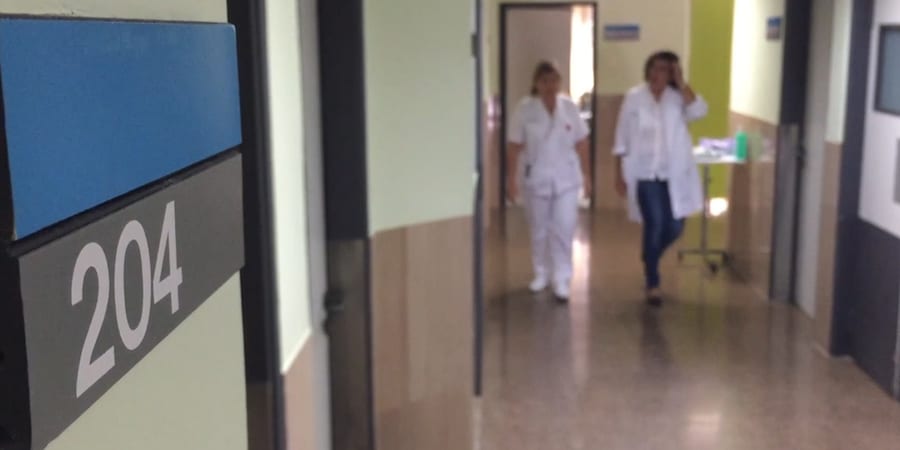
Transforming your hospital using lean thinking
VIDEO CASE STUDY – In the past couple of years, the Consorci Sanitari del Garraf has been able to leverage the commitment of its people to perform a lean turnaround. Its story shows you don’t need lots of resources and money to do lean in a hospital.
Words and interviews: Roberto Priolo, Editor, Planet Lean; video commentary: Prof Daniel T Jones, co-founder of lean movement
Extra support by: Oriol Cuatrecasas, President, Instituto Lean Management
Music in videos courtesy of: http://www.bensound.com
In 2009, three medical facilities in the comarca del Garraf, near Barcelona, merged into one organization, the Consorci Sanitari del Garraf. Faced with a 17% budget cut, a result of the financial crisis, the newly created hospital had to find a way to improve its processes and become more efficient.
In just a year, lean thinking led to a revolution in the way the hospital is managed. The videos in this case study will take you through the transformation of CSG, and prove how a hospital doesn’t necessarily need a lot of extra resources (and money) to “do lean.”
But first, what does lean look like in a hospital? According to Professor Dan Jones, lean in healthcare means:
- Improving the quality of care and the patient experience;
- Simplifying tasks for providers;
- Better utilizing resources (equipment, beds, nurses and doctors, etc) so that we can treat a growing number of patients with existing resources.
Transforming a hospital (or any organization really) and making it a lean enterprise requires the continuous improvement of the work, the development of people, and the full commitment and enthusiastic involvement of leadership.
PROCESS IMPROVEMENT
So, how did the CSG change its processes in order to provide for better care with the same amount of resources?
The first experiments with lean took place in the Surgery Department, which volunteered to try out the new approach.
Prior to the budget cuts, the department was performing operations in the afternoon to absorb the long waiting list. After the cuts, however, this was no longer allowed (ORs could only be used in the morning), and the team had to find a way to complete the highest possible number of procedures in the morning.
This short video explains what happened in Surgery when lean was introduced.
The results achieved in Surgery encouraged other areas of the hospital to come forward, and before long the lean improvements spread to Intensive Care and Emergency Department.
The higher number of operations had resulted in a need for extra space in the Intensive Care Unit. The organization had to become faster in getting patients out of surgery and into the unit, which was always at full capacity. They had to get better at discharging patients.
The goal (which CSG had had for quite some time) was to discharge as many patients as possible before 12pm. To achieve it, the hospital re-organized the entire working system for the Intensive Care Unit, introducing new standards of work for nurses and doctors.
This way they managed to re-establish the flow of patients, both those coming in from Emergency and those getting out of surgery.
The following video, from which you can draw inspiration for your own lean improvements, explains some of the changes implemented in the Internal Medicine ICU and in the Emergency Department:
PEOPLE DEVELOPMENT
No lean transformation can succeed without the involvement of the people performing the work. At Garraf, the workforce is extremely engaged to improve patient care, which means that it will be much easier for the hospital to sustain results.
In the following video, we look at the development of people at the Consorci, which began with the creation of a lean implementation team and with the design of bespoke training courses that would help people understand what lean is and why it could make everyone’s life better.
It is the way of managing that has changed completely. Top management now listens to people, encouraging them to find solutions to problems and coming up with improvements.
In the following video, Planet Lean speaks with two members of the board of the hospital, the Medical Director and the Deputy Director of Nursing.
WHAT WAS THE ROLE OF LEADERSHIP?
The role of leadership in a lean transformation is about supporting and enabling the front line to solve their own problems. At CSG the CEO, Josep Lluís Ibáñez Pardos, already had experience with consultants-led lean programs in other hospitals, and when he was faced with 17% budget cut he was determined to create a lasting solution in his hospital. He wanted to help, mentor and support his people (together with Instituto Lean Management) so that they would be able to lead the change. This way the Garraf people owned the results of their hard work, and were able to sustain them.
Mt Ibañez Pardos commented: "Our focus was on the cultural transformation, not on short-term savings. In time we managed to make lean part of mechanism of CSG, part of its DNA, by concentrating on our core business: the quality of care, and being good doctors and nurses.
"My role as CEO is to back people and to be available whenever a problem arises. It is my responsibility, after all, to create a sense of need for change and to encourage the whole organization to embrace lean. In order to do that, a CEO must be fully committed and convinced – if not, getting others on board will be impossible."
WHAT DID THE HOSPITAL ACHIEVE?
CSG was able to achieve great results in a number of departments, including shorter waiting times, an increased number of discharges, and a more efficient Surgery Department.
However, as Quality Director Rosa Simón Pérez says in the following video, the biggest change was the fact that people have learned what teamwork means.
More details on the results the hospital was able to achieve in the last video of this case study:
This case study shows how small to middle sized hospitals don't necessarily need lots of money and extra resources to apply lean thinking. With the right mentors and the right approach to people engagement, they can do it on their own.
THE AUTHORS
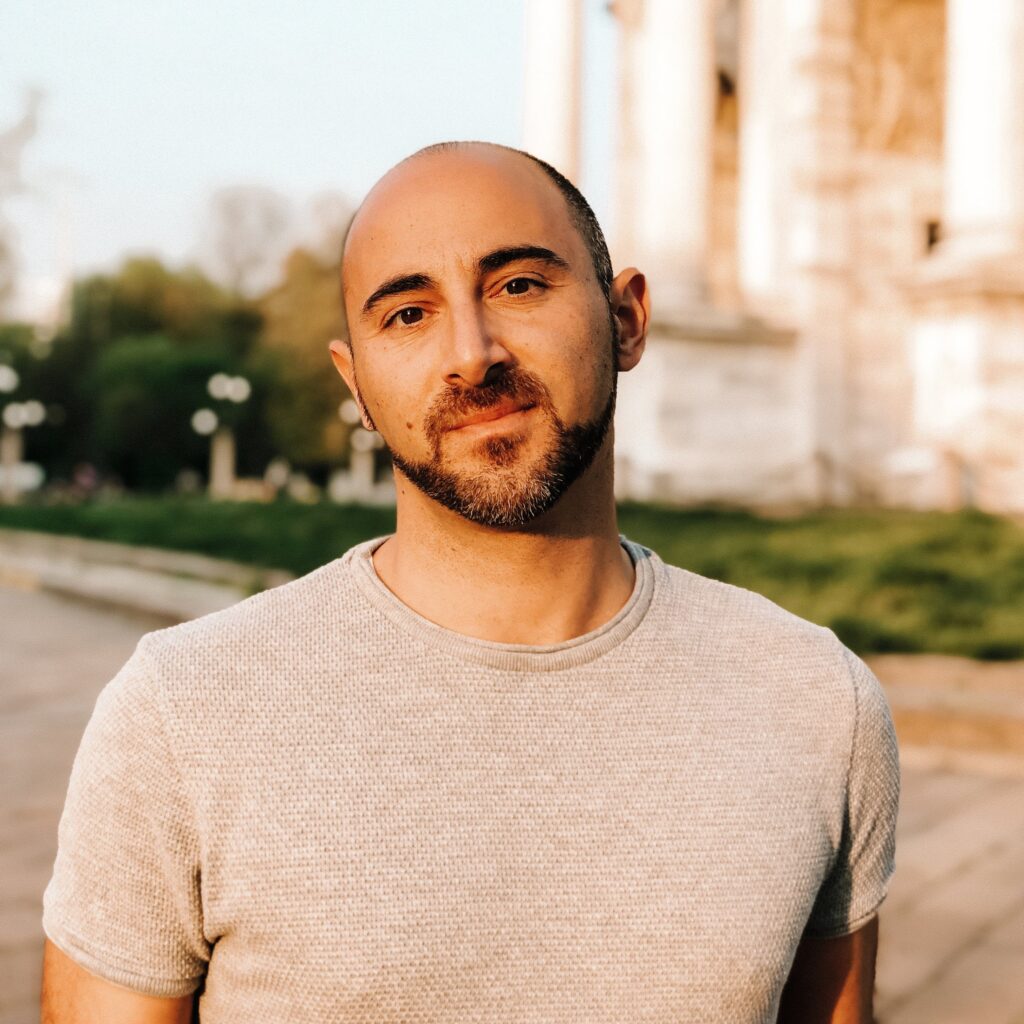
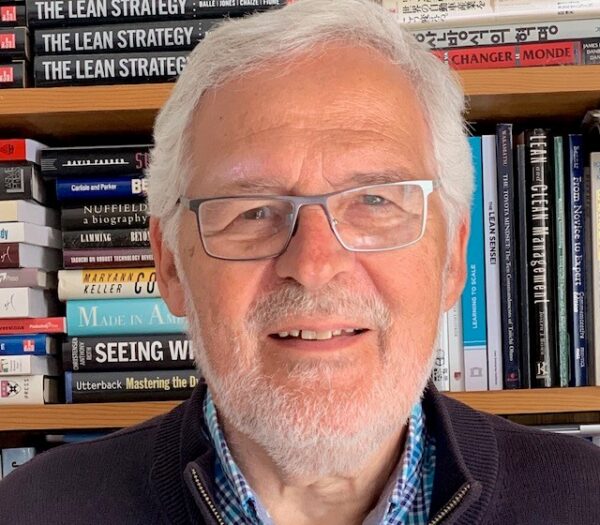
Read more
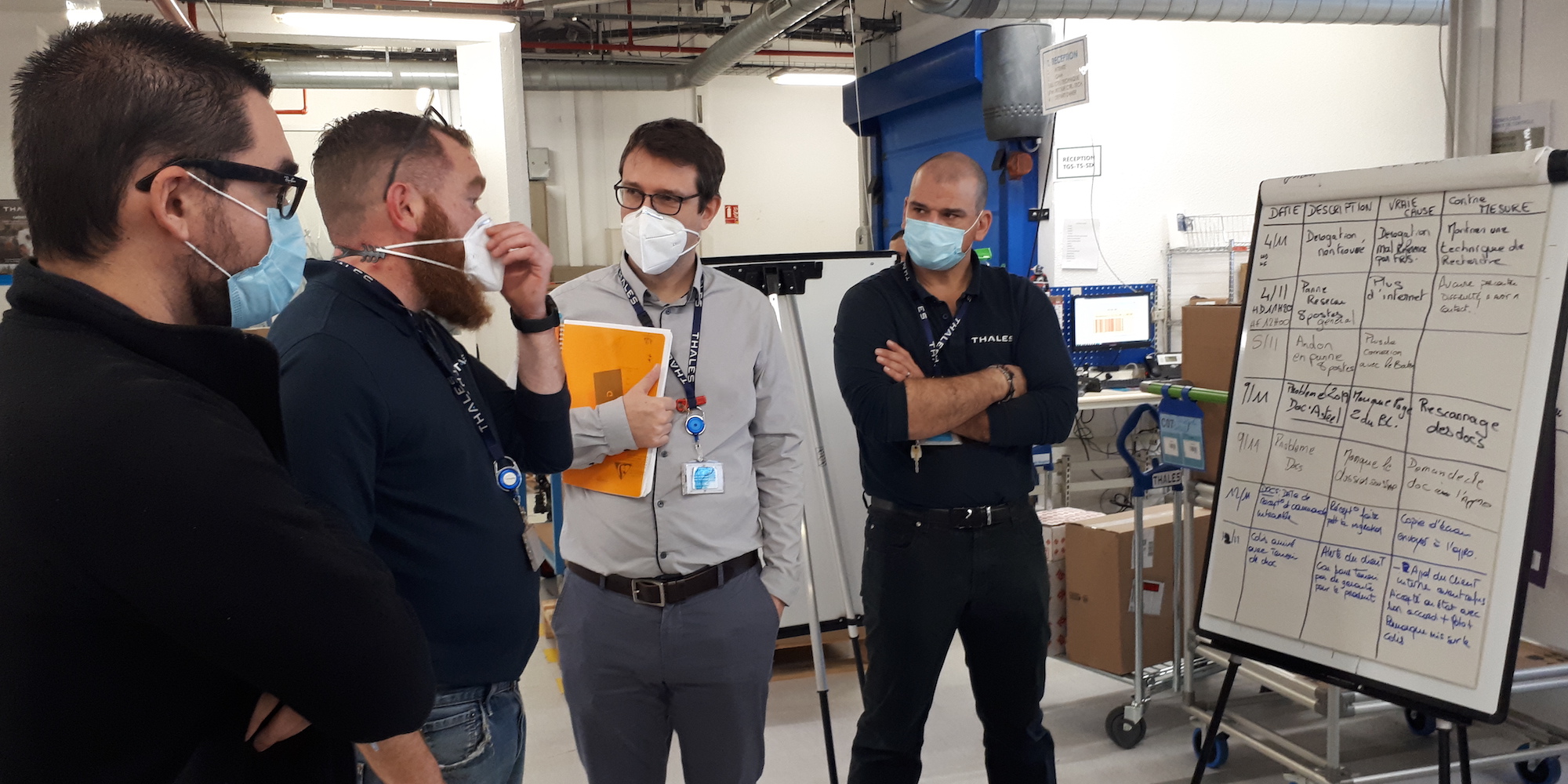
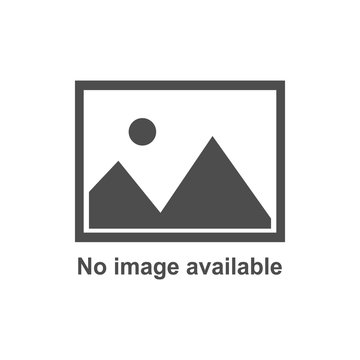
NOTES FROM THE GEMBA – Thanks to the effective application of Just-in-time and Jidoka, Thales LAS has managed to turn around its logistics department. Catherine Chabiron reports.
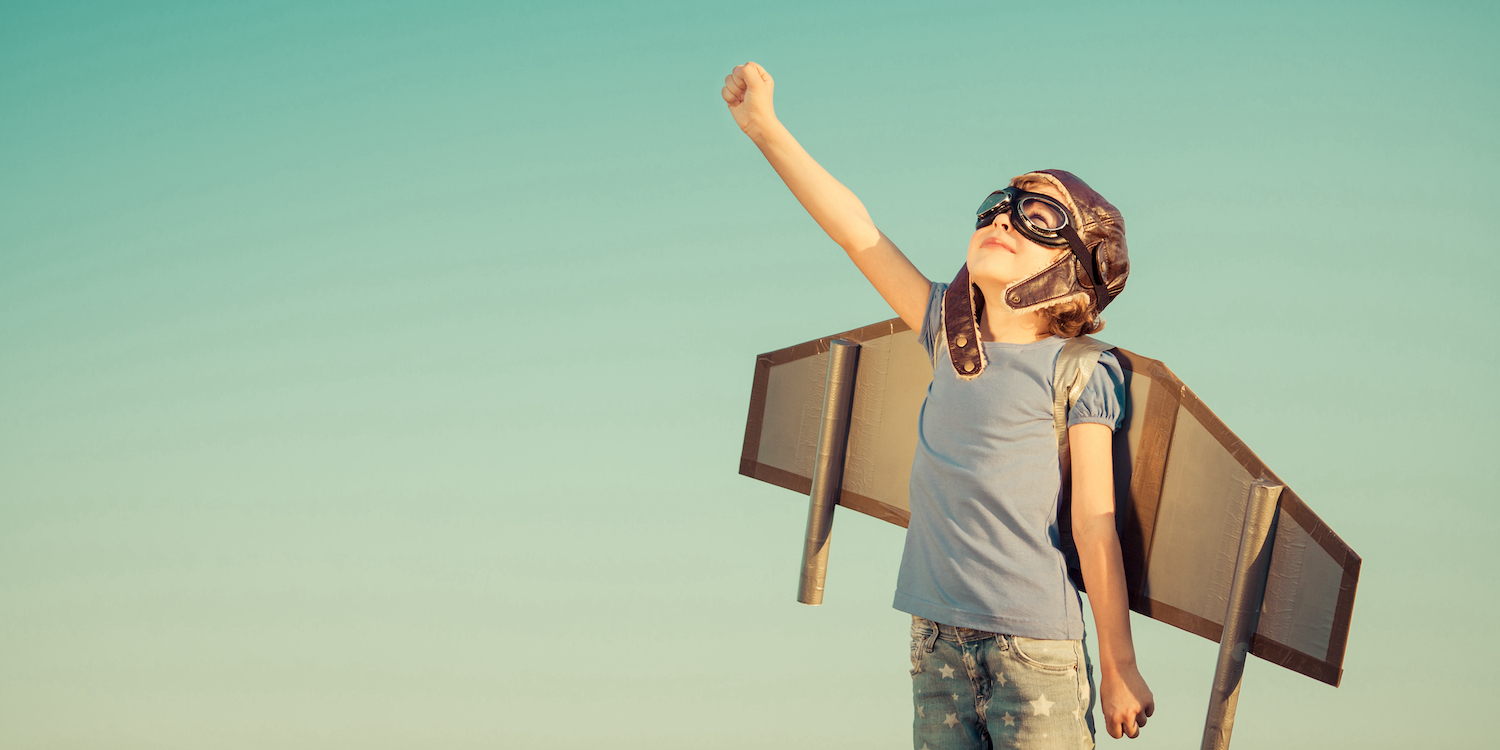
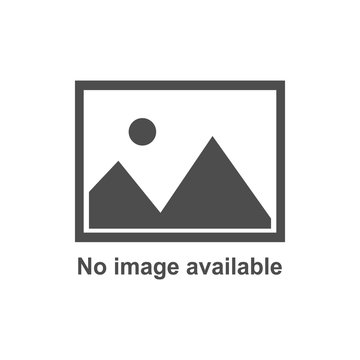
FEATURE – In this new series, the author will walk us through some uncommon ways to apply lean – with a particular focus on establishing productive and enjoyable relationships. In the first instalment, he introduces the concept of lean parenting.
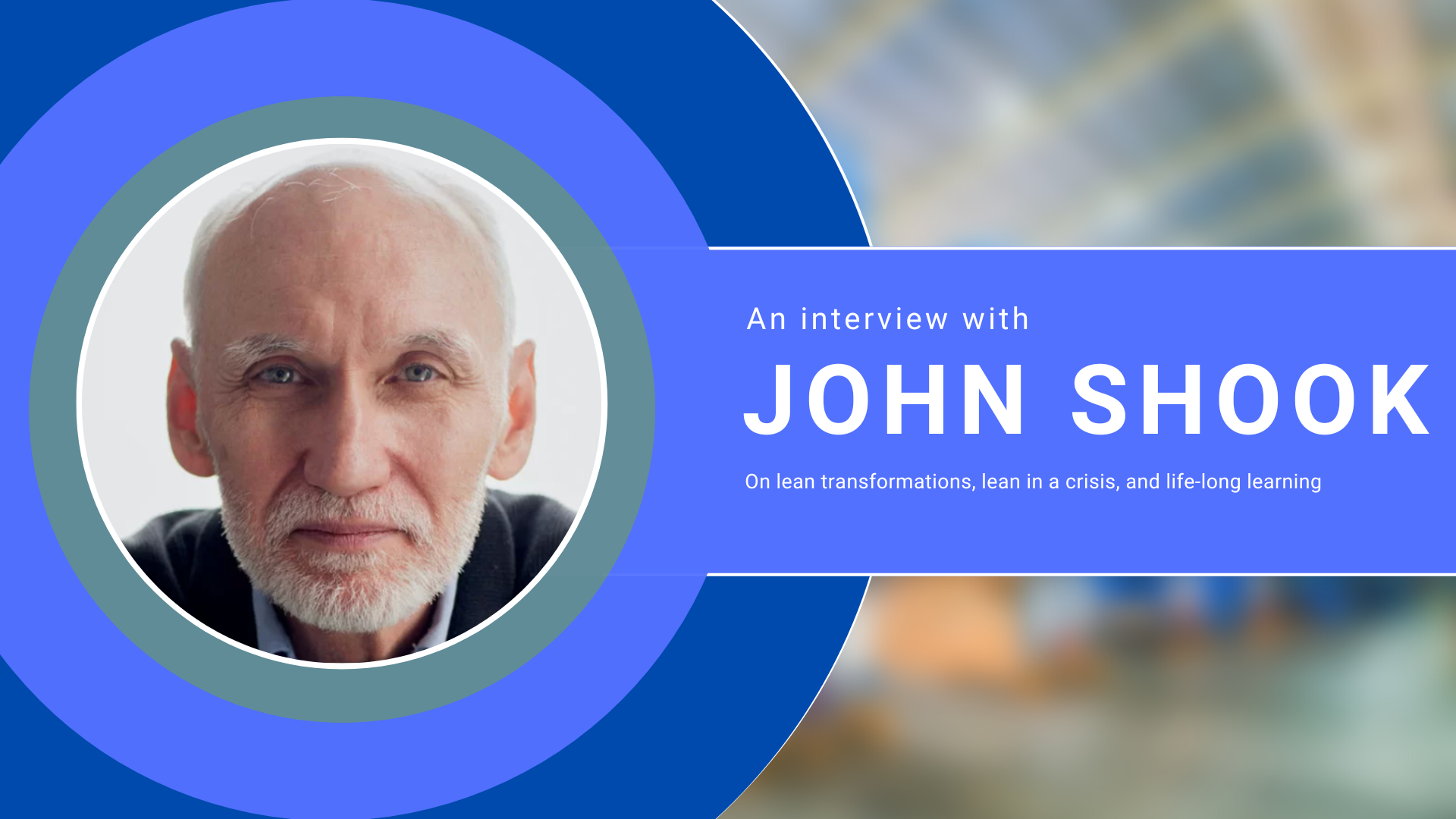
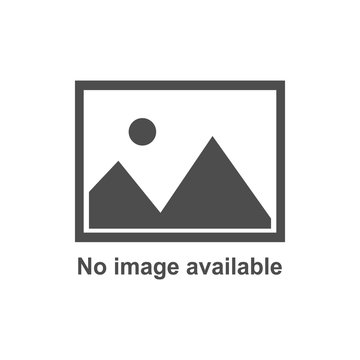
VIDEO INTERVIEW – We recently caught up with John Shook at the Lean Healthcare Academic Conference in Stanford and asked him to share his thought on the questions we need to ask ourselves in a lean journey and on lean in turbulent times.
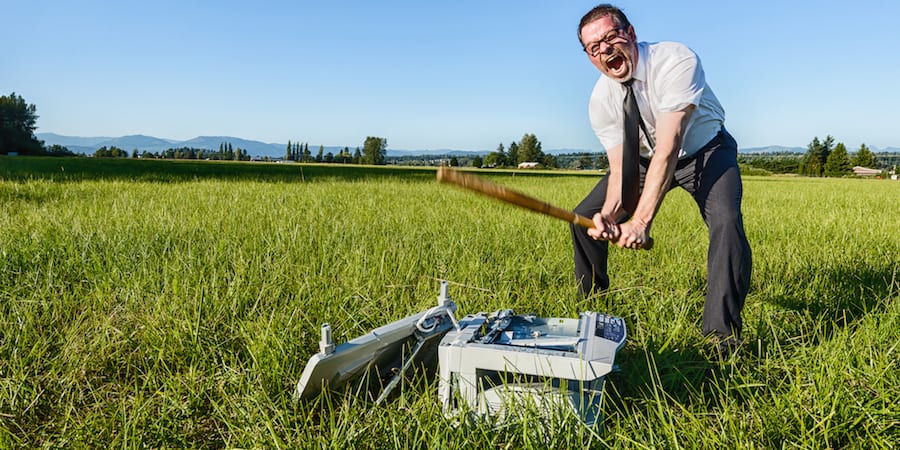
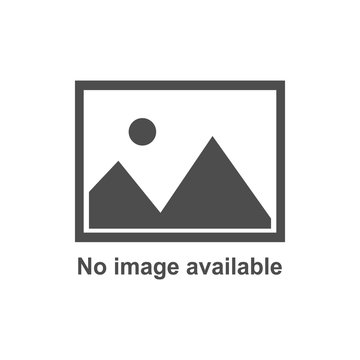
FEATURE – A broken phone or a clock showing the wrong time may seem small details to you, but they actually make people's jobs more difficult. Fixing these issues improves work and boosts morale... It also says a lot about you as a company.