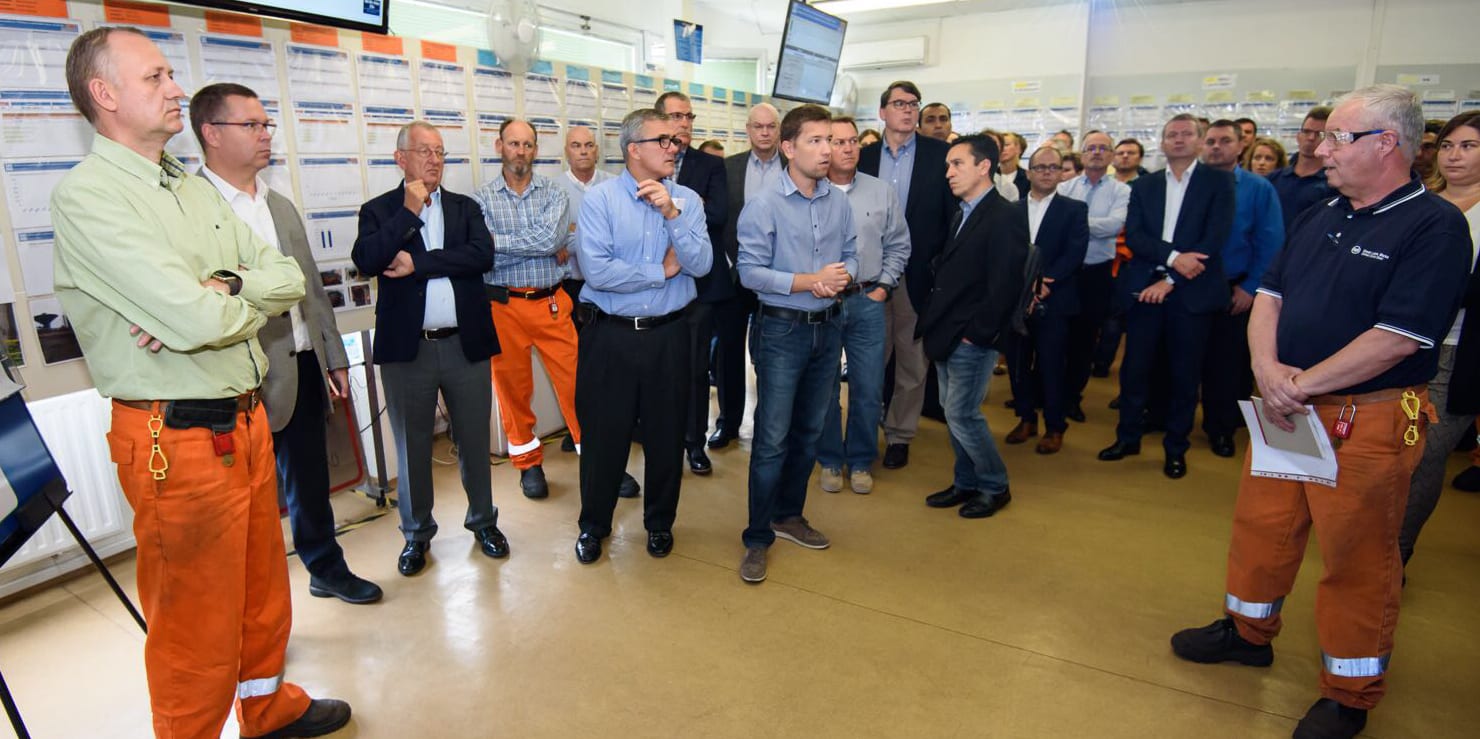
When a top exec becomes the lean manager
OPINION – What happens when a senior executive jumps the fence and finds himself having to drive the very same lean management transformation he was asking others to take on?
Words: Jan Petko, General Manager of Process Technology Excellence, American Steel – Slovakia
Twenty-two years ago, I started my career at American Steel as a shift manager. Over time, I have moved up the ranks, with my first experience as a general manager in 2010. For five years, I managed Production Support, Maintenance Reliability and, finally, operations for US Steel’s “daughter companies” in Slovakia.
In 2015, my job title changed dramatically. I became General Manager of Process Technology Excellence – in essence, I am responsible for the application of lean principles and techniques in our operations. You could say that I have “jumped” the fence, suddenly finding myself having to drive that change that, as a top manager, I had been supporting but had not directly gotten involved with.
One of the first things I noticed – it was a great surprise – was a tendency of our lean coordinators to complain about the fact that operators weren’t appreciative of their efforts to improve our manufacturing operations. This is a common point of view in top management, one I was familiar with, but it was surprising to learn that lean coordinators were also thinking like this.
The reality is that in many cases line management and operators strongly oppose the implementation of lean (or any improvement efforts, for that matter). And you know what? It is absolutely natural. People don’t like change, which is normally associated with stress. When asked to change the way they work, operators will typically have a million questions in their minds: will I have to work more for the same money? Will they fire me? Will they transfer me to a different team? Will I have more rules to deal with?
In my experience, it is important to be aware of people’s fears and keep them in mind at all times during a lean transformation. As a former line manager myself, I fully understand the problems that people on the floor experience on a daily basis. They are always under a lot of pressure to meet the planned operational KPIs in terms of quality, productivity, cost and, critically, safety.
Therefore, the primary focus on my new job was to change the thinking and behaviors of our lean coordinators, so that they could earn the trust of line managers and operators. To break the barrier that was preventing change from taking roots in our organization, I encouraged coordinators to listen to the problems of the front line (you’d be surprised to see how different they are from the problems top management normally thinks are important) and set a vision of how things will change for the better once change is achieved. This is important to answer the oft-mentioned question, “What’s in it for me?”
Only at this point should they introduce the expectations of top management, remaining open to constructive criticism coming from operators. After all, they are the ones who will have to implement the change. I tried to explain to my lean coordinators that it is important people know that they are not left to face problems alone (whether or not these are related to the project) and that the improvement of processes will happen step by step. “Communicate, communicate, communicate!” I would constantly remind them.
COMMON MISTAKES LEAN MANAGERS MAKE
As we climb the corporate ladder, our belief in our own infallibility, wisdom, openness to new challenges and irreplaceability becomes stronger and stronger. I went down that path myself, and I have seen how dangerous such an attitude can be. (And how big a waste of time it is to try and change the mindset of bitter managers frustrated about having remained unnoticed.) Lean strives to change this dynamic.
As lean managers, we should never forget what our role actually is – shadow support. Rather than fearing being overlooked, we should gladly embrace our role of taking care of people. We need to see ourselves as their bodyguards: we appear exactly when we are needed, we are ready to sacrifice ourselves for our people, and we are not standing in the way.
When I first started as General Manager of Process Technology Excellence, I quickly realized that “lean specialists” tend to live in their own world, often quite far from reality. They tend to forget, for example, that their efforts must always be in line with corporate strategy, regardless of whether the focus is on productivity increase, quality improvement or cost reduction. The core value of our company, for instance, is Safety First and I often had to make sure that the coordinators always took this fundamental aspect into consideration.
Another common problem inherent to our job as lean people is so-called “paralysis by analysis”: corrective actions that are not perfect but that can be implemented quickly are better than perfect ones that takes ages to plan and execute. We should never forget that our role is to respond to issues and help people reach solutions as quickly as possible.
There’s more. I found it strange that, in a company where performance is measured at all management levels, lean facilitators worked without any specific performance parameters. How were they supposed to assess their performance? In trying to change this, I heard bizarre statements like “Mental work cannot be measured” or target definitions like “Our goal is to build a high-performance organization”. How is it that operations managers can’t just say that their goal is “to try and increase productivity”? How come do they have to be specific and lean managers don’t? Our goals, too, should include figures, for example “5% reduction in cost per ton” or “increase productivity by 10%”. Perhaps this reluctance stems from the fear of setting ambitious goals, but the truth is that the tougher the target, the happier one will be once that target is achieved.
My previous experience managing operations is helping me greatly now that I have to run the lean transformation of the department. To me, this is a reminder of the fact that lean is rooted in practice and that it can only be learned and communicated on the job. Delegating it to a team of experts alone is not enough, as traditional thinking can permeate their thinking just as easily as it can that of top managers. One more time, we need to change ourselves as managers (even lean managers) if we want to change people’s way of thinking.
THE AUTHOR
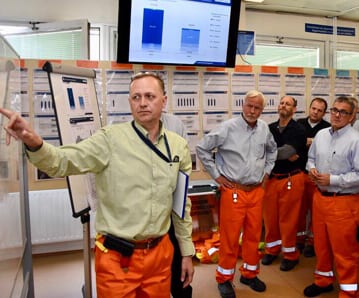
Read more
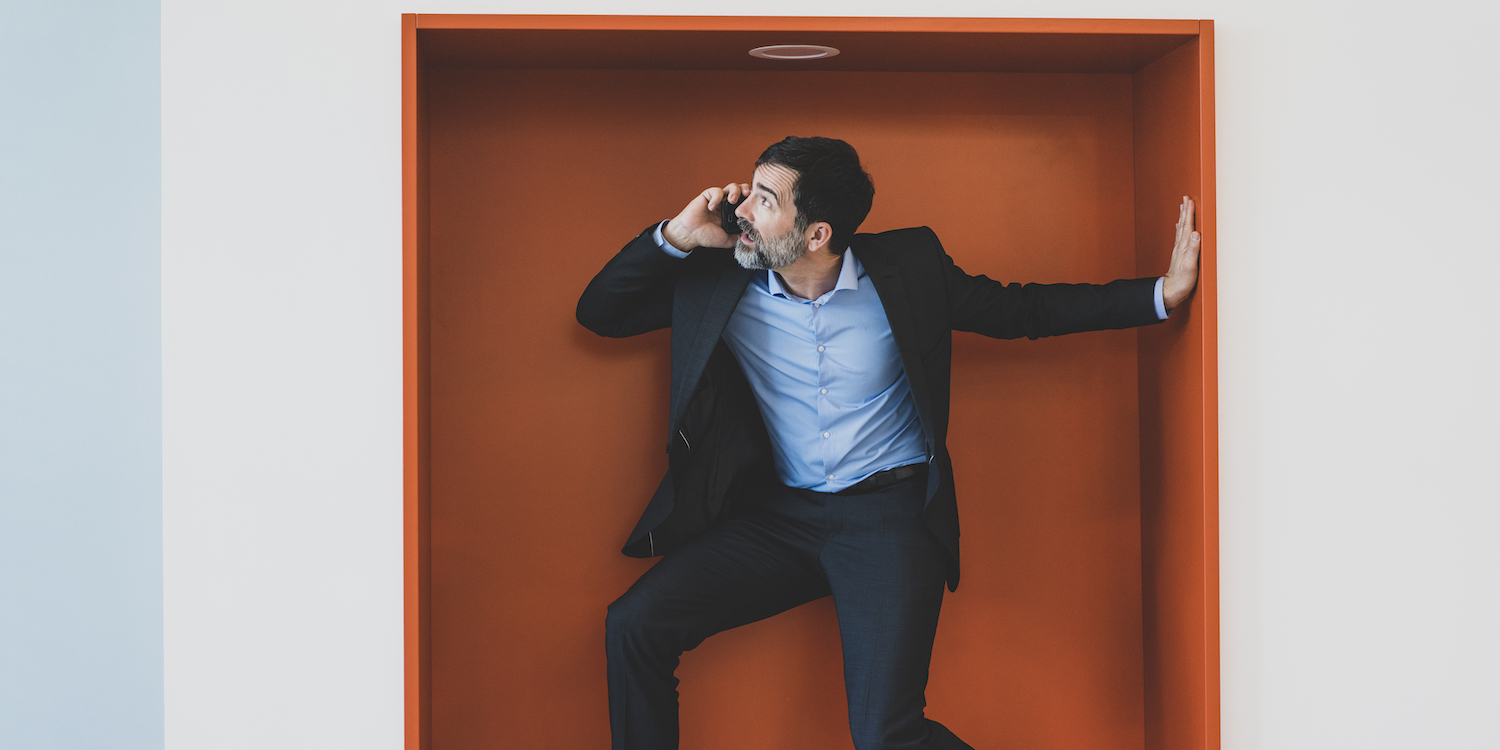
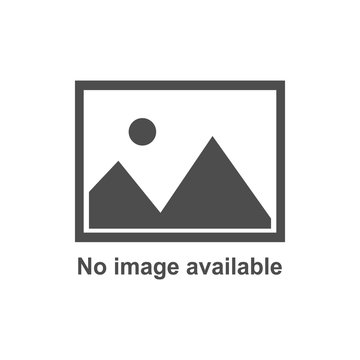
FEATURE – How does the improvement department of a company become a hindrance to the transformation? The author answers this question and discusses how this can be avoided.
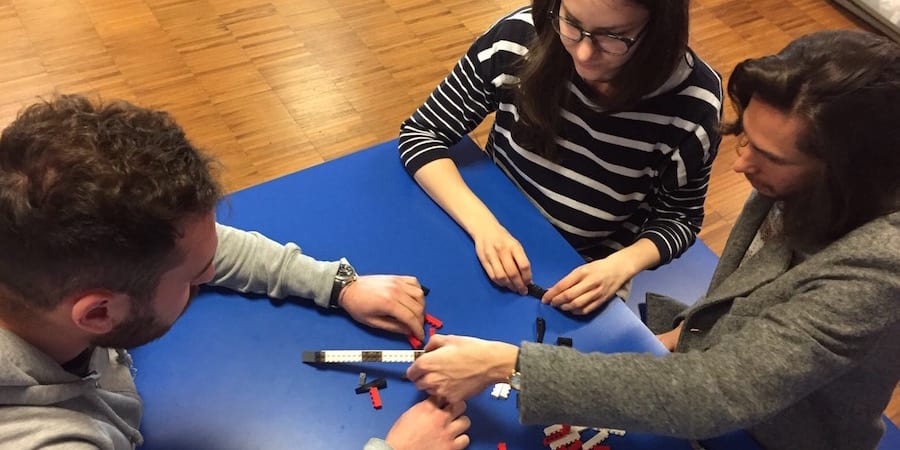
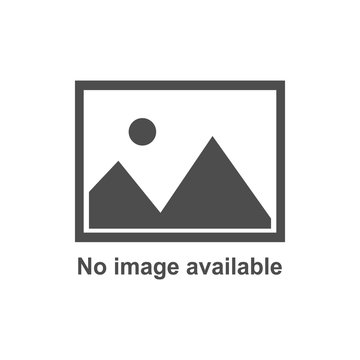
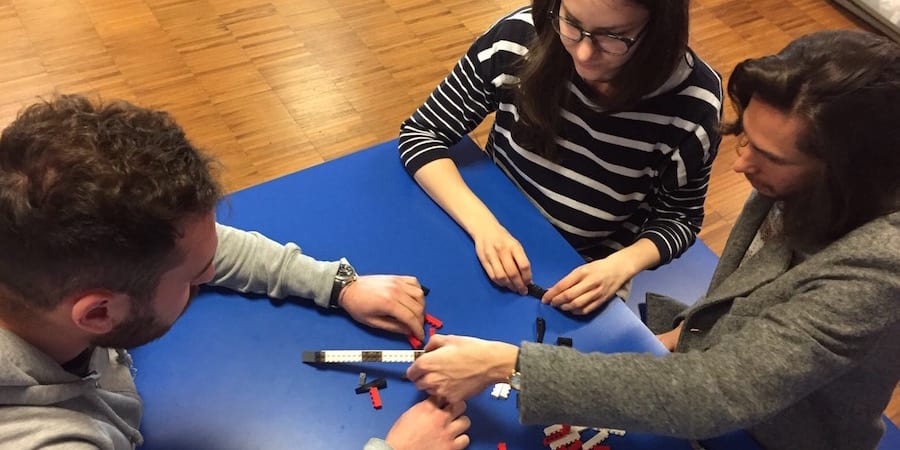
FEATURE – In a world of disruptive innovation, being faster and smarter at developing new products has become critical. The authors explain why set-based concurrent engineering is the answer, and why a game is the best way to learn it.
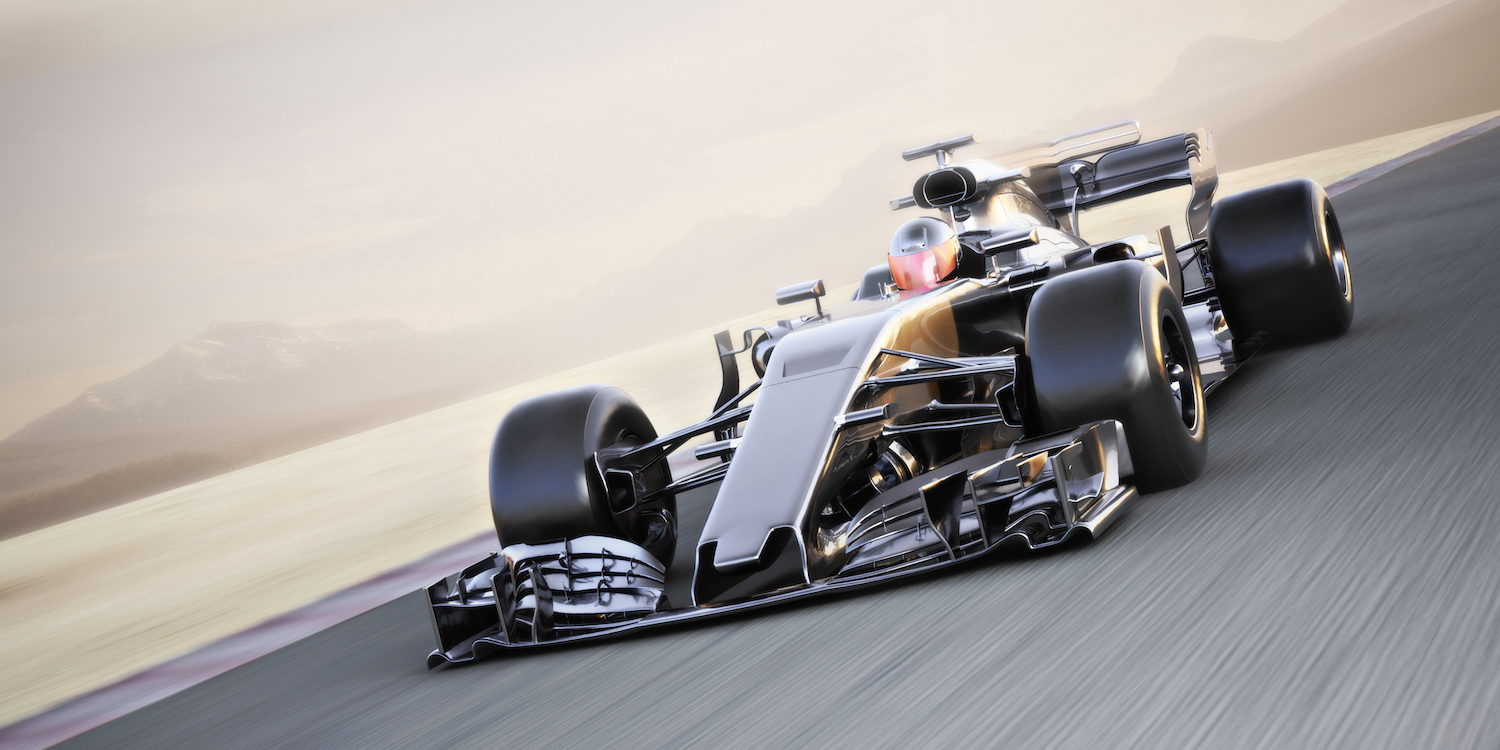
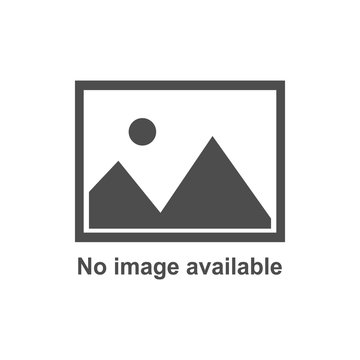
FEATURE – In part 2 of his article, the author unveils an improved process that allows this Hungarian company to replace machine parts with minimal production downtime.
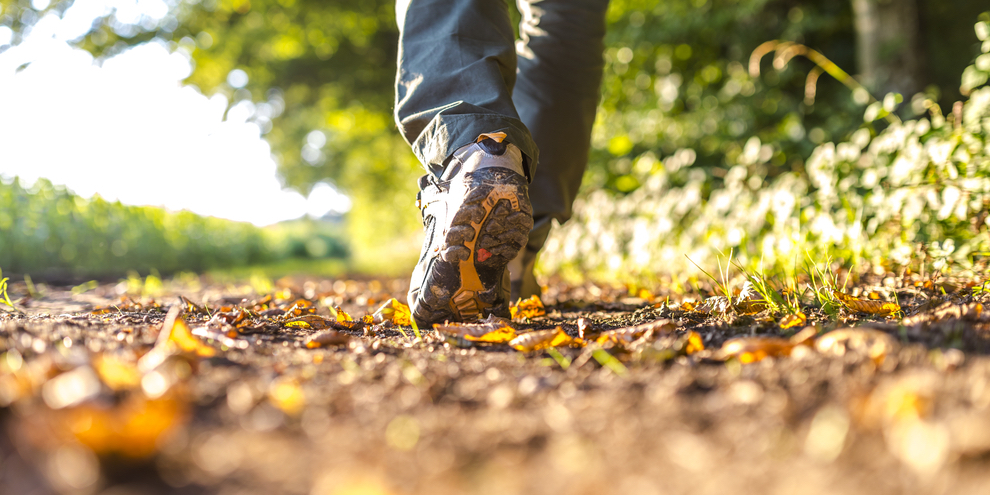
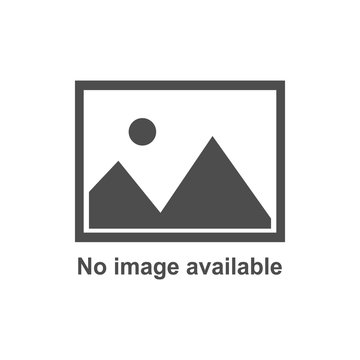
FEATURE – We assume that what holds our transformations back is the lack of high-price resources, but more often than not it is the simplest of items.