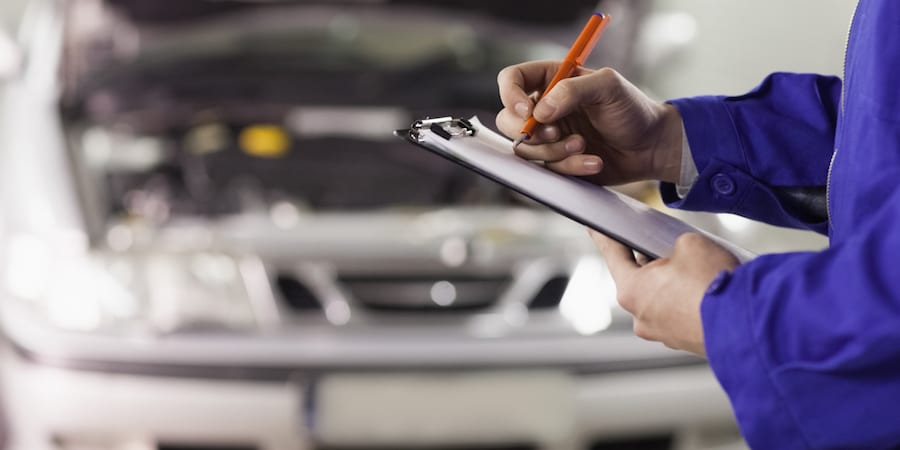
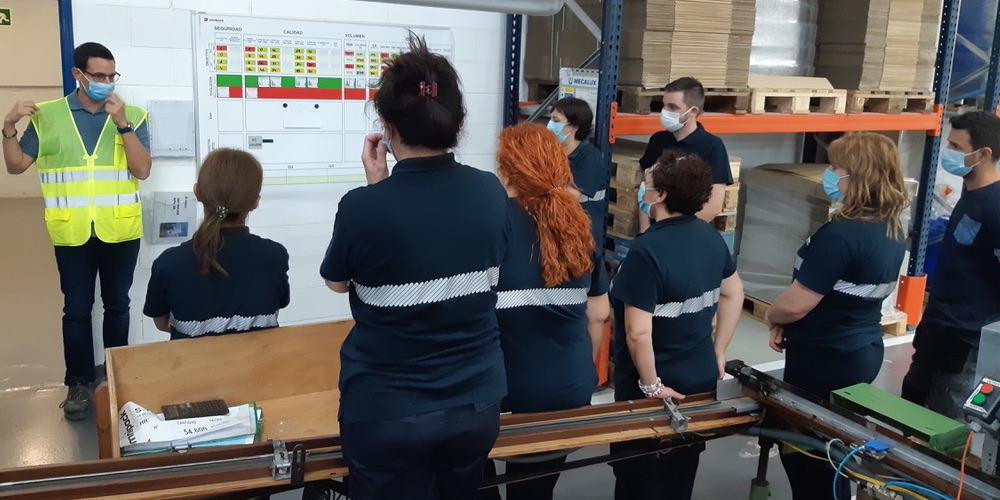
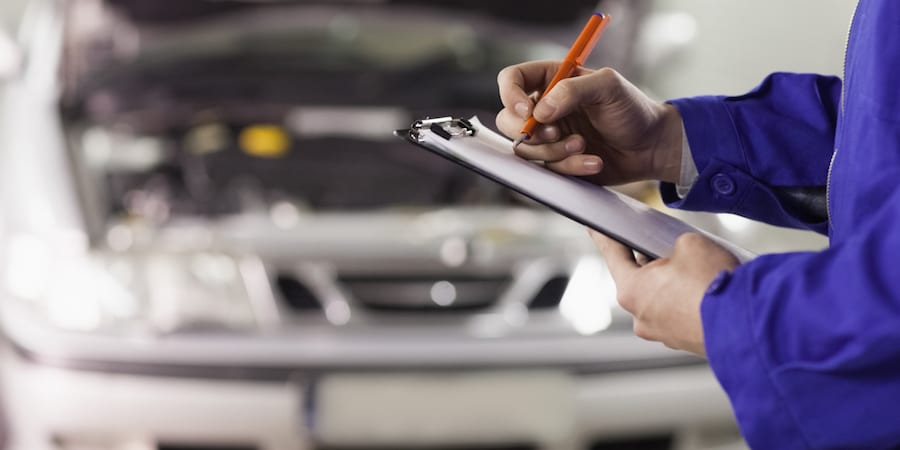
WOMACK'S YOKOTEN – In our lean journeys we spend so much time on improvement (kaizen) and innovation (kaikaku) that we often forget to address the issue of how to maintain our gains. Do you know iji? Perhaps you should.
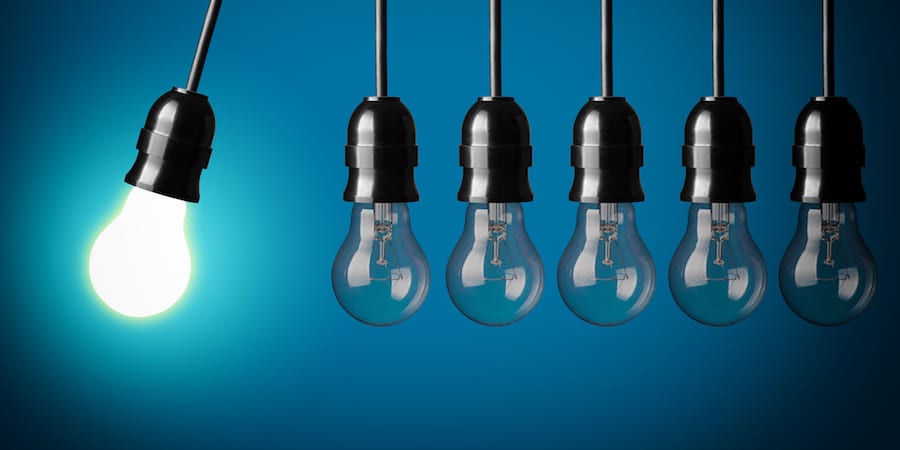
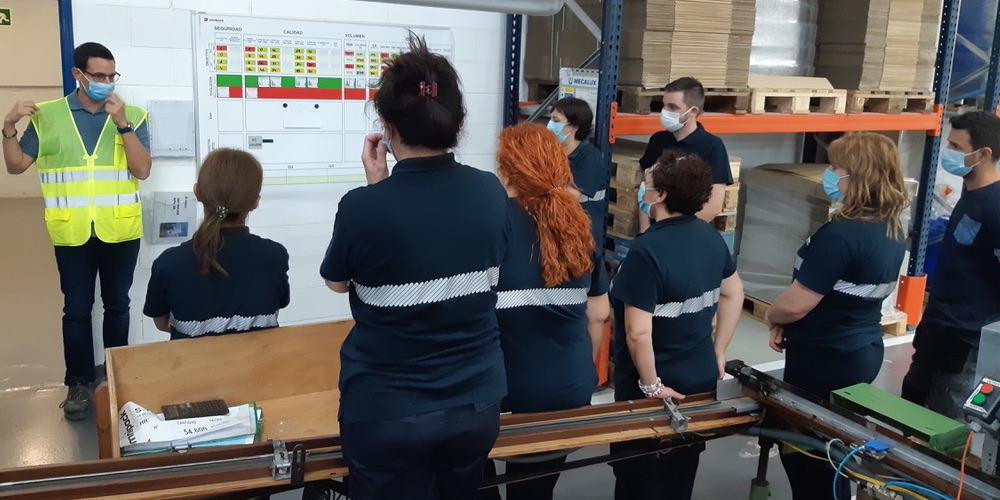
1 QUESTION, 5 ANSWERS – Without the active participation of people in improvement activities, lean is nothing but theory. Sadly, engaging folks is easier said than done. We asked five lean practitioners to share their approach to people engagement.
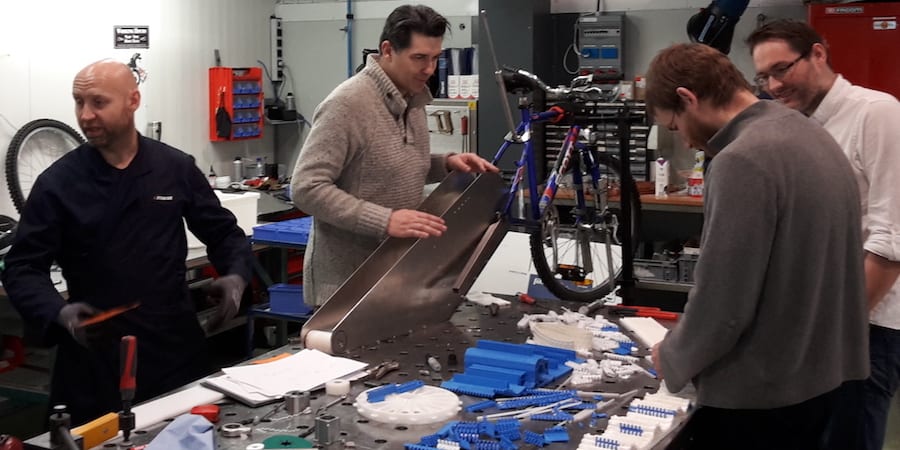
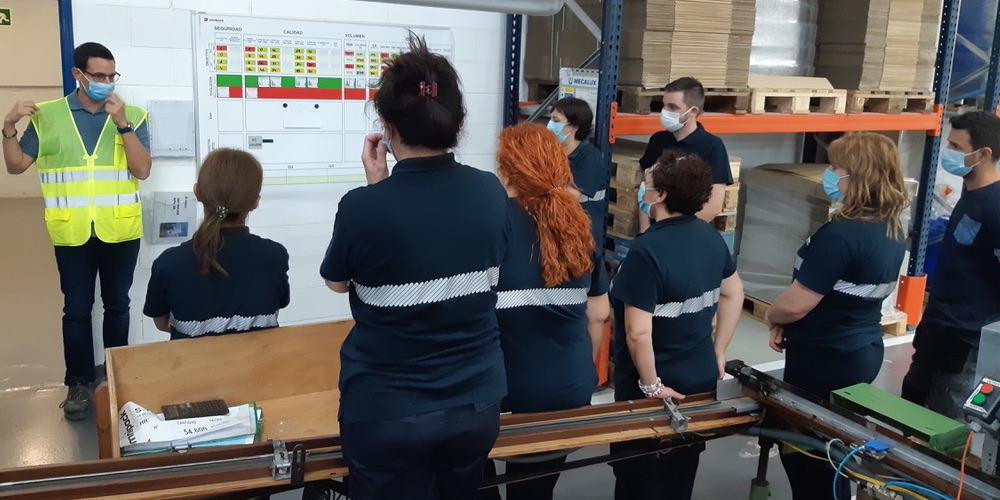
FEATURE – As an experiment to boost cross-functional collaboration, creativity and joy on the workplace, Iceland-based machining manufacturer Marel recently ran a hackathon. Here's what the experience taught them.
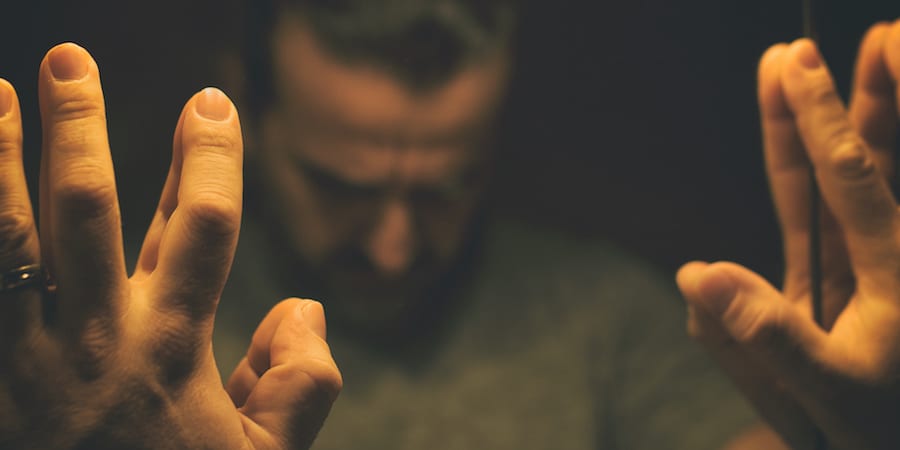
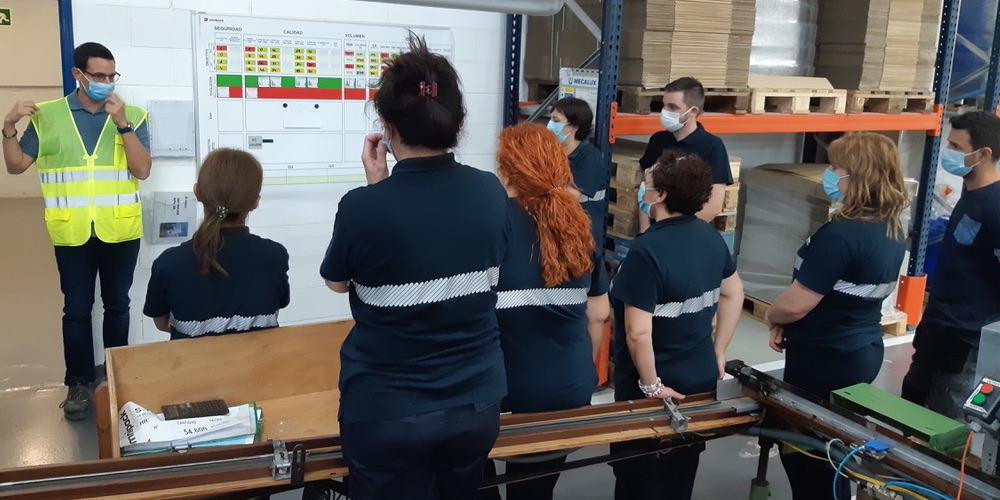
FEATURE – The role of experts in lean thinking is often the subject of heated discussions. Here, Michael Ballé tells us about the common mistakes lean experts make, and explains why – before helping others – they should help themselves.
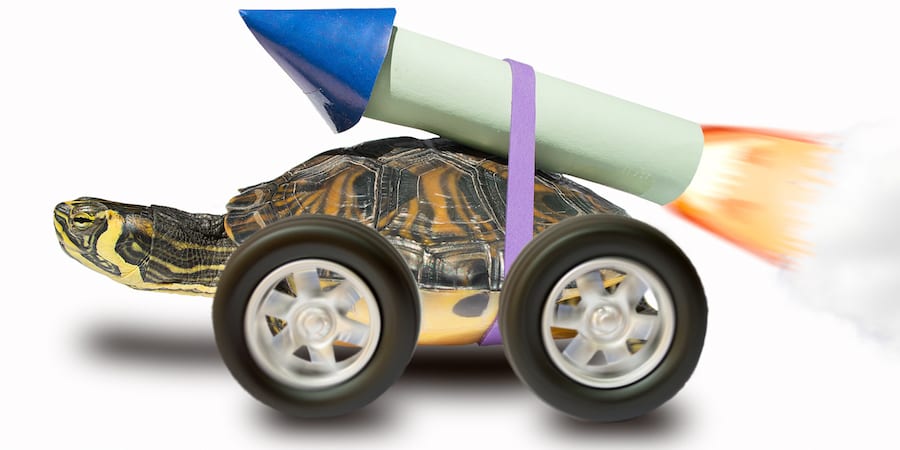
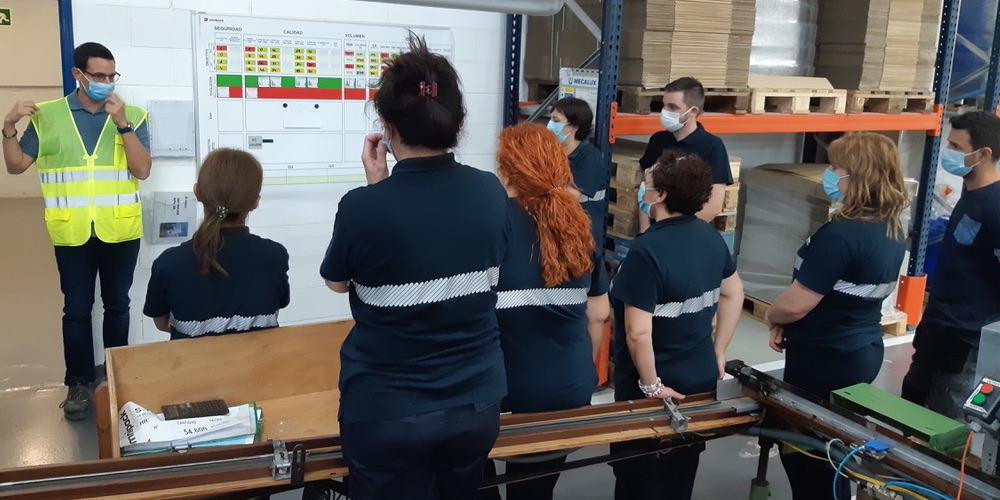
WOMACK'S YOKOTEN – How it is that some ideas and innovations spread like wildfire while others are slower to take roots? It is clear that lean thinking belongs to the latter category, but how can we speed up its diffusion?
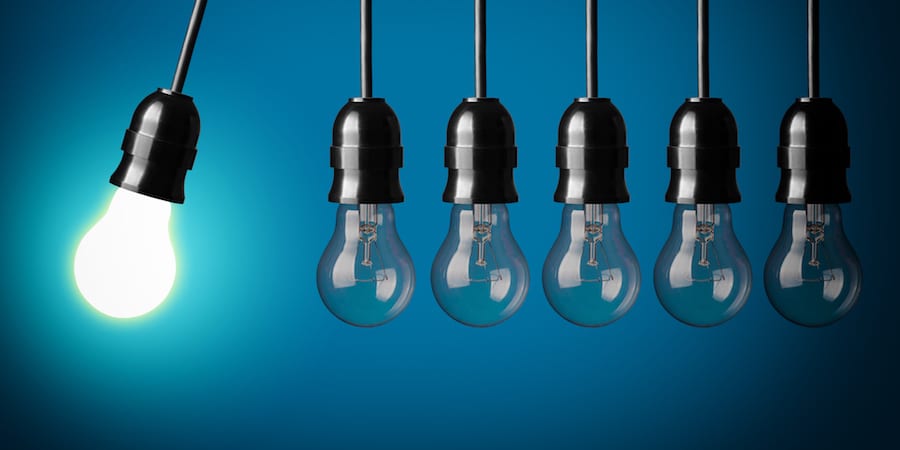
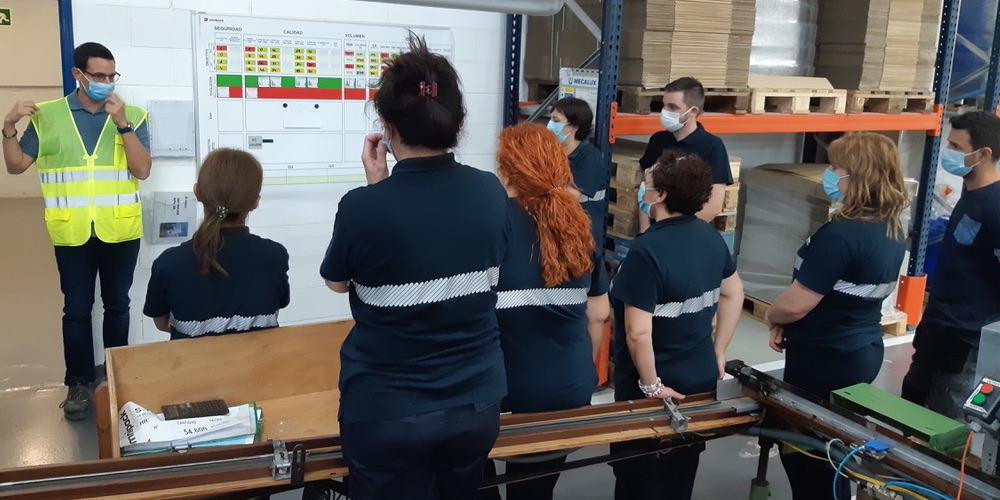
1 QUESTION, 5 ANSWERS – Lean management causes a huge shift in the mind of leaders, one that dramatically changes the way they think of themselves and the way they behave. We asked five leaders to tell us how lean changed them.
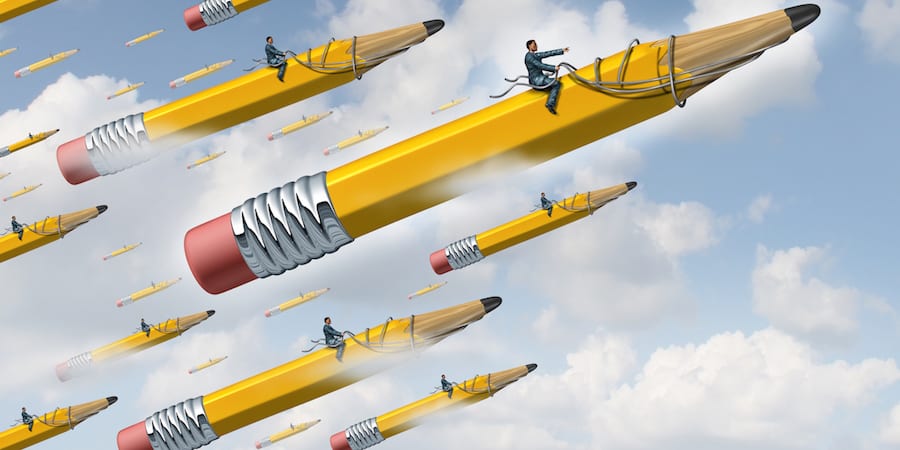
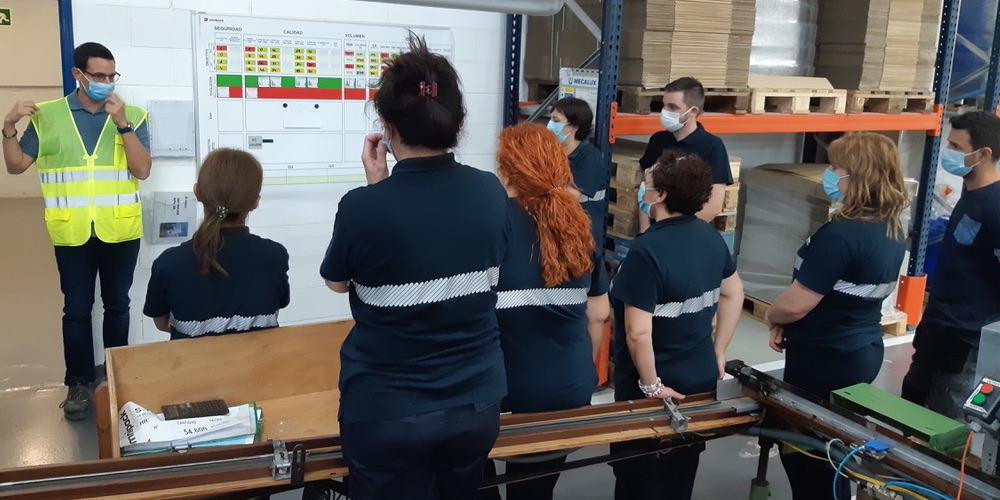
FEATURE – This powerful article explains why we should place learning at the heart of our lean strategy to build better products – something Toyota has always done – and how management fits in the picture.
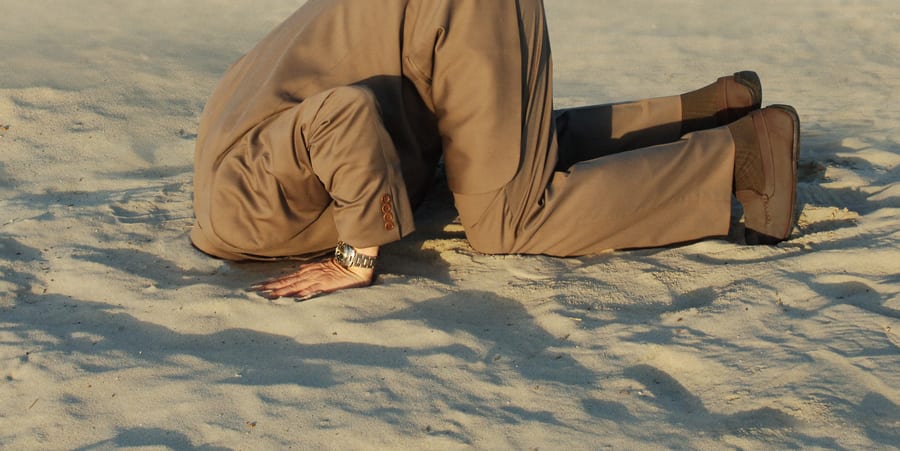
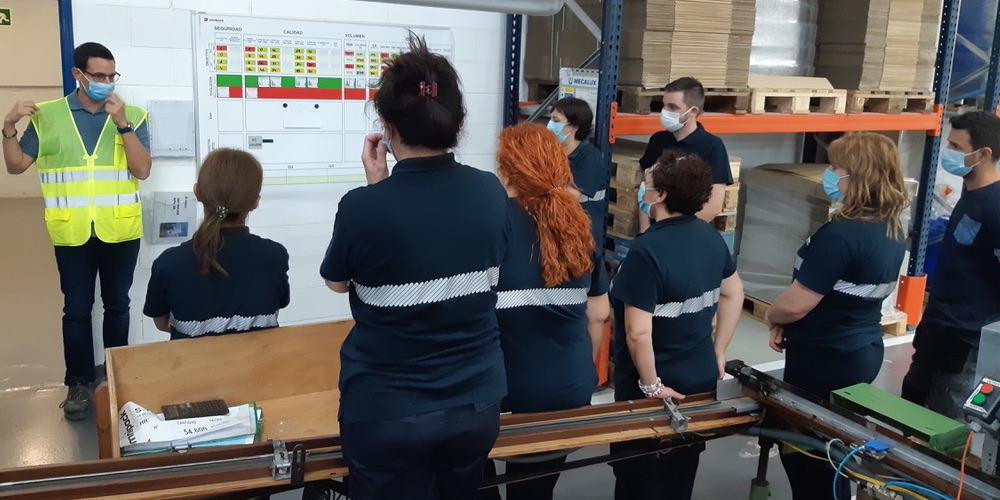
FEATURE – There are five dimensions to a lean transformation – purpose, process, people, management behaviors, and mental models – and it is the role of leadership to adjust its stance to each of them.
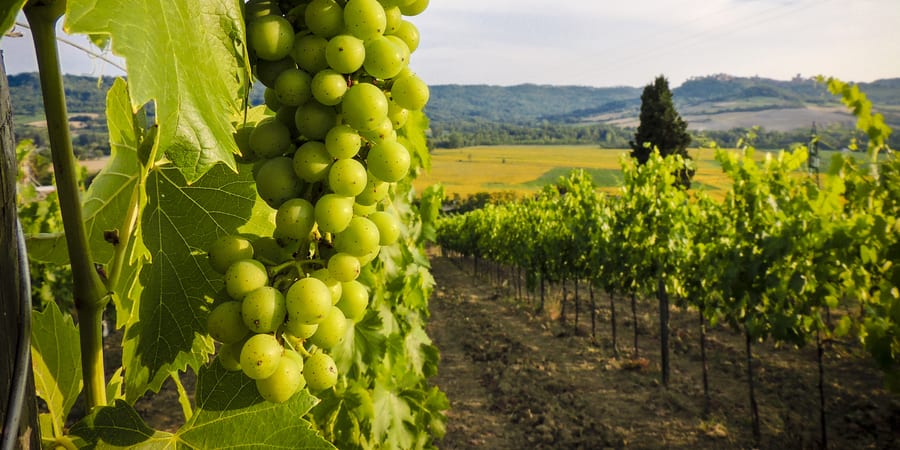
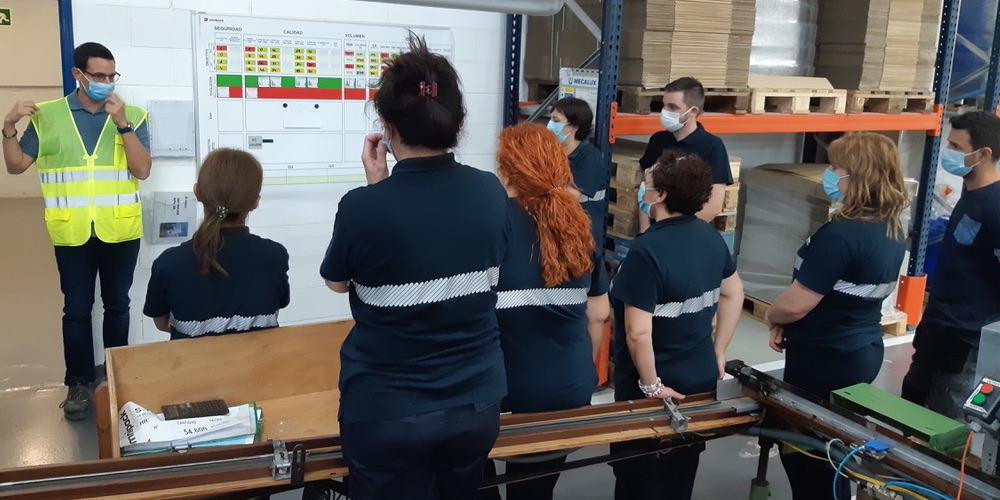
WOMACK'S YOKOTEN – Lean in agriculture might still be in its infancy, but there is a small farm in Indiana that is already proving how valuable lean principles and techniques can be to this industry.
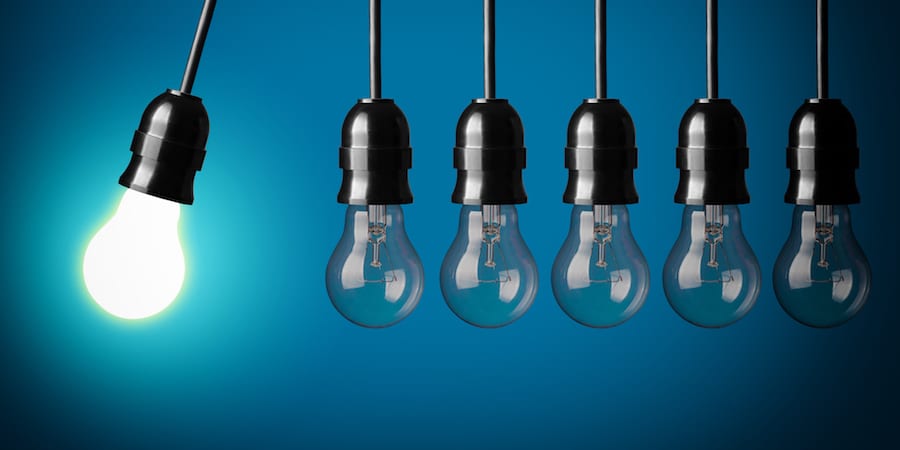
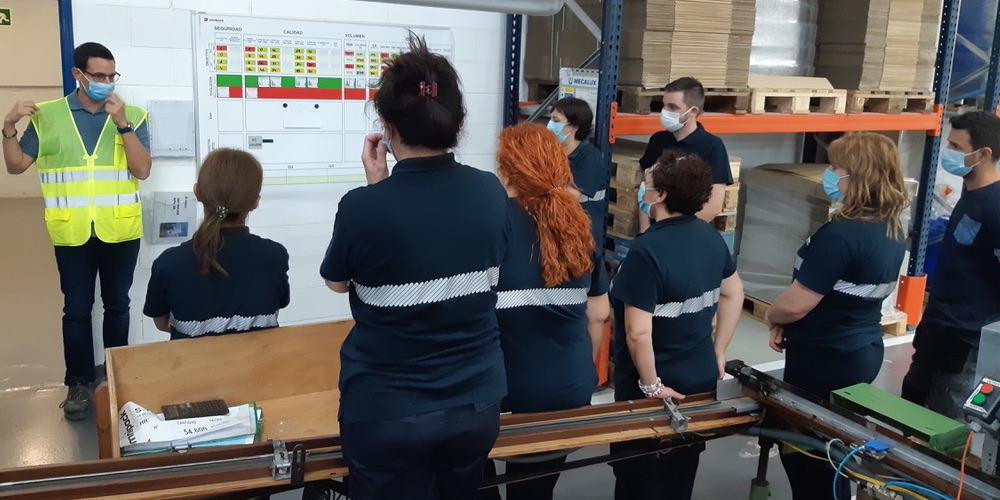
1 QUESTION, 5 ANSWERS – Because each of us has a different learning path, “a-ha moments” come to us in a variety of shapes. We asked five practitioners when their lean epiphanies happened.
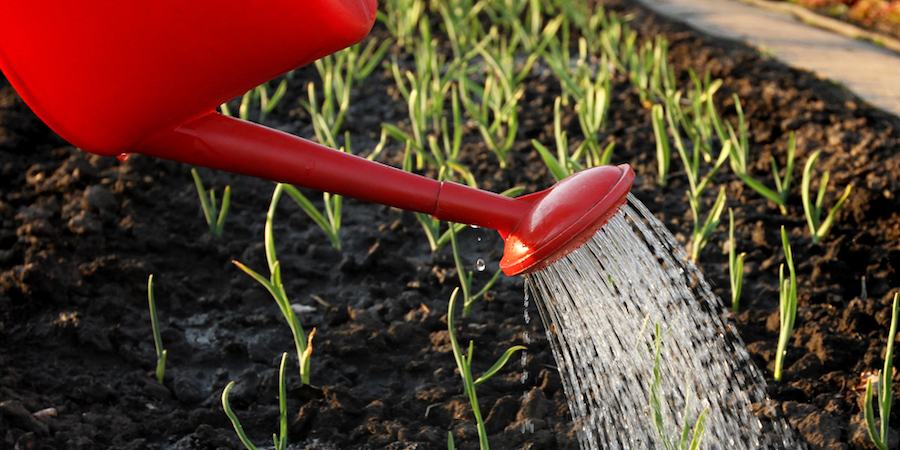
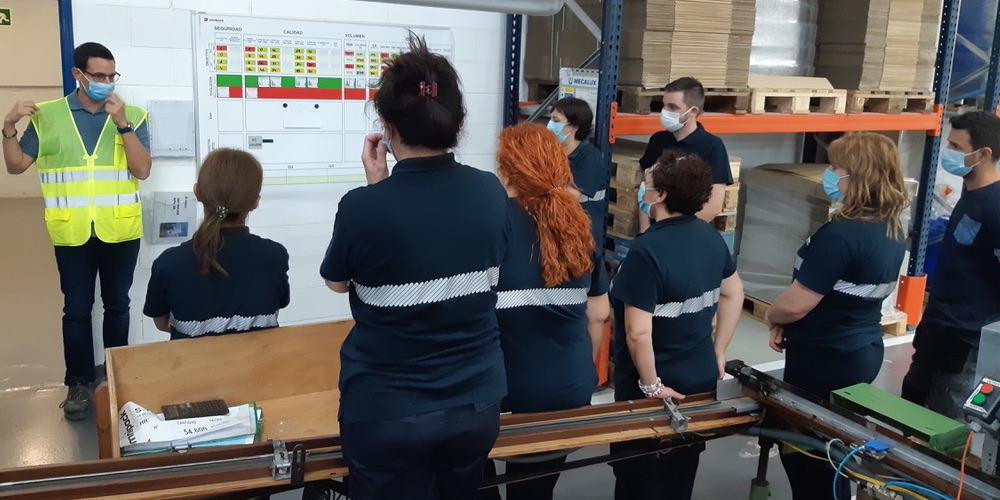
FEATURE – When middle managers are stressed and overworked, there is no time left for them to improve. Changing the interaction between leaders and teams, using lean principles and empowering people, can truly ignite your transformation.
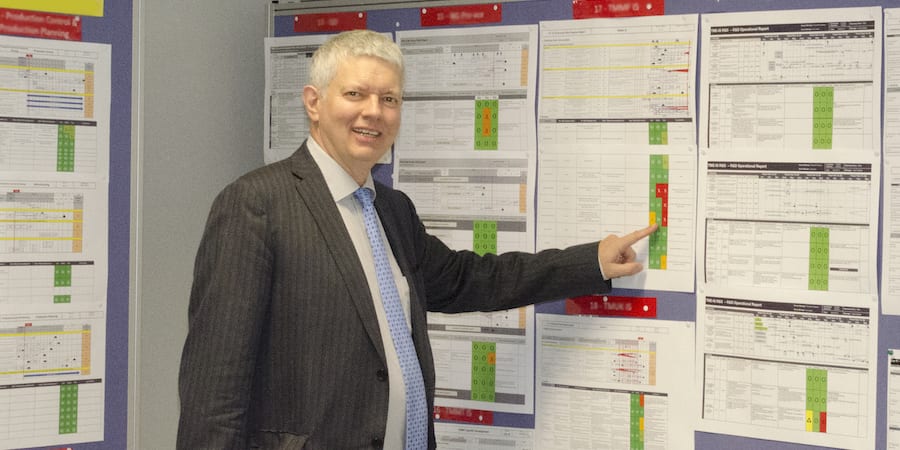
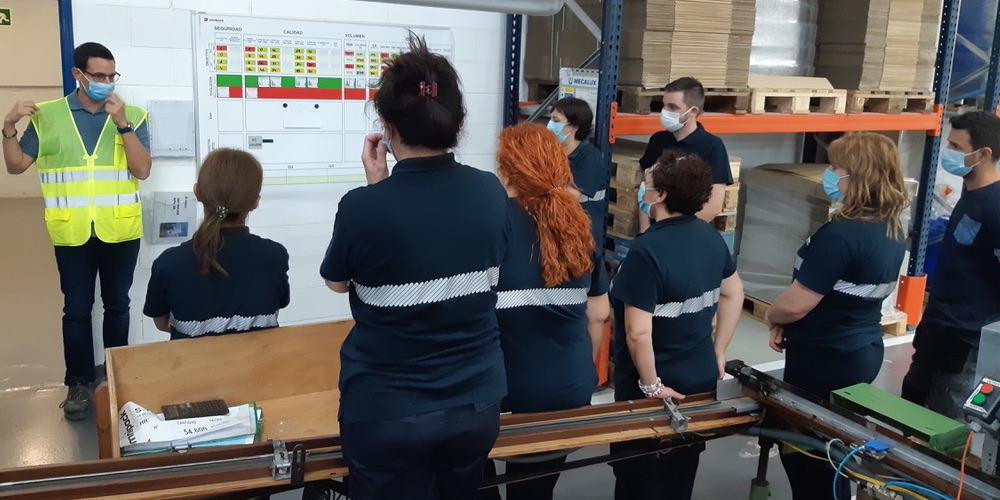
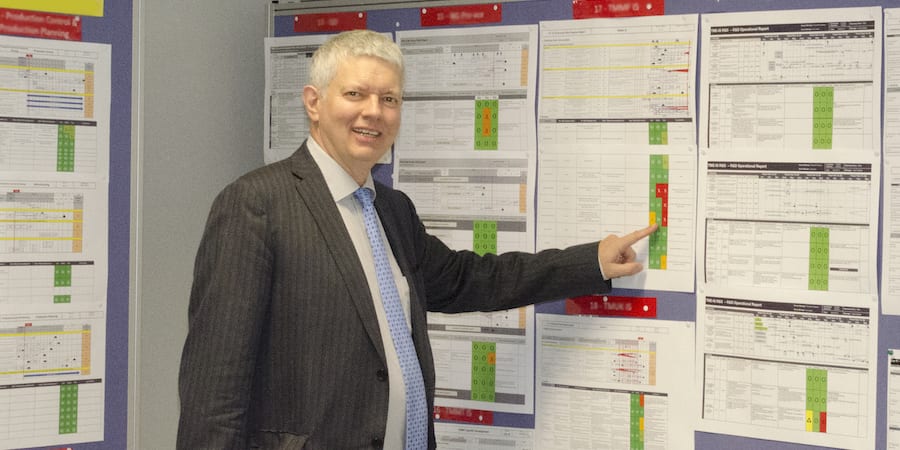
PROFILE – A commitment to learning and the humility to understand we never really know enough have led a Belgian mathematician to become a polyglot… and the CIO of Toyota Motor Europe.
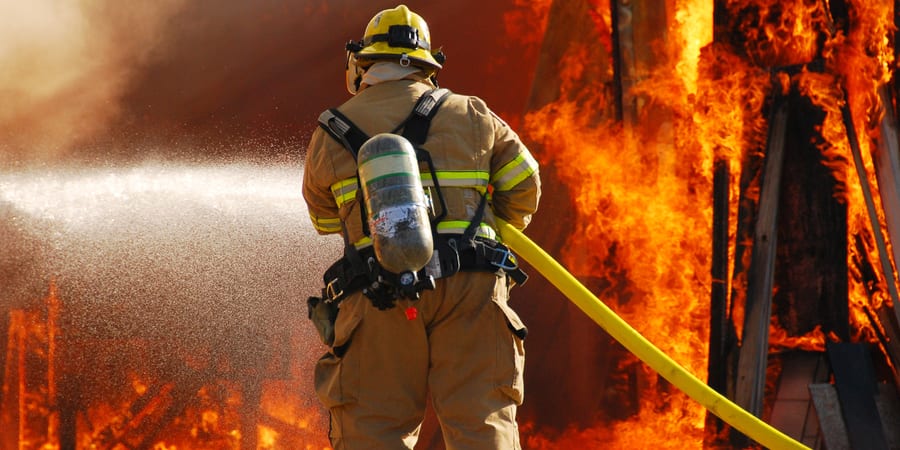
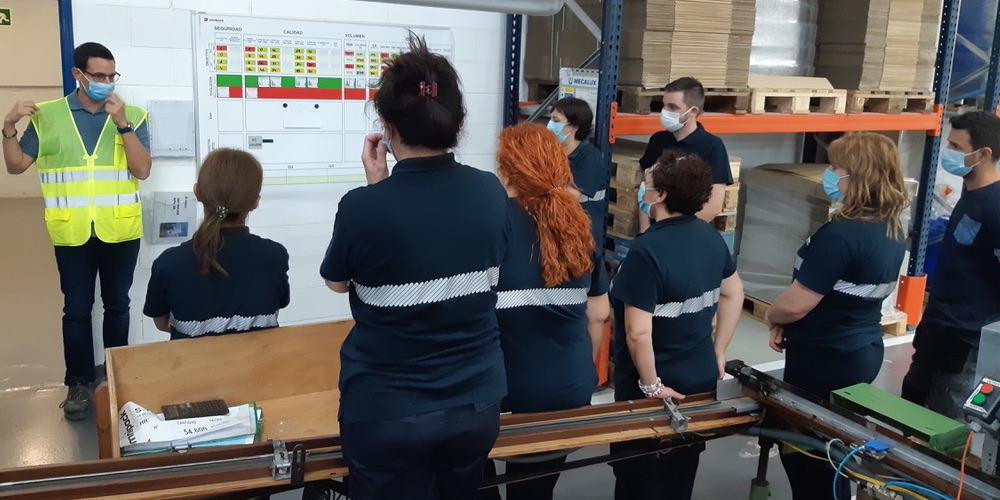
FEATURE – Too often we tend to focus on trying to replicate success, rather than analyze failure. Yet, learning from mistakes is a fundamental principle in lean. This account of a transformation gone south offers an insightful critique of lean.
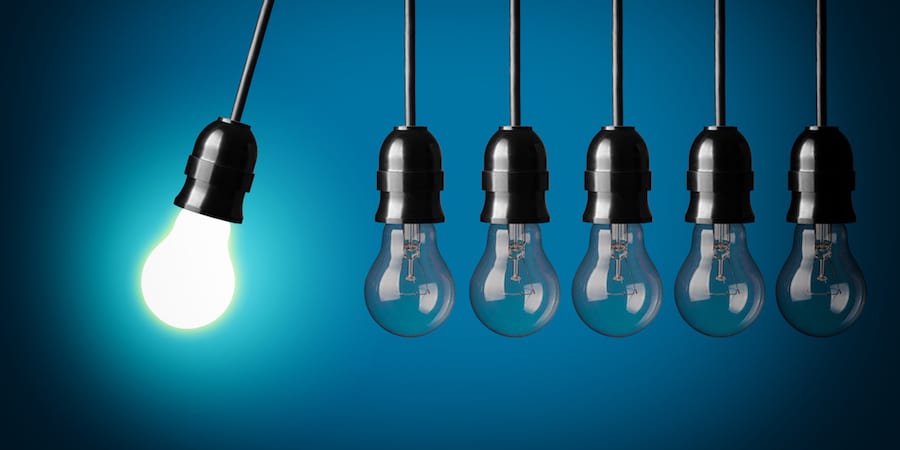
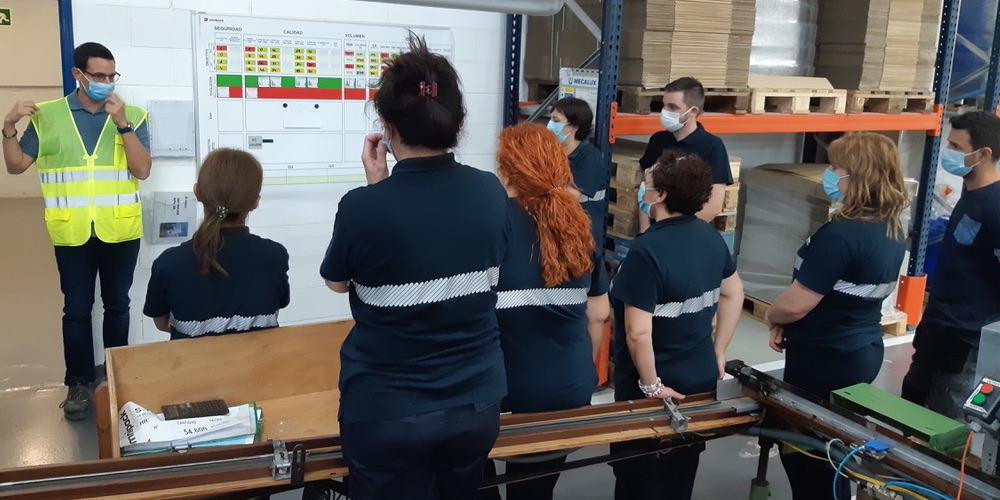
FEATURE – For this new monthly article, we will be asking five lean practitioners the same question and share their answers with you. We started by asking them about their biggest lean mistake.
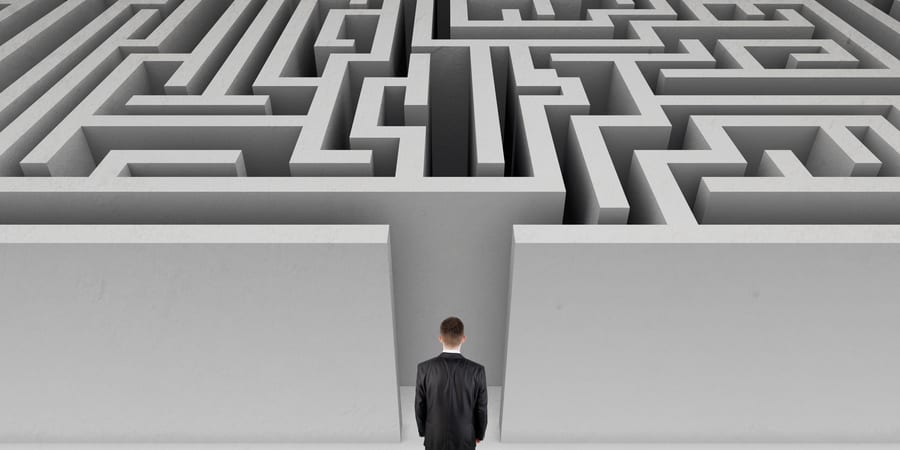
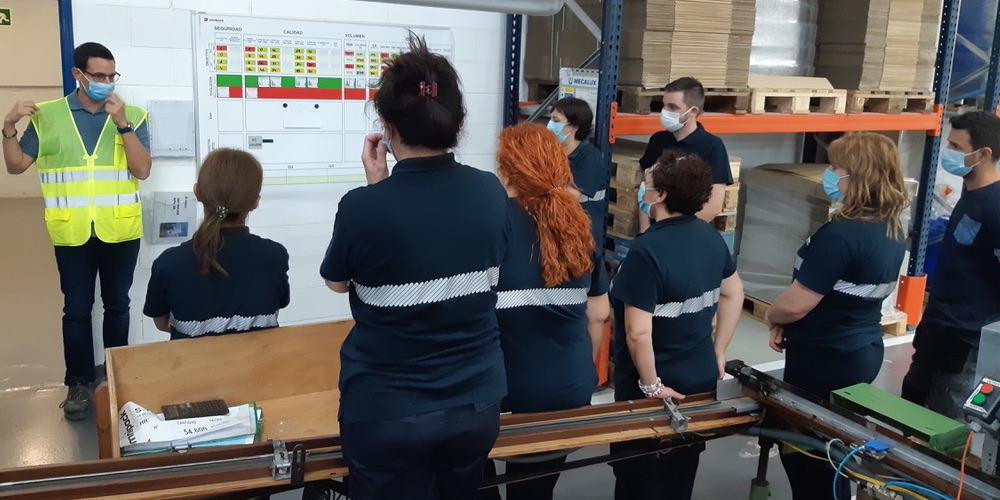
RESEARCH – The author explores the effectiveness of five common managerial practices in driving a corporate lean initiative forward, analyzing the data gathered while visiting 36 factories of a large corporation.

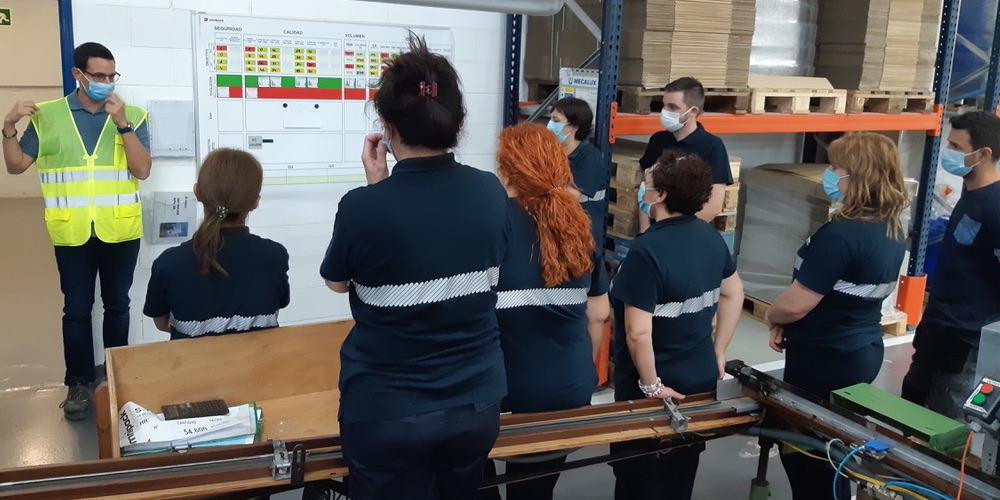
CASE STUDY – The extraordinary transformation of Kinross' Round Mountain gold mine in Nevada over the past six years shows that lean thinking can – quite literally – move mountains.
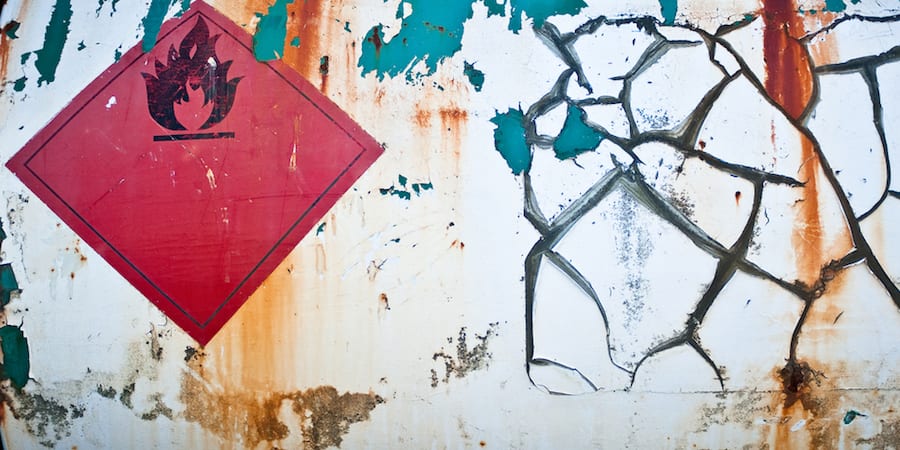
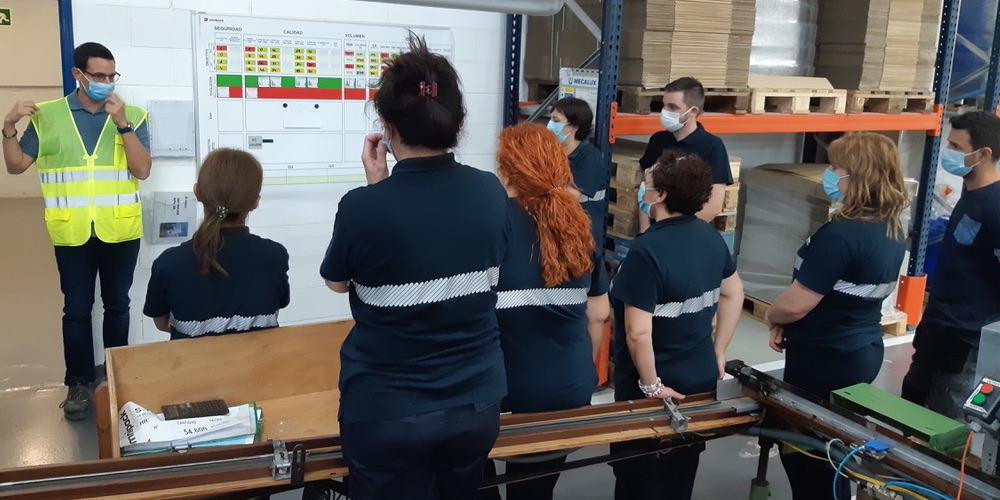
FEATURE – What are the immediate signs that tell us that our workplace is not conducive to kaizen? The author draws on his experience as a coach at the gemba to highlight them. Look out for them in your own company!
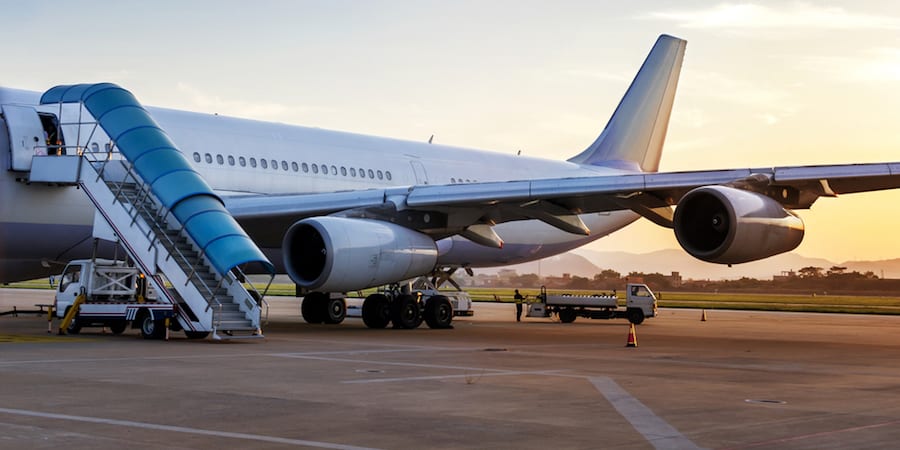
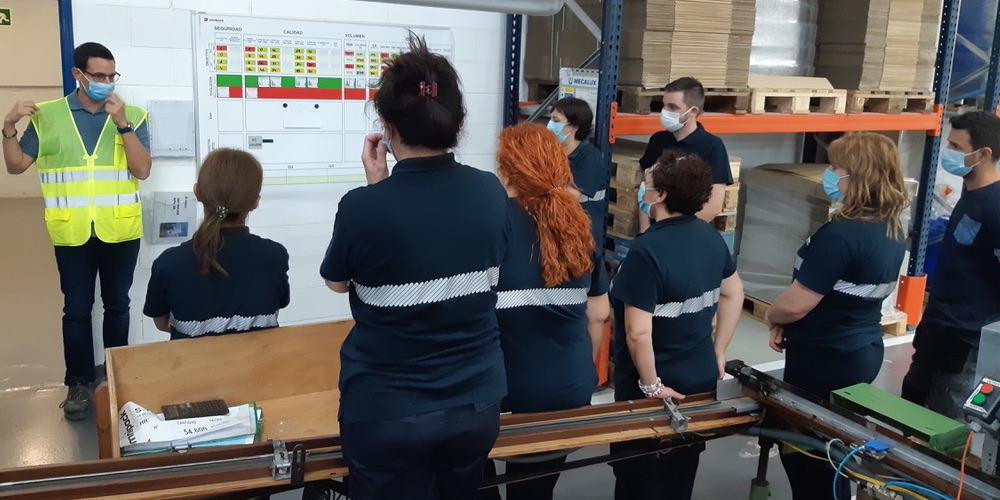
WOMACK'S YOKOTEN – As a new age in aerospace dawns, with a need to move from huge and bespoke designs to affordable and high-volume production, lean thinking has a key role to play. But will the industry listen?
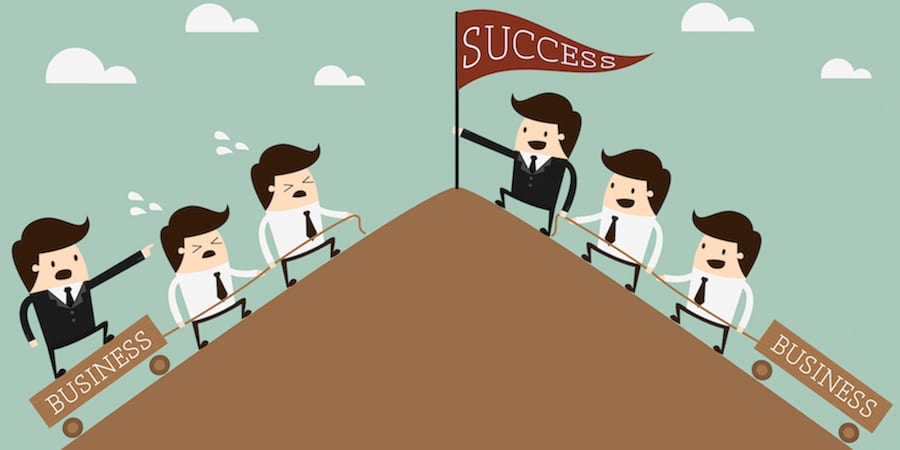
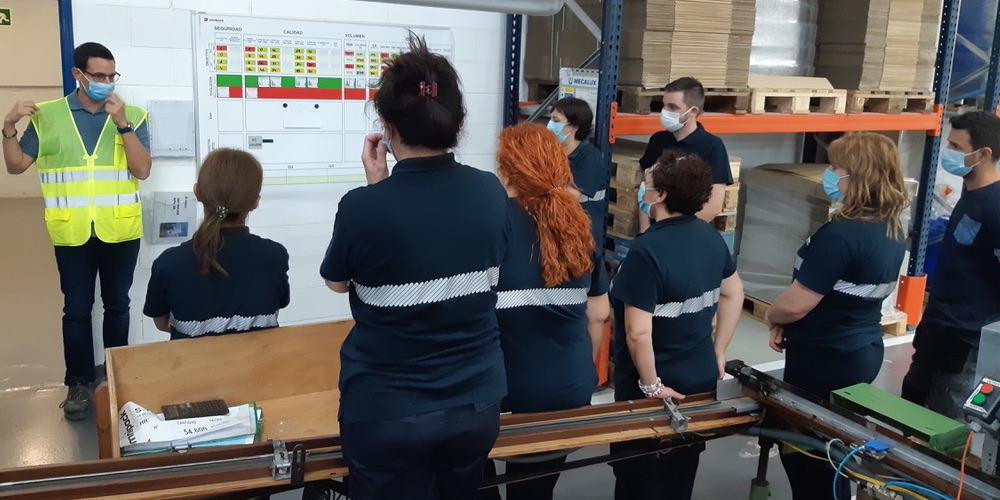
INTERVIEW – Last month we caught up with Toyota veteran Art Smalley in Las Vegas and discussed with him the role of leadership in a lean transformation and the four different types of problem solving he talks about in his new book.
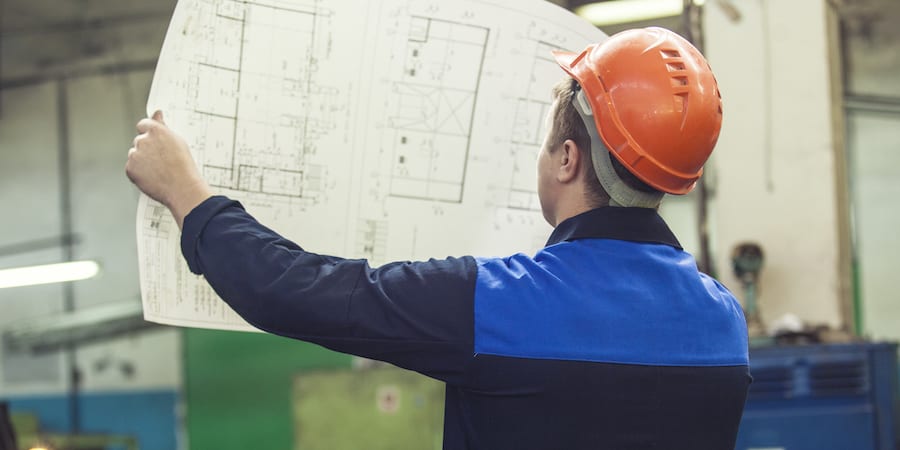
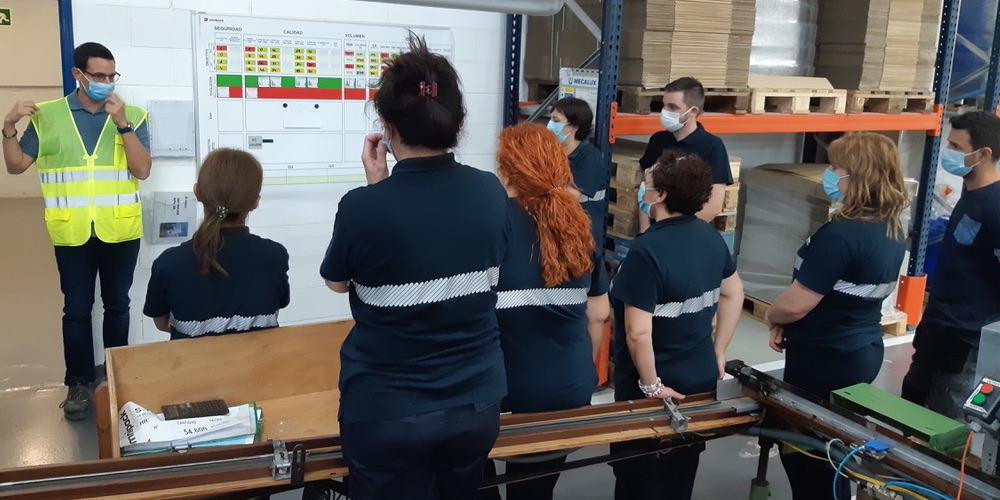
WOMACK'S YOKOTEN - Kaizen or kaikaku? This is the problem. When it comes to the pace of change, should we carry on with small, incremental improvements or aim at more revolutionary changes instead?
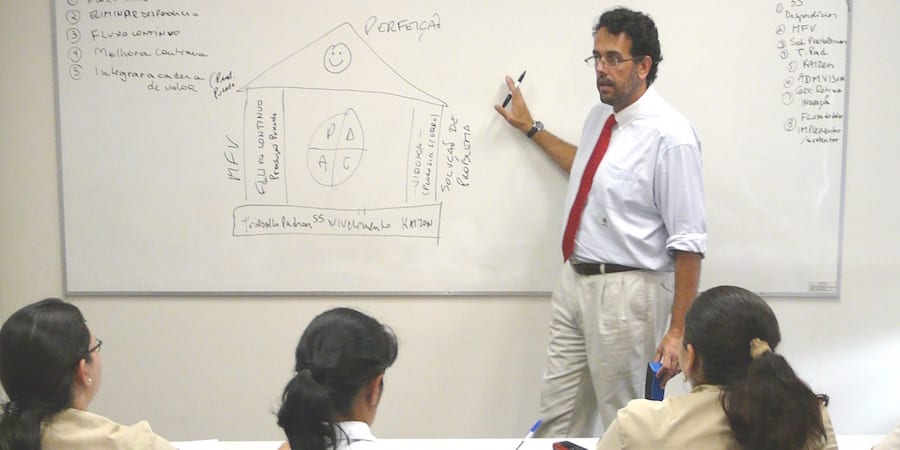
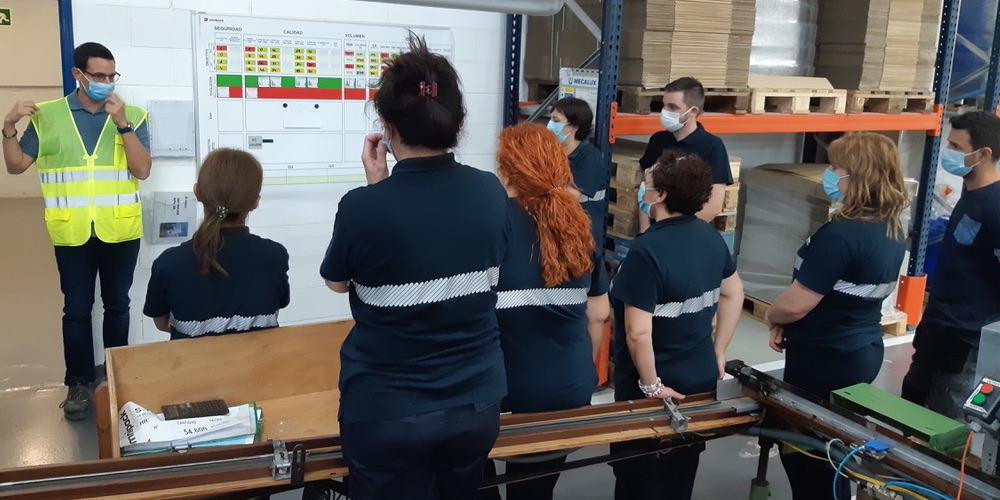
PROFILE – It isn’t every day that you come across a hospital CEO coaching people on A3s and following his own standard work. So when you do, it’s important to share their story. This month we profile the CEO of a Brazilian cancer treatment center.
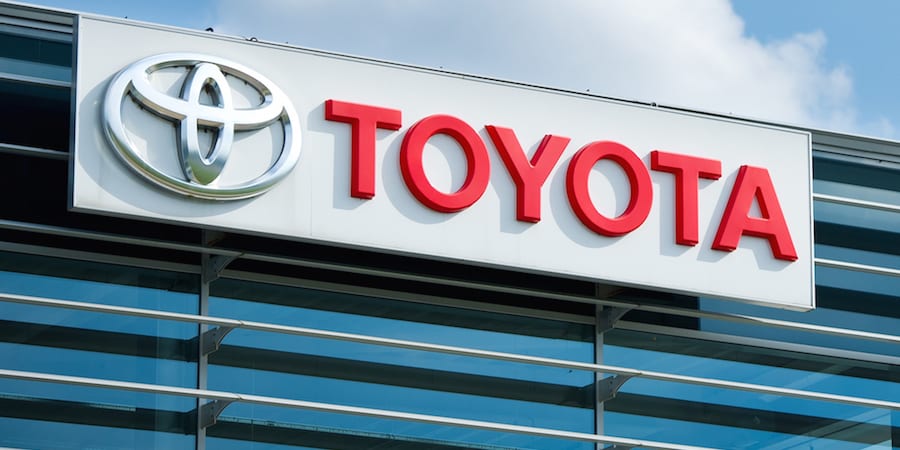
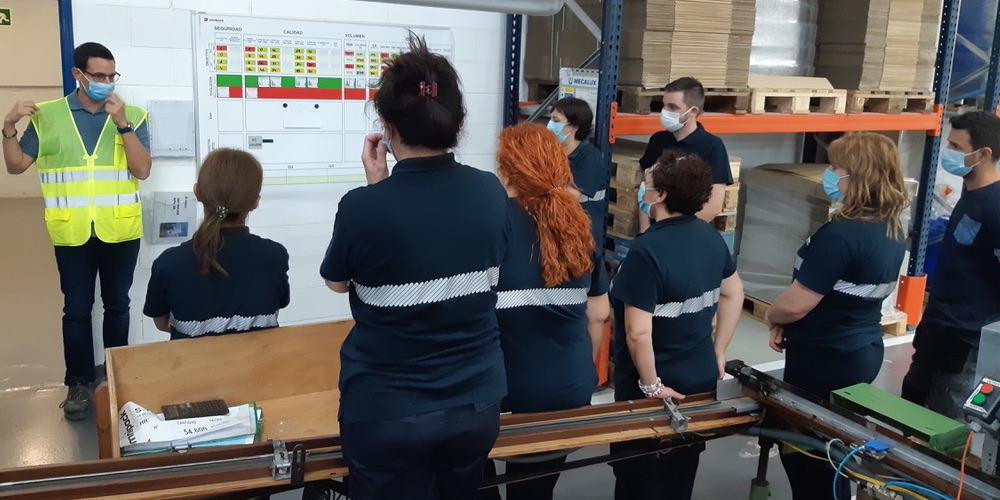
INTERVIEW – At the recent UK Lean Summit, Ian Hurst and Keith Edwards of the Toyota Lean Management Centre ran an insightful workshop on standard work. We sat down with them to discuss standardization, respect for people and waste elimination.
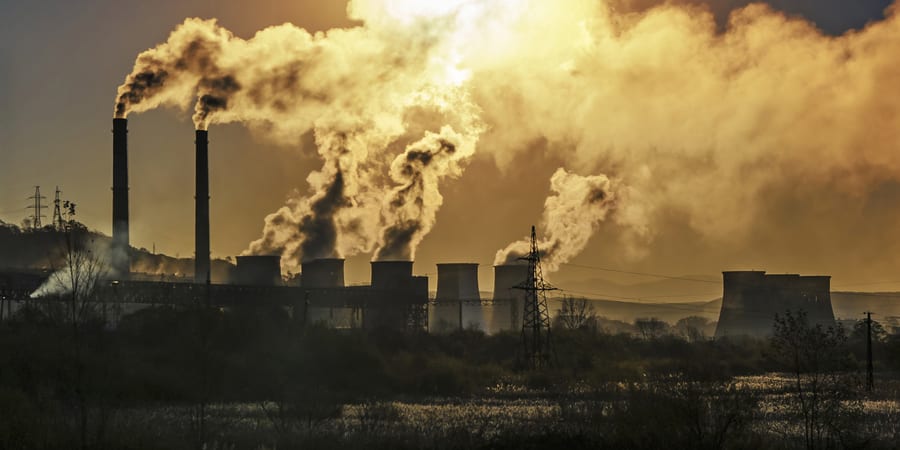
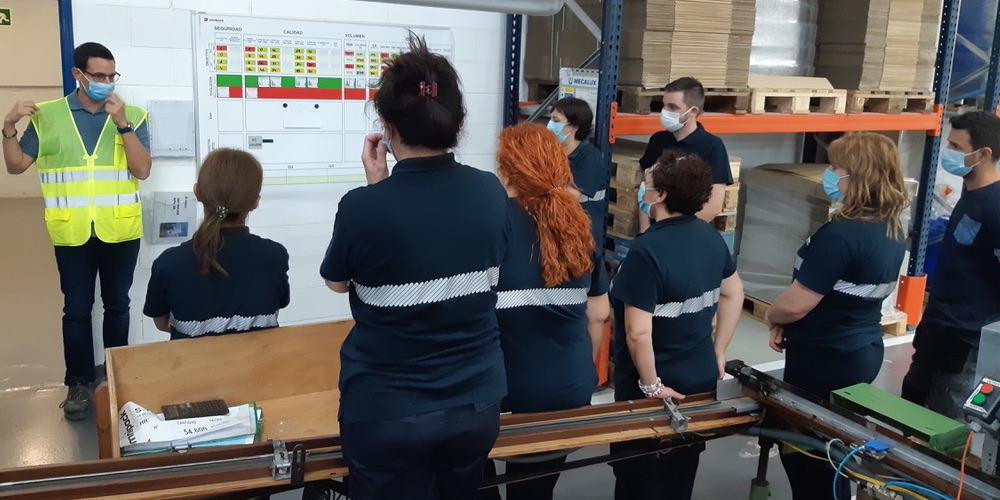
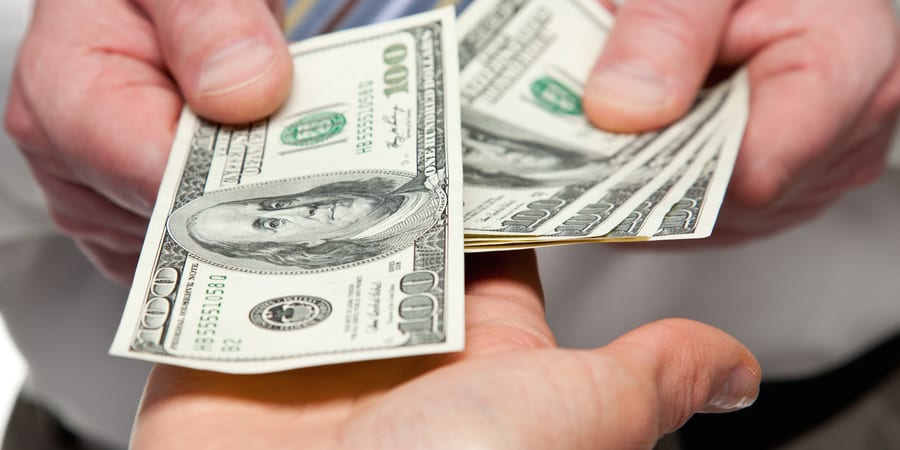
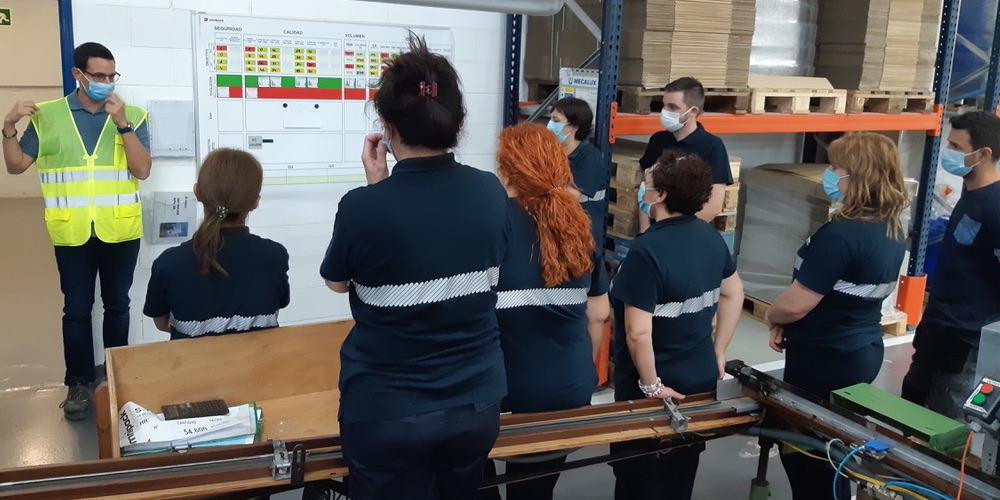
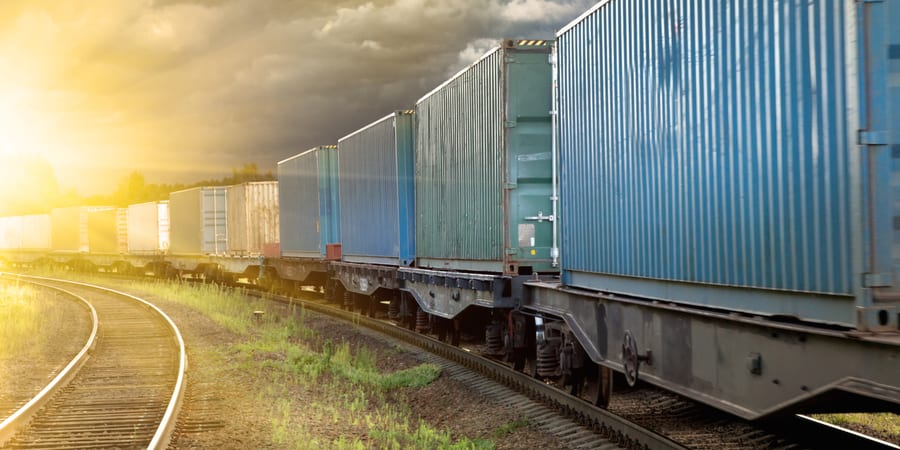
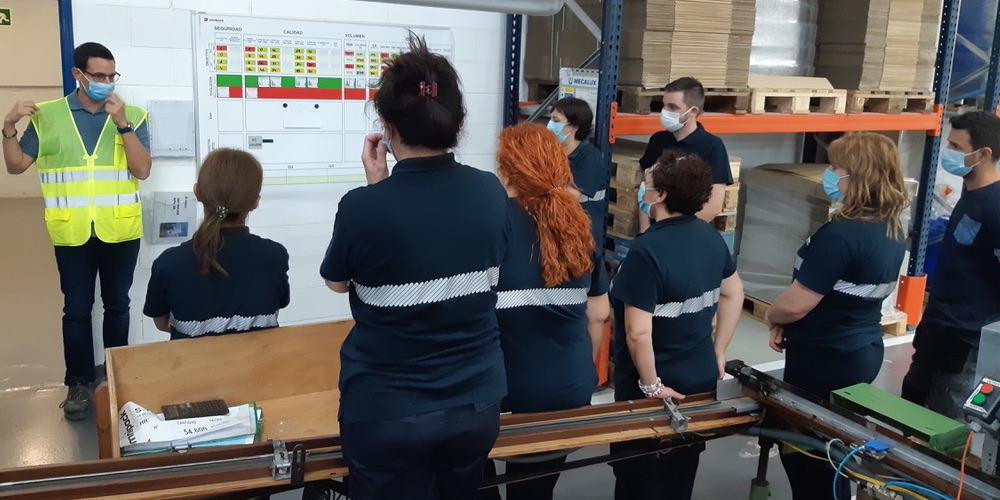
FEATURE – Starting off a lean journey is no easy feat, and existing models won’t tell you what the next steps are. That’s why you should go back to basics and let the Toyota Production System “house” from the mid-1980s show you the way.
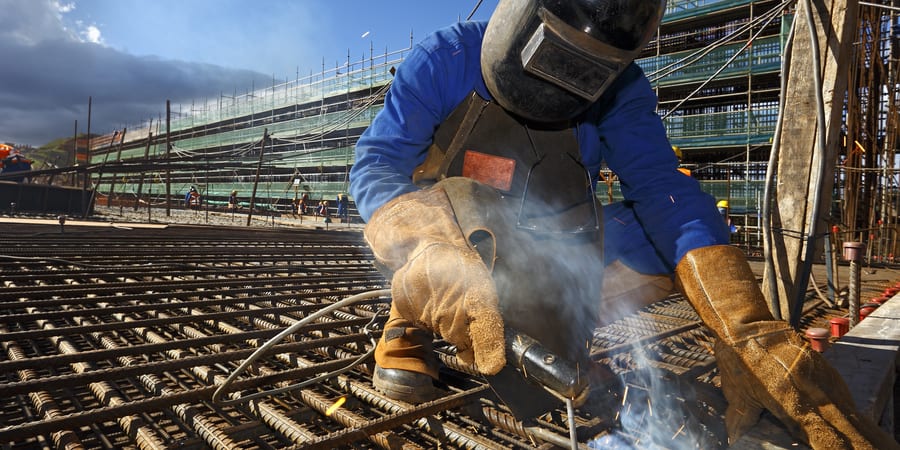
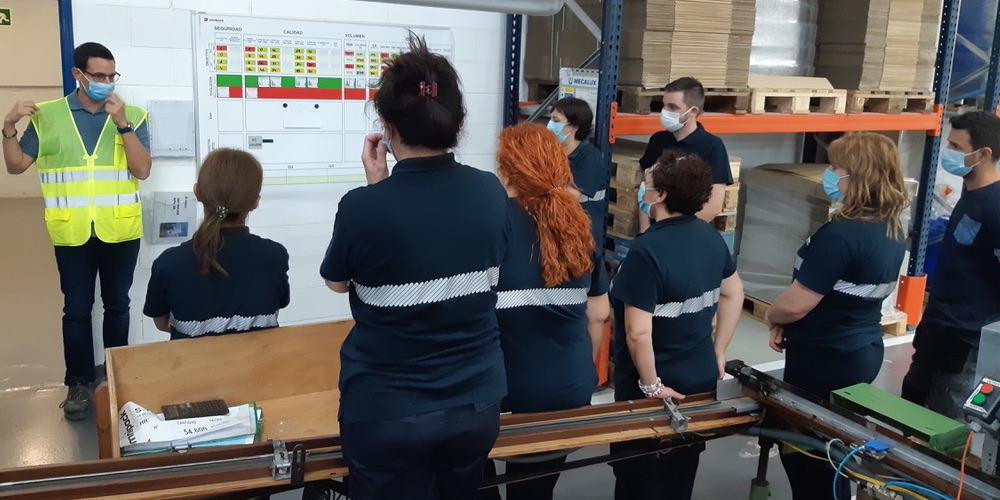
WOMACK’S YOKOTEN – If truly embraced, lean thinking sustains and (in the long run) even creates jobs, but if a transformation is to last these jobs must be “good,” says Jim Womack.
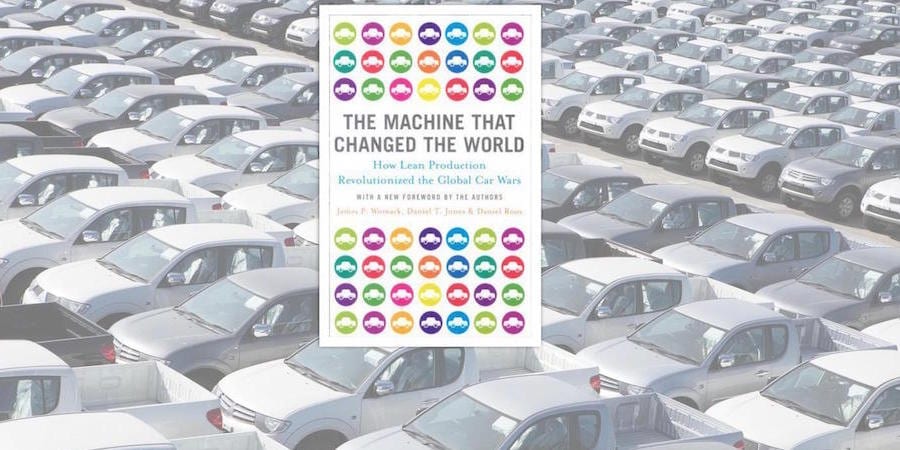
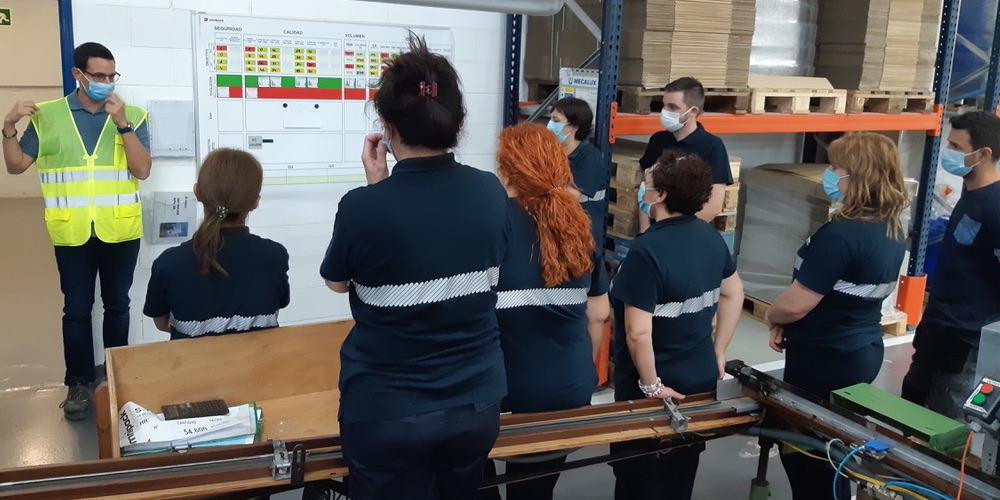
WOMACK’S YOKOTEN – On October 10, 1990 the book that introduced lean thinking to the world was published. Twenty-five years after Machine, one of the authors reflects on what the lean movement has achieved and on what is slowing it down.
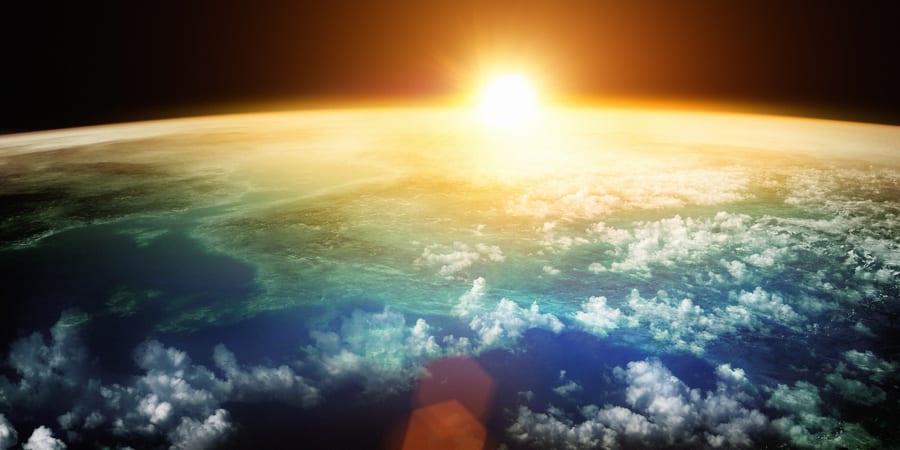
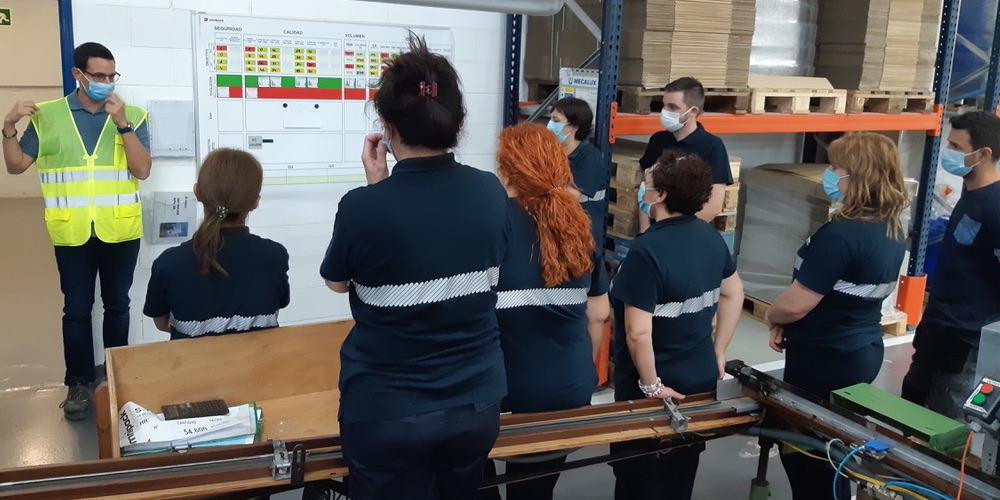
FEATURE – If we see lean thinking as a paradigm, which we do, then we should be able to define a set of values this paradigm is built on. So, are there lean ethics? Michael Ballé identifies 10 undisputed lean values, plus one.
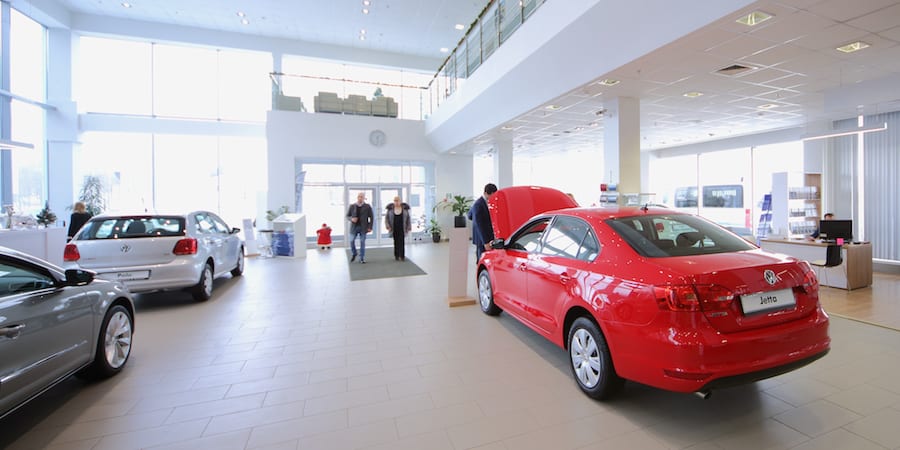
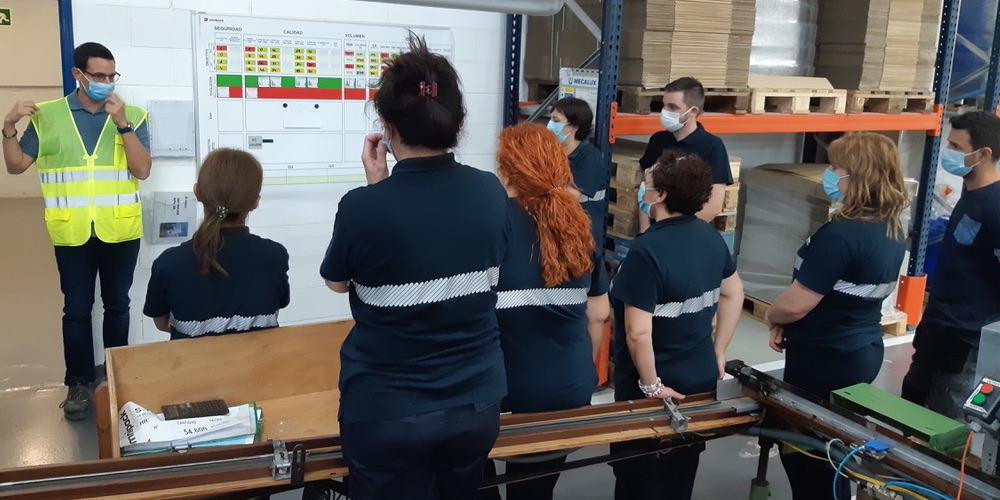
WOMACK’S YOKOTEN – The Volkswagen “defeat device” scandal is the latest example of a company that has chosen to focus on growth rather than the customer. What can we learn from this, and what should we do when such a shift takes place?
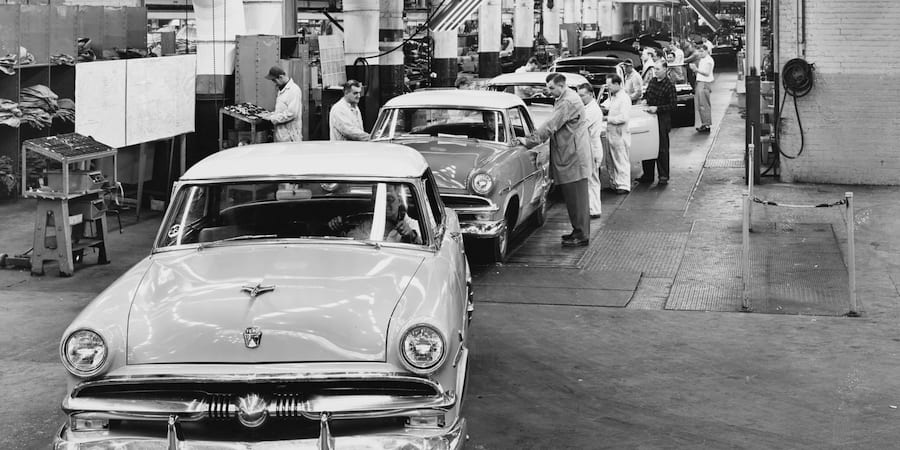
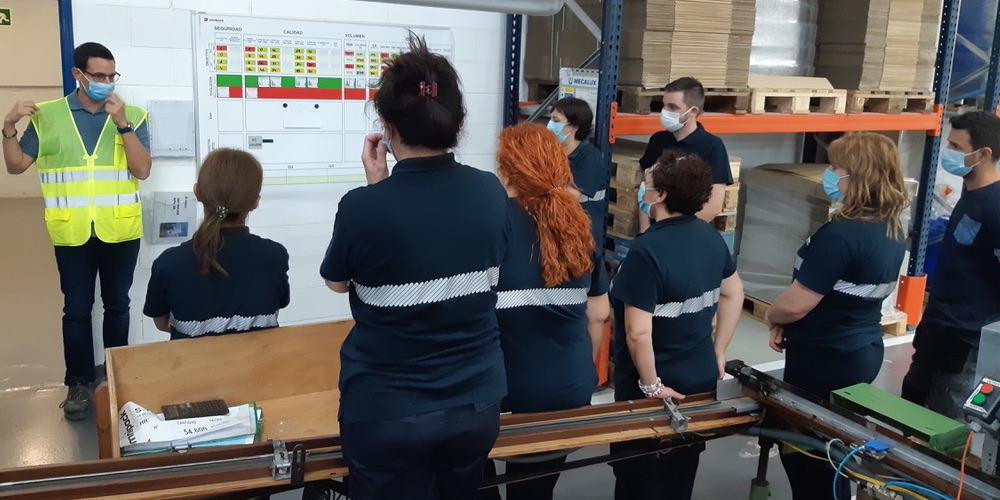
FEATURE – By offering an alternative approach to management, lean thinking has disrupted the business world in the past three decades. But in what way has it really innovated?
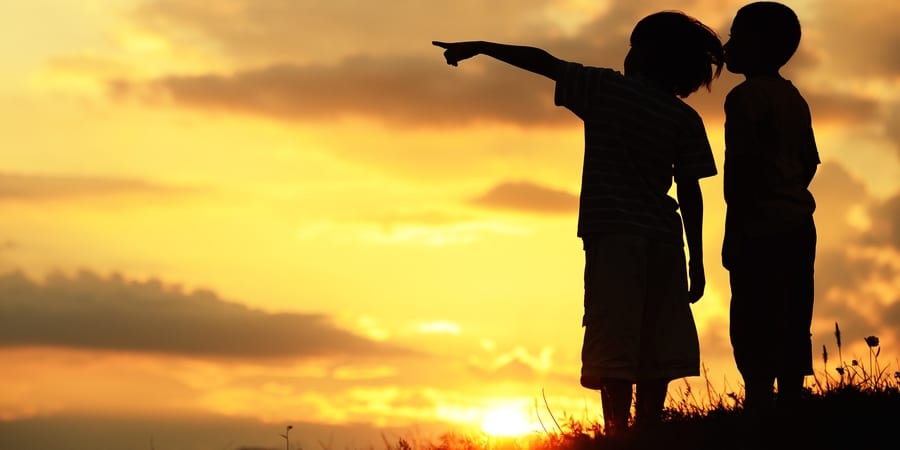
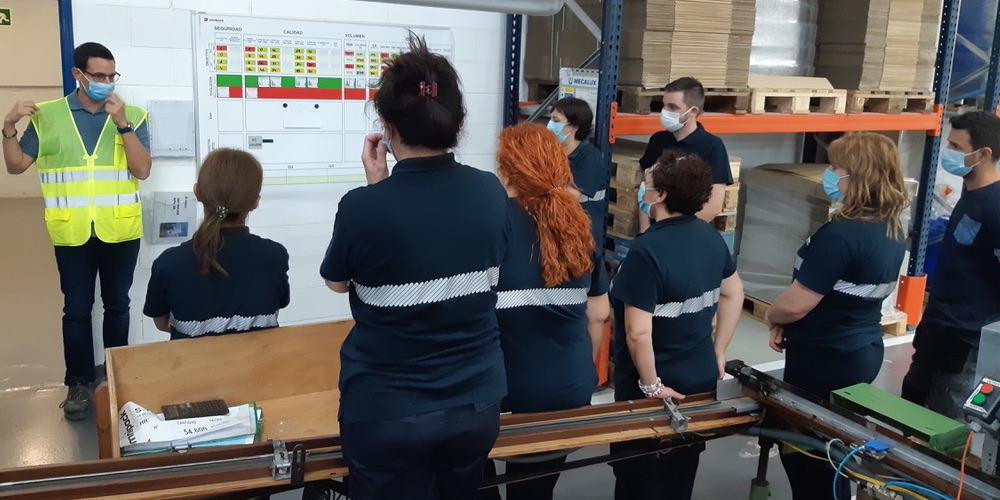
FEATURE – For the last article of their series, the authors ask themselves the ultimate question: who wins at lean, and who loses? What makes change sustainable? Turns out, it’s all about the fundamentals.
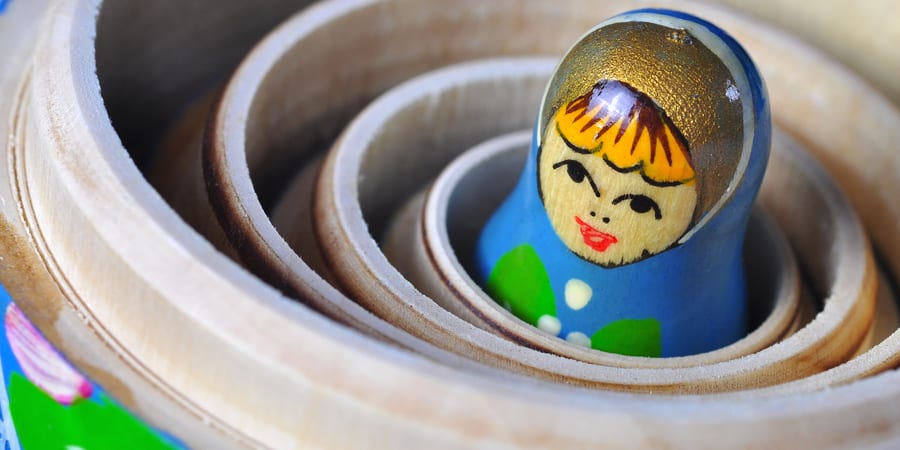
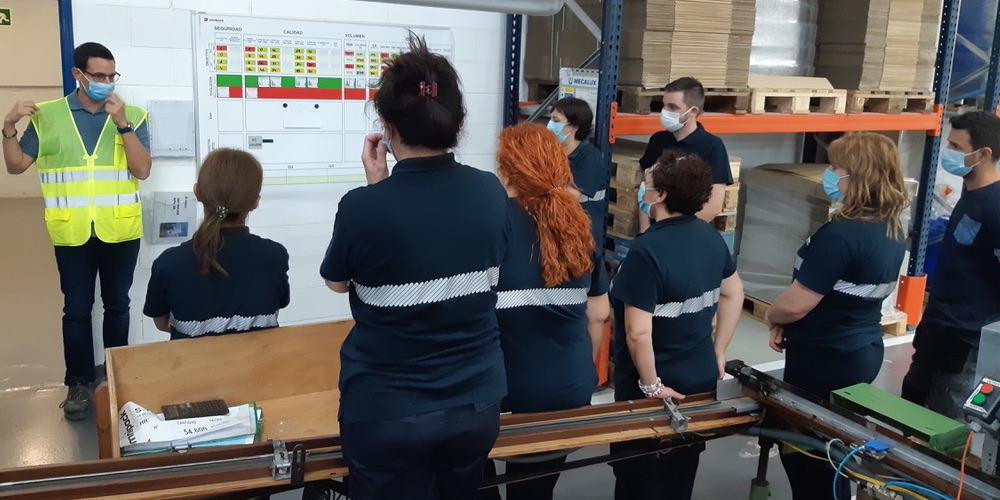
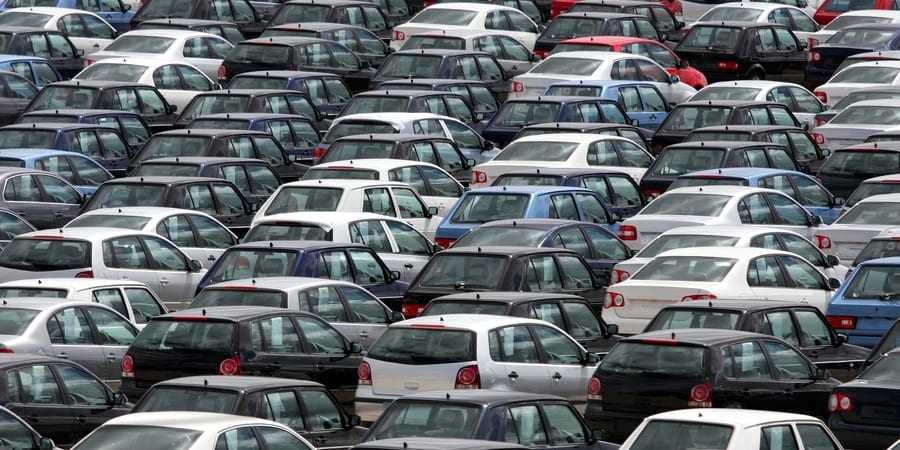
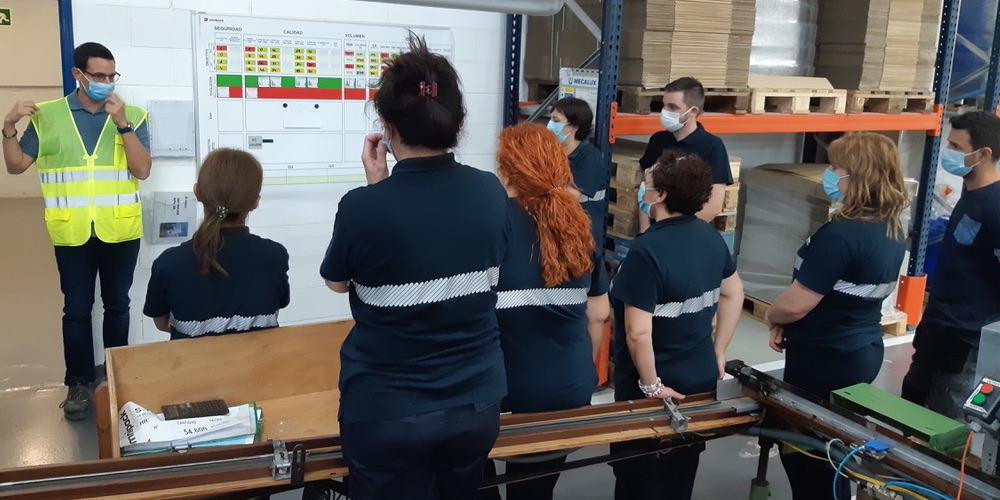
WOMACK’S YOKOTEN – The sharing economy came with a very “lean” promise – underutilized resources made available to those who need them for a reasonable fee – but not all that glitters is gold.
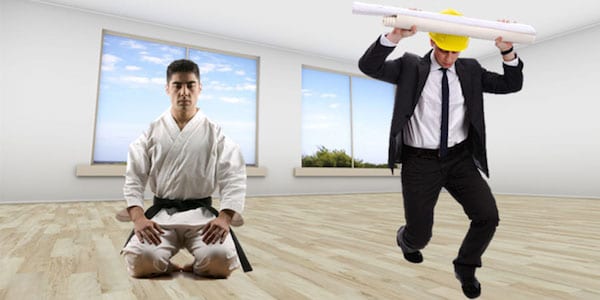
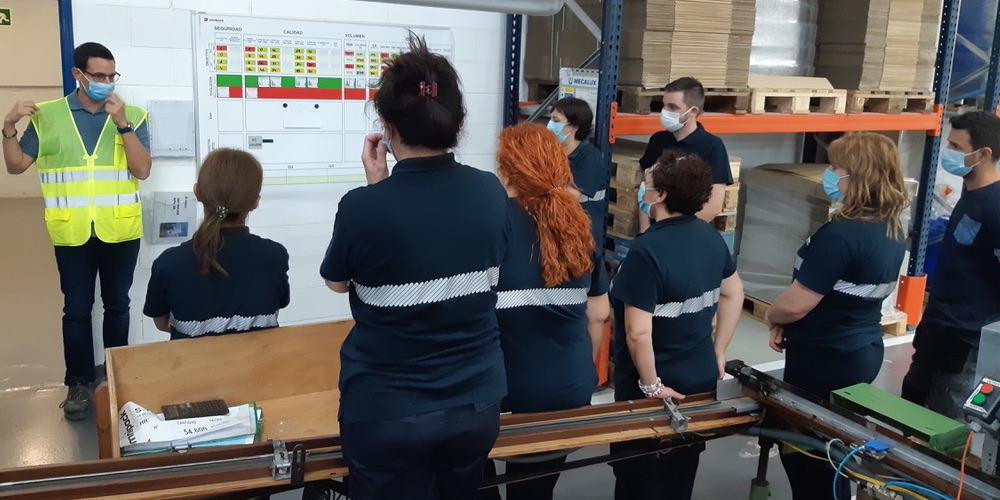
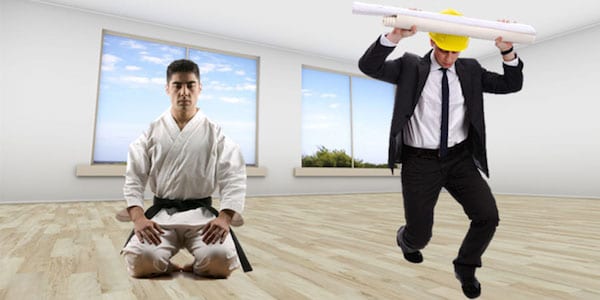
ARTICLE – In her second piece for PL, Frances Steinberg returns to the topic of working more effectively with people and the importance of going beyond the structured approach of kata familiar to so many of us.
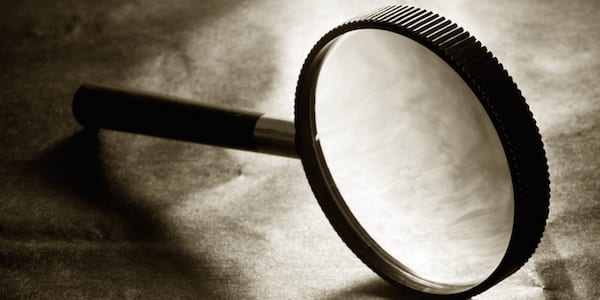
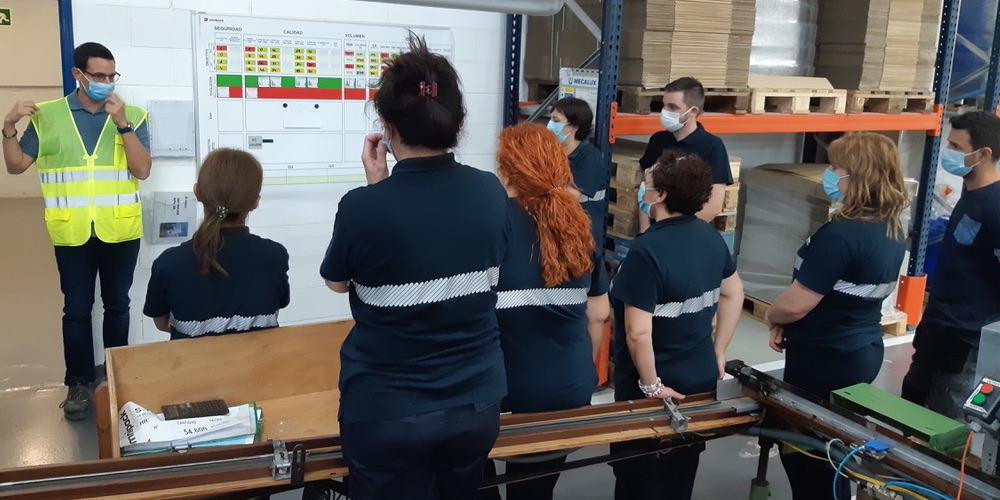
FEATURE – Until “check” and “act” become a natural part of daily work, we will always need formal audits to keep people focused and to sustain results. Here’s a few tips to make them work.
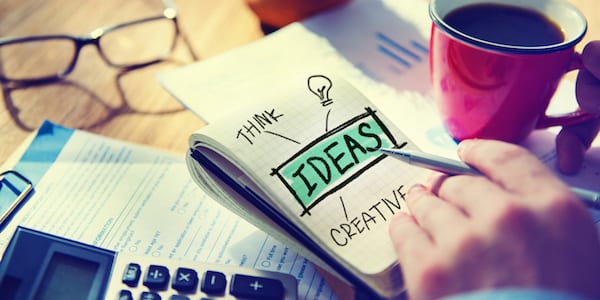
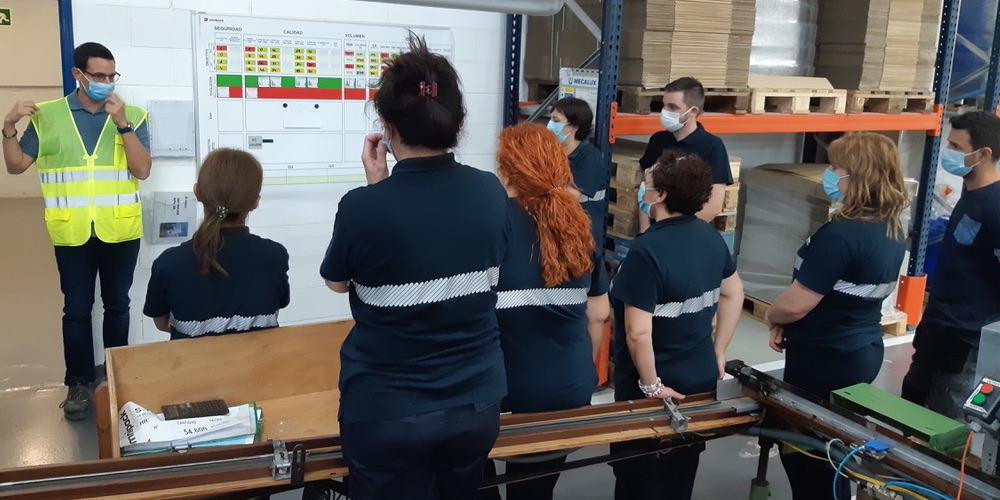
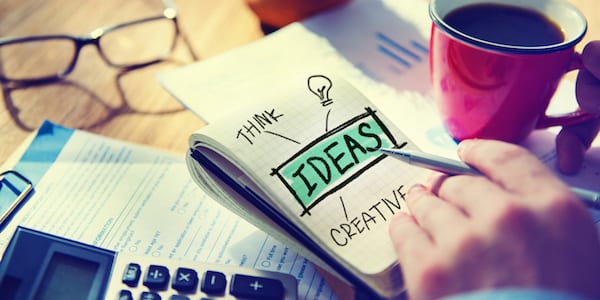
VIDEO – Meetings are critical to create a culture based on teamwork and to establish a learning organization, but their traditional format tends to encourage individual agendas. Not Lean Coffee…
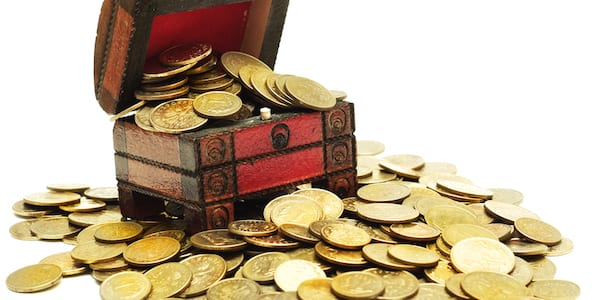
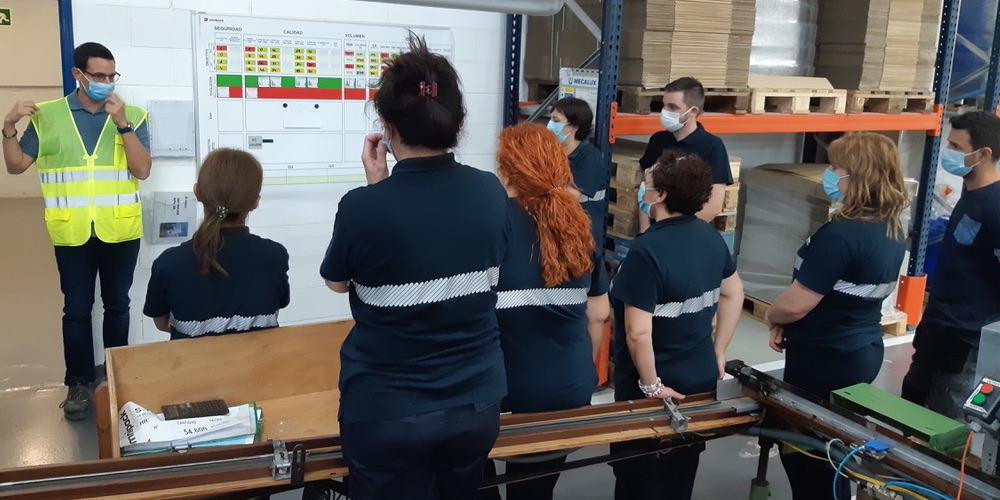
WOMACK’S YOKOTEN - When managed poorly and tied to the wrong performance metrics, financial rewards can seriously damage your organization, Jim Womack warns in his latest column.
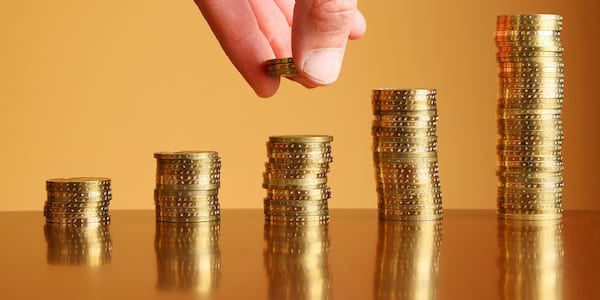
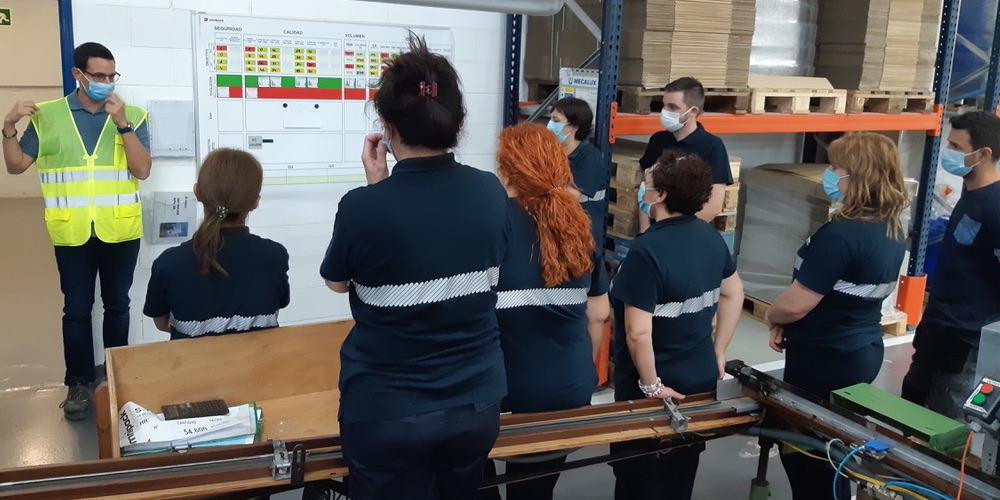
INTERVIEW – How many times have you been asked, “What is the ROI of lean?” Jean Cunningham provides her insight to help you measure the financial impact of your lean improvements.
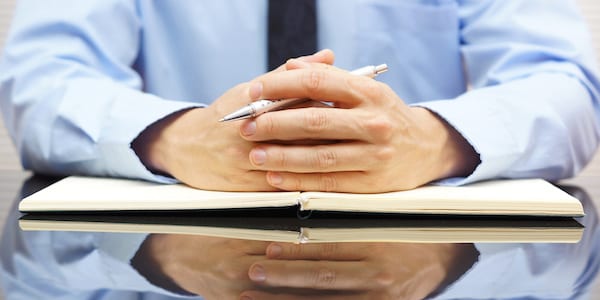
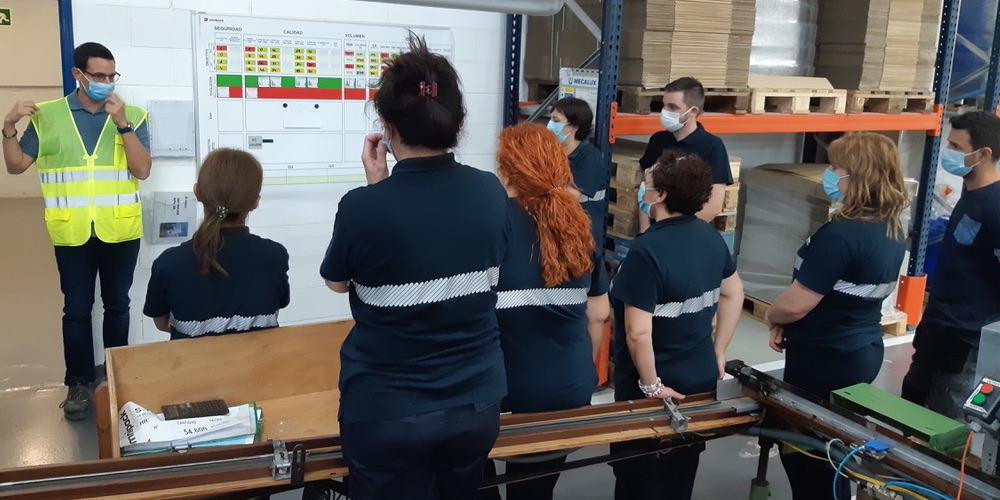
FEATURE – Most organizations rely on the support of lean consultants to bring their transformations forward, but how can they make the most of their expertise and knowledge?
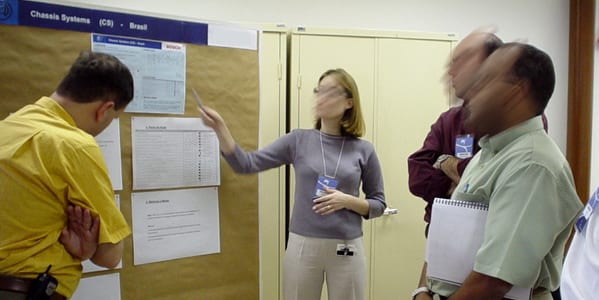
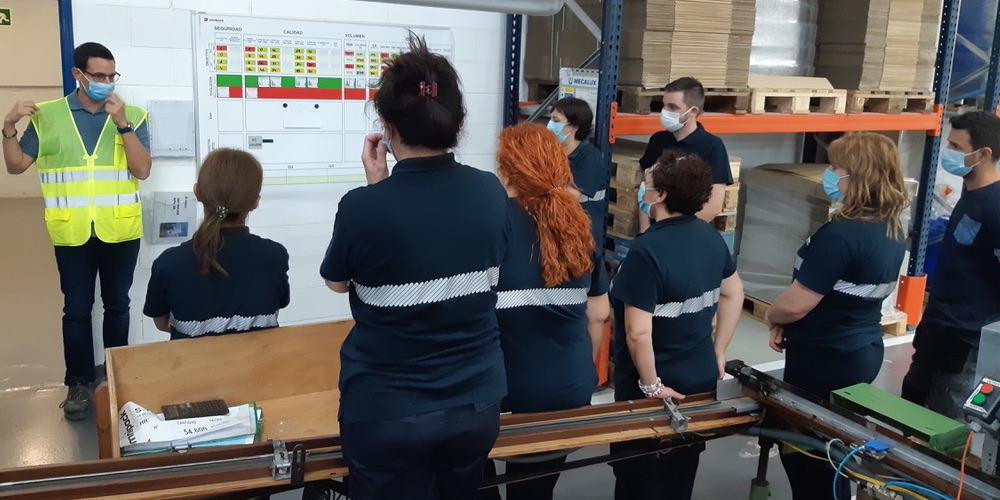
FEATURE - With daily management at the heart of its modus operandi, an organization will be able to quickly identify deviation, start solving problems and make strategy deployment a success.
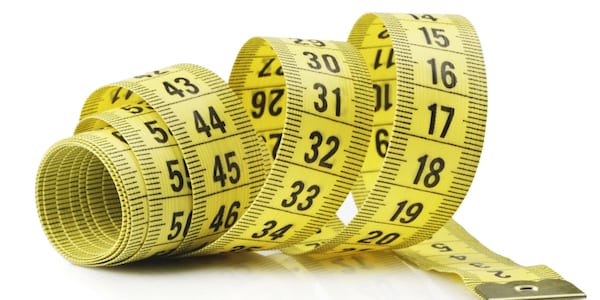
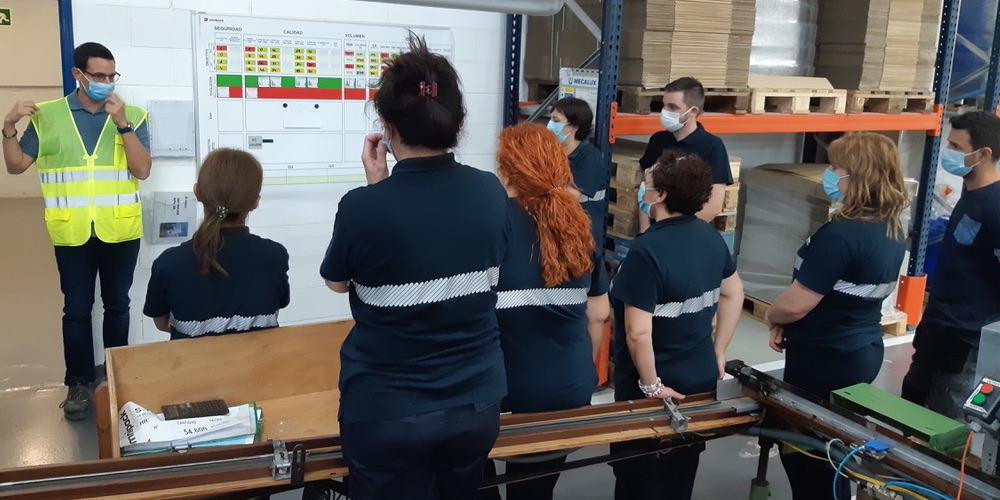
WOMACK'S YOKOTEN - Senior leadership must learn to understand the work if they are to move away from the mindless metrics that lead managers to "game" numbers or to shift responsibility on to other departments.
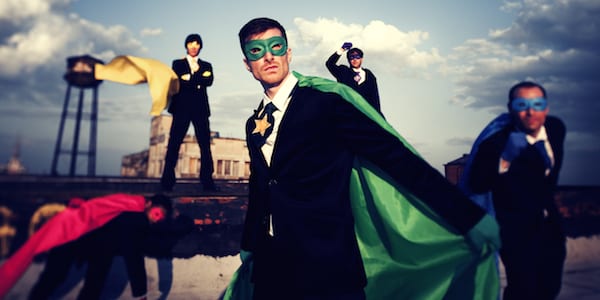
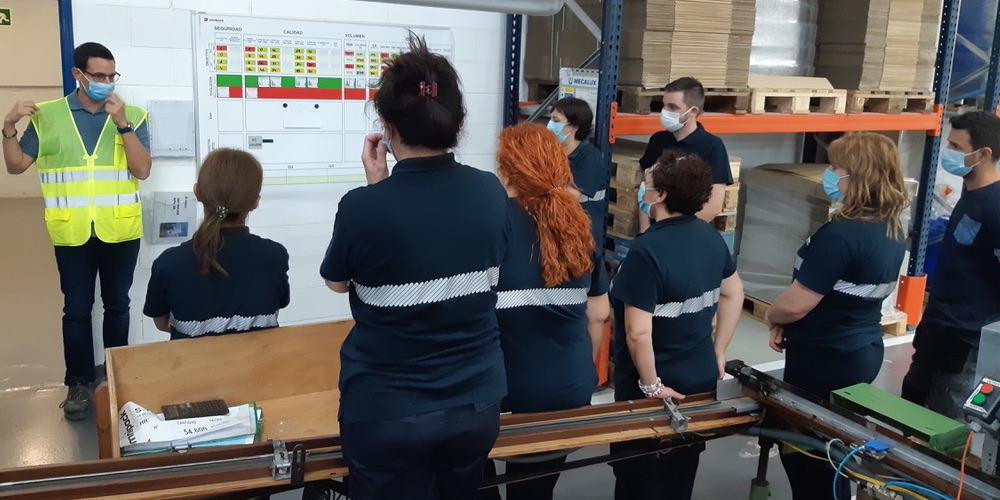
FEATURE - Michael Ballé shares a few thoughts on leadership and respect for people, and tells us why lean management is the only way to make adaptive change a way of life.
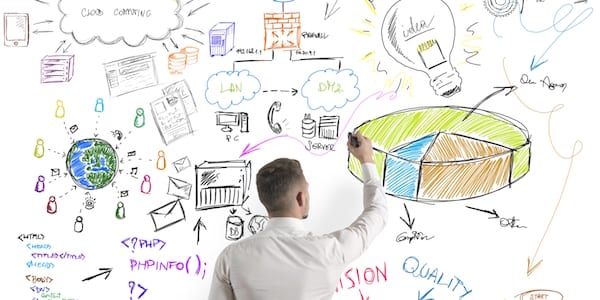
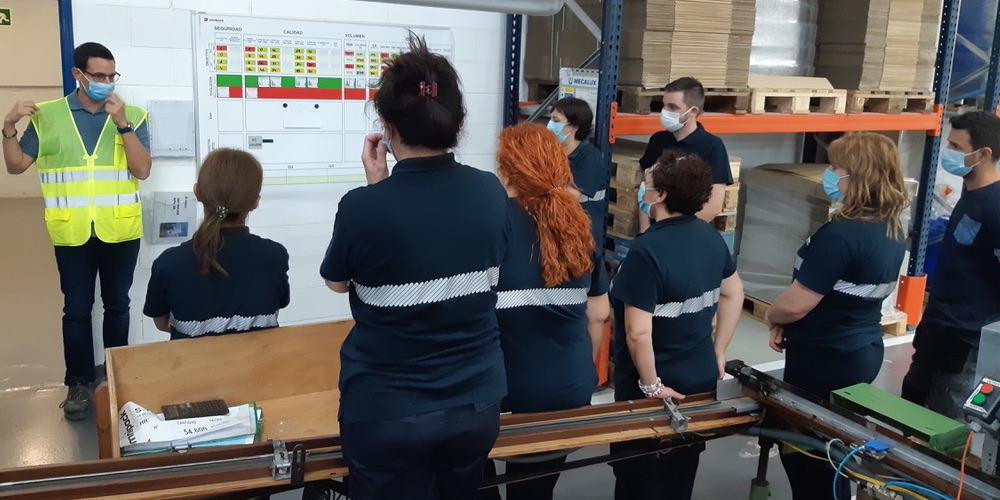
COLUMN - For her latest column, Sari Torkkola describes the initial steps that must be taken to move towards becoming a lean CIO and warn us against some of the pitfalls along the way.
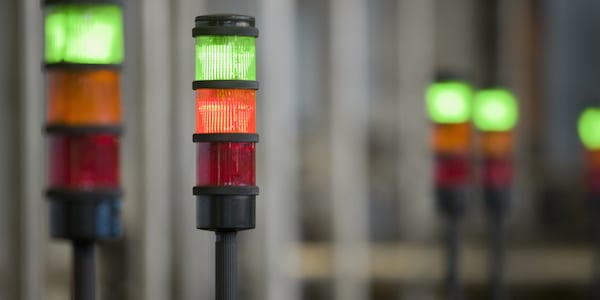
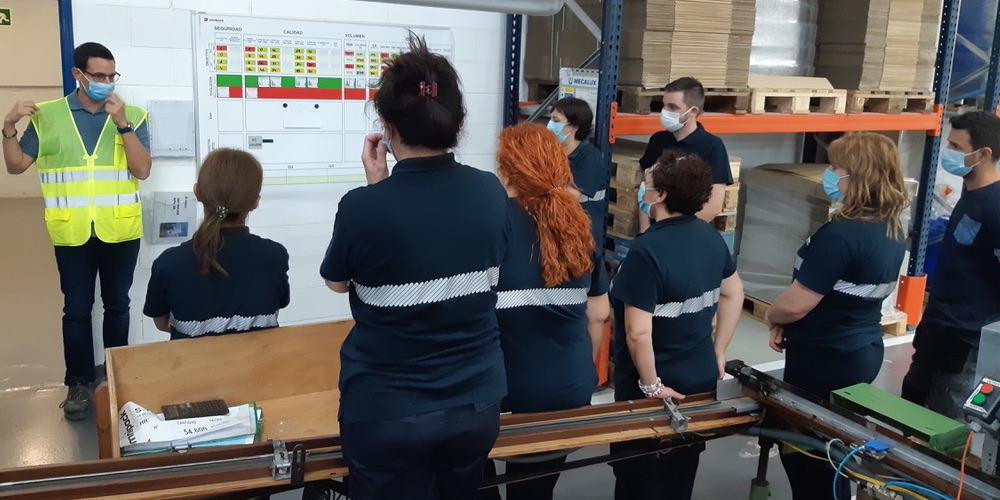
WOMACK'S YOKOTEN - Given the name of this column, it only makes sense to analyze the word yokoten. So, how can we effectively help others to apply what we learn at the gemba? What makes yokoten successful?
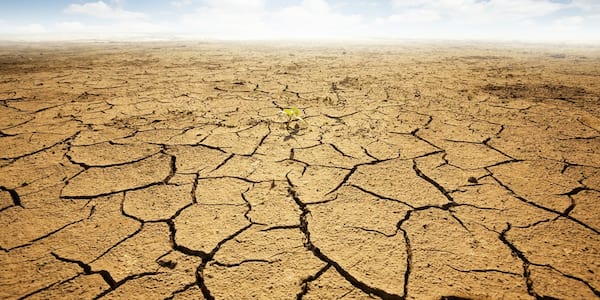
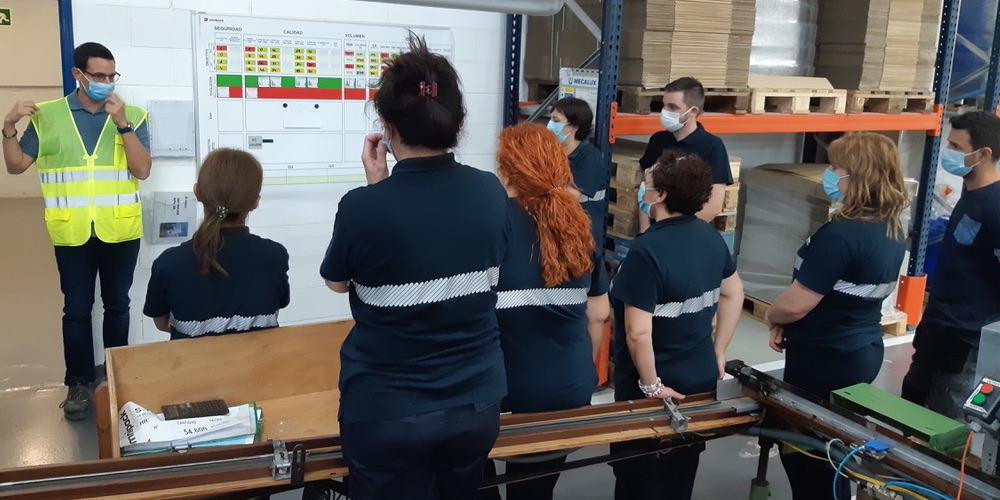
FEATURE – A kaizen suggestion scheme has the ability to unlock the potential of lean change in our organizations, but too often our mistakes kill it before it even has a chance to take off and gain momentum.
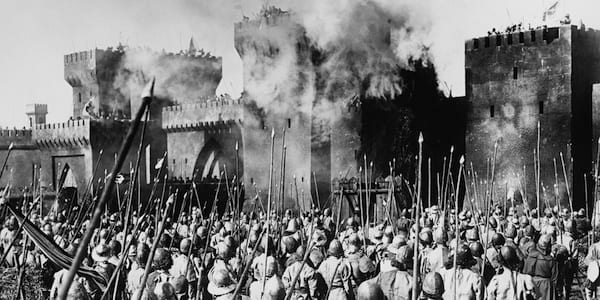
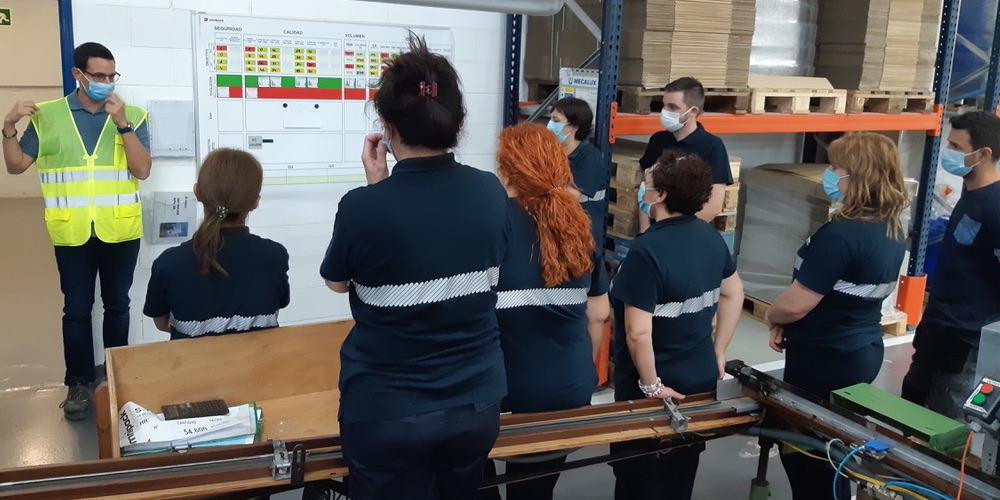
WOMACK'S YOKOTEN - Every practitioner has encountered employee resistance to lean at some point. Here's a few tips on how to win over naysayers and perhaps even turn them into some of your biggest supporters.
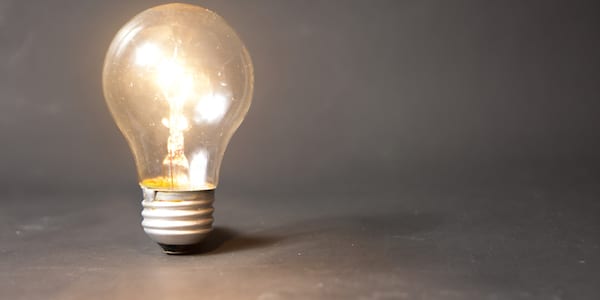
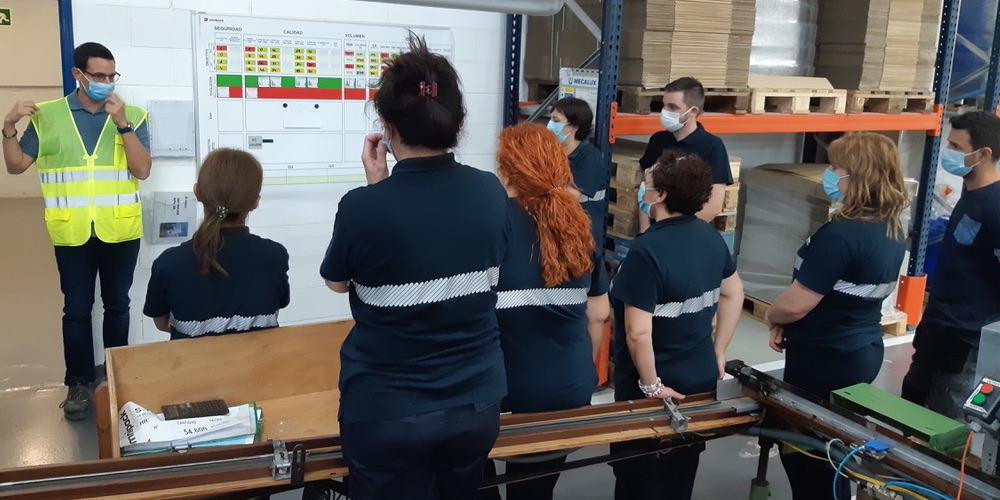
ARTICLE - A-ha moments... we have all had one at least. In this personal account, the author reflects on what his own experience has taught him about changing our mindset and being stuck in our ways.
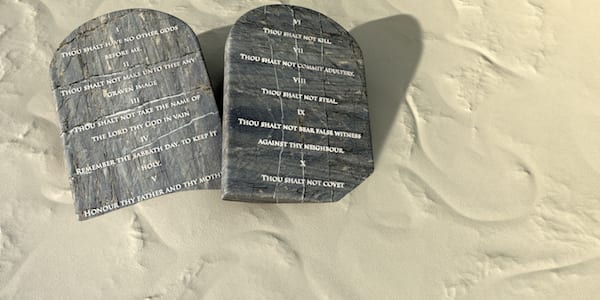
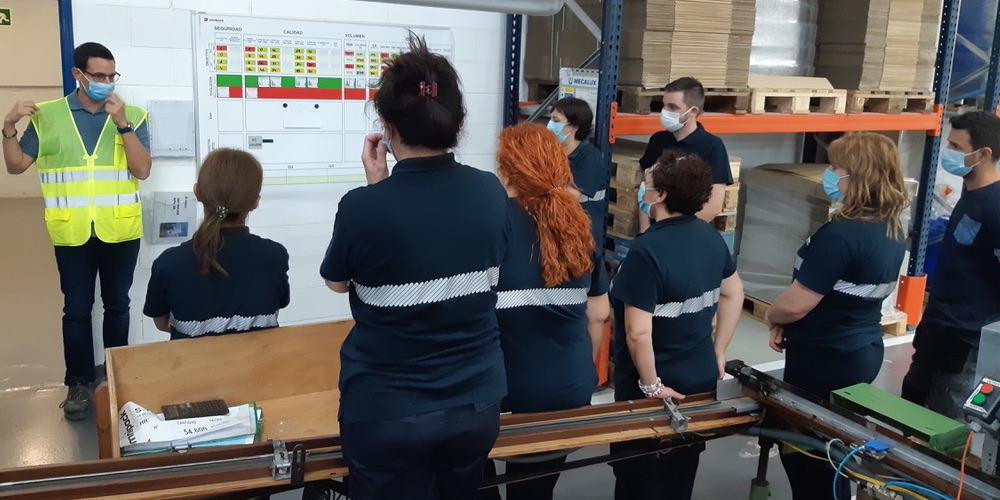
FEATURE - One big "introduction to lean" course isn't enough to teach people continuous improvement. Training, and therefore learning, must happen on a daily basis. Here's the Ten Commandments of lean training.
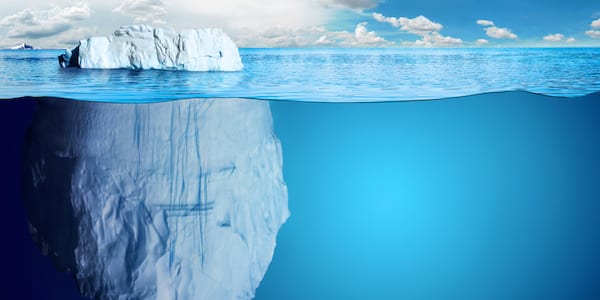
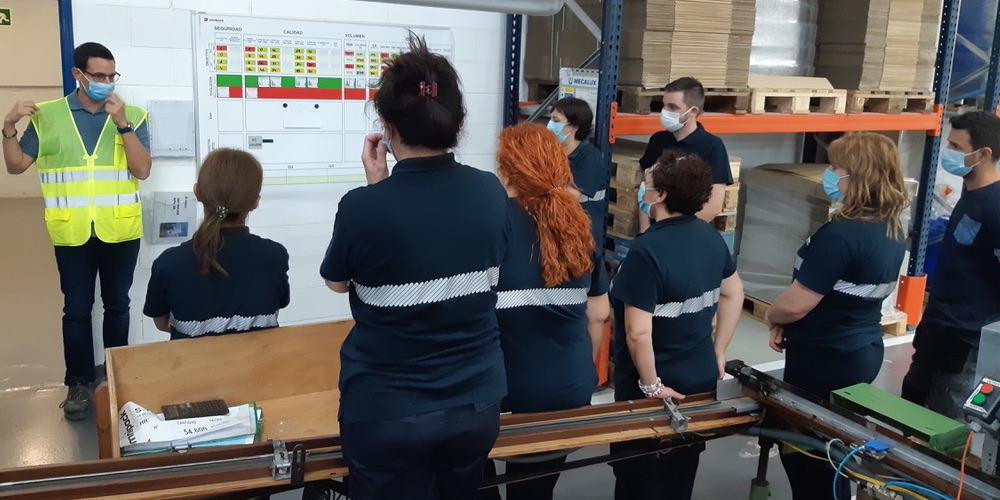
ARTICLE - What is lean? We all like to think that we know. This personal story reminds us all of how elusive the methodology can be, and how determined a practitioner has to be to fully grasp it.
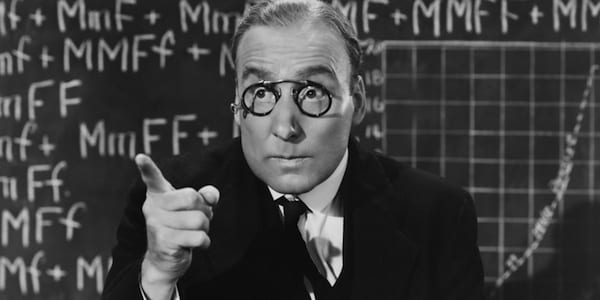
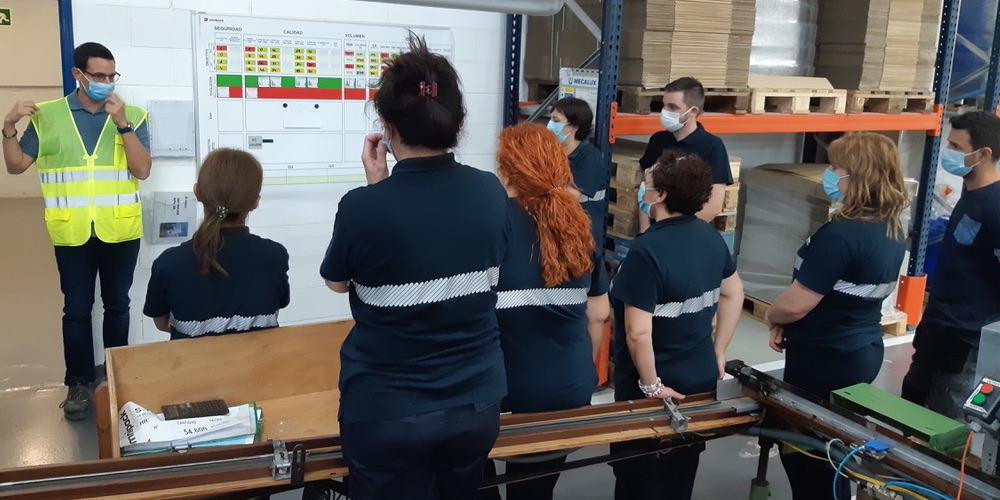
ARTICLE - Organizing for learning is critical to sustaining your kaizen efforts and improving your company. Choose the right managers, make sure they can self-develop and develop others, and help lean to take root.
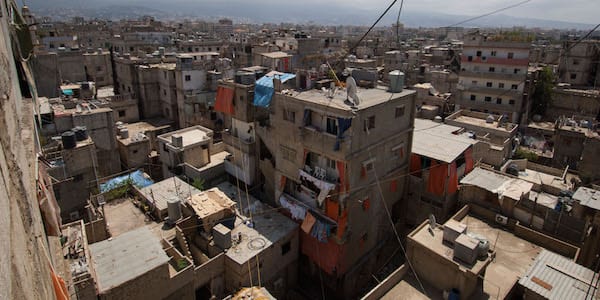
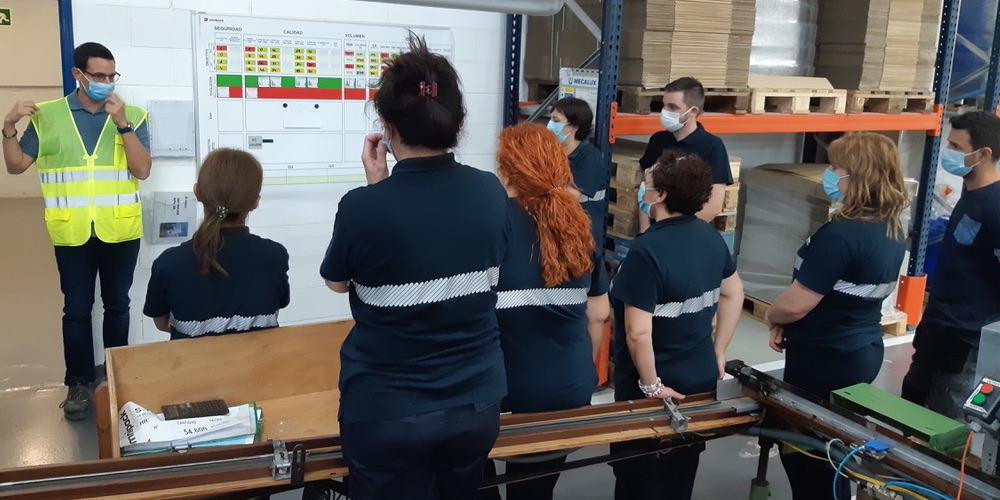
FEATURE – In the Shatila camp south of Beirut, a self-help program is making a difference in the lives of Palestinian refugees, engaging them in rehabilitating their shelters.
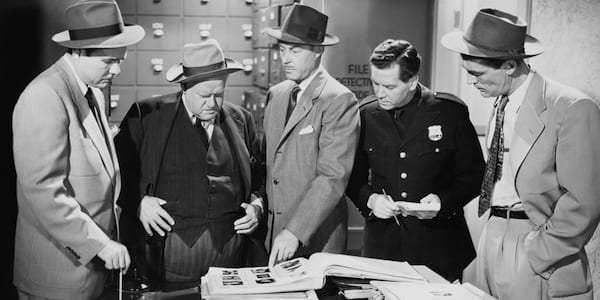
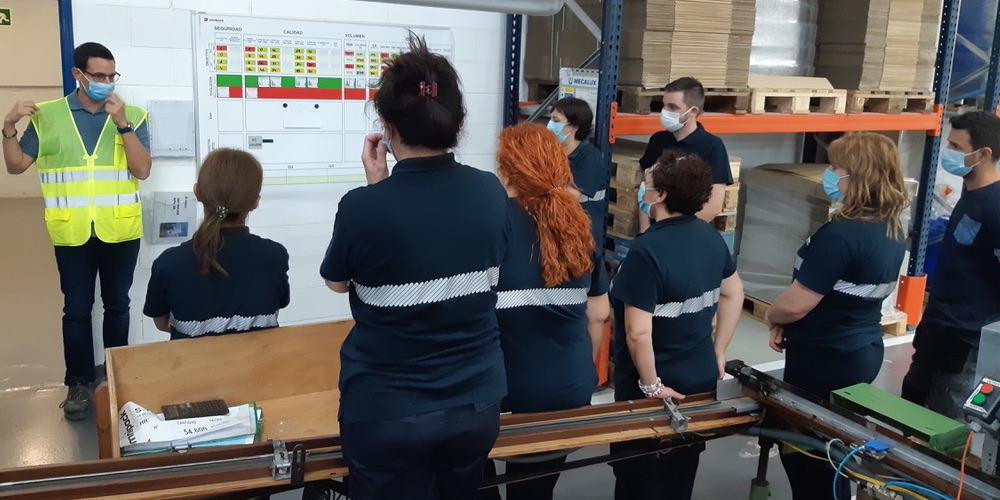
ARTICLE – You need to have a solid and complete process in place if you want your problems to be actually solved, and it is more than just developing an A3 or drawing an Ishikawa.
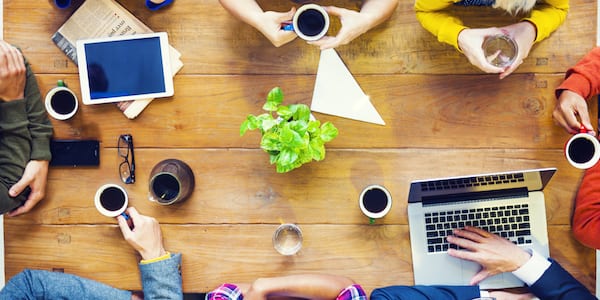
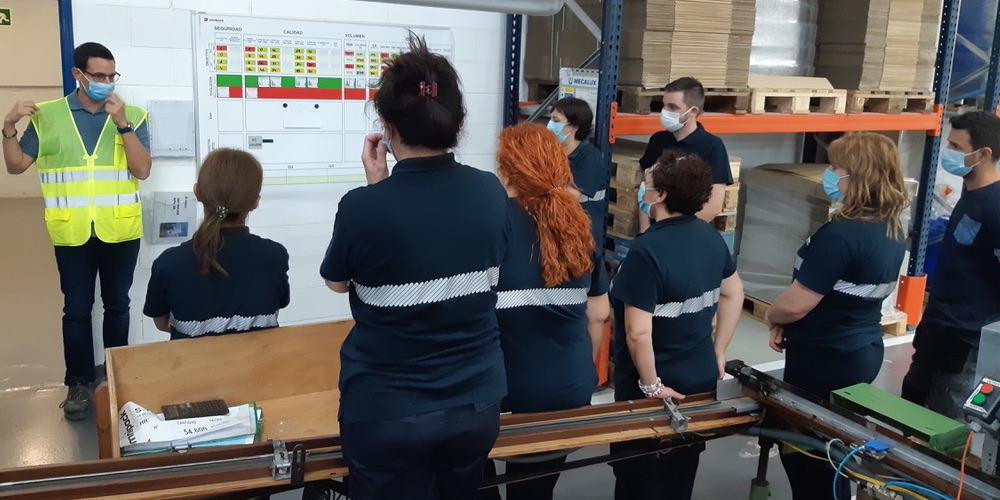
FEATURE - An initial look into the impact of lean management principles on the growth of young organizations hopes to encourage further analysis into why and how lean startups succeed.
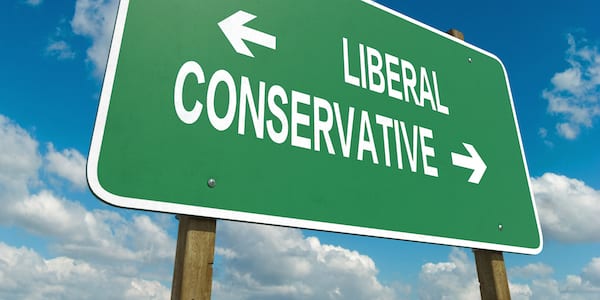
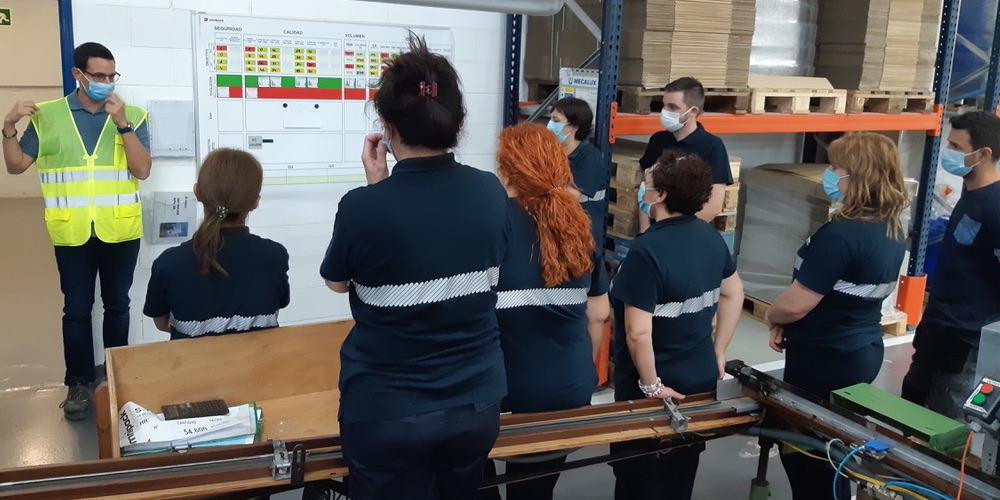
COLUMN - In political terms, is lean management more in line with conservative principles or progressive ideas? Michael Ballé reflects on a tough question.
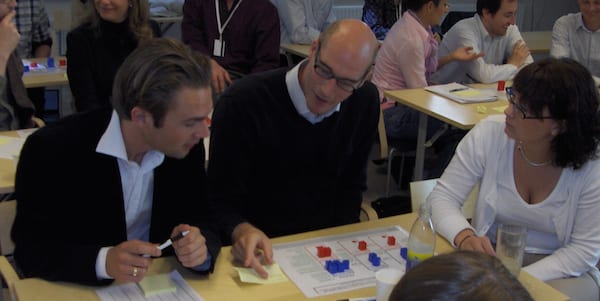
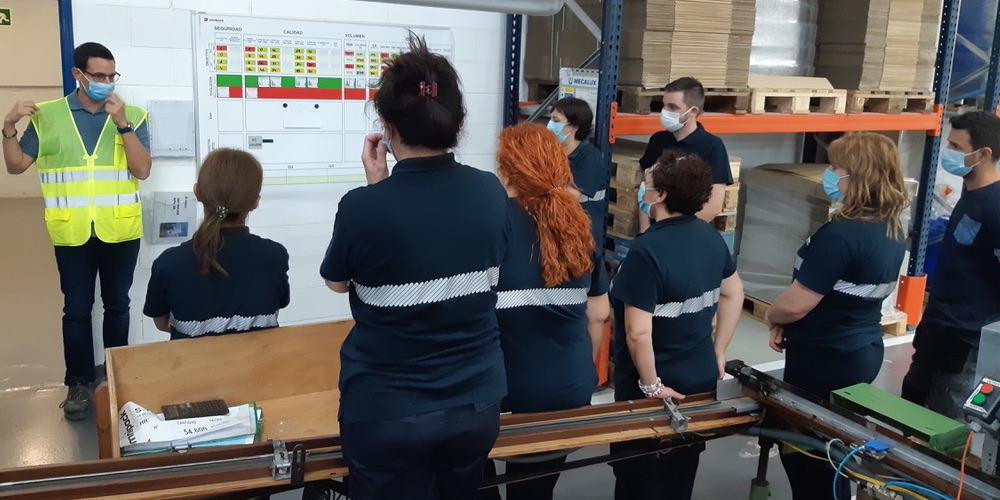
FEATURE – Games can help you to engage people and communicate lean management principles. Here is a number of useful tips and suggestions on how to make training more… playful.
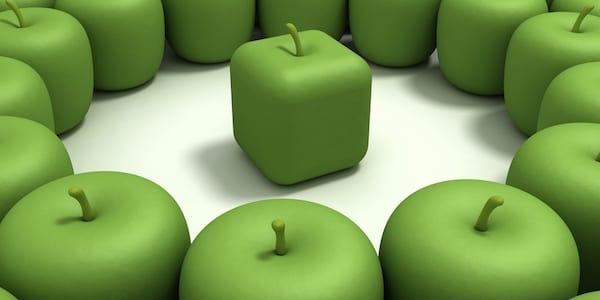
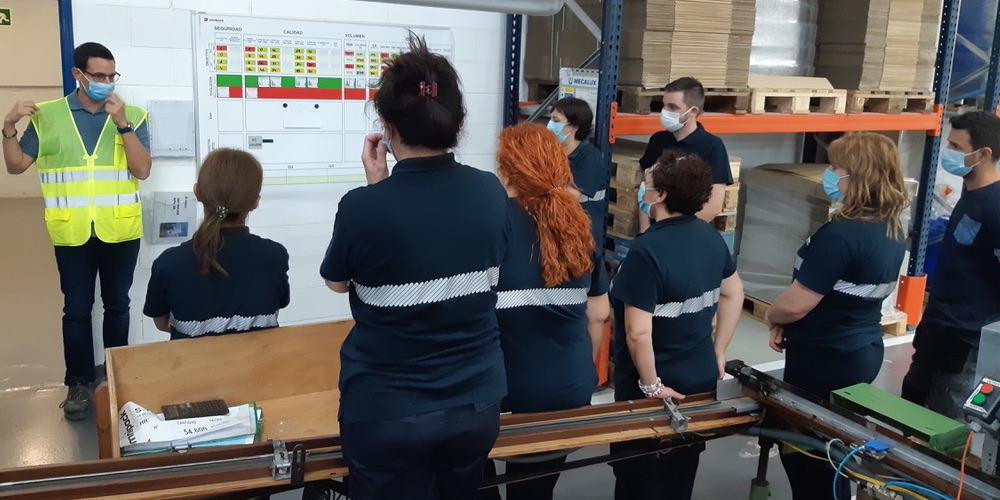
FEATURE – The fifth article in the series Hazards on the road to lean analyzes the role of quality defects in helping to develop a lean management culture in your organization.
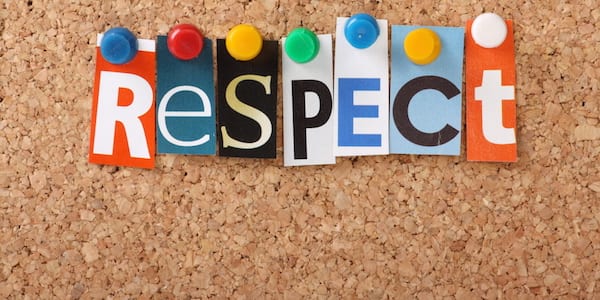
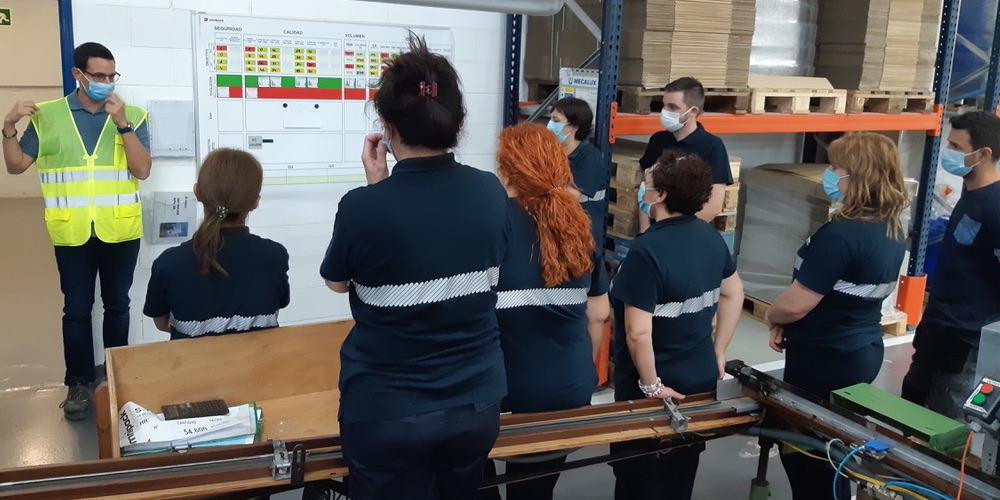
FEATURE - Mission creep, silos and a disengaged workforce are some of the negative effects of traditional management. Michael Ballé offers an alternative based on the respect for people principle of lean thinking.
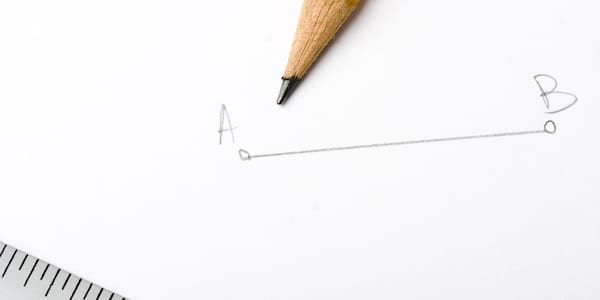
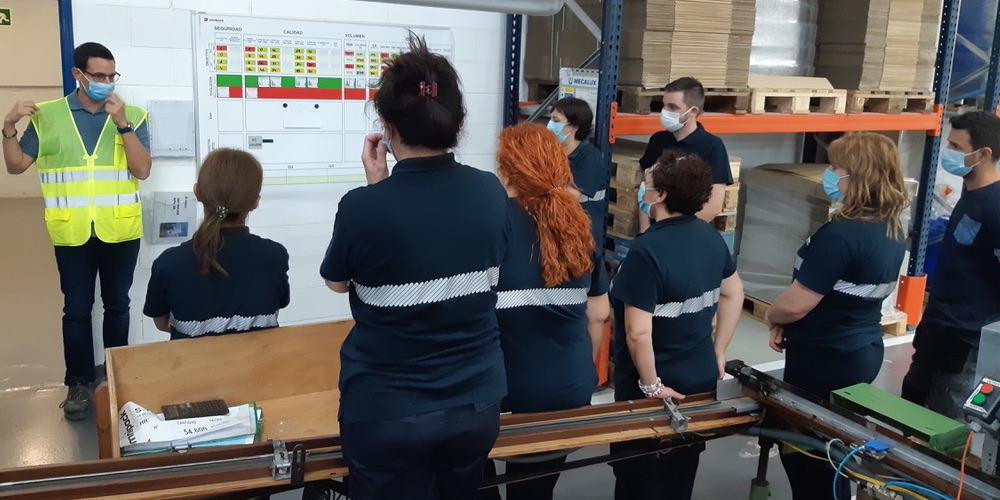
OPINION - What does it take to start a lean implementation? People often hesitate, blaming lack of preparedness at different management levels. Truth is, all you need is two front line people who are committed.
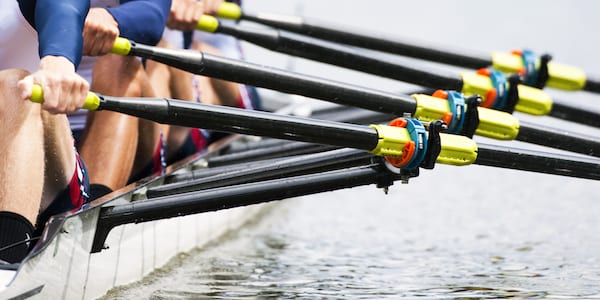
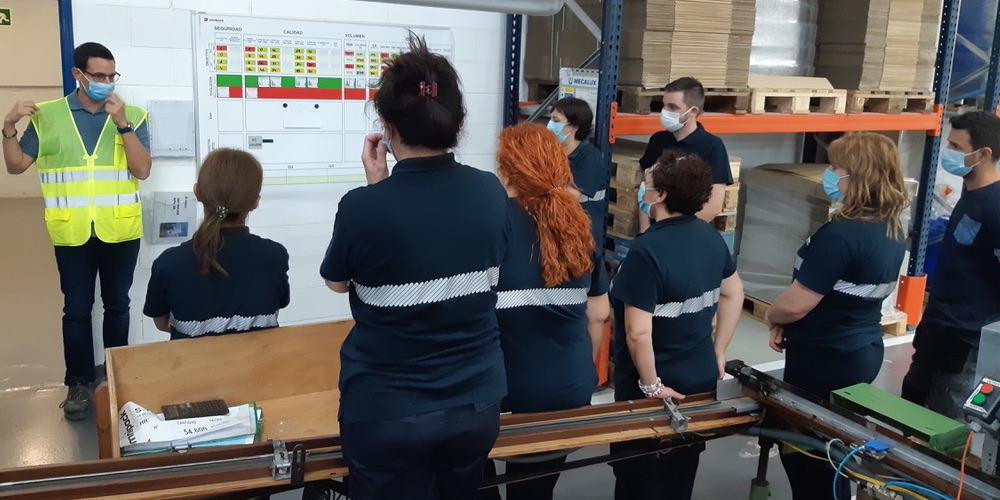
FEATURE – René Aernoudts discusses how to use standardized work in an organization, providing a lowdown of the techniques available to the lean practitioner.
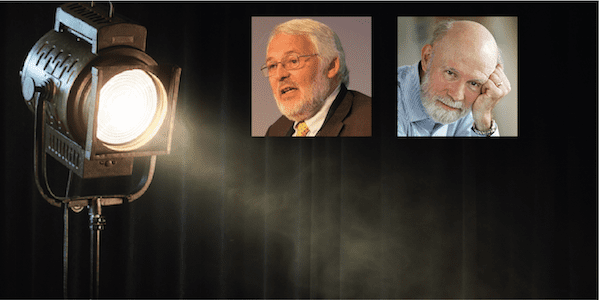
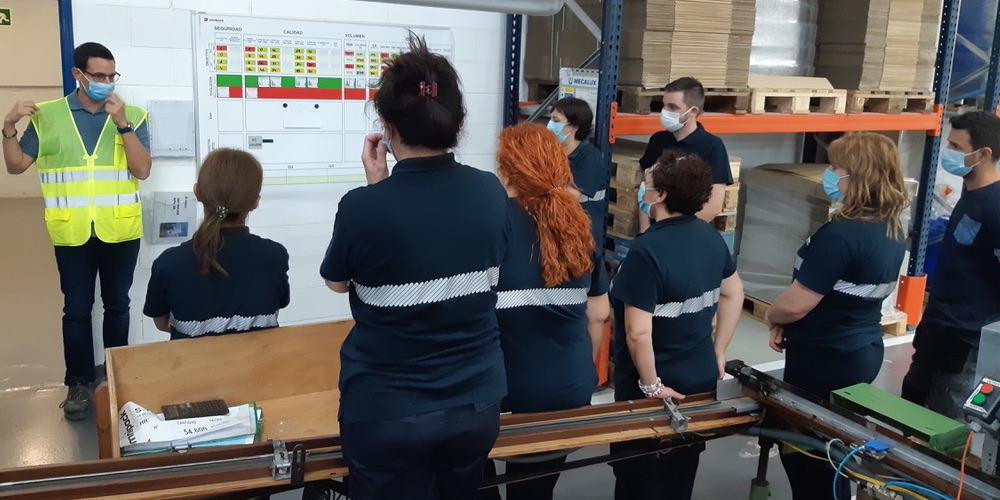
VIDEO INTERVIEW - At last month's UK Lean Summit, we sat down with Dan Jones and Jim Womack, founding fathers of lean thinking, to discuss the evolution, current state and future of the methodology.
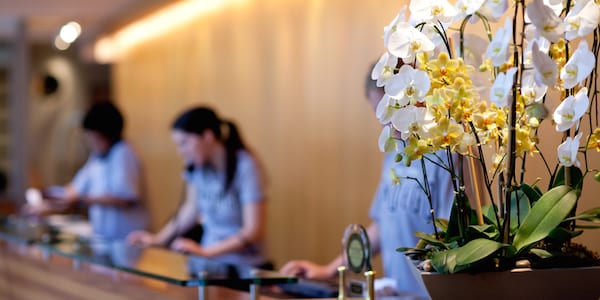
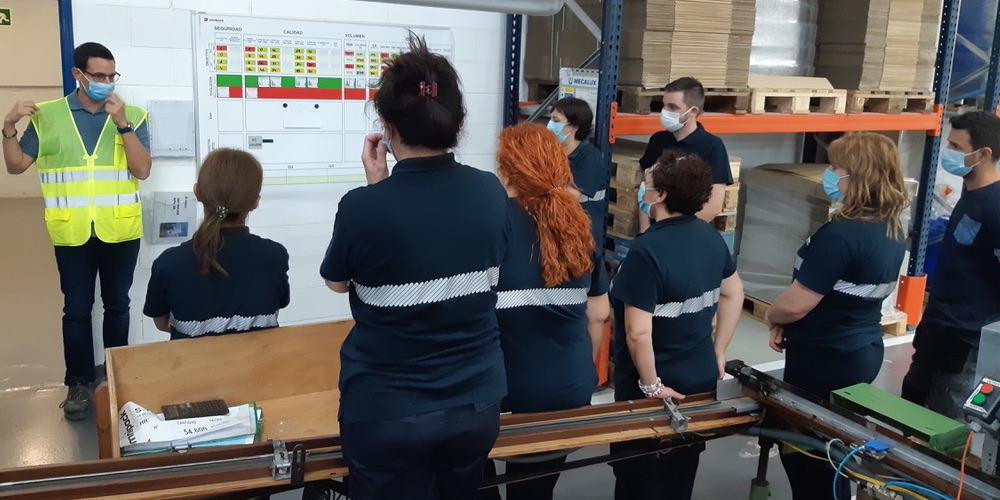
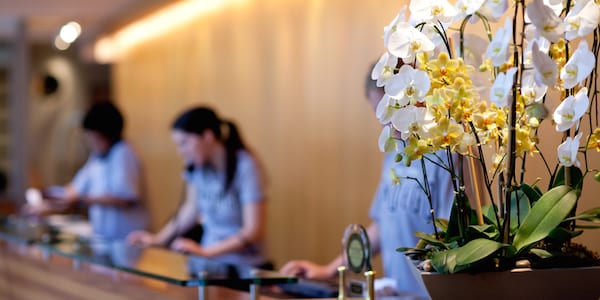
ARTICLE - To operate successfully we need systems, but as we grow these often give us "big company disease." The solution is bringing leadership at work level to really guarantee customer satisfaction.
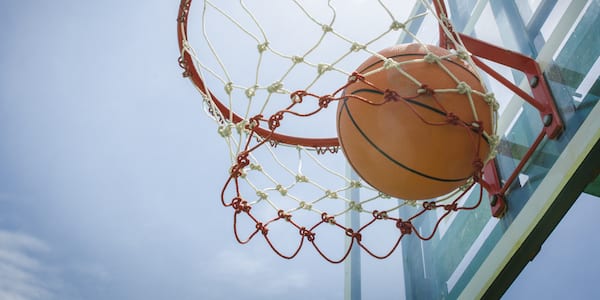
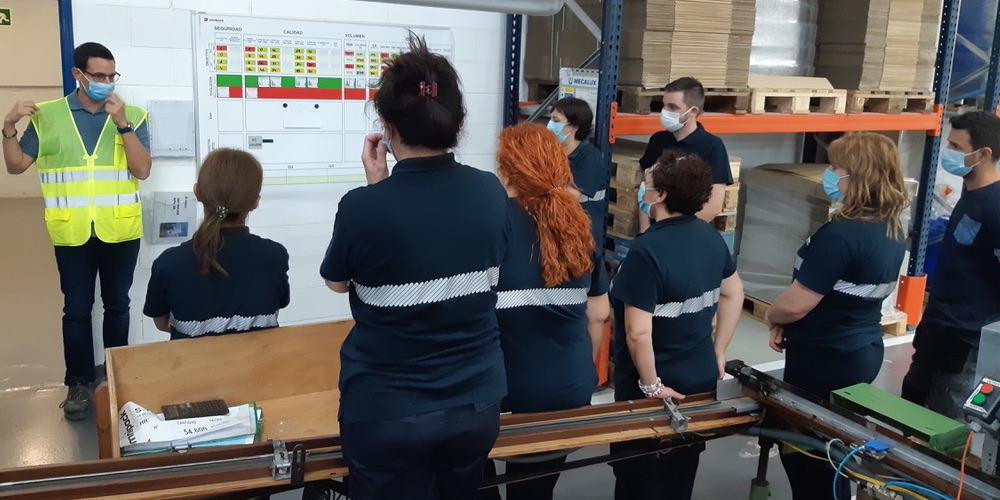
FEATURE – We can have the best processes in place and the best people on payroll, but if our goals are wrong our drive towards lean management won't be enough. Part 3 of Hazards on the road to lean.
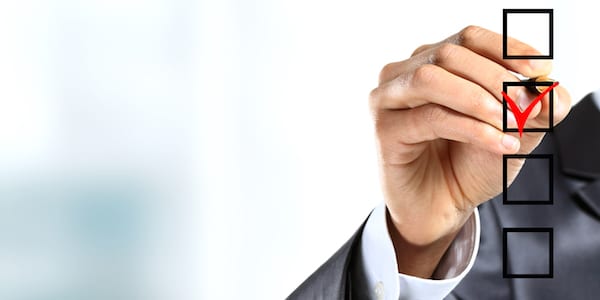
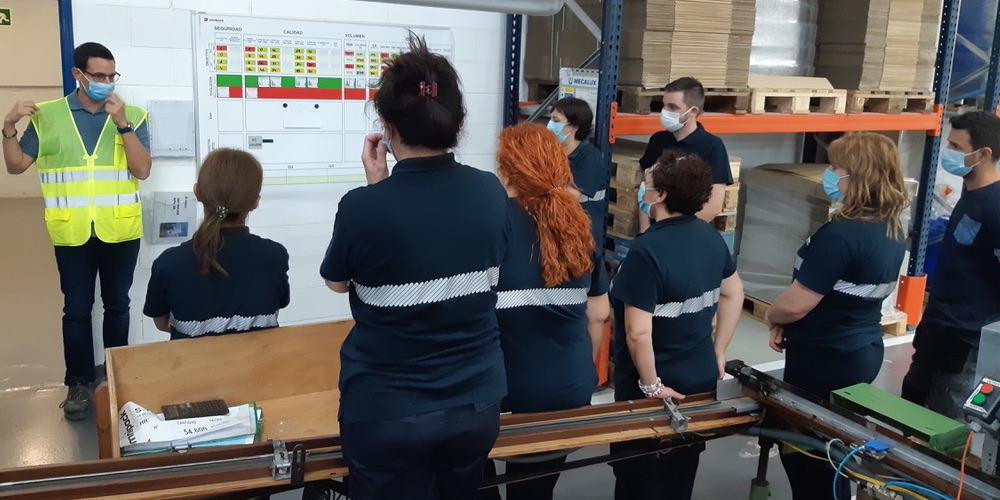
RESEARCH - Standard work is not meant for senior leadership, but there are activities that CEOs can carry out systematically to support a lean management system, starting from problem solving.
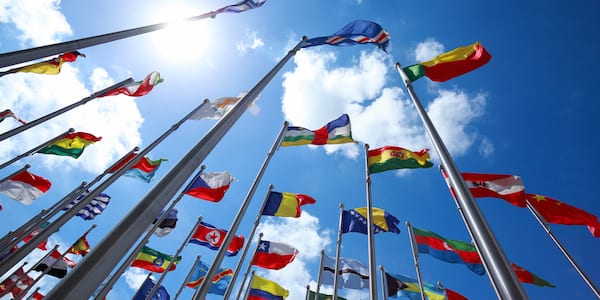
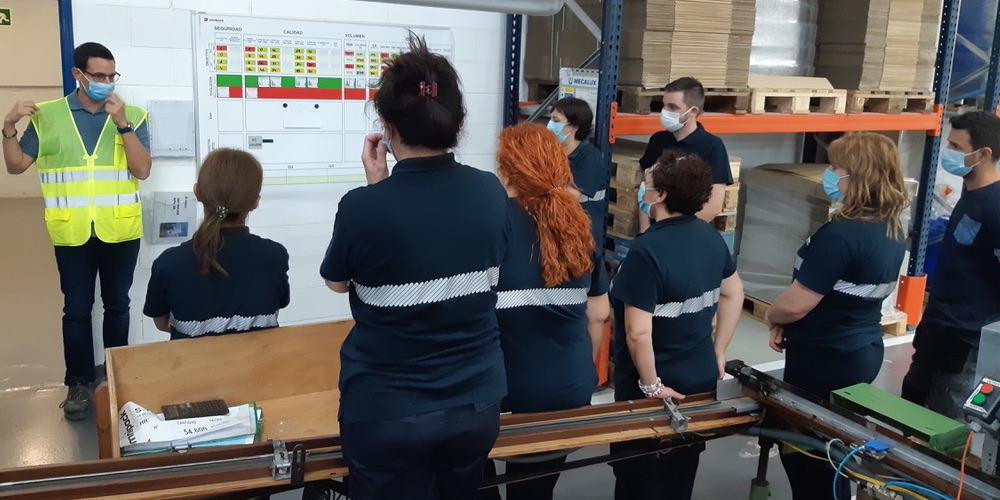
ARTICLE - Are some national cultures better suited to implement lean thinking? This article, based on research on 45 Volvo factories, reflects on the role of local cultures in the rollout of a corporate lean program.
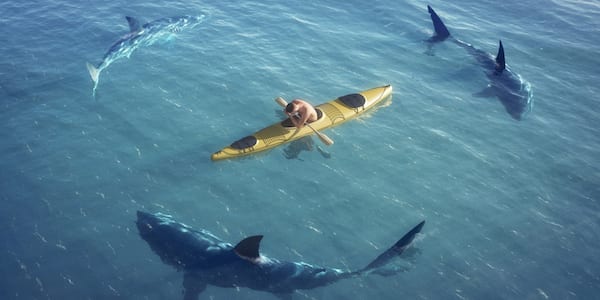
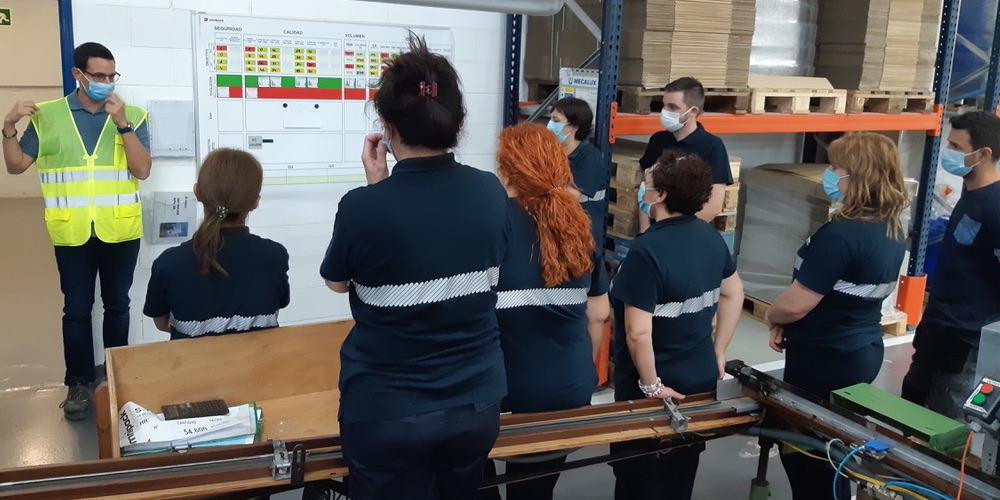
ARTICLE - How can creativity and standards coexist? How do we move beyond silos? How do we fully understand the voice of the customer? Dan Jones reflects on three key questions for the lean movement.
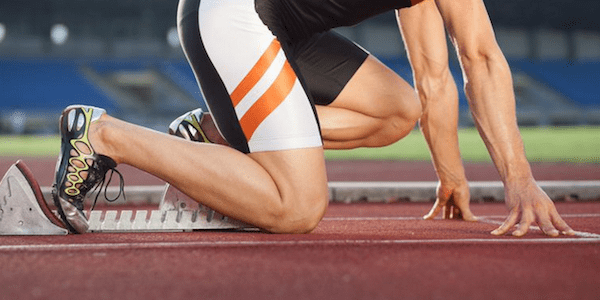
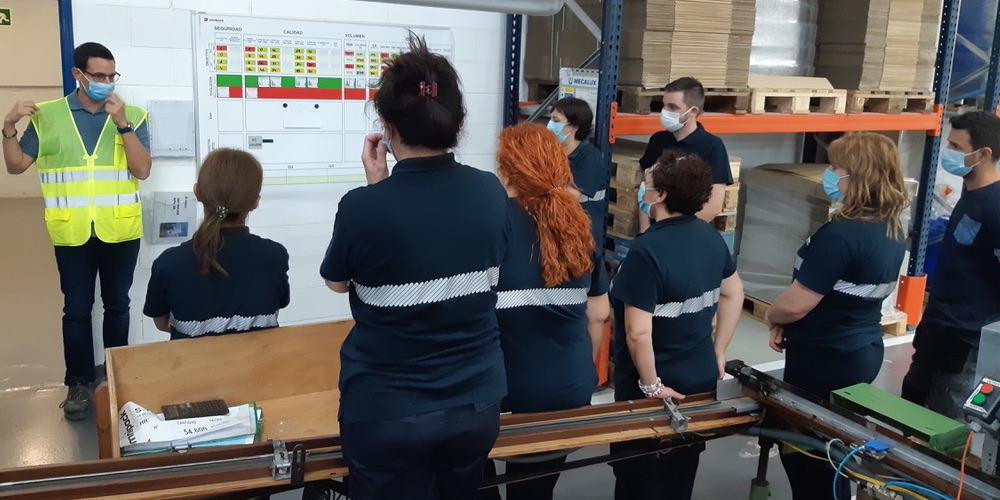
FEATURE - In this new series, our Polish colleagues draw on their experience with customers and discuss the most common mistakes people make in their lean implementations.
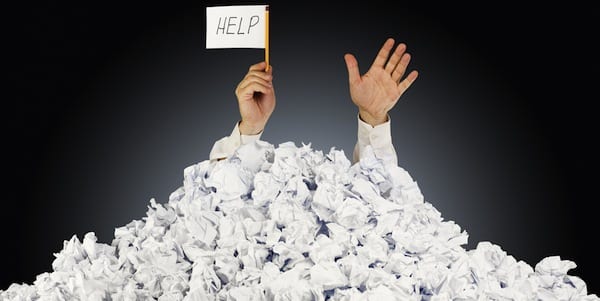
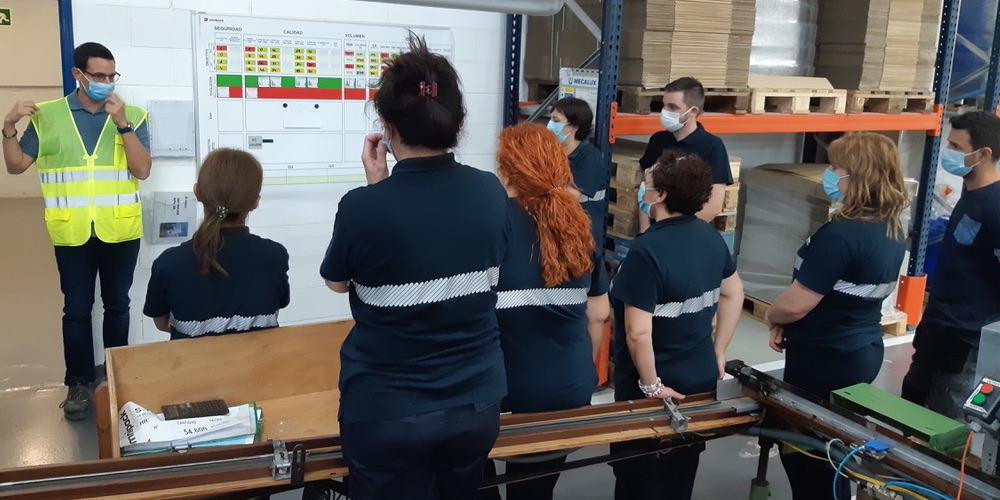
FEATURE - Develop your people if you want to develop a better (lean management) system in your business. This is the key message of this article, which looks at the role of management in an organization and in society.
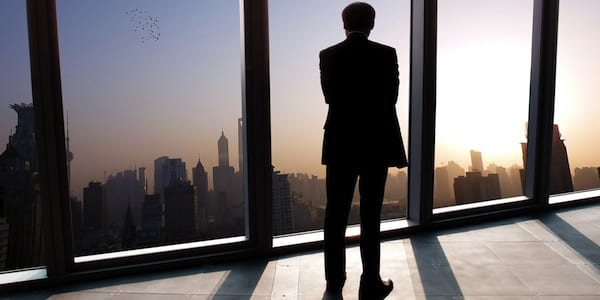
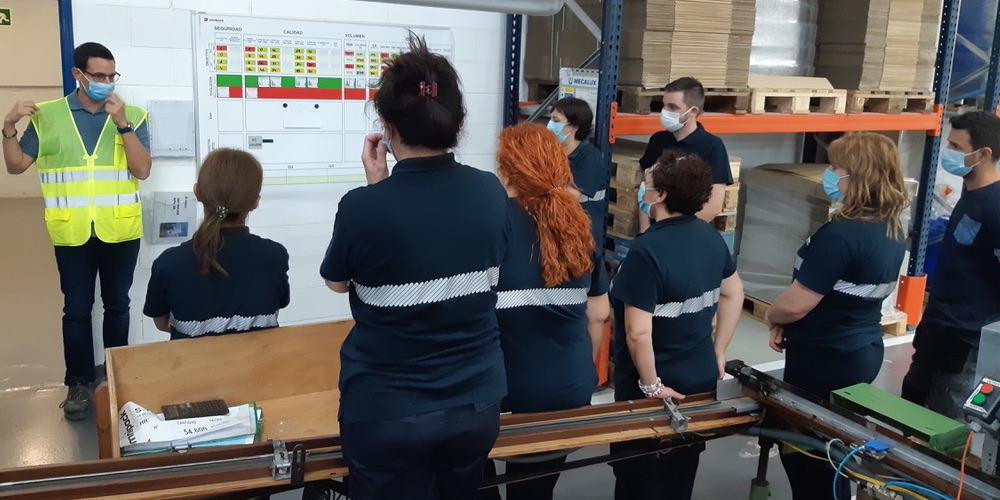
RESEARCH - This interesting study, based on 44 Volvo plants and 200 Volvo interviewees, looks at how the implementation of lean thinking influences a plant’s performance over time.
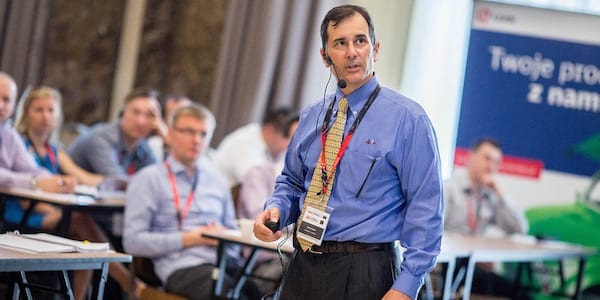
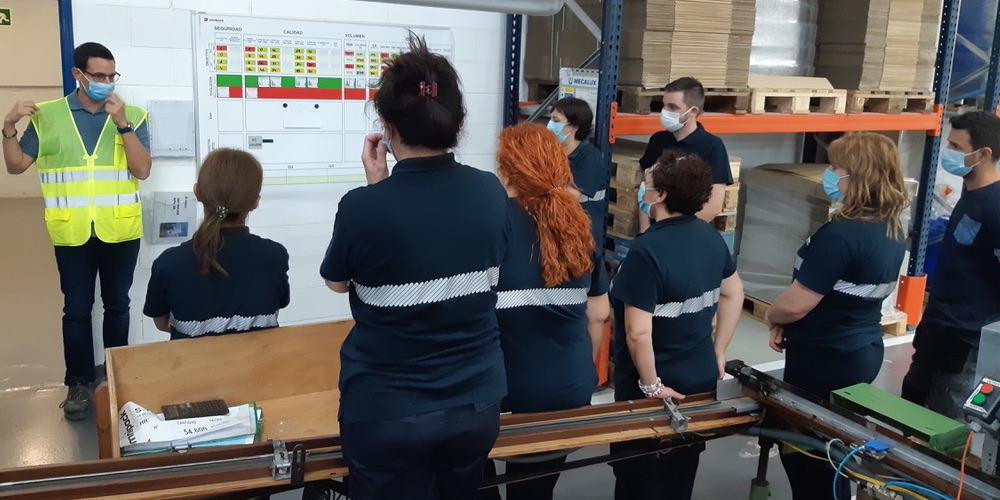
INTERVIEW - What lies at the core of kaizen activity? How has the concept of kaizen evolved over time? Planet Lean’s editor Roberto Priolo discusses these and other topics with kaizen expert Mark Hamel.
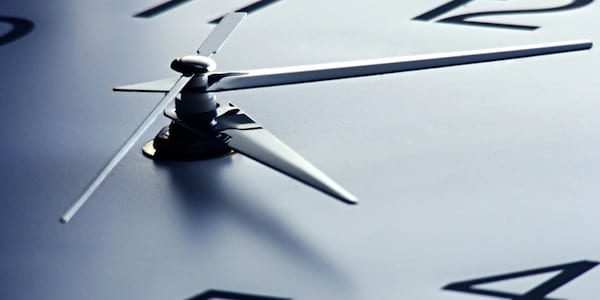
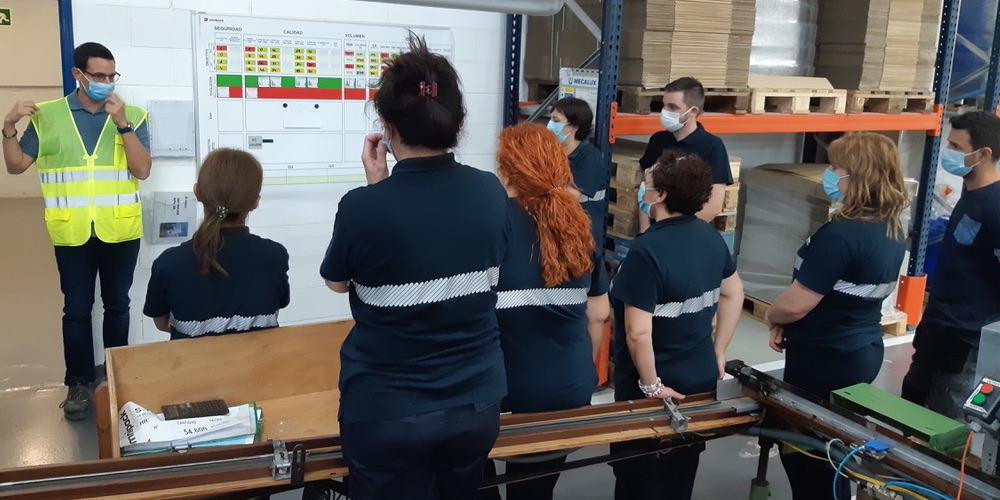
FEATURE - Whether an organization pursues a lean transformation often depends on the early financial results - the low hanging fruit - it's able to achieve. This article offers a model to meet business needs while ensuring a transformation lasts.
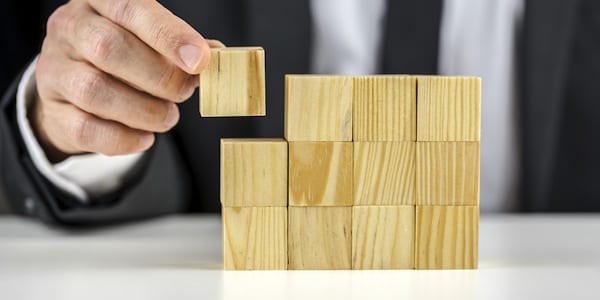
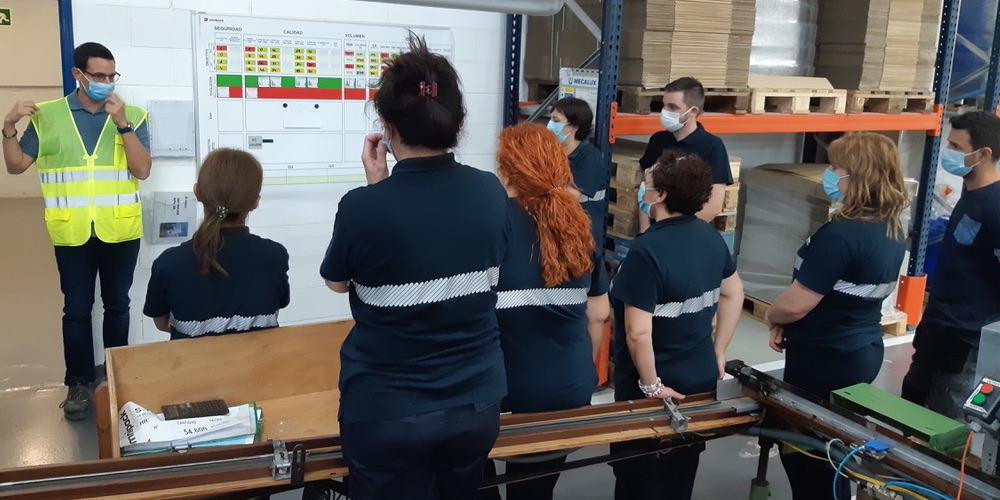
RESEARCH - Offering us a glimpse into how the human mind works and into Toyota's approach to people engagement, this article tells us how to create a better working environment for our employees.
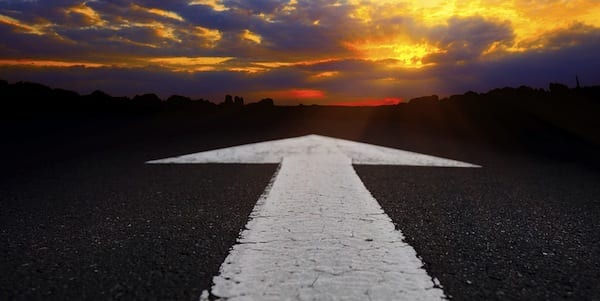
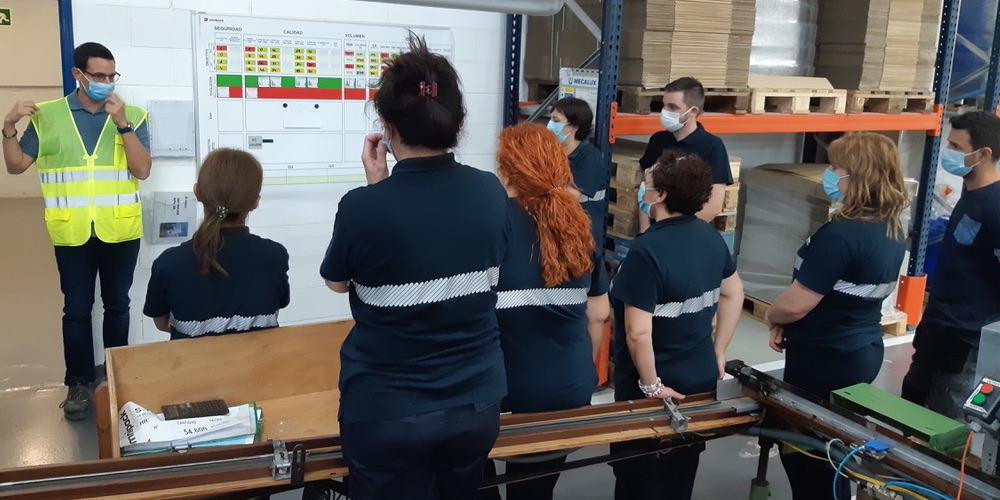
FEATURE - The author looks back at his many years with Toyota and shares some of the key lessons he learned along the way. What a unique company!
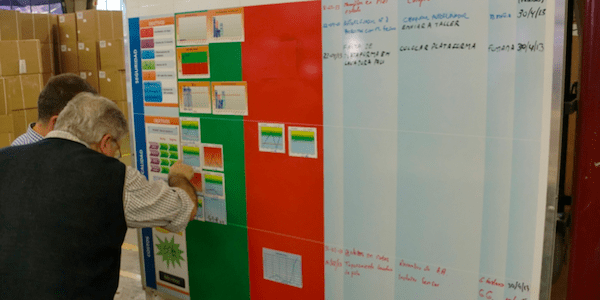
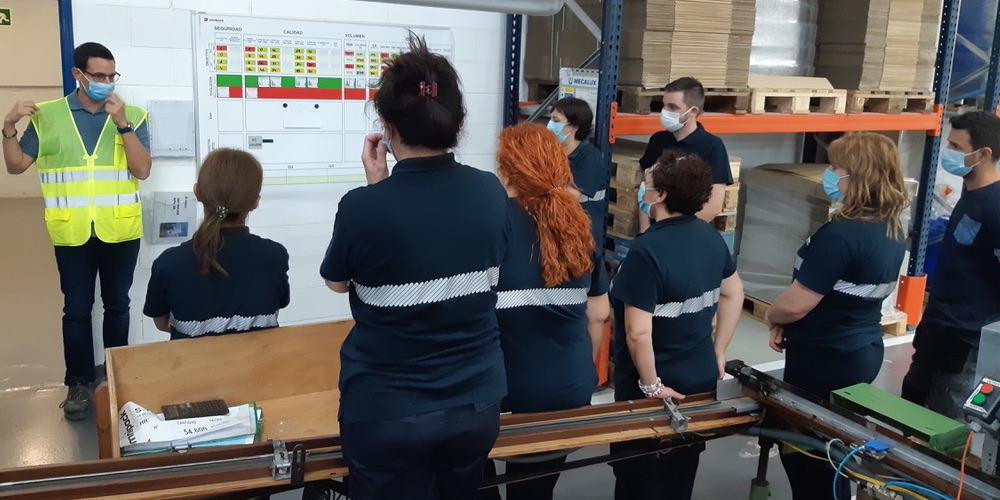
FEATURE - Strategy deployment is fundamental to a lean transformation, but managers often struggle to understand its importance amid the day-to-day firefighting. This article will tell you how to make hoshin happen.
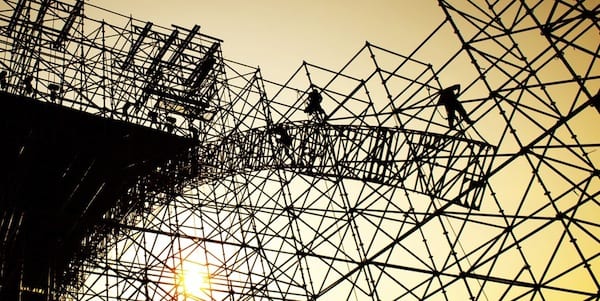
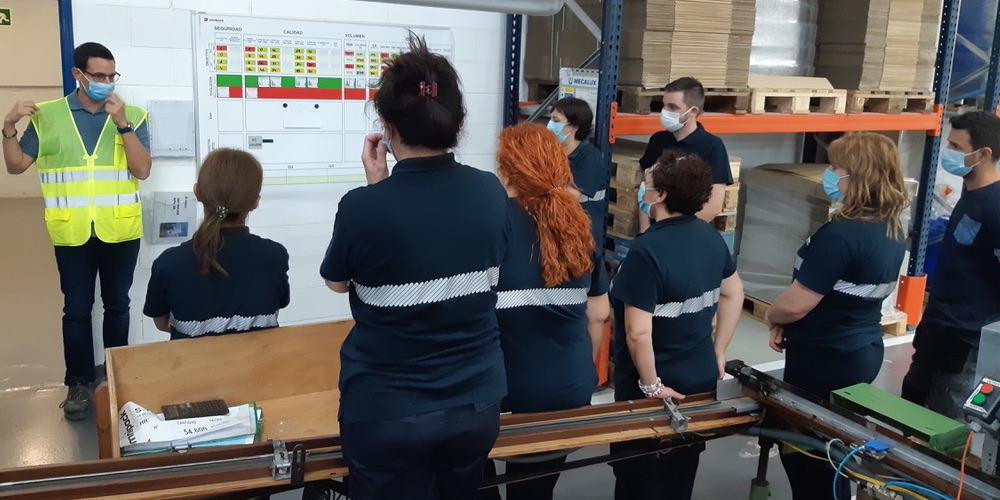
RESEARCH - For most CEOs, working with a sensei is common practice. Yet, many questions remain on this role. This paper aims to bring clarity to the "sensei mystery".
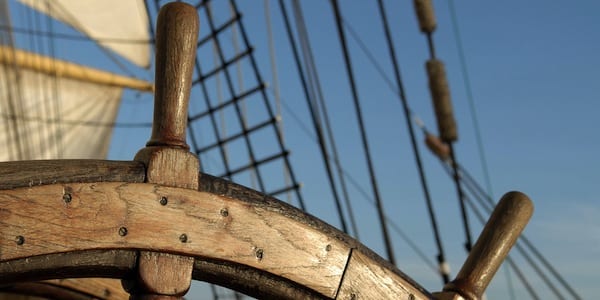
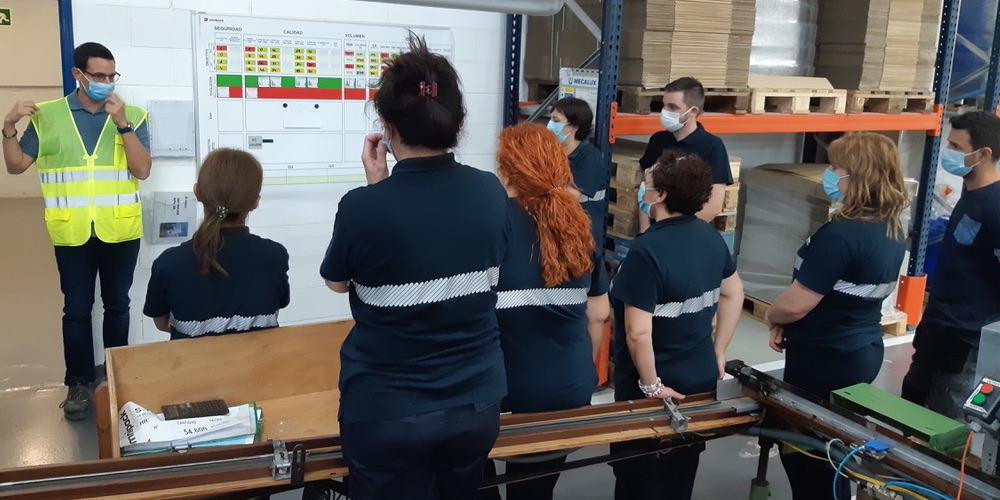
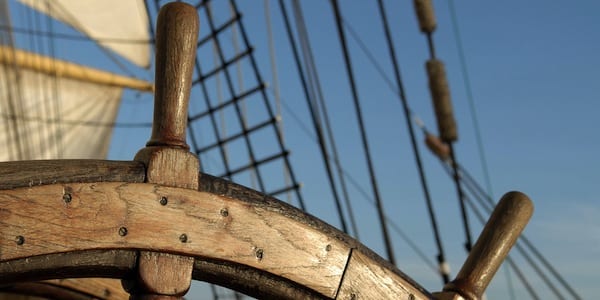
FEATURE - We are often told that employee resistance to change is natural, but it’s really just the result of a wrong approach to lean thinking. Learn to effectively engage people and change will follow.
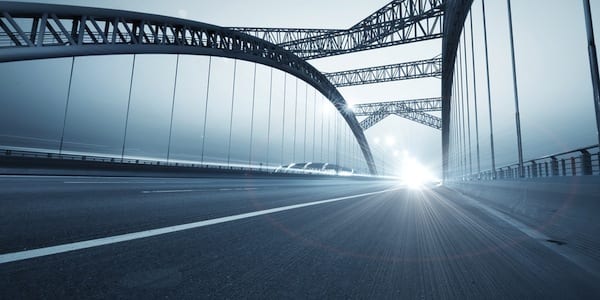
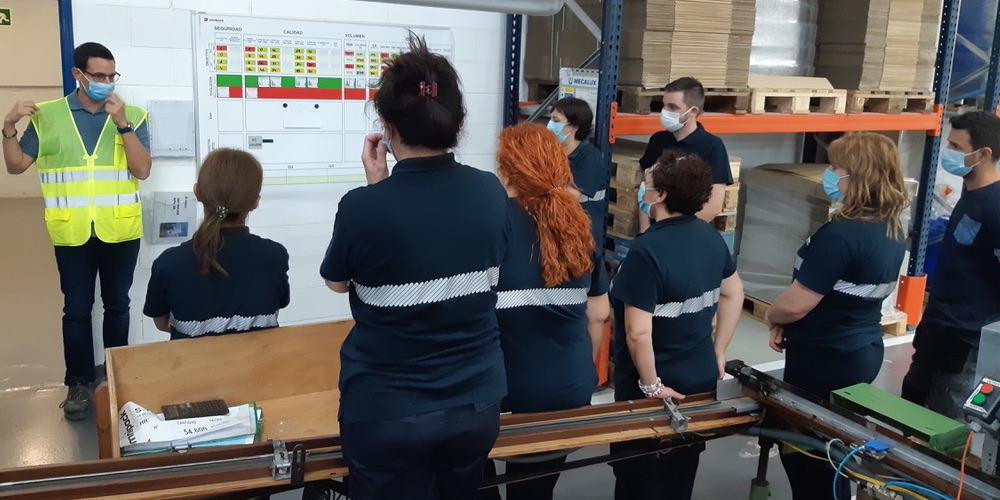
COLUMN - What does lean do for people in your organization? This column explores how their way of thinking changes as a culture of continuous improvement and problem solving takes root.
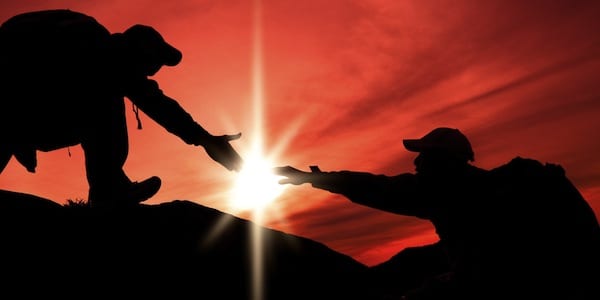
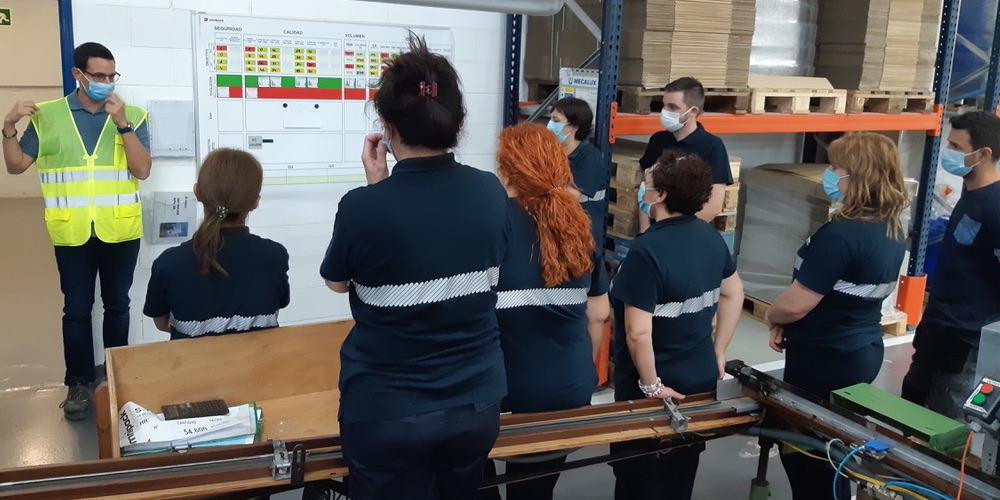
FEATURE - Two weeks ago, the authors shared their thoughts on mindset. In part 2, they discuss how to grasp the true spirit of lean.
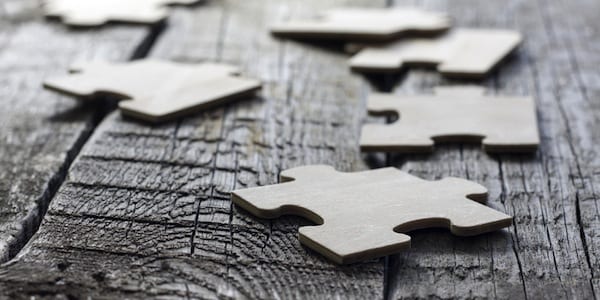
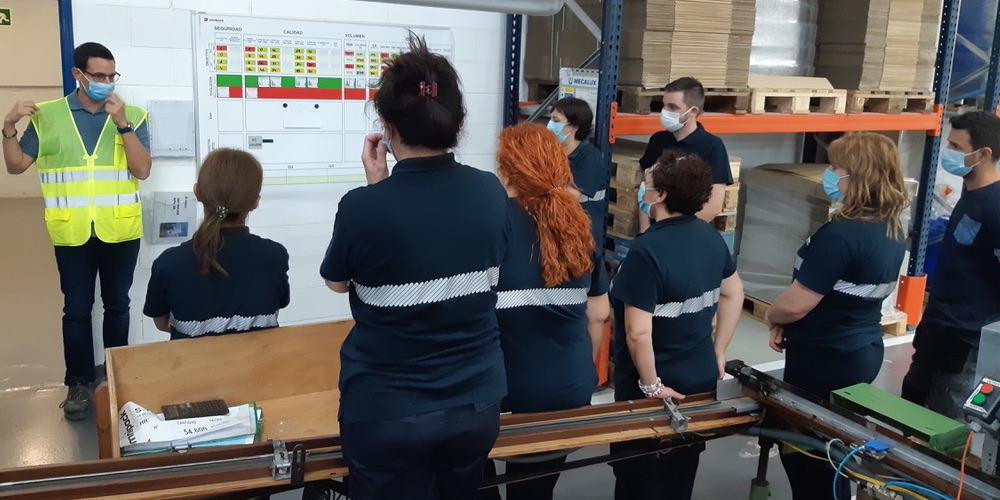
FEATURE - This set of guidelines will help you to understand how to properly structure your lean transformation, keeping into account the entire organization as it tries to embrace and manage change.
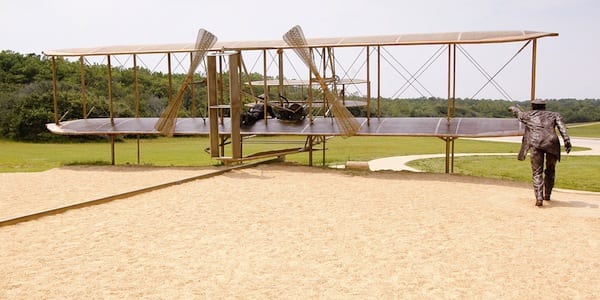
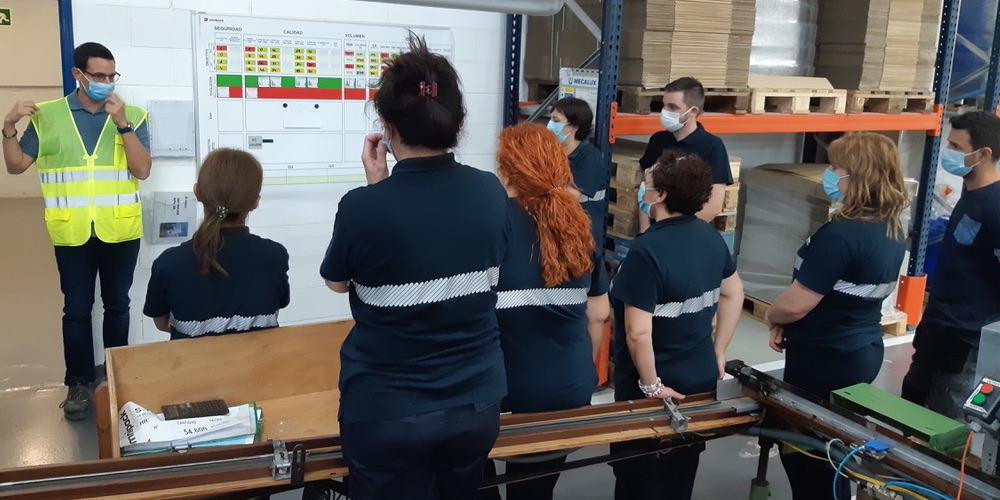
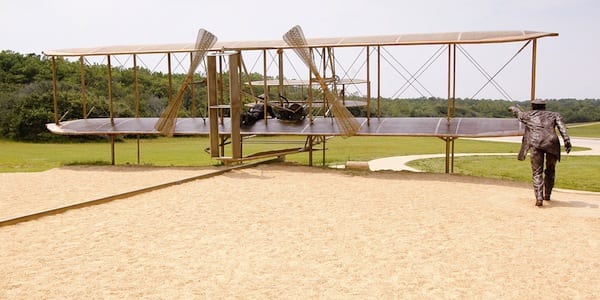
FEATURE - We talk about “changing our mindset” all the time, but do we really understand what this means in the context of our lean transformation? This two-part article tries to understand what the spirit of lean really is.
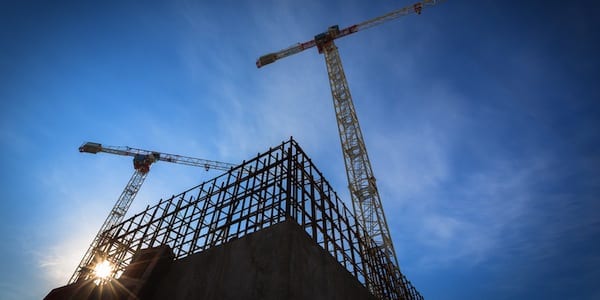
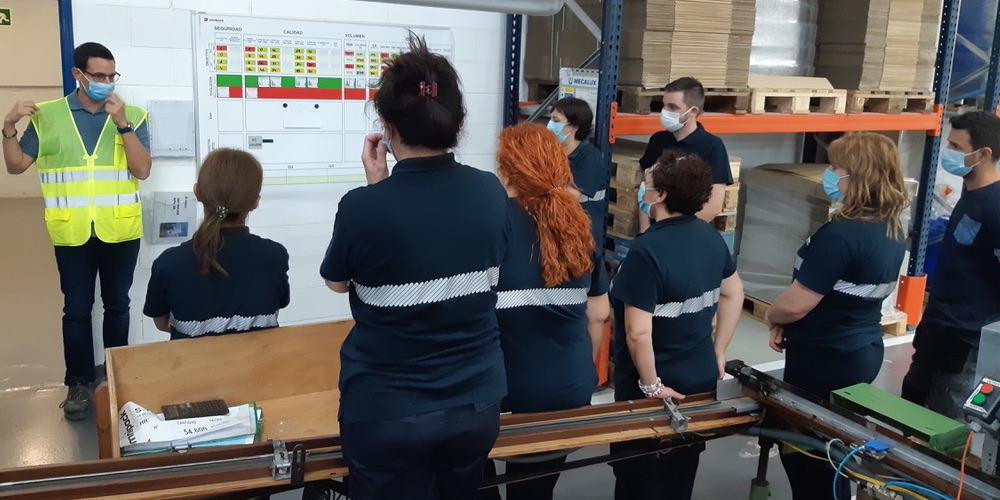
FEATURE - The author addresses the ongoing debate on rewards and recognition, explaining how an optimal relationship between team members, team leaders and group leaders will influence motivation.
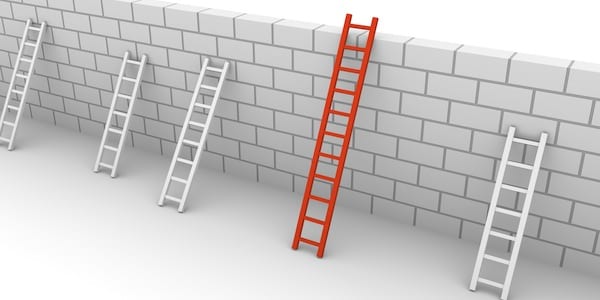
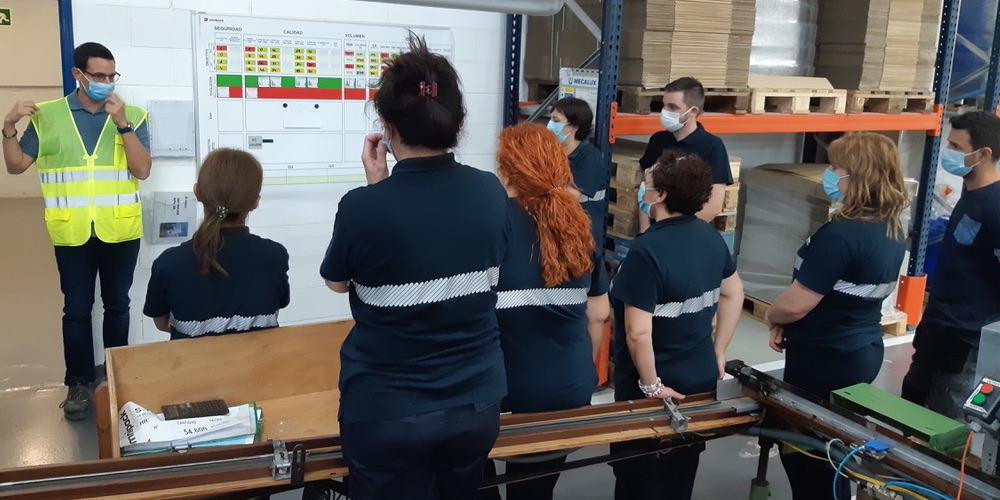
OPINION - How often have you heard the sentence, “Lean can’t work here – this isn’t Japan”? Probably more than you can remember. Here’s why national traits are simply another excuse for a failed attempt to change.
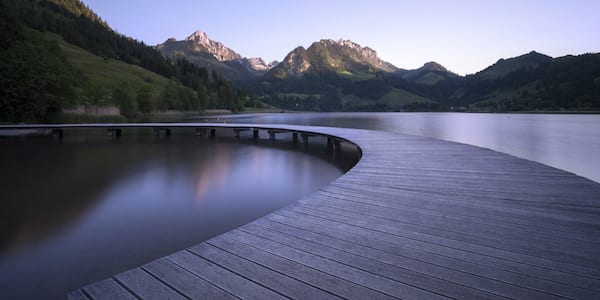
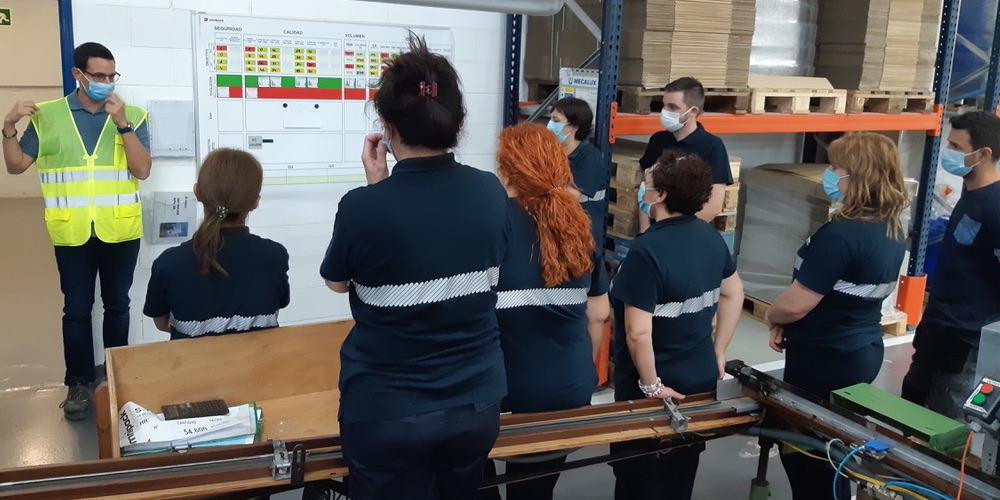
INTERVIEW - To really change, an organization must use lean management as a strategic asset rather than just a set of tools. In this interview, Art Byrne talks about rewarding people and the process of transforming companies.
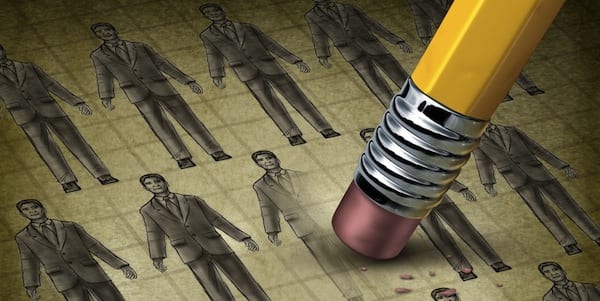
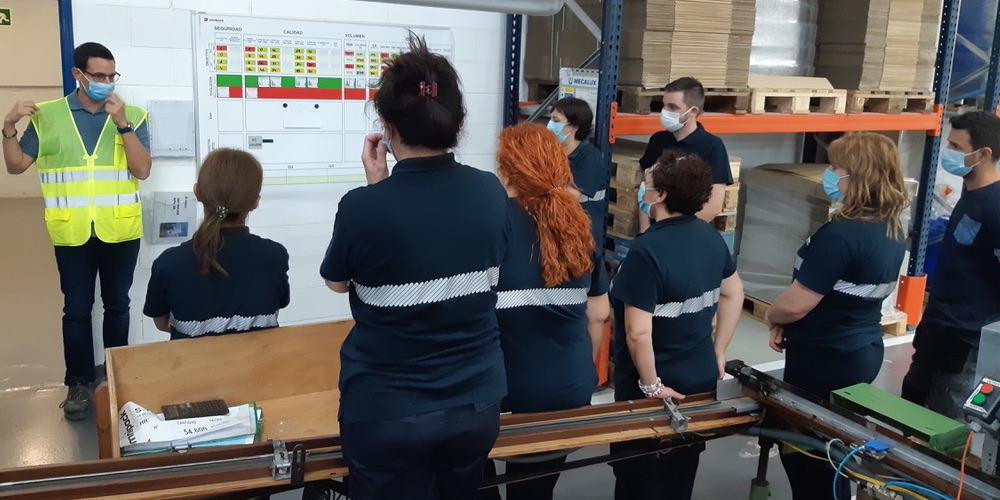
FEATURE - Can a company be considered lean if its improvement efforts result in layoffs? The author answers this frequently asked question drawing from his own experience dealing with organizations.
The idea of “lean management” can refer to both individual managerial behaviors and, more in general, the set of principles and practices characterizing the adoption of lean thinking in an organization.
In the first case, lean management is closer in meaning to the idea of “lean leadership” and entails the development of behaviors that foster continuous improvement at the front line, such as respect for people, asking questions (rather than providing answers), going to see to really understand the work and the causes of problems, and scientific problem solving. In the second instance, lean management describes the lean philosophy more in general.
In its more general meaning, lean management – or lean thinking, if you prefer – derives from the Toyota Production System and is now recognized as a superior management approach that, through continuous improvement, customer focus, teamwork and relentless people engagement, leads to great results in terms of quality, performance, delivery, and cost. The promise of lean management is to create the most value for customers using the least possible amount of resources. As an approach to running a business, it brings benefits to all parties involved, from customers to employees, suppliers to wider society.