
Where the Lean Community is and where it should go
WOMACK'S YOKOTEN – As the Lean Enterprise Institute turns 20, its founder provides us with a bit of hansei on where we are and where we are going next as a community, and on what challenges we might tackle.
Words: Jim Womack, Founder and Senior Advisor, Lean Enterprise Institute
In the spring of 1997 someone – not me – had a brilliant idea. Dr. Don Berwick, the founder of the quality-focused Institute for Healthcare Improvement in Cambridge, MA, told me that I should found a non-profit institute to explain Toyota's ideas about business systems and to promote their application in every value-creating activity.
I'm not a perfect patient but I do try to be compliant with "doctor's orders". So on May 1, 1997, in my home office, I hired the first Lean Enterprise Institute employee. The incorporation of our 503(c)(3) non-profit (American tax talk for being tax exempt) came a bit later – doing this was the first job of Employee Number One Jane Ross – but LEI was in business.
I decided pretty quickly that we should pursue the mission through five "value streams":
- Publications outlining the many lean concepts that I felt had not been adequately explained, at least in English. The first was Mike Rother and John Shook's Learning to See, which set a high standard that I hope we have been able to maintain. In doing this we got a lucky break with the maturing of the web so that we could take orders without need for distributors or retailers and fulfill them at very low costs while learning the name of every customer.
- Workshops to teach lean concepts, which proved a great way to test ideas and how to present them before the expensive task of turning them into publications.
- Conferences to bring together lean thinkers from a wide range of industries and with a wide range of responsibilities (line and staff, and the consultants who I knew would be the greatest single transmission mechanism.) By 1997 I already had five years of experience with lean conferences and I knew that, when done correctly, they could create energy and give attendees courage to try experiments when they returned to work. So getting started quickly was easy and I hope we have been able to keep you – our customers – happy.
- Experiments with founding sponsors followed by partner firms to see what we could learn together about applying and adapting lean ideas in every value-creating activity.
- A website to share information and bring together lean thinkers across the world, which we were soon calling the Lean Community. (This was another lucky break. The web eventually allowed us to be in touch with more than 250,000 lean thinkers with minimal cost for connectivity.)
These value streams were the organizational pillars of LEI (but I hope not the silos!) and they continue to this day. However, our focus in each value stream has gradually shifted from tools and methods for improving processes of every imaginable sort to the lean management systems that align them and make them deployable and sustainable. As a result, under the leadership of John Shook who succeeded me as CEO in 2010, we now talk more about the elements of a lean transformation for traditional and modern management organizations and less about technical methods. But we will never lose our interest in lean tools. These are the fundamentals that create the firm foundation for pursuing new frontiers.
Along the way we also created the Lean Global Network of 22 aligned organizations in 22 countries which try to make lean thinking and lean management available to as many people across the world as possible. (Planet Lean is one of the initiatives of the LGN and I'll have more to say here about this remarkable collection of independent organizations flying in formation in my September column as the LGN celebrates its 10th anniversary.)
This is all nice and I look back with satisfaction on my contribution as Founder, CEO for the first 13 years, and Senior Advisor for the last seven. However, as I tell the audience in every presentation, the only way to judge the value of our work is by determining how effective we are in changing management practices and organizational performance across the world. Efforts without results, no matter how earnest, are muda.
On this metric, I think we should be modest about the improvements we have achieved to date but optimistic about the future. I believe that together we have boosted an invaluable set of ideas and methods into low earth orbit. While many fads in management and methods have come and gone in the past 20 years, I have little fear that our ideas and practices will fall from orbit and vaporize. This is for the simple reason that our ideas actually work, unlike many others. When implemented properly, they always produce remarkable results.
But we now know that true organizational transformation takes years, even decades, and there are setbacks along with advances. To take one well-known example that I discussed in my previous column, Lantech has long been a lean poster child. But in reality it made a dramatic leap in practice by deploying lean tools to create product family value streams and flow and then fell back due to the limits of its management system. Twenty years later, with a new generation of family leadership, it made another dramatic leap by mastering daily management. (See Jim Lancaster's The Work of Management for the details.) Meanwhile Toyota, our uber-poster child, has had similar experience, making dramatic advances in greenfields across the world, then losing the vision as the founding generation moved on, and then finding new energy through a conscious process of revitalization.
I have concluded that this is the norm rather than the exception. So, one of our greatest challenges going forward is to keep the interest in lean thinking alive for the long run so that the slow work of transformation has an opportunity to achieve its full benefits. And this is daunting, because the world loves novelty and the next new thing. It turns out that many managers are serial adopters of new programs who confuse motion with direction.
So, what can we do that is new and exciting after applying our ideas in at least one organization in practically every industry and in many countries? (This is not to say that there are no frontiers left along this path – just this week I made my first visit to a mining and ore transformation operation and LGN continues to receive inquiries from lean thinkers wanting to start new affiliates in new countries – Russia being the most recent. But like the elderly mine I just visited, there are diminishing returns along this path.)
One new idea I am pursuing is to apply lean thinking to big systems, not just to individual organizations and their constituent elements as we have to date. (Our focus has been on individual points of value creation and on the processes, often extended across many departments and firms, that transport value from raw materials to customers.) Big systems by definition are comprised of many value streams creating complex outputs that need to be managed in combination.
The two systems that seem most promising at the moment are mobility (combined with logistics) and good job creation. (I've written about these in my previous Planet Lean columns, Lean Thinking for Mobility 2.0, May 30, 2016, and Let's Make Jobs Great, December 20, 2016, and don't intend to go into them here.)
My idea is to apply one of the most powerful tools of lean thinking to the challenge of mobility that addresses environmental and energy needs while making transportation easier, faster, and cheaper, and to the challenge of creating not just jobs but good jobs that pay adequately and are rewarding. This tool, of course, is A3 analysis. I call it "A3 Thinking for Big Things", in contrast with the smaller but vitally important things we have addressed with A3 thinking to date.
A3 is a social process in which everyone touching a value stream or, in this case, a vast system is engaged in conversation by someone taking responsibility for better performance. This conversation starts with determining the current state and the root causes of poor performance. A discussion follows about the potential countermeasures, a ranking of those with the most potential, and critical evaluation of experiments to address them. (In the ideal case, this conversation might instigate new experiments with mobility innovations that were not previously known or appreciated.) Note that the "responsible person" (prospectively LEI) has no authority over the system. And this is the simple truth whether anyone conducts an A3 analysis or not: There will be no single architect for future mobility systems. It will only be possible to lead a transformation in mobility by knowing more about the problems and potential solutions than anyone and by being in continuing conversation with all of the participants in the system.
Can this work? Nobody really knows, but it certainly meets the criteria for the term "daunting"! And forecasts about innovations in my experience are usually wrong. But I think it is a worthy experiment that could potentially do some good for society while elevating knowledge of lean thinking and boosting our ideas into a higher and more secure orbit.
But this is just one idea. Surely there are others, perhaps much better. I would be delighted to hear from other members of the Lean Community about their ideas for raising the visibility of our core principles and securing their future. Please let me know your thoughts, perhaps for summarizing and calling out in a future column.
What do you think the next big challenge for lean should be?
Leave a comment below
THE AUTHOR
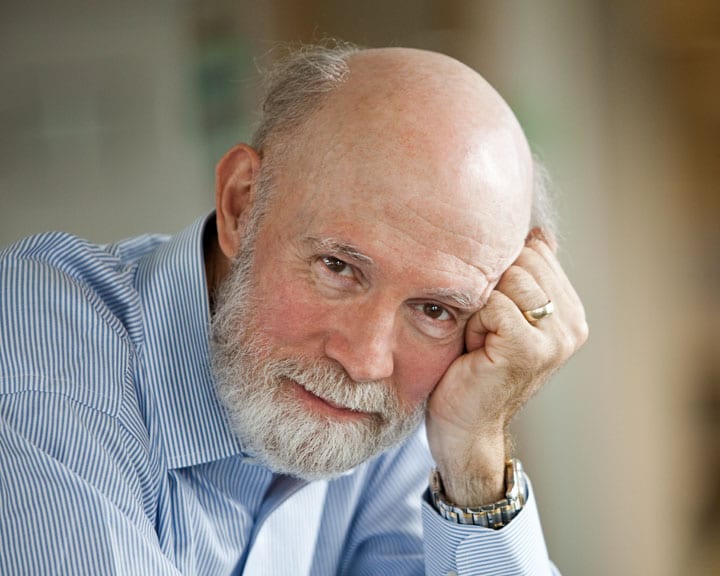
Management expert James P. Womack, is the founder and senior advisor to the Lean Enterprise Institute. The intellectual basis for the Cambridge, MA-based Institute is described in a series of books and articles co-authored by Jim himself and Daniel Jones over the past 25 years. During the period 1975-1991, he was a full-time research scientist at MIT directing a series of comparative studies of world manufacturing practices. As research director of MIT’s International Motor Vehicle Program, Jim led the research team that coined the term “lean production” to describe Toyota’s business system. He served as LEI’s chairman and CEO from 1997 until 2010 when he was succeeded by John Shook.
Read more
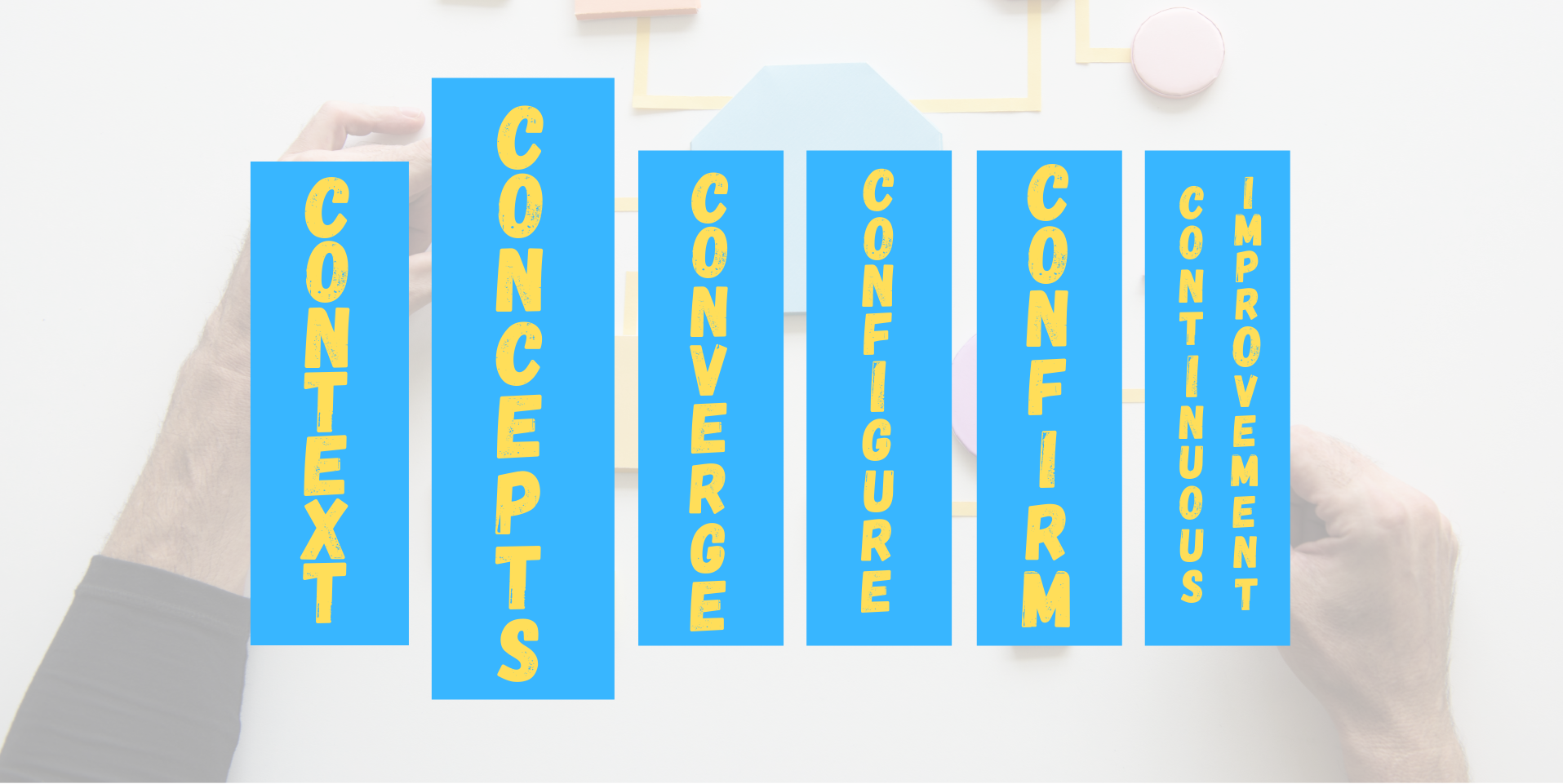
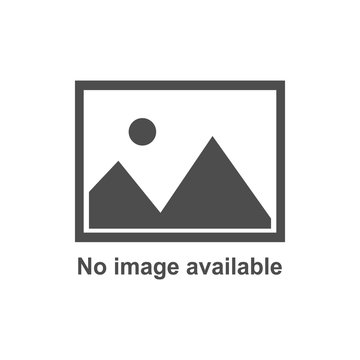
SERIES—The authors discuss Concepts, the second of six elements in their process development model, discovering the key knowledge gaps and exploring multiple process design options to facilitate learning.
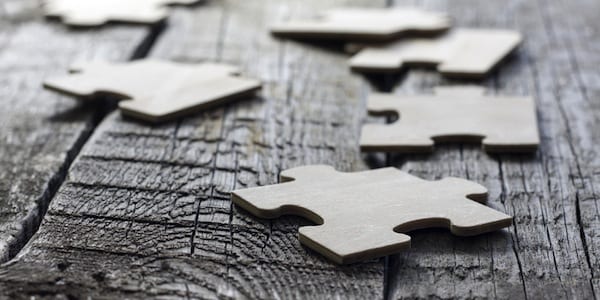
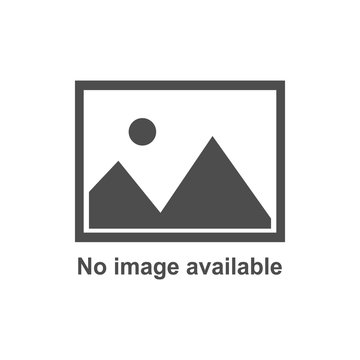
FEATURE - This set of guidelines will help you to understand how to properly structure your lean transformation, keeping into account the entire organization as it tries to embrace and manage change.
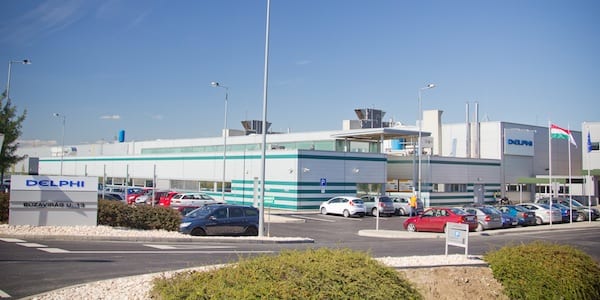
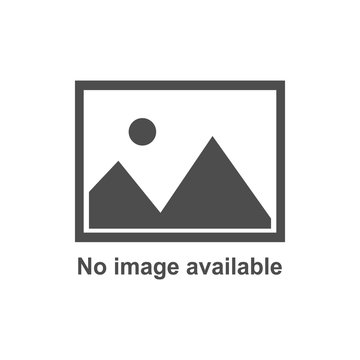
INTERVIEW - The General Manager of a Delphi plant in Hungary talks about the lean transformation the site went through and the challenges automotive suppliers face in this day and age.
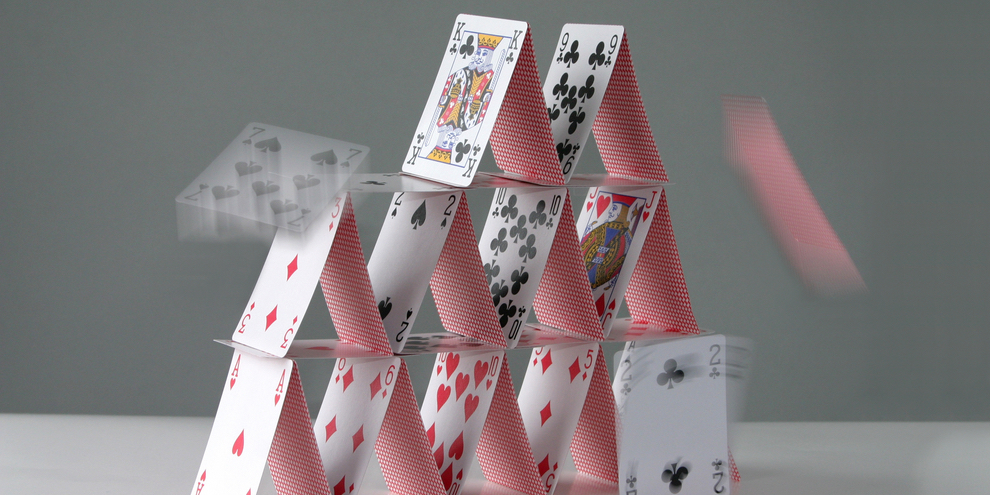
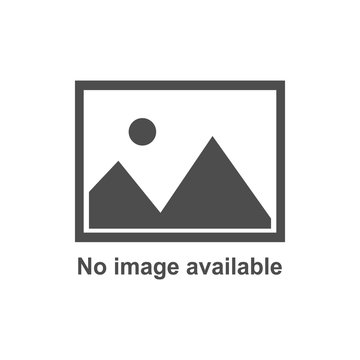
FEATURE – Drawing inspiration from his research into the causes of failure of transformations, the author discusses how these can directly be linked to the most common misconceptions on Lean Thinking.