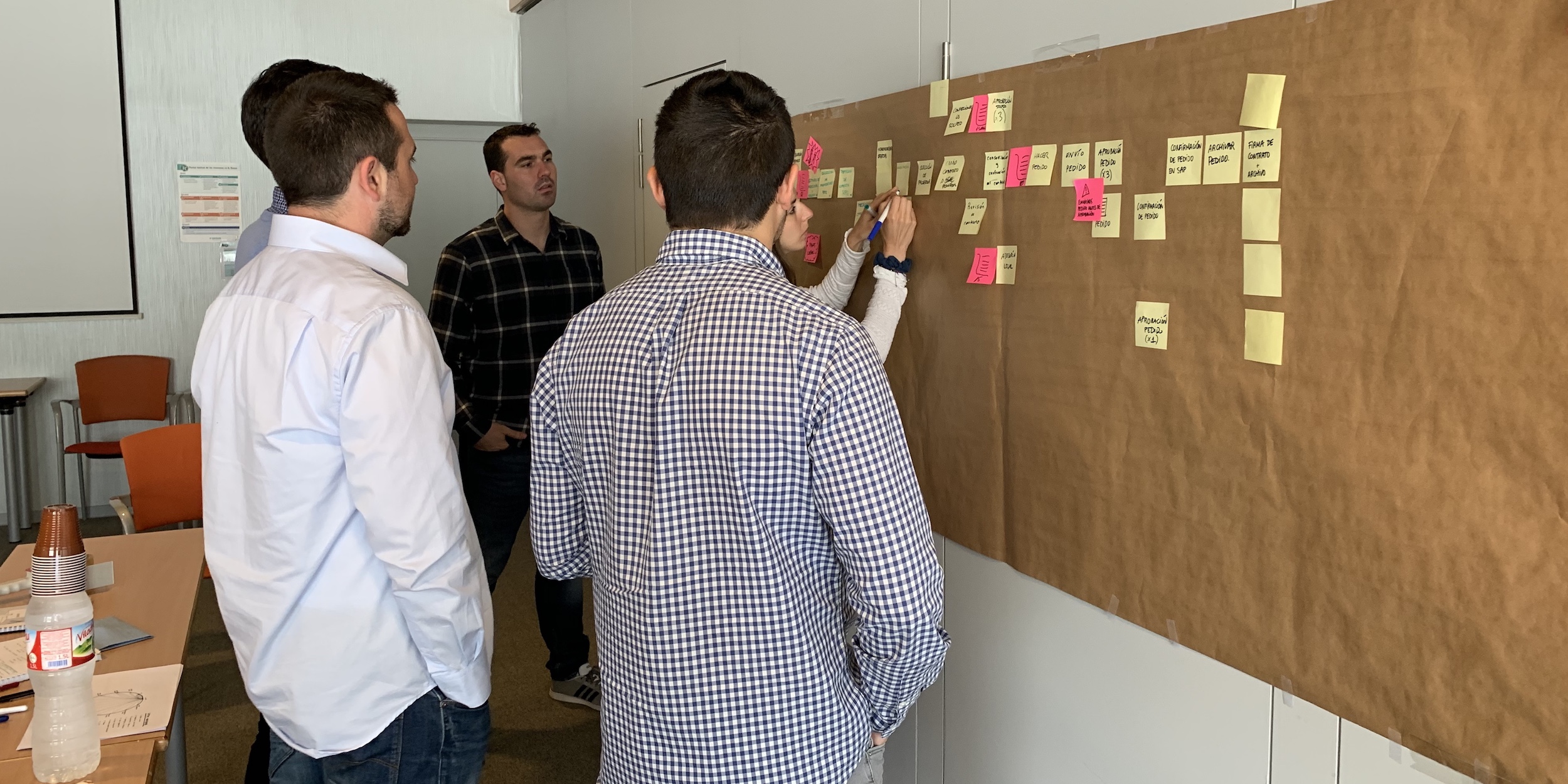
Avoiding the most common mistakes with VSM
THE NAKED GEMBA – Value stream mapping is a fundamental tool in any lean transformation. The author takes us the most common mistakes companies make using it, so that you can avoid the pitfalls.
Words: Severino Abad, Lean Coach, Instituto Lean Management – Barcelona
When we are faced with the challenge of transforming our processes in order to deliver value to the customer, we need to have tools at our disposal that will help us make the right decisions. Getting to know how the process works and to detect interruptions in the flow is particularly important to achieve our improvement goals. This is why Value Stream Mapping is a fundamental tool for any lean practitioner.
We are lucky to have many resources to tap into as we try to understand how to make use of this tool, starting from the book Learning to See by Mike Rother and John Shook (essential reading by two of my favorite lean authors).
In this piece, I will share some of the lessons I have learned about the implementation of Value Stream Mapping over the course of many years and in many different environments.
First, we need to understand what this tool brings us:
- VSM allows us to simultaneously visualize the flow of materials and information, through the flow of the process leading to the delivery of the value the customer expects. (In fact, Toyota refers to these maps as MIF - Material and Information Flow.) The goal of this representation of the flow is to identify waste. Moreover, as a good lean tool, VSM relies on standard symbols that make a map readable by anyone, whether or not they know the process at hand.
- VSM established a common language that is used to find synergies among the activities necessary to create value. Think about this: when we talk about process flow, we are talking about process engineers; when we talk about material flow, we enter the realm of supply chain; and when we talk about information flow, we are really referring to logistics. We are all aware of the problems stemming from the difficulty in communication that often exists among different company departments (this is linked to both the fact that departments report to different people, who might very well have conflicting objectives, and to the fact that they typically use different indicators to evaluate their contribution to value creation). A tool that aligns different functions helps us to bring out the best in each of them.
- VSM allows us to focus on a critical element in lean thinking – lead-time – and helps us to identify which places, activities or management approaches significantly contribute to influencing it – and whether or not this contribution is positive in the eyes of the customer. In this sense, through lead-time, VSM also allows us to evaluate the situation of a process from an objective and quantitative point of view.
- VSM enables us to create a plan for the transformation of a process, by helping us to evaluate first thing the effort and impact that each improvement opportunity will have – thus ensuring the success of the transformation.
THE MOST COMMON PROBLEMS WITH VSM
So, what are the difficulties most commonly encountered when one tries to create a Value Stream Map? (To learn how to actually draw such a map, I once again encourage you to read Learning to See.) For me, one of the hardest things to do is differentiate between “how things happen”, “how we say things happen”, and “how things should happen”. This is a huge problem: the further away we move from reality and from what takes place at the gemba, the deeper we dive in the dark underworld of uncertainty and, worse, discussions and looking for culprits rather than root causes. We are not used to correctly “seeing” what happens around us, and too often we base our observation on guesses, interpretation and assumptions coming from our previous experience. All of this leads us further and further away from the reality of the gemba. But if we can’t reflect on how things truly happen, how can we agree on the best way to improve our situation?
The situation described above worsens when we have to quantify things like takt time, cycle time of operations, first-time quality, OEE (Overall Equipment Effectiveness), changeovers, batch sizes, or even the size of intermediate stock. Sometimes it’s a miracle we can still manage the process, despite all this! When real information is missing, we tend to use averages or worse, the numbers someone had put together when they tried to complete an analysis of the process.
A critical lesson for me refers to that person – let’s call him Manolo – who is able to greatly influence the different flows in the processes to the point that he can change the production plan (because he knows a more efficient way of completing the work) or change the strategy around materials supply (because he is able to foresee future problems). It is very important that this person be included in the VSM exercise, at least in the definition of the current state. Otherwise, we won’t be able to understand the real mechanism of the process and the tools won’t tell us where to attack. You might wonder how you can find Manolo in your organization. It’s easy: when he is on holiday or on sick leave, the process works in a completely different way or doesn’t work at all.
Another risk inherent to VSM activities is getting lost in the detail. It is tempting to go from 0 to 100 in a couple seconds, from not having mapped any process to wanting to map everything. This is, however, very dangerous for the team because it can lead to analysis paralysis rather than mapping the flow. There is a reason we decided to map a certain process – it’s what we need to “change” to provide value to customers – so we must avoid the “what ifs” and “what abouts”.
Another potentially dangerous situation we can find ourselves in is disconnecting the process of mapping the work and identifying waste from improvement and problem-solving activities. The risk here is to frustrate the teams who took part in the VSM exercise by not allowing them to pursue the opportunities for improvements they worked hard to uncover. By tying the two processes together, we would always know the potential impact of a project before getting started and use the value stream map to prioritize accordingly.
At times, I also see VSM used more as “decoration” and as a tool for information-sharing than for functional purposes. It’s all too common to find companies that believe that Value Stream Mapping has to be completed one time and that after that rely on the very first iteration of the map to inform and develop people. A good value stream map, however, is alive – reflecting the changes in our processes over time. This misunderstanding on the potential of VSM inevitably leads to information becoming obsolete (either following process improvements that changed the initial situation or, indirectly, because of the deterioration of unsupervised processes). Furthermore, when we merely use this tool to “explain how we work” we are not rewarding the giant effort made by our people to capture information at the gemba.
In the same way, limiting the VSM activities to certain functions in the business will necessarily result in a limited vision of the “reality” we face in our processes, which in turn will affect the results we can achieve. This approach turns a value stream map into another reason for conflict among people who no longer feel part of the results and conclusions achieved (when it could have been a document facilitating the vision of our current and future state and creating consensus on the measures to take to move from one to the other).
Finally, it’s common for organizations operating in non-manufacturing sectors to struggle to adapt VSM to their environments, where flows are typically less linear and homogeneous as they are in a production setting. So, how we map processes in an office, for instance, or in the development of projects? How can we reflect in our map the fact that the main interruptions in the flow occur when the process moves from one department to another? This is normally not an issue in manufacturing, where activities tend to either be “departmentalized” or affects flows that are mapped in the VSM. When it comes to describing these processes in non-manufacturing environments using the techniques used in manufacturing, I have witnessed some wonderful creative thinking over the course of my career. A great way to map processes and their interactions in complex environments is using swimlane diagrams (also known as makigami in Japanese) to indicate which function or department an activity refers to and separating them in lanes. This tool is particularly useful in environments where we are trying to map information flows.
In conclusion, Value Stream Mapping is a fundamental lean tool, but its application doesn’t always lead to the expected result. I hope this article helps you to avoid some of the most common pitfalls lean companies encounter when they try to implement it.
To learn more about Value Stream Mapping, don't miss Learning to See.
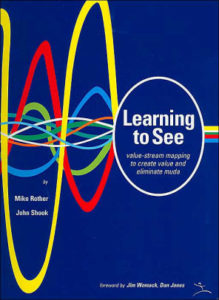
THE AUTHOR
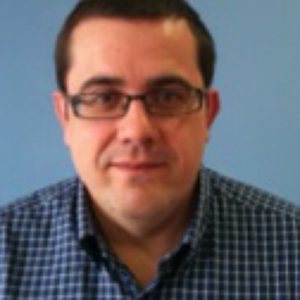
Read more
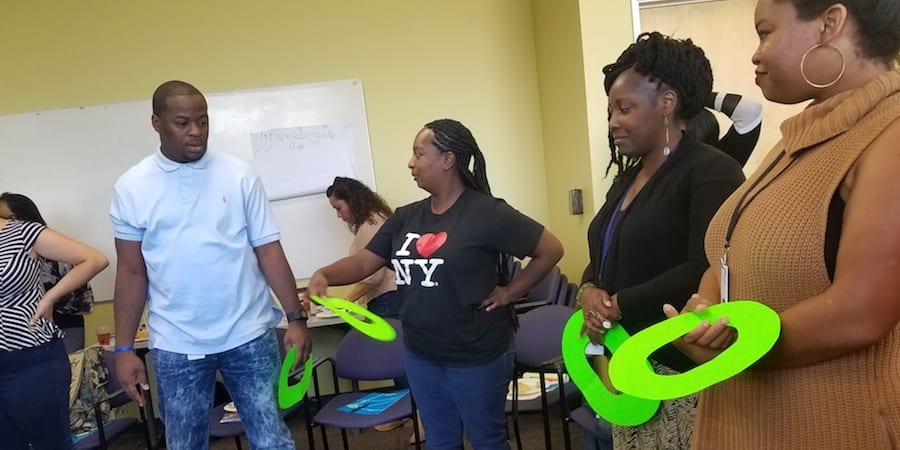
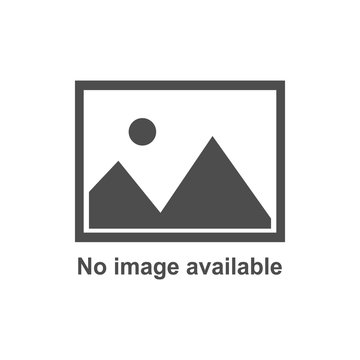
INTERVIEW – An organization in the San Francisco Bay Area is using coaching to increase its impact on the lives of foster youth. We had a chat with an extraordinary group of women to learn how they are doing it.
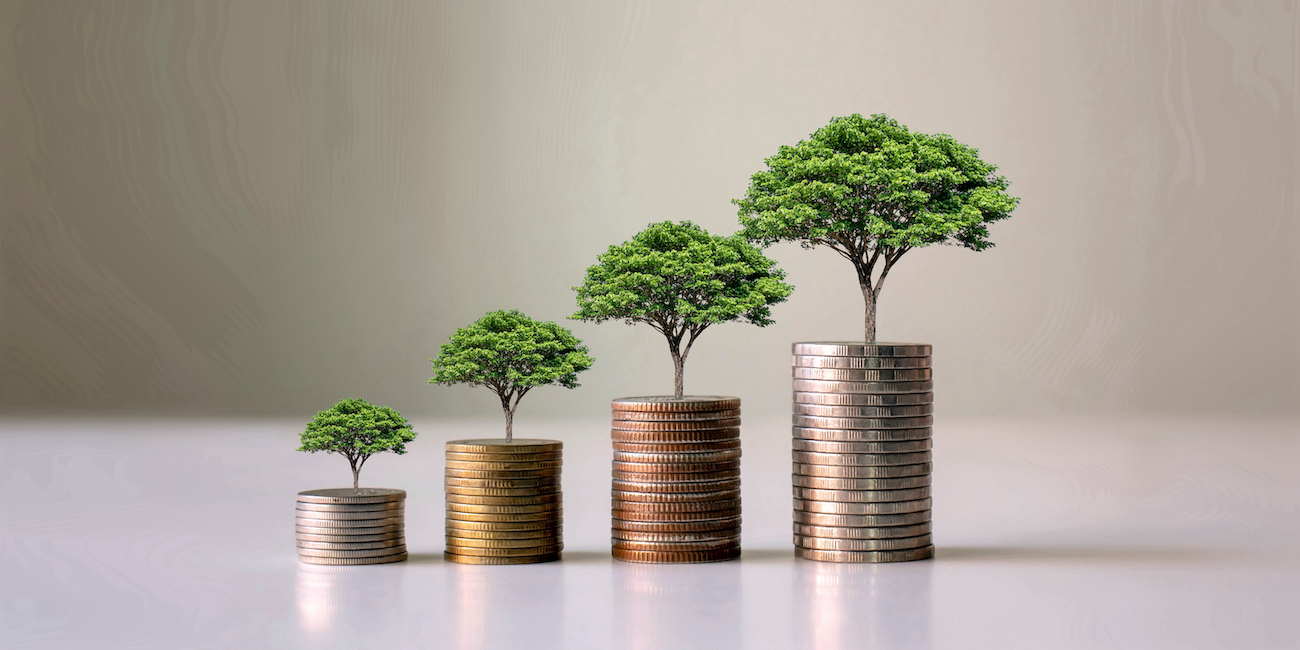
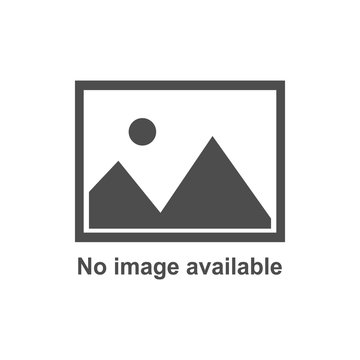
FEATURE – The impact of humankind on the environment is now beyond dispute. Yet, too little is being done to adapt our business models. This compelling read explains why we need to create prosperity beyond profit.
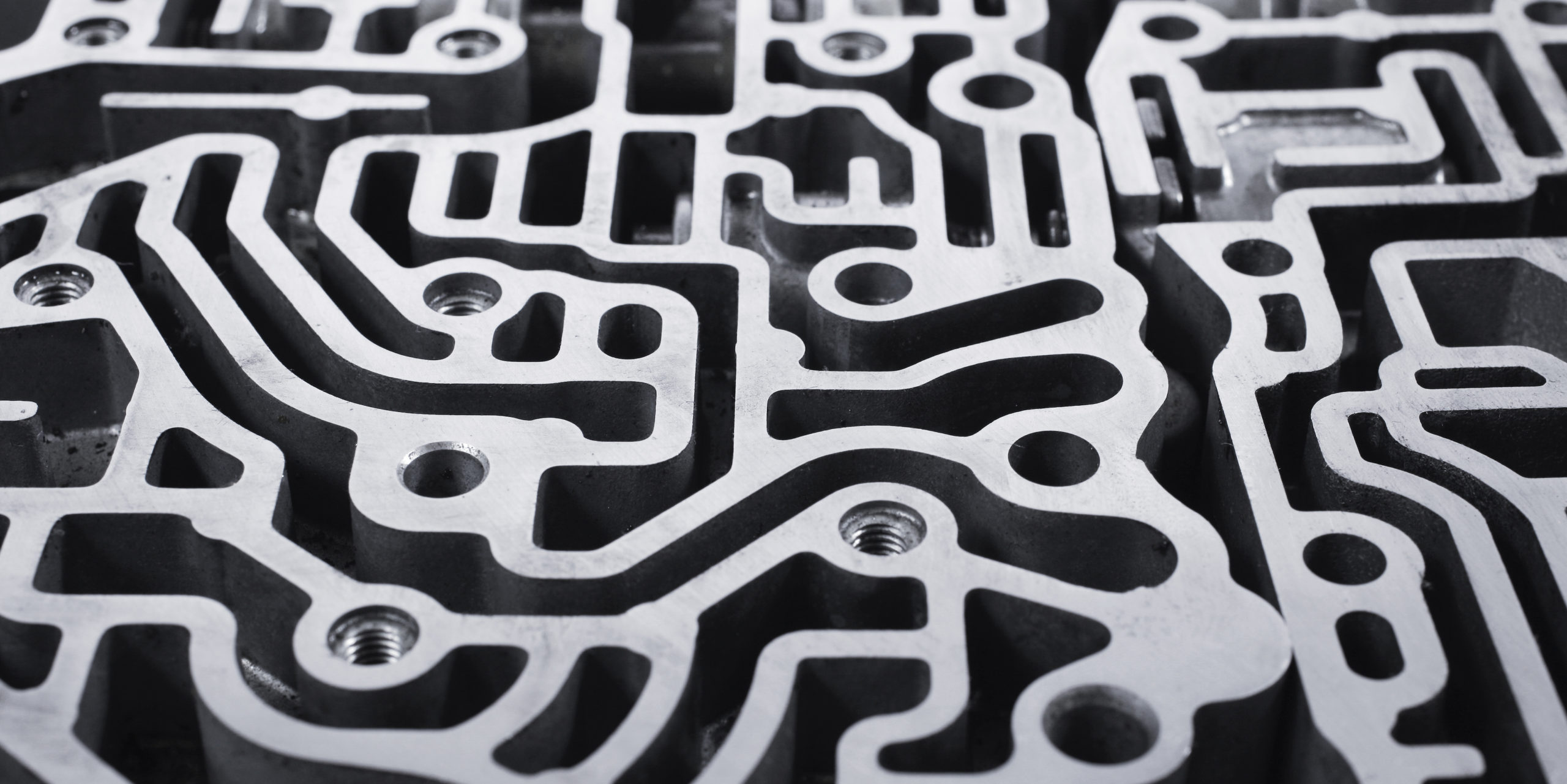
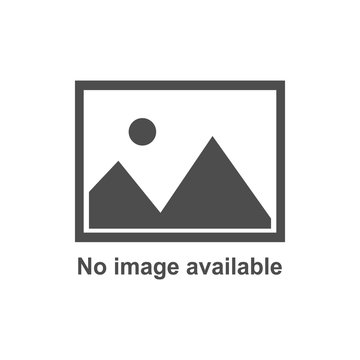
FEATURE – In a market where products become obsolete very fast, this Toyota supplier has learned the importance of staying true to its heritage and developing know-how and people’s capabilities.
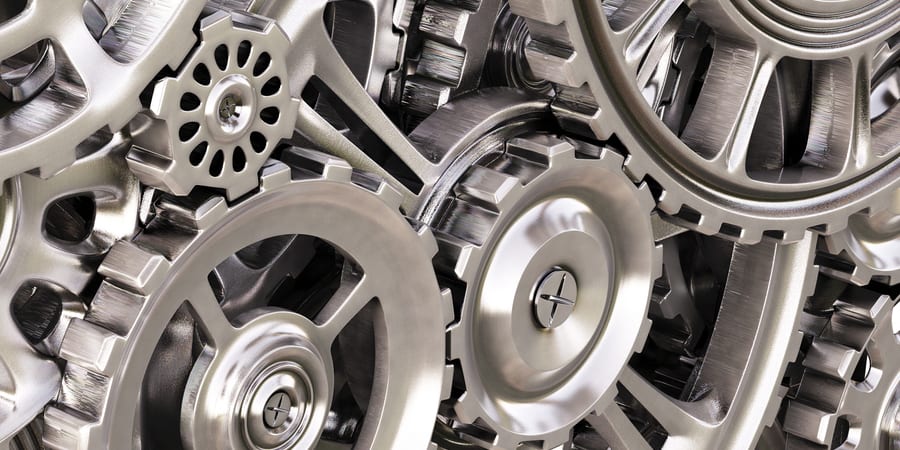
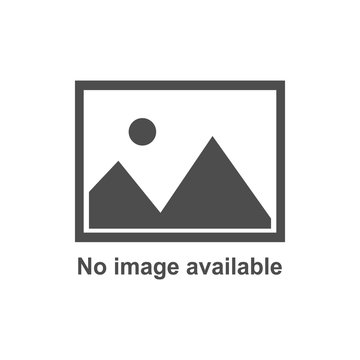
90-SECOND Q&A – At a recent summit, our editor Roberto Priolo sat down with Durward Sobek to discuss design thinking, obstacles to the application of lean in product and process development, and why LPPD in services is a bit different.