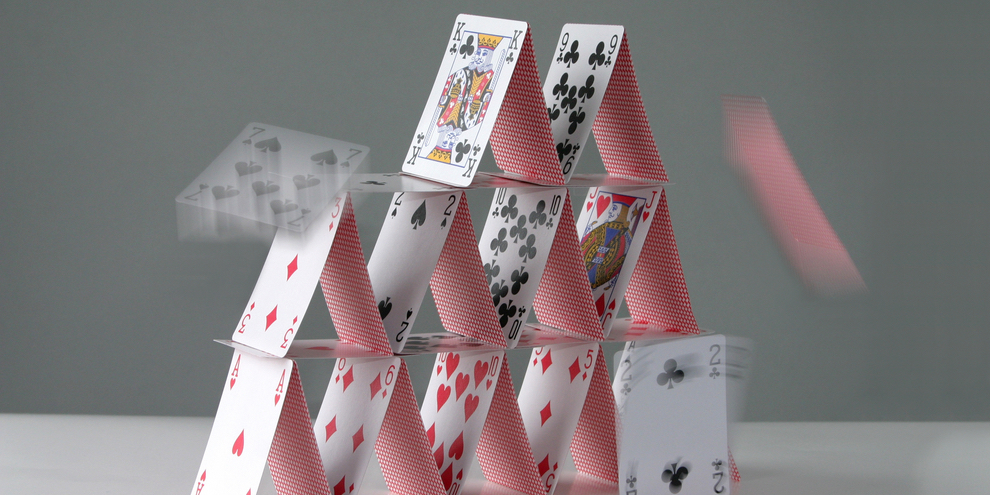
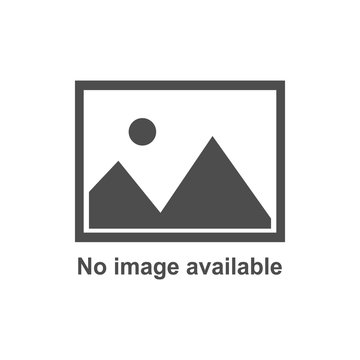
FEATURE – Drawing inspiration from his research into the causes of failure of transformations, the author discusses how these can directly be linked to the most common misconceptions on Lean Thinking.