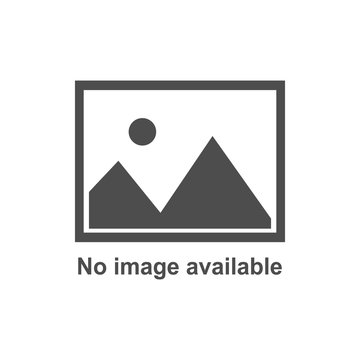
CASE STUDY – Faced with safety and quality issues, this Brazilian manufacturing plant installed a dojo, and the results are very promising.
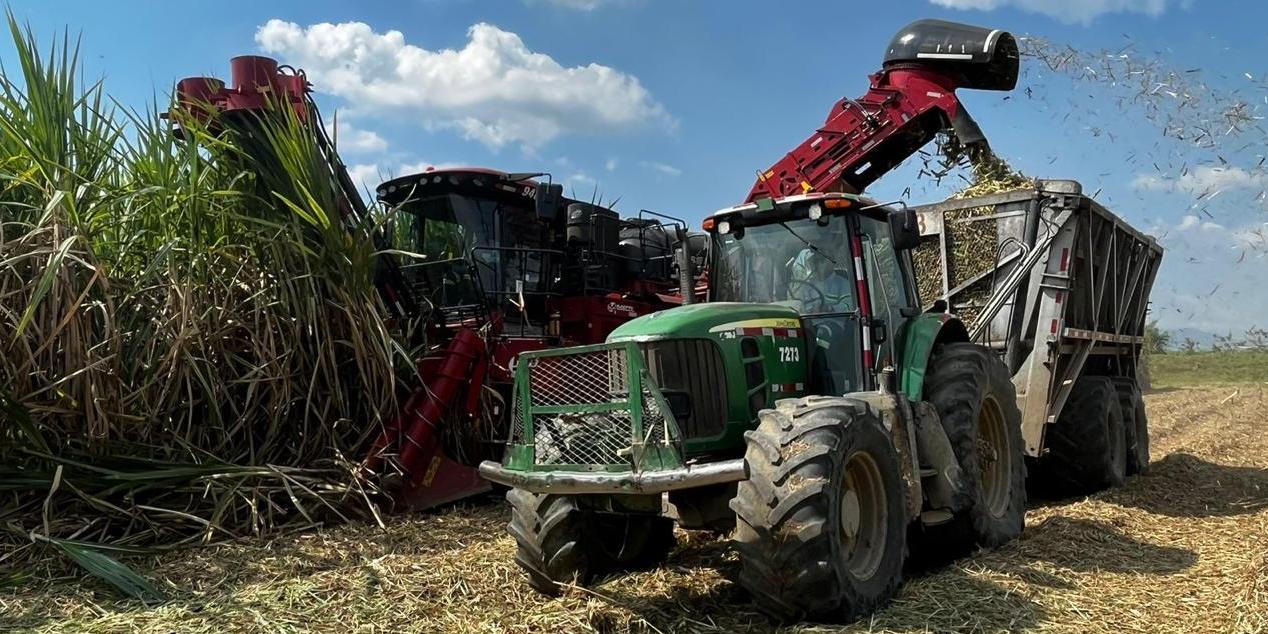
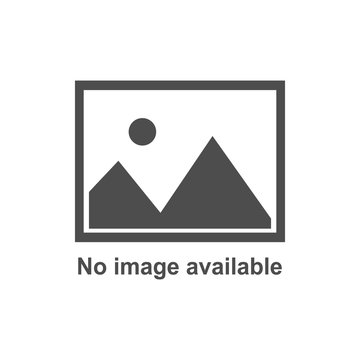
CASE STUDY – Manuelita Sugar Mill in Colombia adopted Daily Management to bolster leadership effectiveness and operational outcomes, addressing siloed thinking and communication challenges.
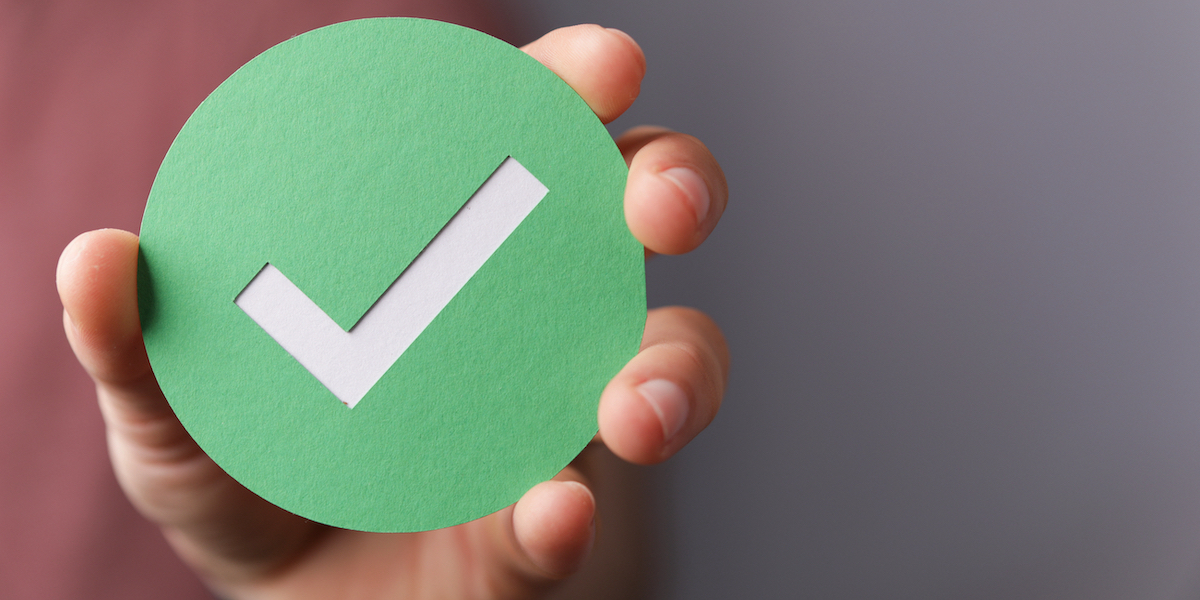
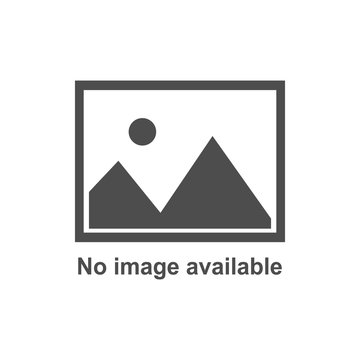
FEATURE - In this article, taken from LEI's Design Brief, Jim Morgan talks about the often-overlooked topic of building quality into new products. Learn how a customer-centric approach in development can prevent costly rework and build lasting trust.
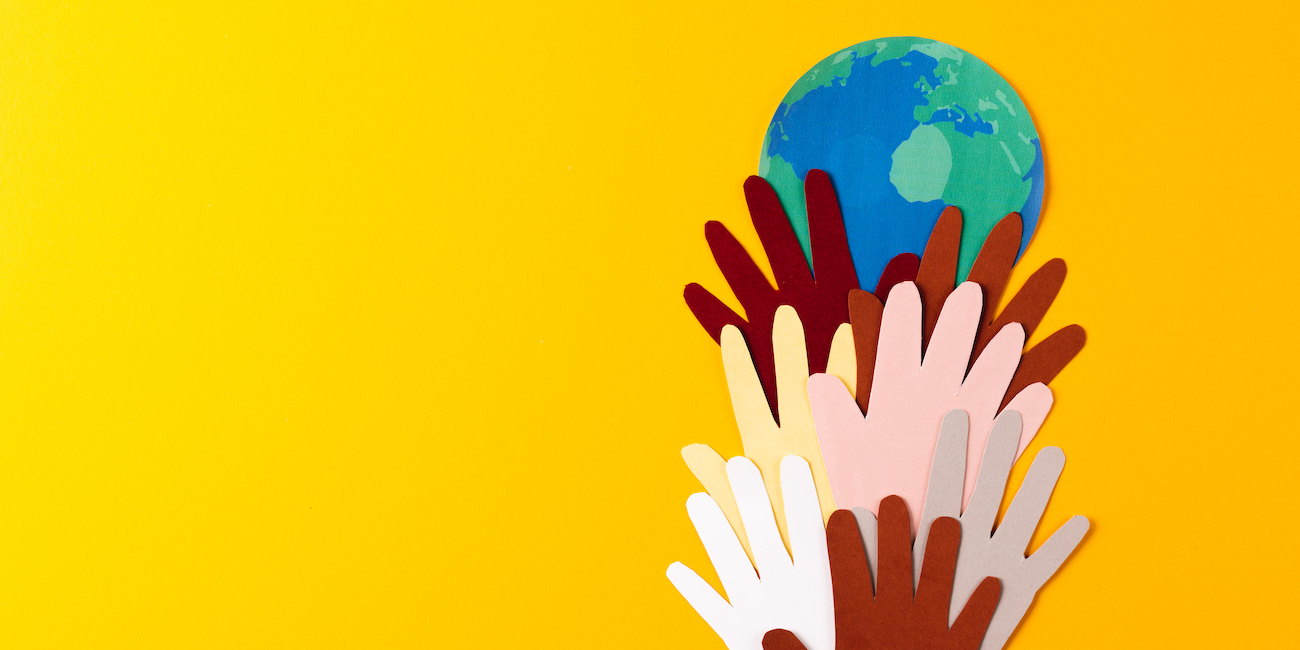
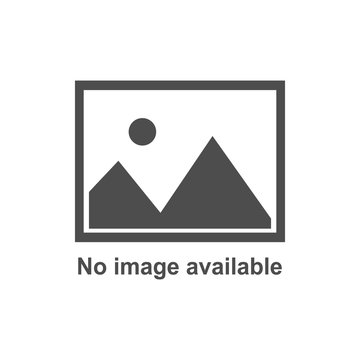
INTERVIEW - In this interview, Lynne Smith discusses the potential and difficulties of applying Lean Thinking to NGOs and looks back at the lean transformation at the Gates Foundation.
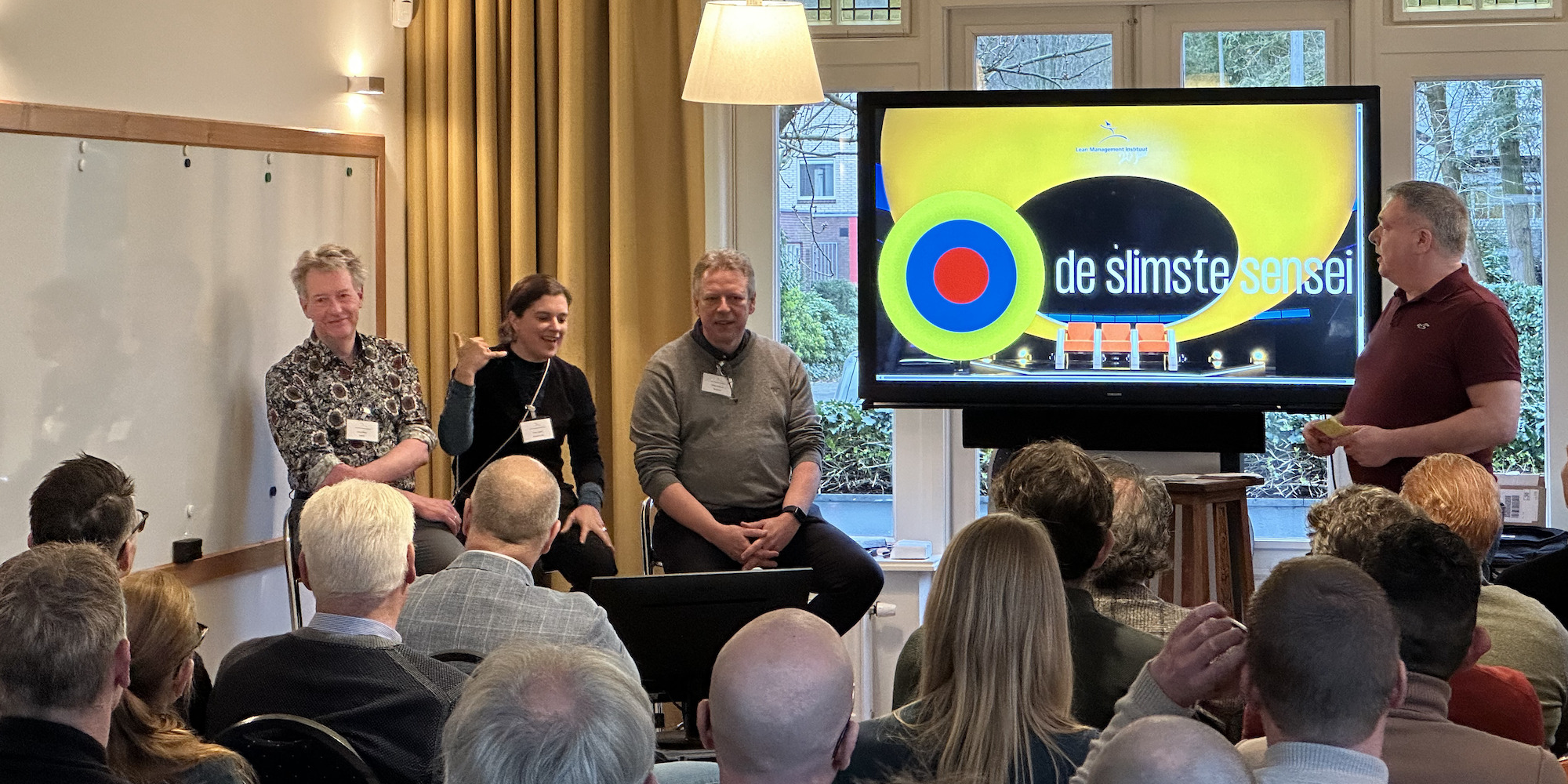
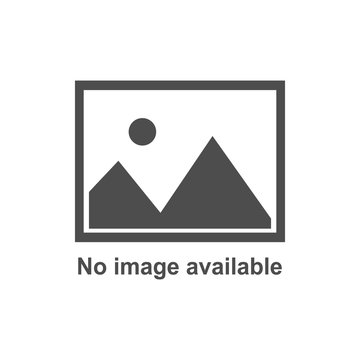
FEATURE – In February, our affiliate in the Netherlands turned 20. The President of Lean Management Instituut reflects on this achievement and looks back at these two decades.
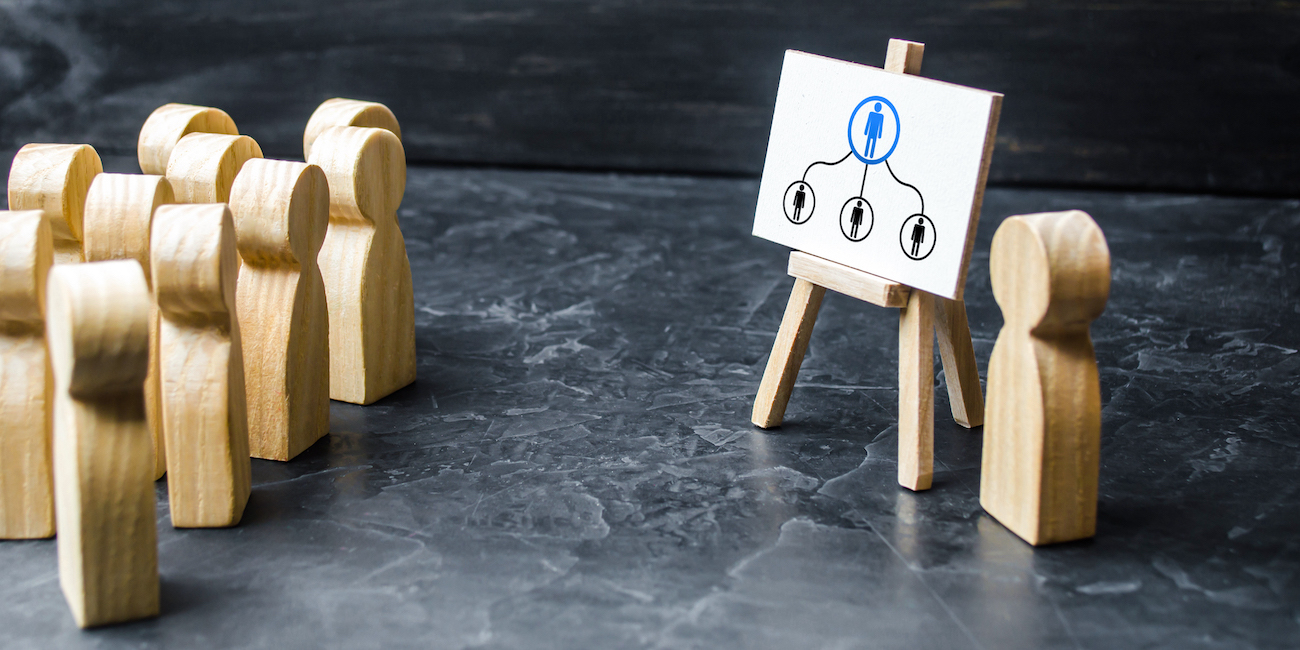
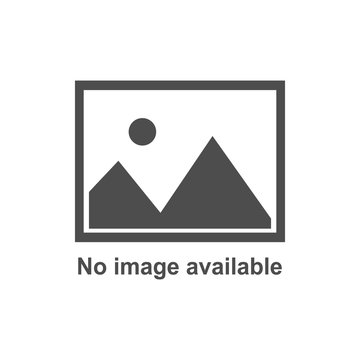
FEATURE – To get the results we want from a system, or prevent it from generating undesirable events, we need to understand how it works and behaves in the real world. That’s exactly what Jidoka does.
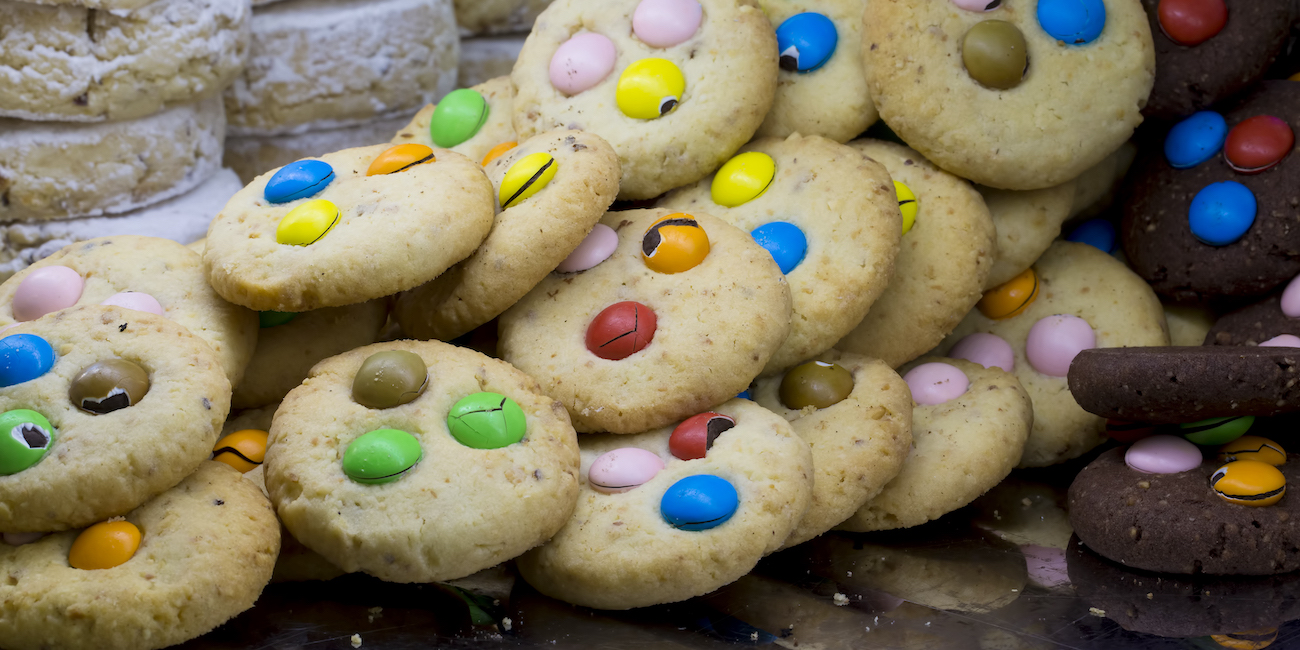
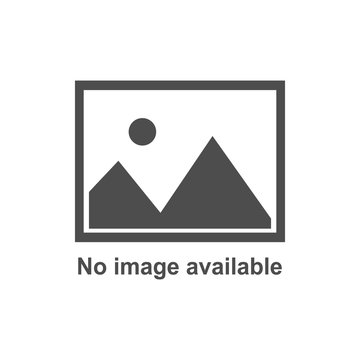
FEATURE – The successful project discussed in this article shows how Lean Thinking can bring huge benefits to small and medium enterprises and paves the way to a new way of looking at lean coaching.
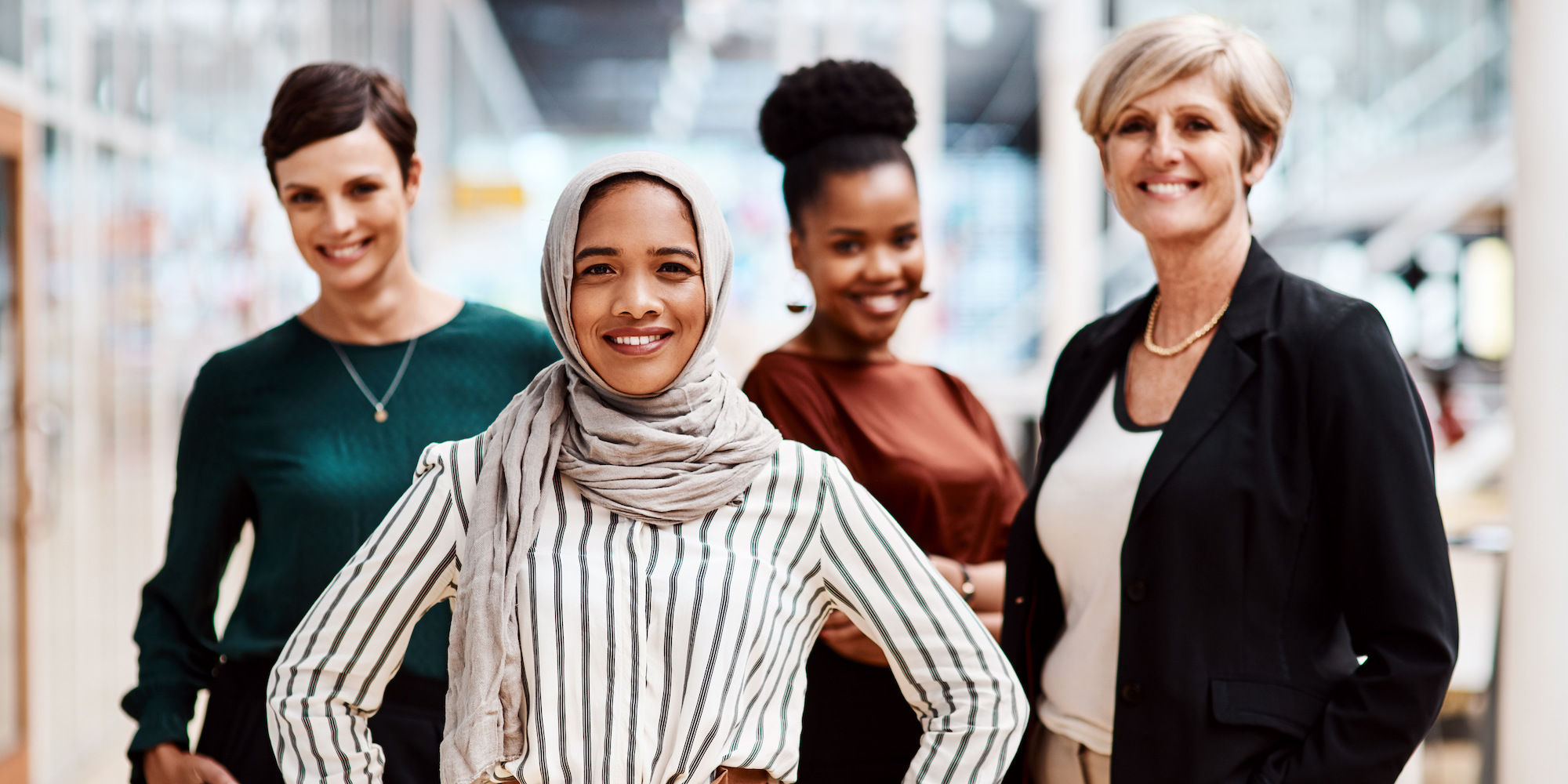
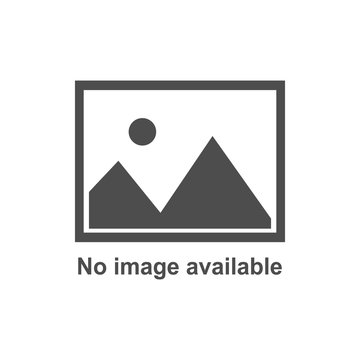
FEATURE – This article applauds the tenacity of women leaders and seeks to illustrate how they motivate others to take on the sustainability challenge through lean practices.
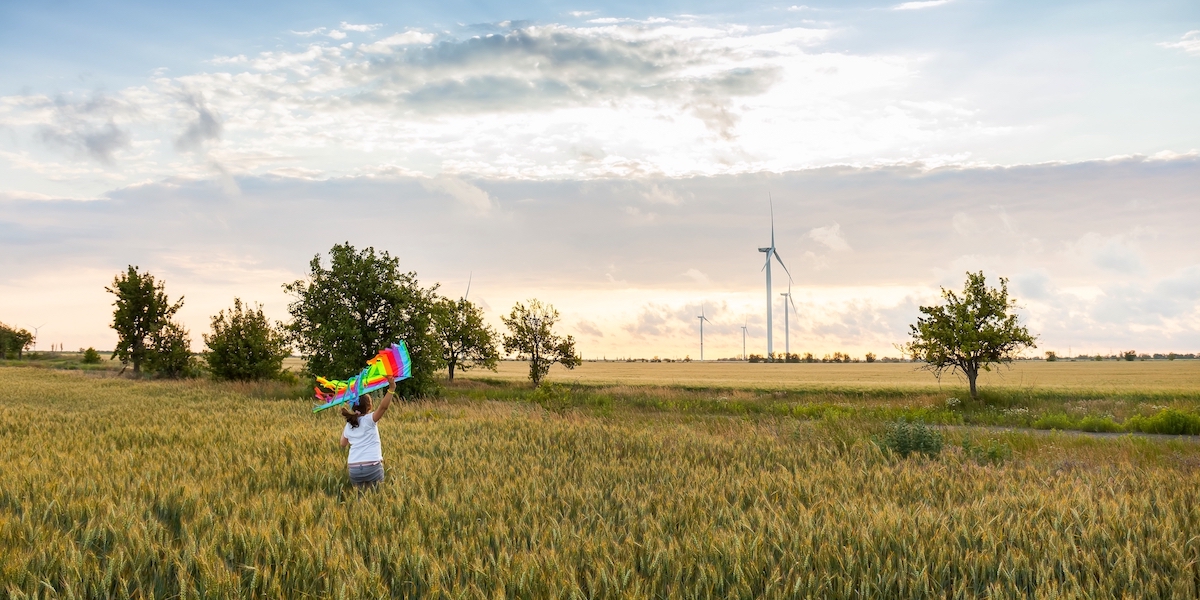
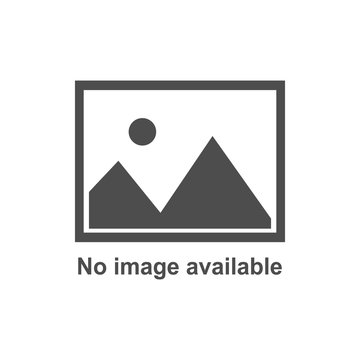
FEATURE – When it comes to the fight against climate change, we can’t expect to achieve much until we fundamentally challenge the way we think about resource consumption. Lean is our tool to do that.
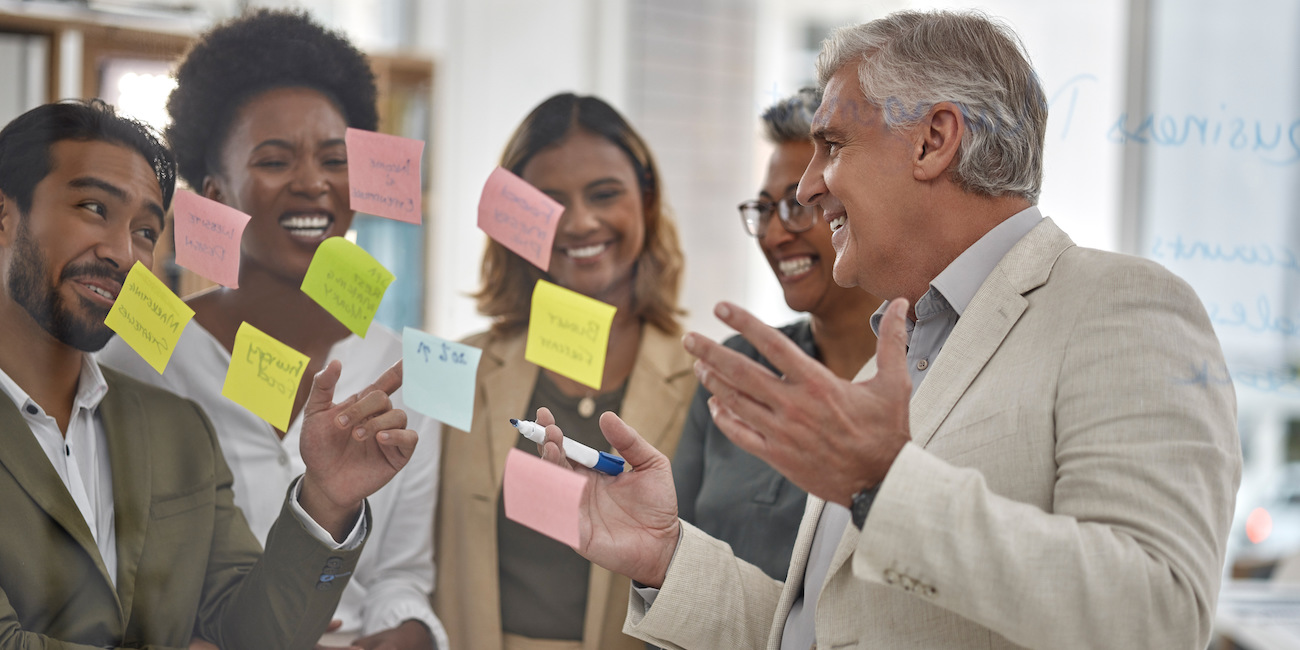
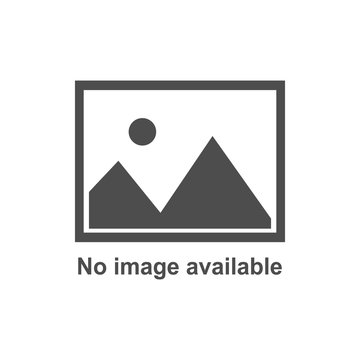
FEATURE – The author highlights the critical “power skills” leaders need to provide the right support to the transformations they lead.
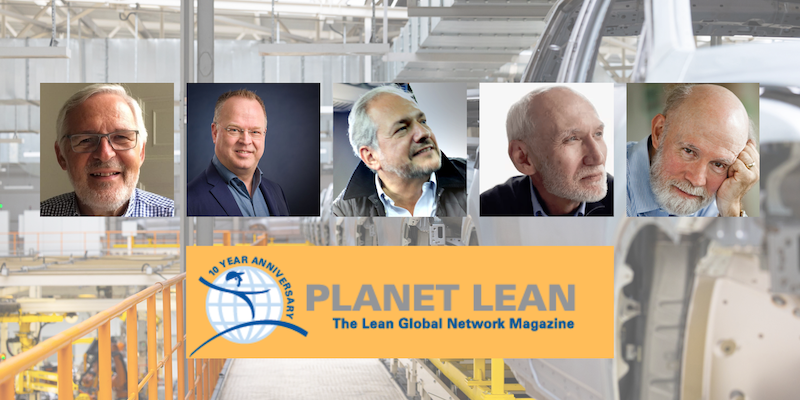
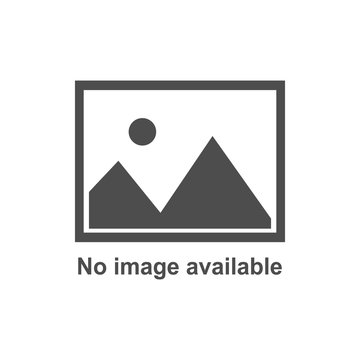
FEATURE - The editorial board members of Planet Lean reflect on the magazine's origin story and its role within and contribution to the Lean Community.
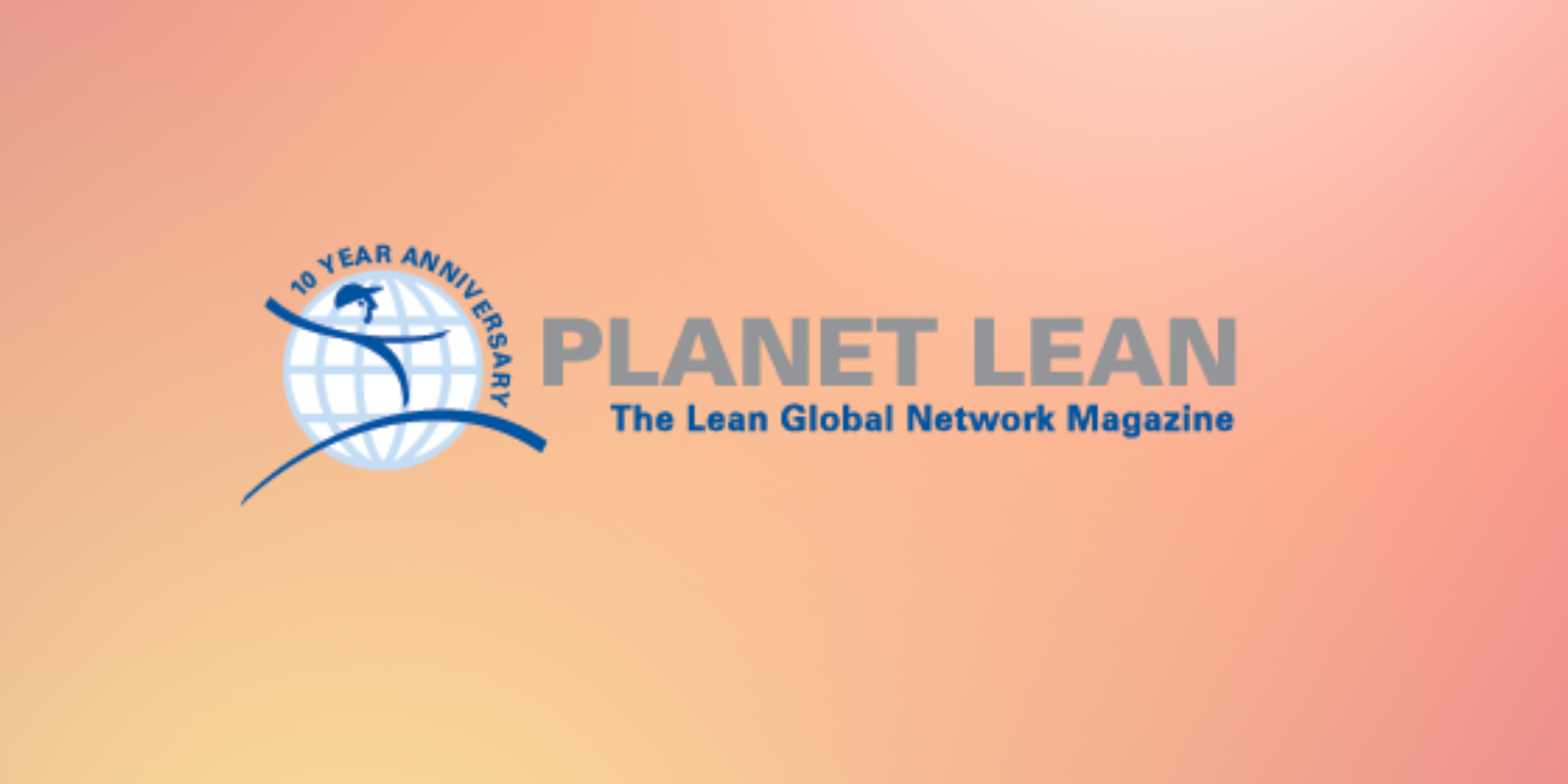
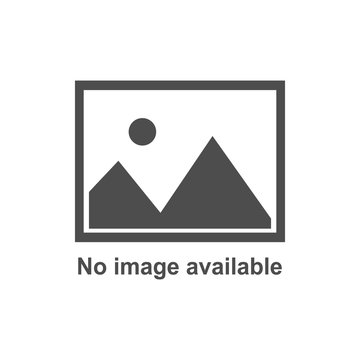
FEATURE – Ten years ago, Planet Lean was launched as a new platform for the Lean Community to share its experiences and knowledge. Our editor reflects on the magazine's mission, history and contribution of the spread of Lean Thinking.
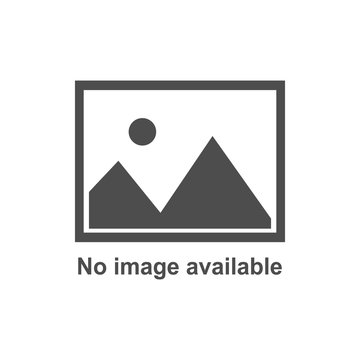
INTERVIEW – The UK Lean Summit 2024 is coming up in April. We speak to Dave Brunt to hear about the event and what we can expect from the presentations.
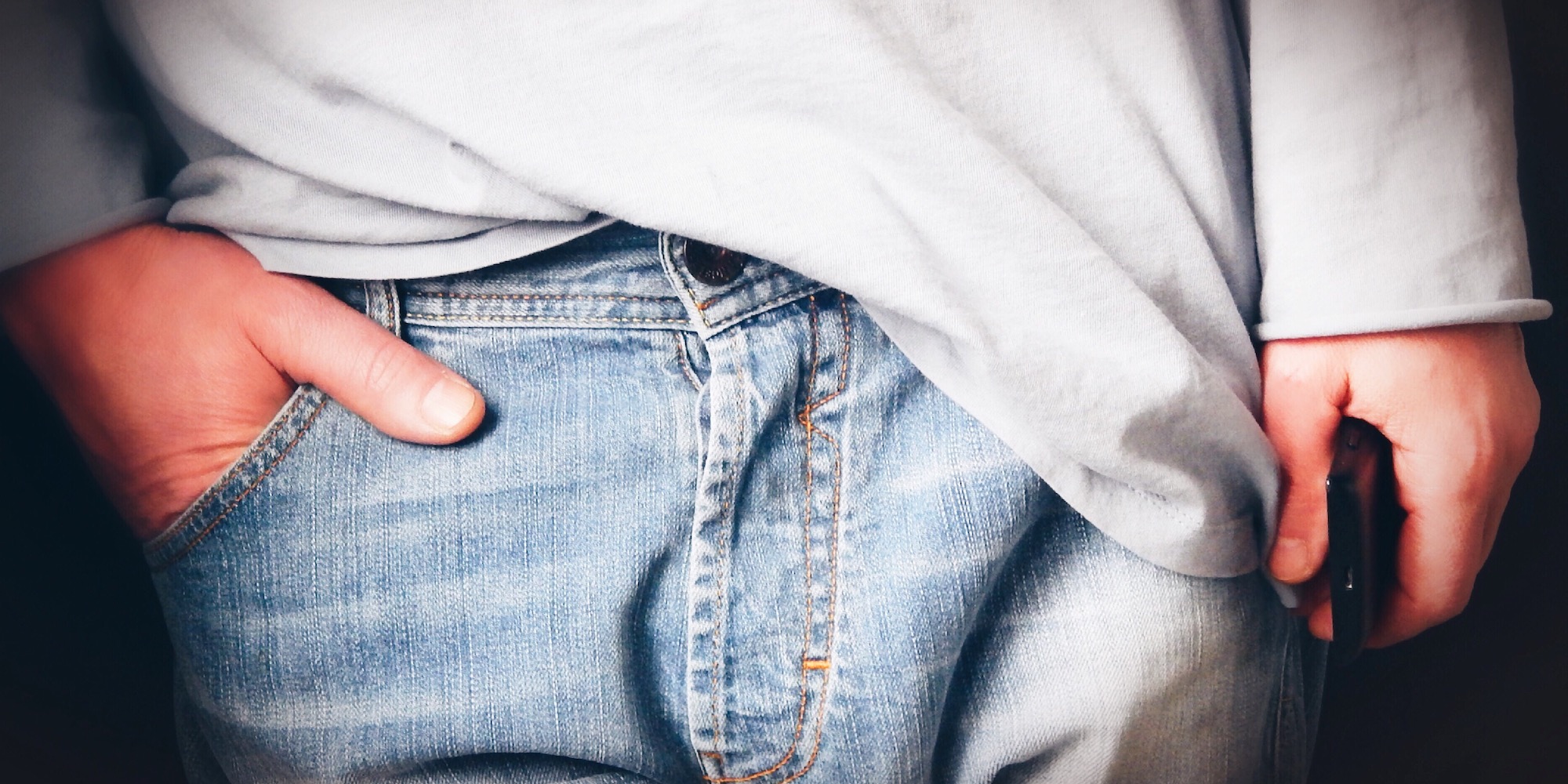
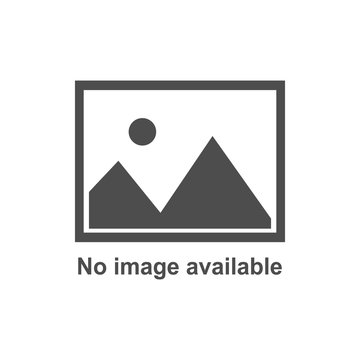
FICTION – In the second and final part of this story, the main characters discuss in front of a board. If you regularly use visual management, their conversation will resonate with you.
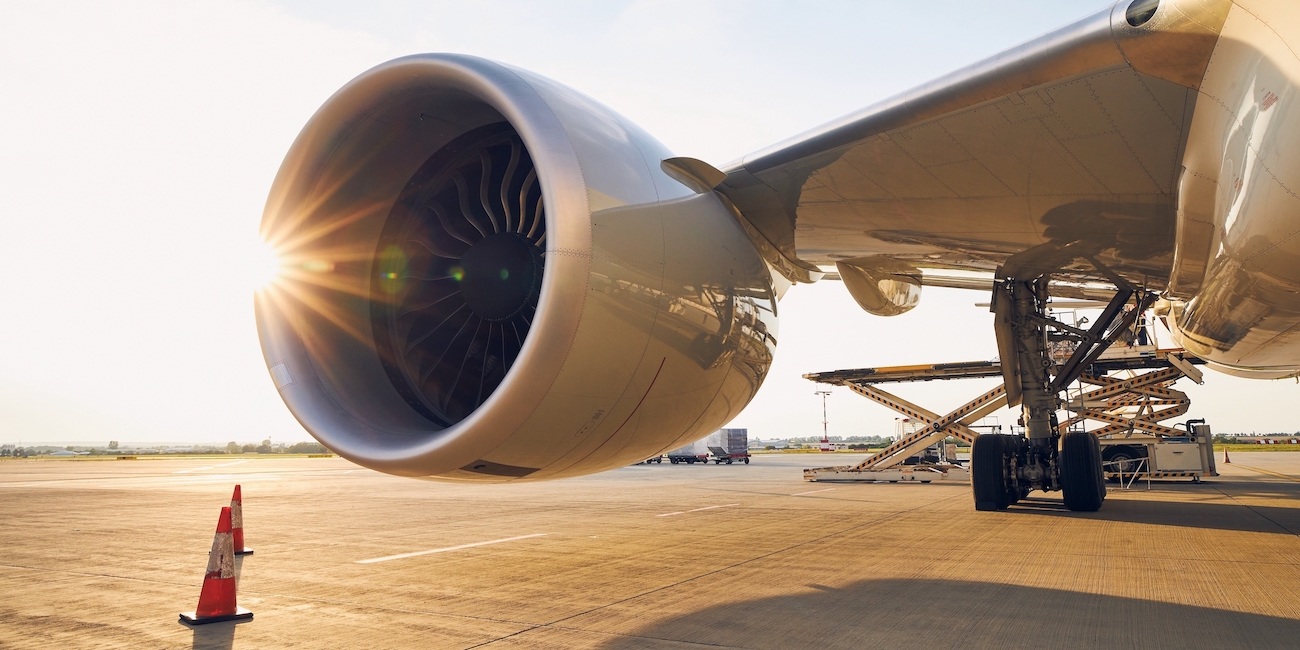
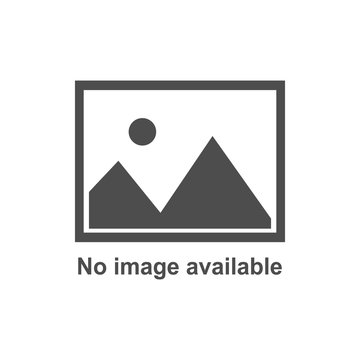
INTERVIEW – We speak with avianca’s VP of Maintenance and Engineering to learn about the efforts the airline is making to fulfil its promise to passengers.
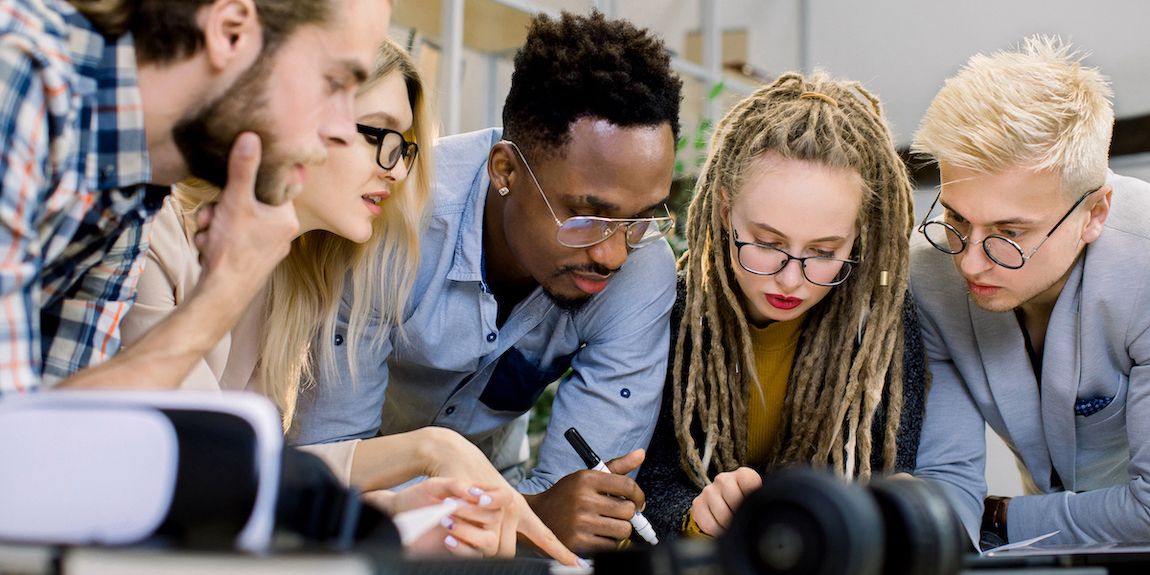
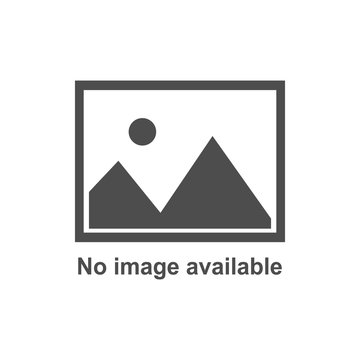
FEATURE – To develop a lean culture means to develop each lean thinker and help them reach their full potential. Here’s how Aramis Group does it.
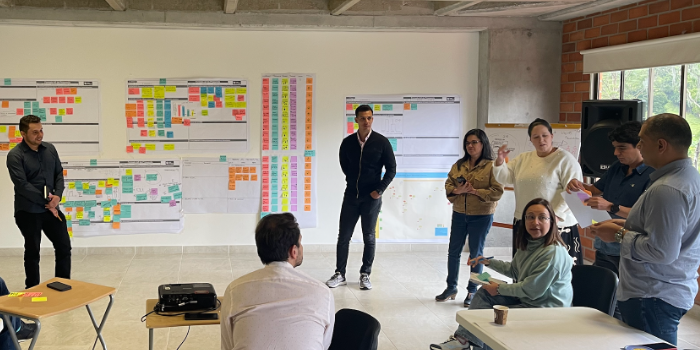
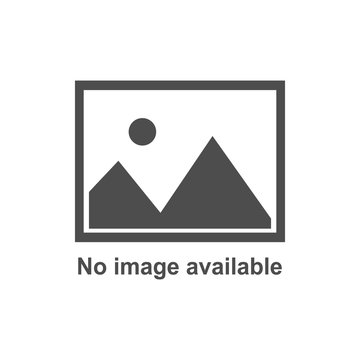
CASE STUDY – Following a positive experience in manufacturing, this Colombian company brought lean to the rest of the organization. Its goal? To become a reliable partner for its clients in the national and international markets.
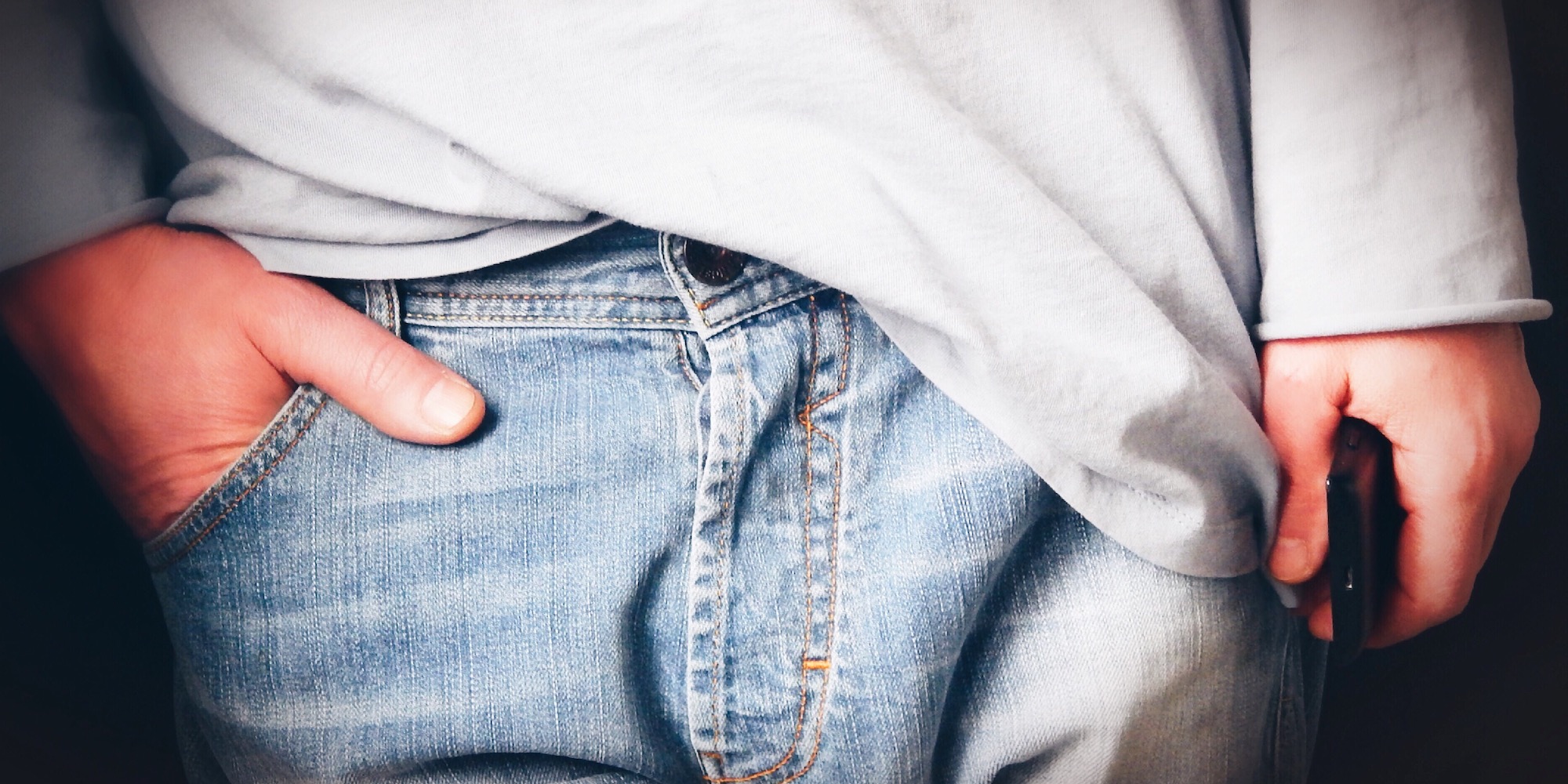
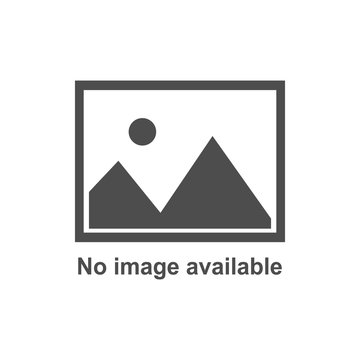
FICTION - Part 1 of this story reminds us that the role of leaders in an organization is to set the example for others, behaving the way they want the rest of the company to behave.
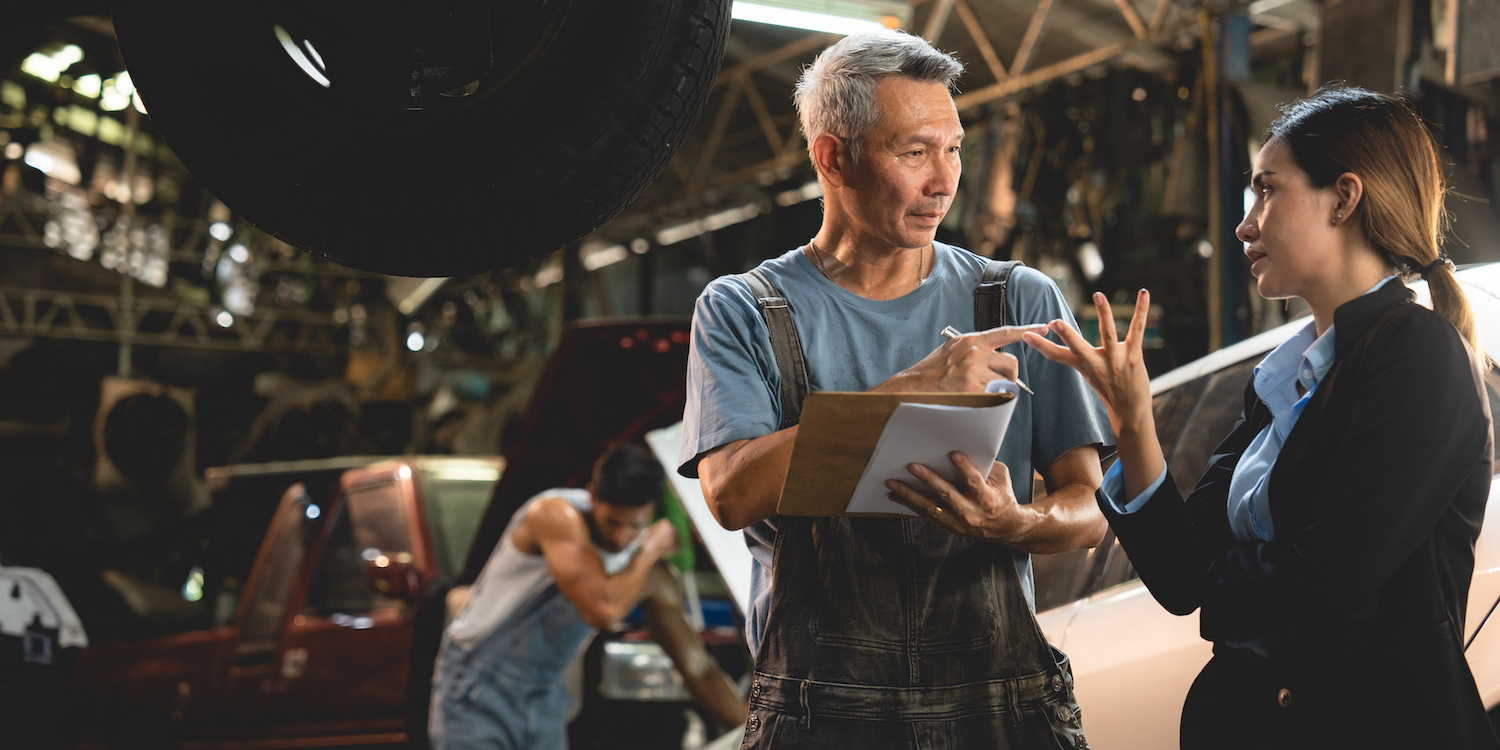
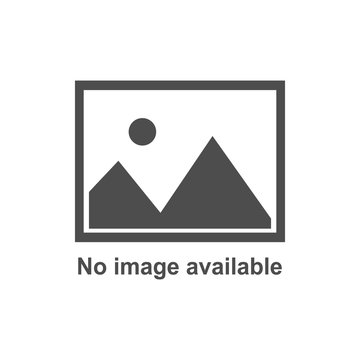
FEATURE – Nobody understands humans as well as humans do, and Jidoka is the key to learning about your customers and create ever-better products and services.
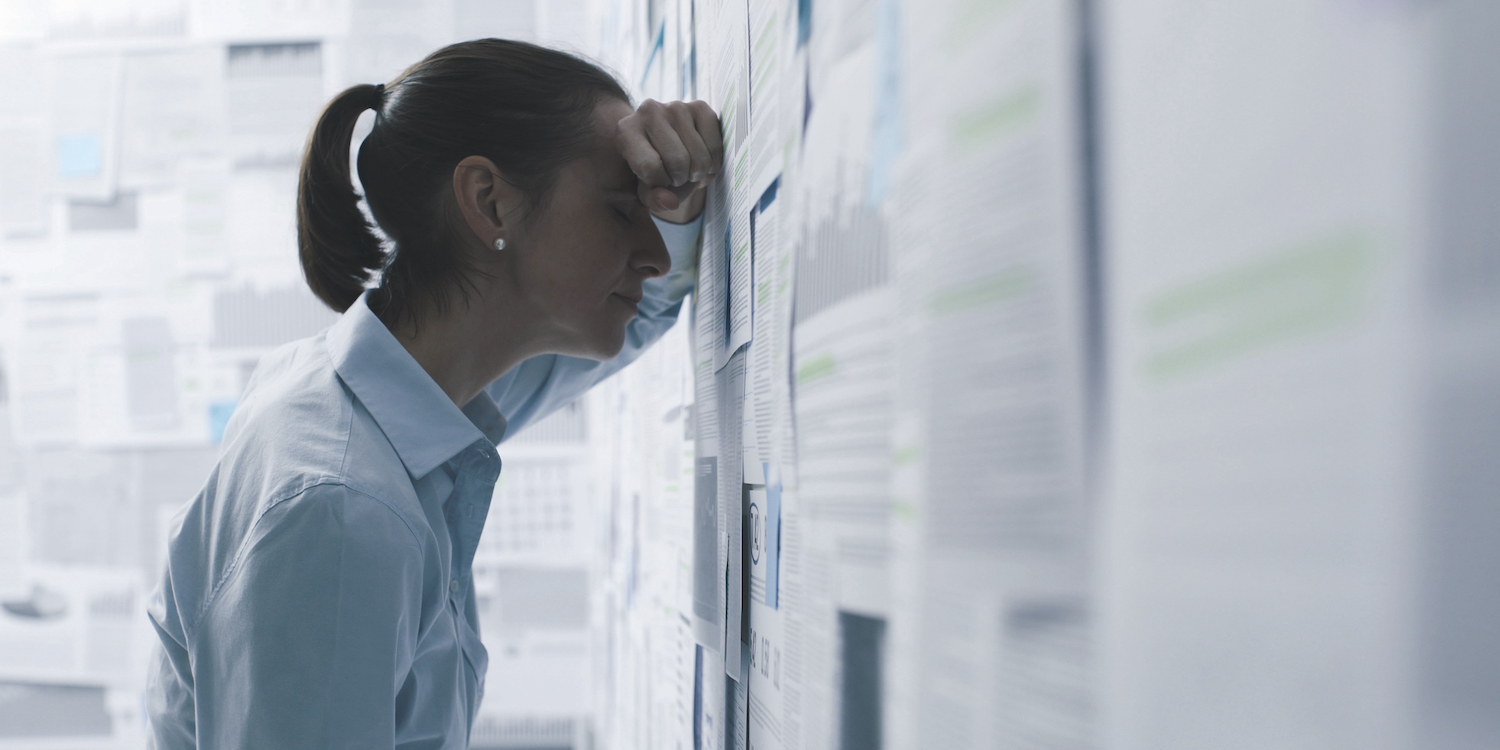
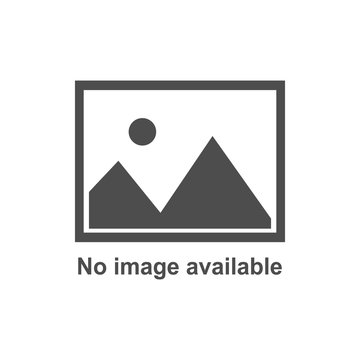
FEATURE – In this article, you’ll understand how potential errors can become an endless source of personal and managerial growth.
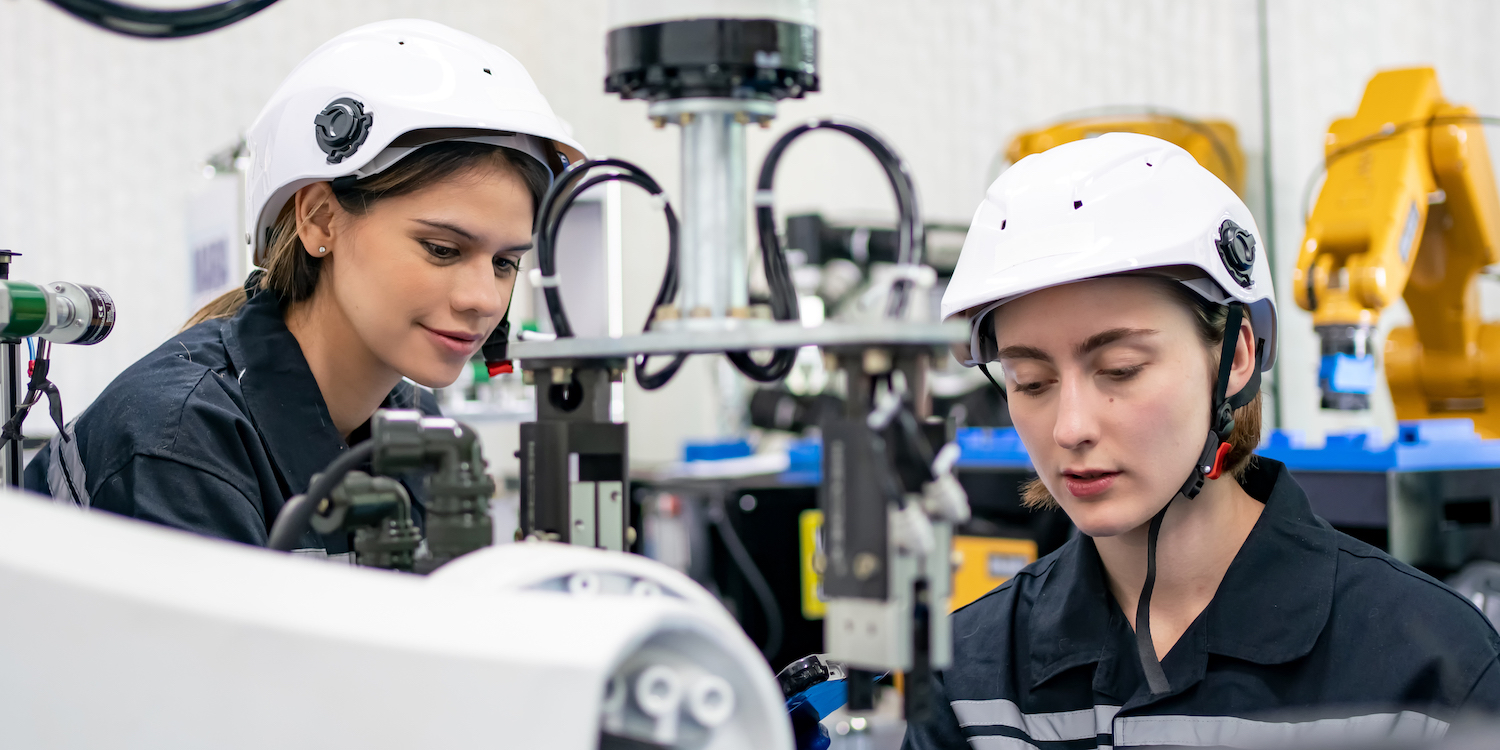
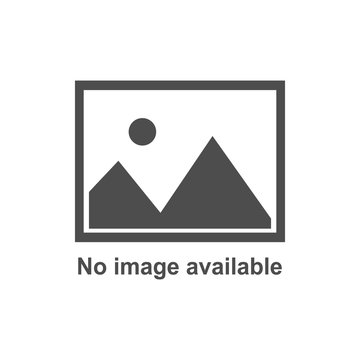
FEATURE – By adopting a product takt time perspective, we can better align engineering decisions with market demands, leading to better design, manufacturing, and material choices.
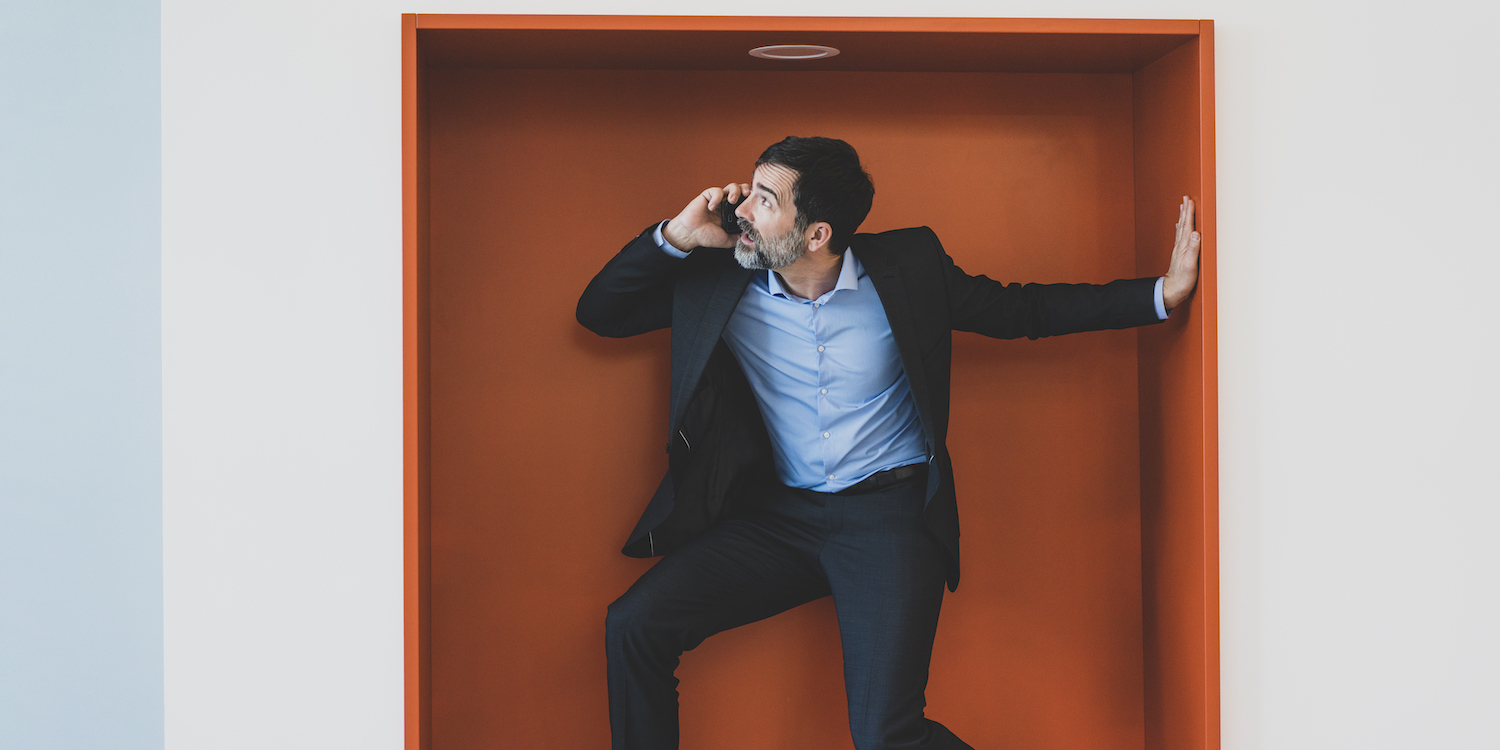
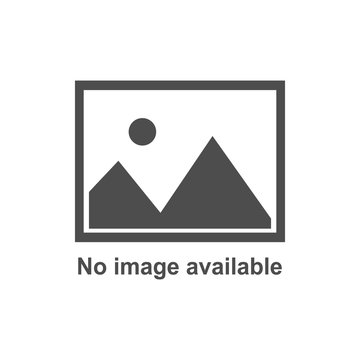
FEATURE – How does the improvement department of a company become a hindrance to the transformation? The author answers this question and discusses how this can be avoided.
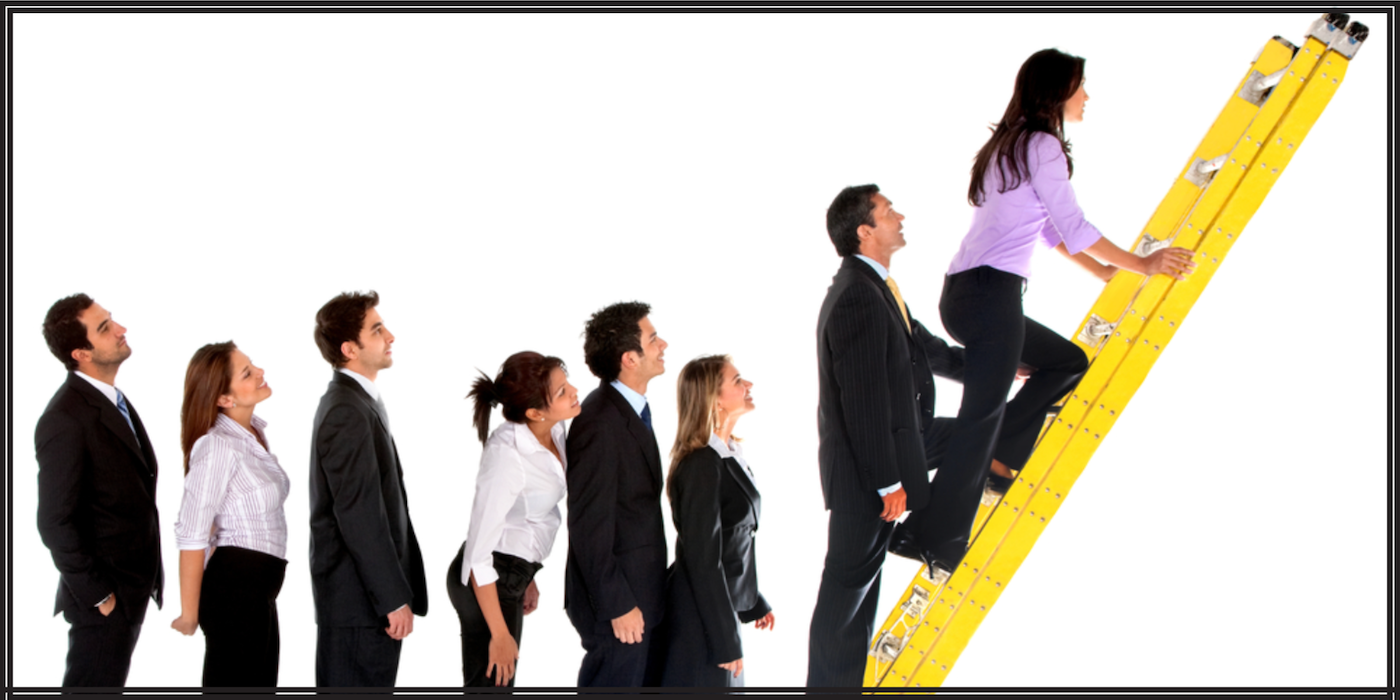
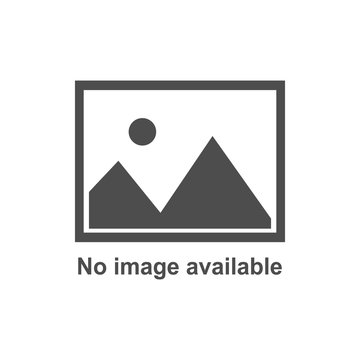
FEATURE – If you think one is born a leader, think again. Leadership can be learned and, in this article, the author provides a four-step guide to developing it.

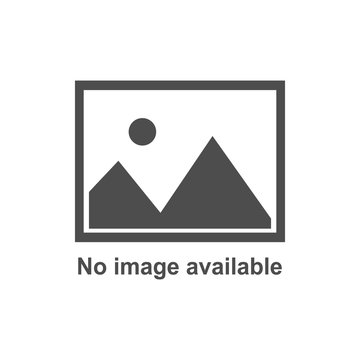
CASE STUDY – The story of Norwegian furniture manufacturer Haugstad Møbel that, thanks to Lean Thinking, was able to transform its culture and unlock the potential of sustainable growth.
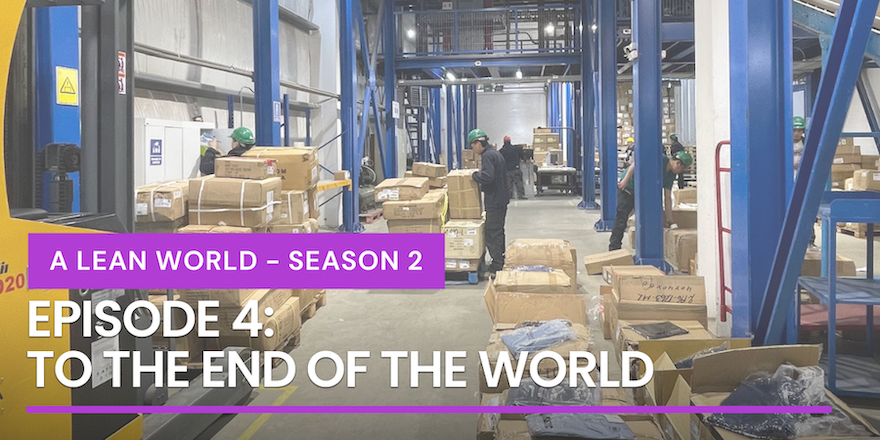
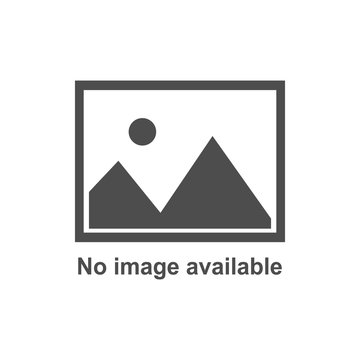
WEB SERIES - In the last episode of our It's a Lean World series, we travel to the tip of South America to visit the southernmost Distribution Center in the world and learn about its lean work.
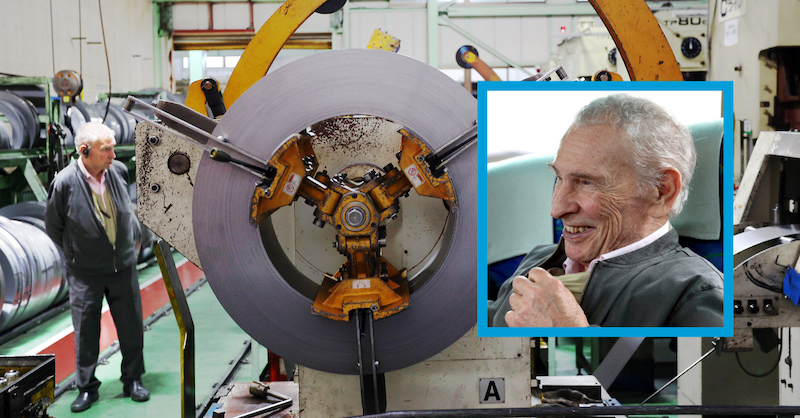
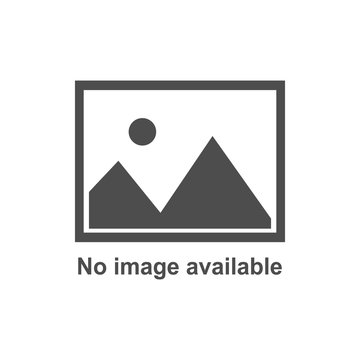
FEATURE – On October 31st, the Lean Movement lost one of his pioneers. In this piece, Dan Jones reflects on Freddy Ballé’s legacy.
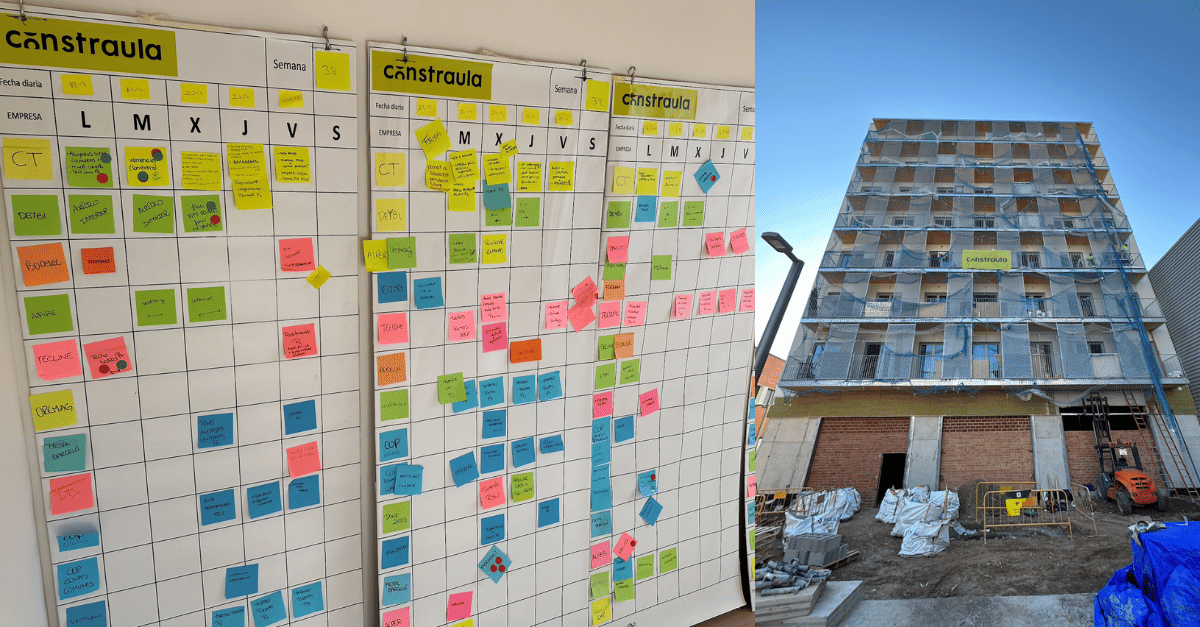
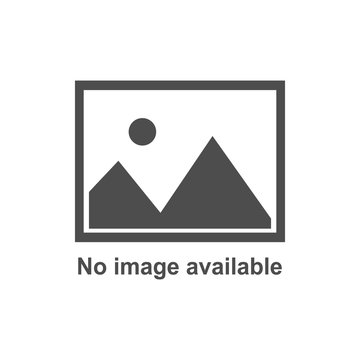
CASE STUDY – Thanks to Lean Thinking, this Spanish construction company was able to deliver a challenging project in one year, well ahead of schedule. Here’s how they did it.
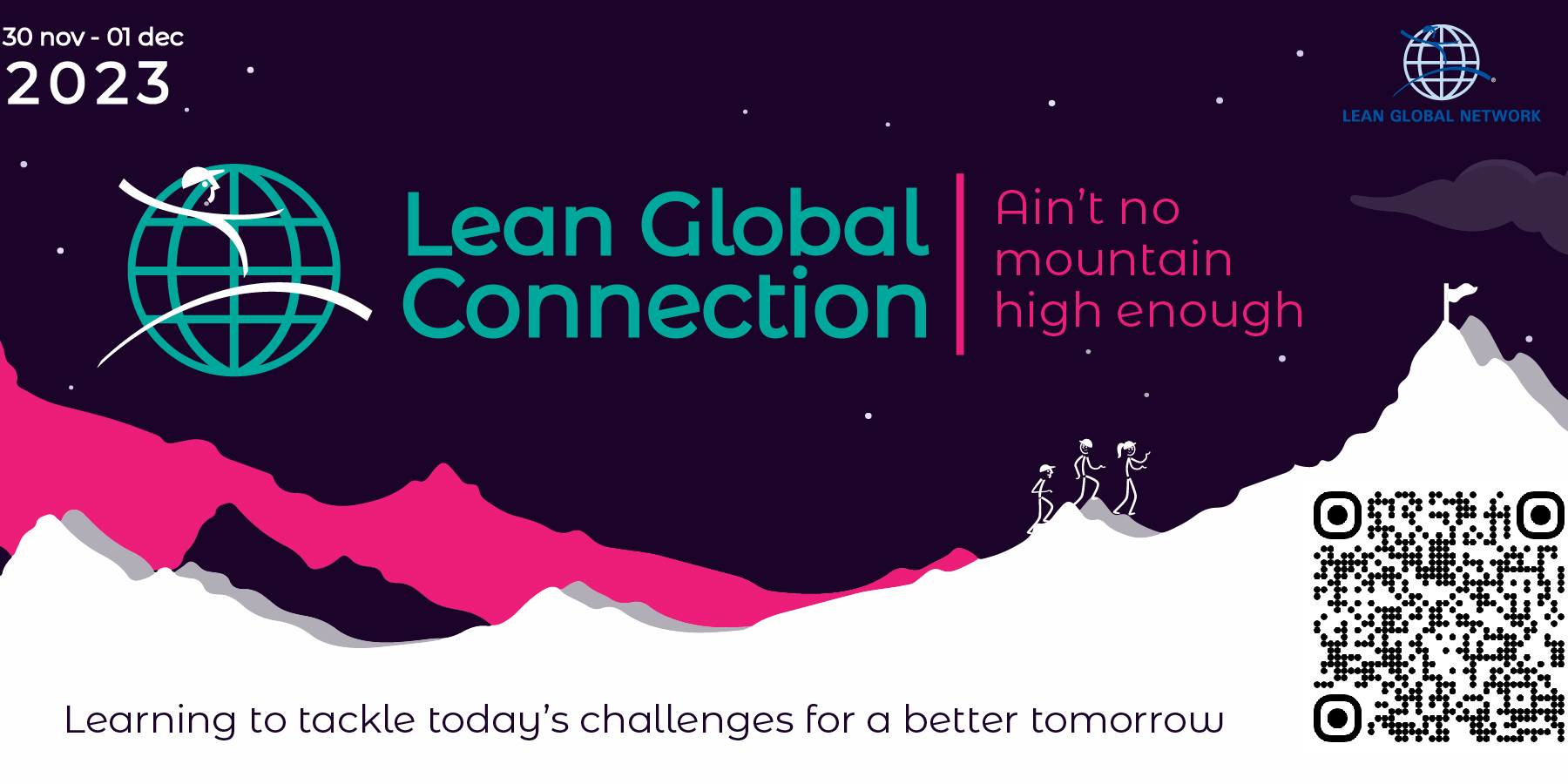
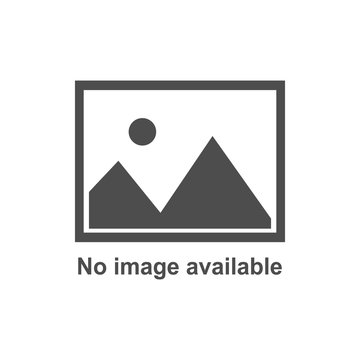
EVENT - The Lean Global Connection is around the corner! Our editor takes you through some of the key highlights you can expect and reminds us of the idea behind the largest online lean event in the world.
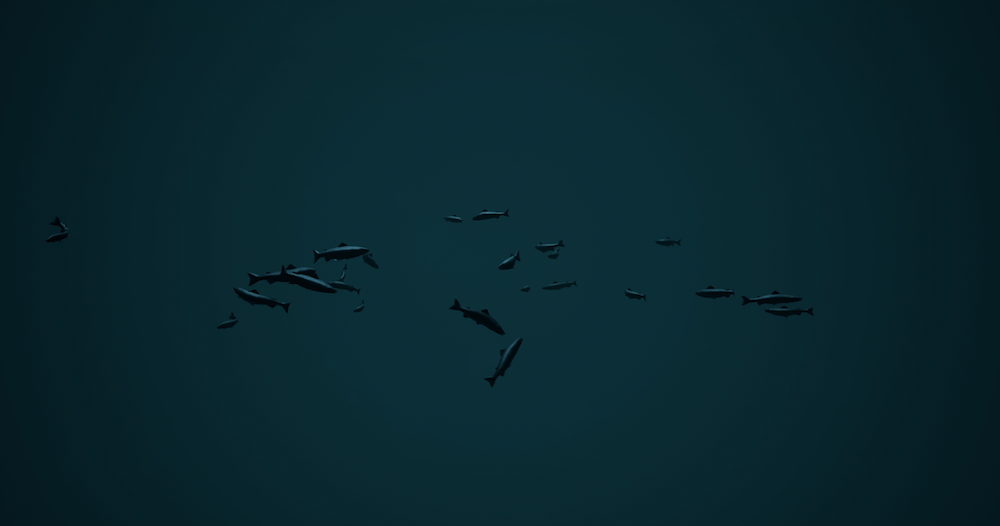
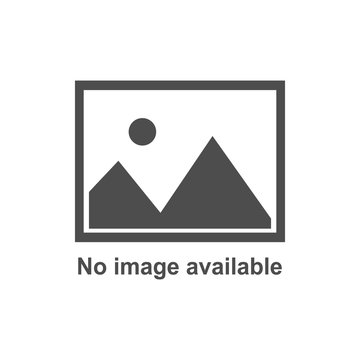
WEB SERIES - In this episode, we head to Chilean Patagonia to visit a manufacturer of fish feed that turned to Lean Thinking to improve yield and eliminate inventory gaps and stock-outs.
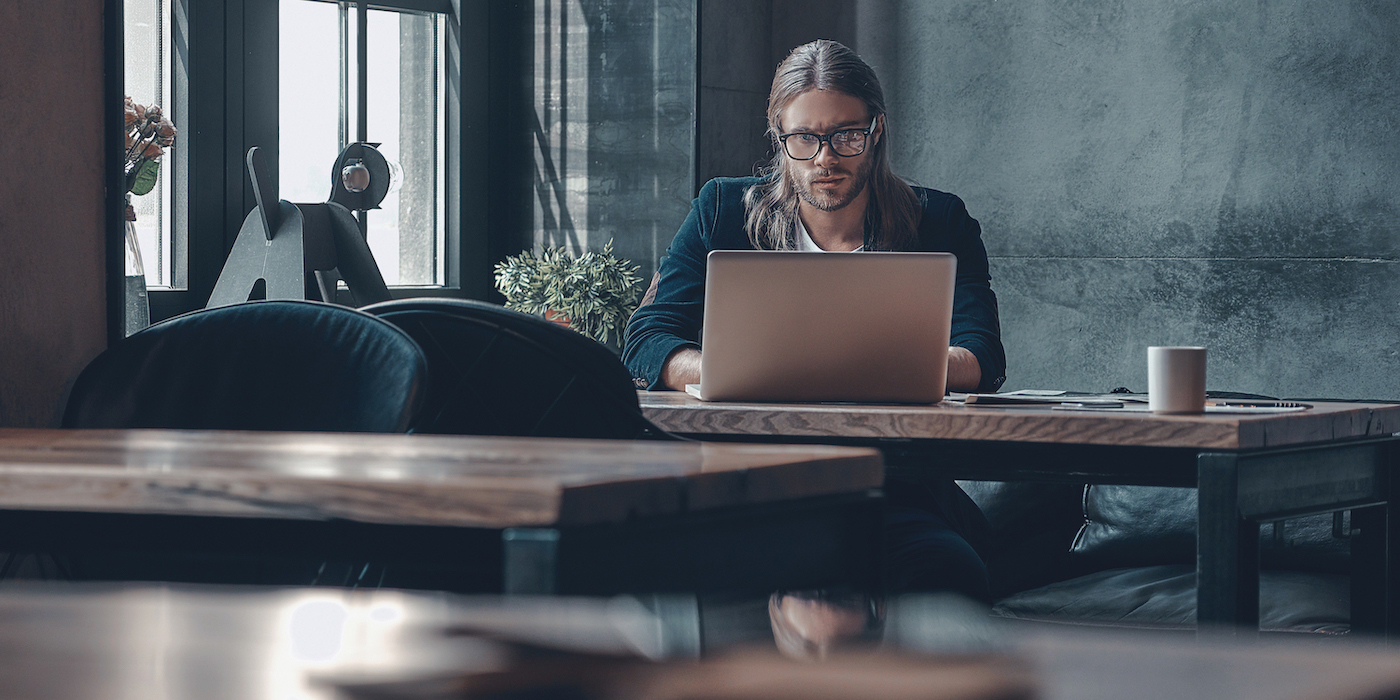
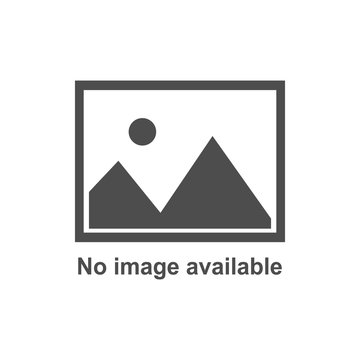
FEATURE – The author explores methods to expand your flow “sweet spots”, enhance focus, and achieve a state of effortless productivity.
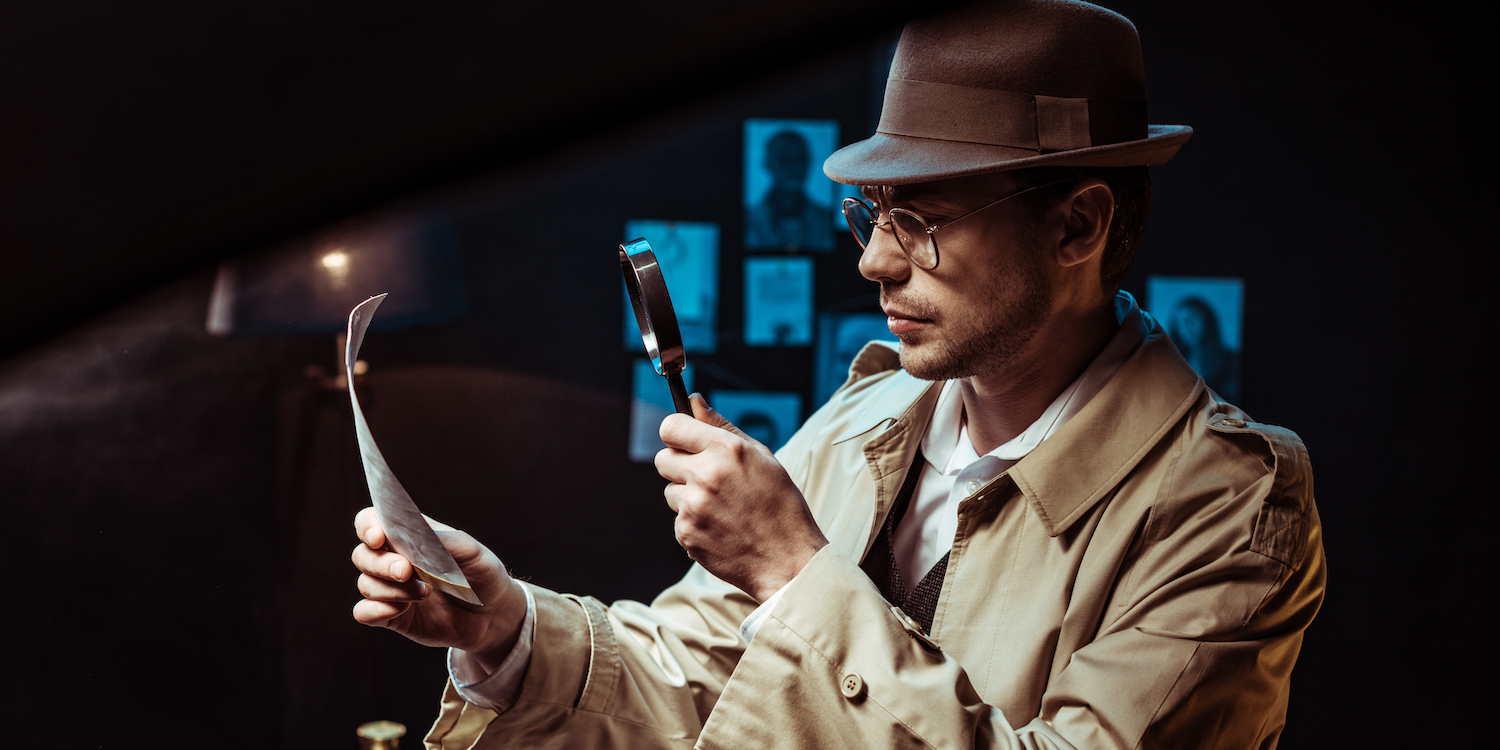
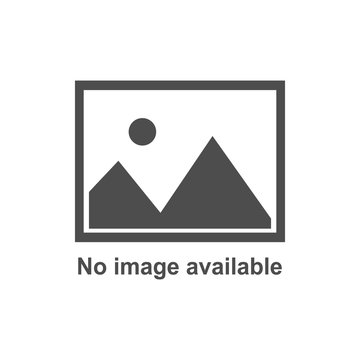
FEATURE – This insightful piece explores the true meaning of problem solving, looking at the common mistakes leaders make when they adopt some of its key practices.
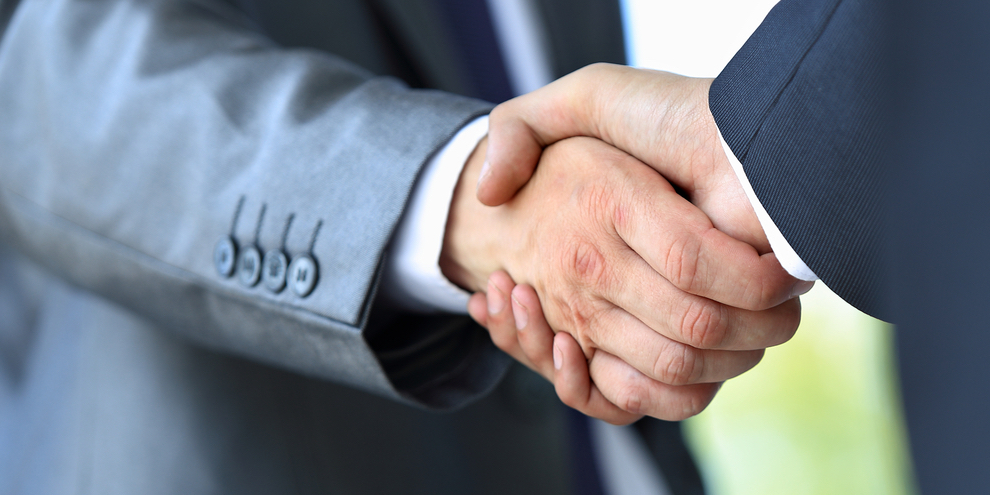
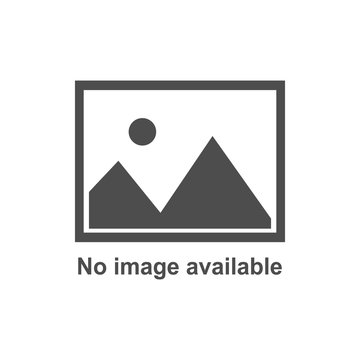
FEATURE – We are used to approaching strategic thinking as if our organization was in a position of stability and dominance. What if we started to look at it as creating better deals with all parties involved?
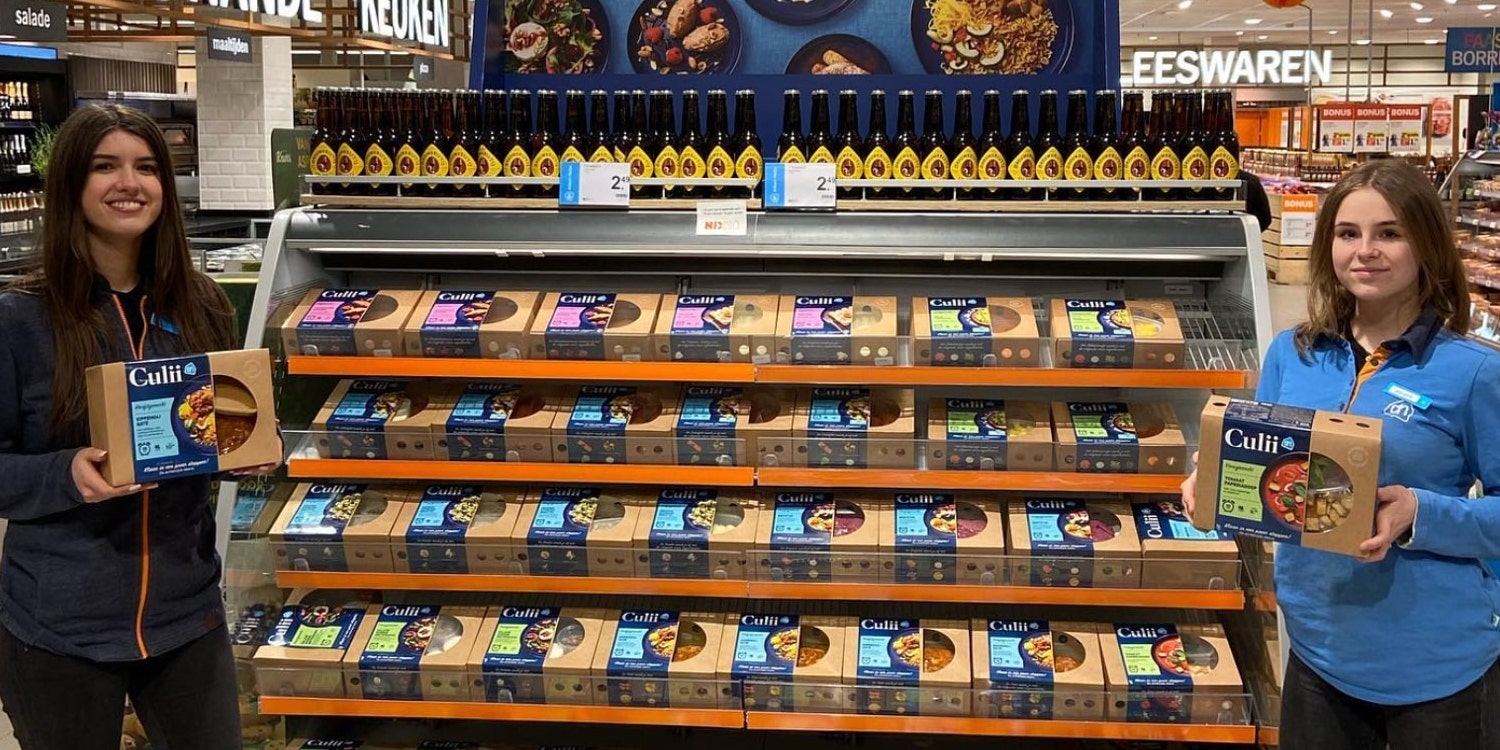
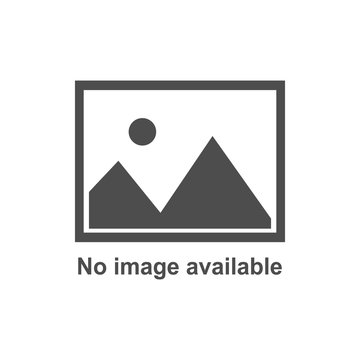
CASE STUDY – When it had to develop a production process for a new product from scratch, this Dutch company leveraged lean tools and practices. And the results were impressive.
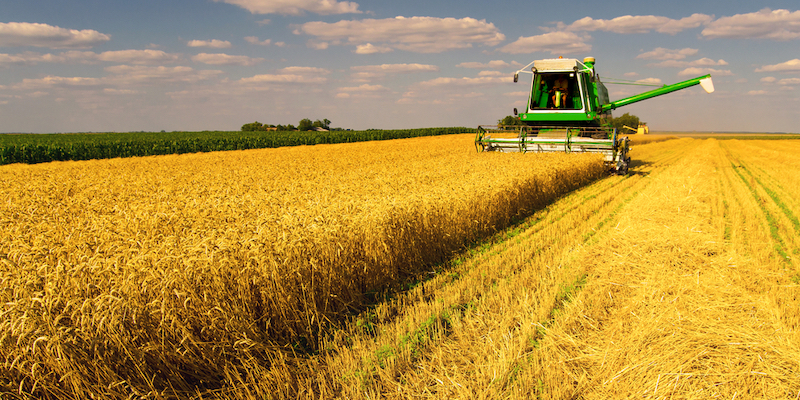
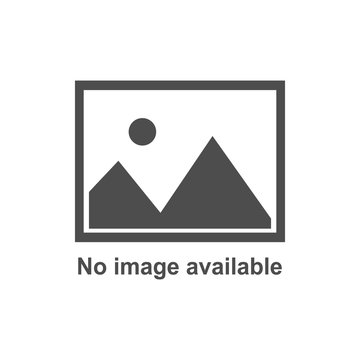
FEATURE – Waste in the agricultural sector is a significant threat not only to the environment, the economy and farmers, but also to food security around the world.
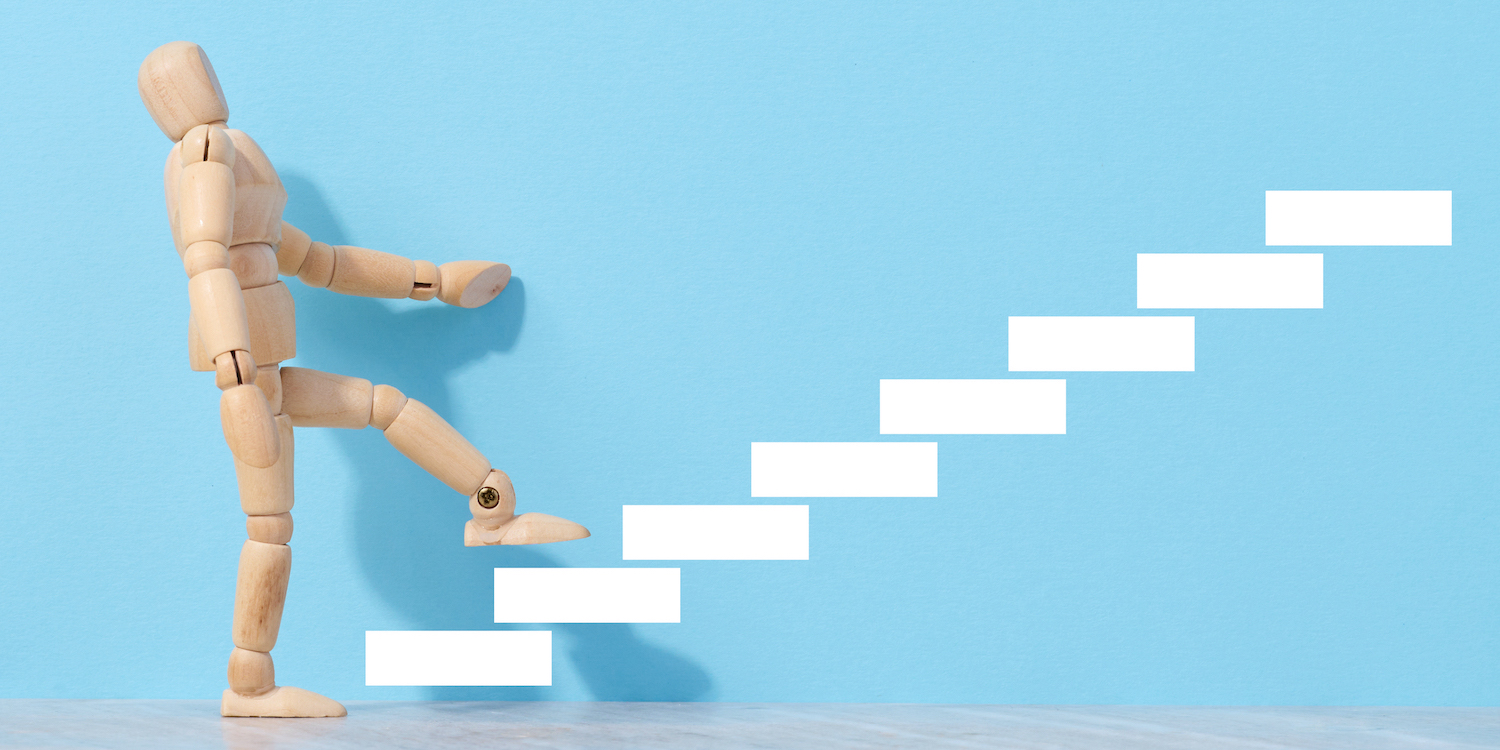
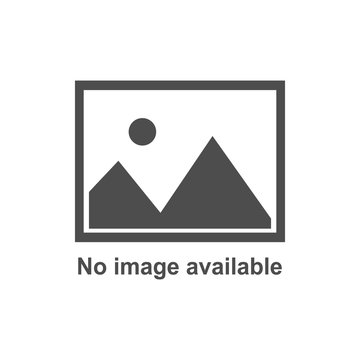
INTERVIEW – We are used to thinking of A3s mainly as a tool for problem solving. In this Q&A, you will learn about the experience of a San Francisco hospital using it for personal development.
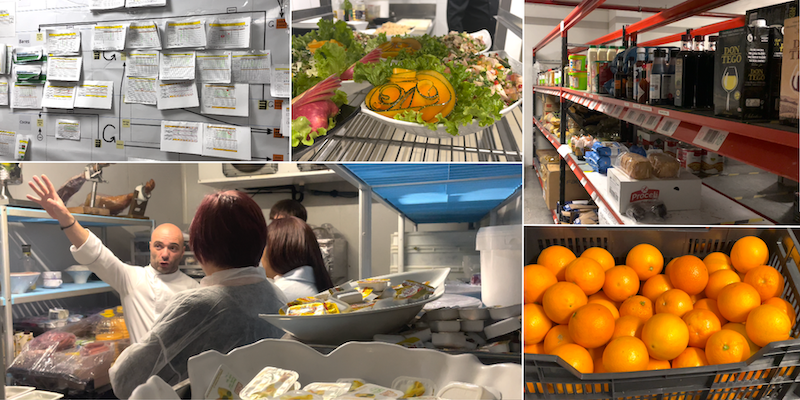
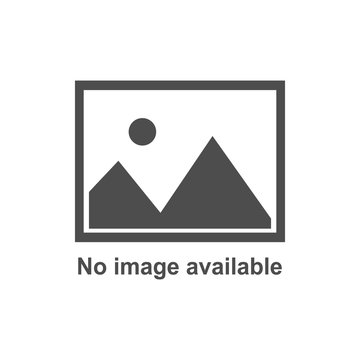
INTERVIEW - The Food&Beverage department of the Gran Tacande Hotel in Tenerife has been using a powerful visual management tool to effectively visualize and track the variables impacting the work flow.
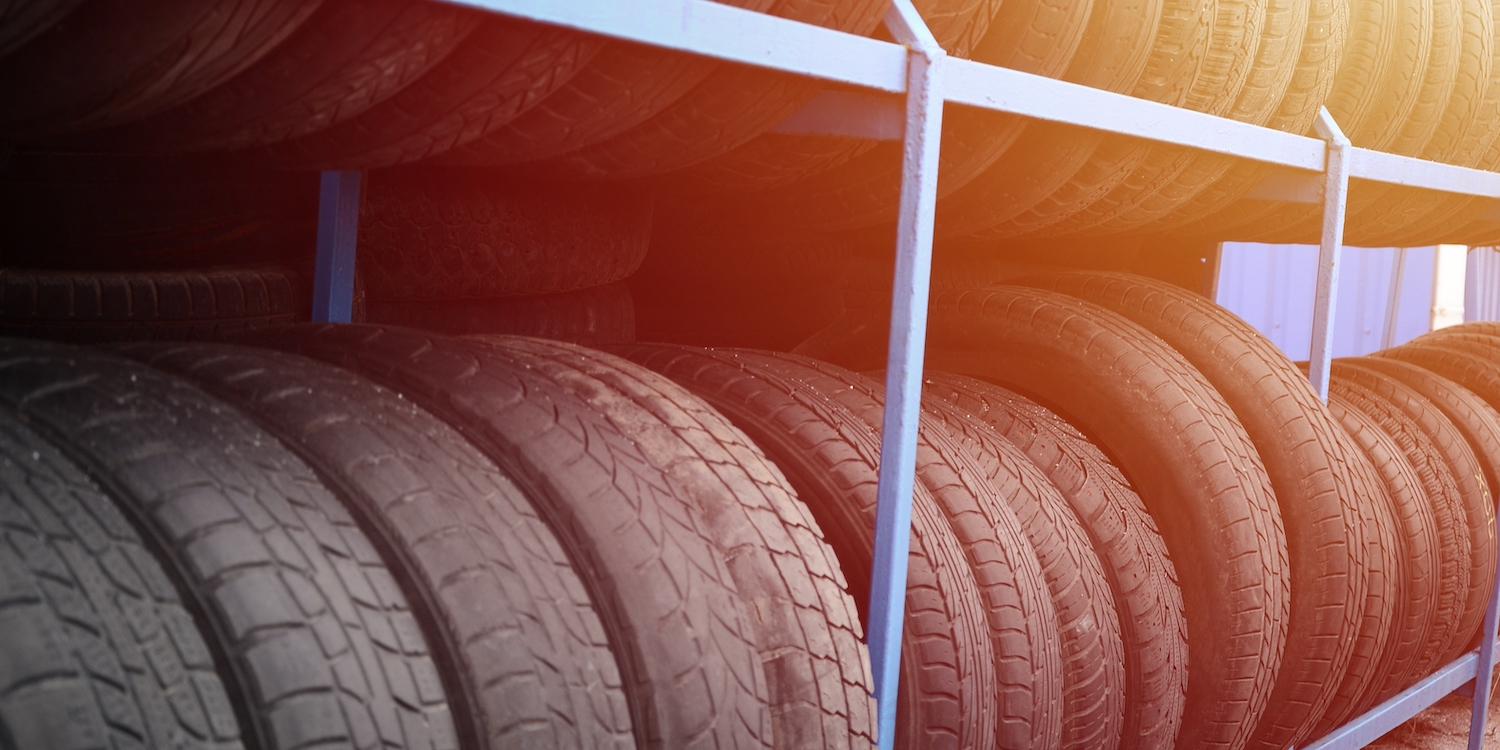
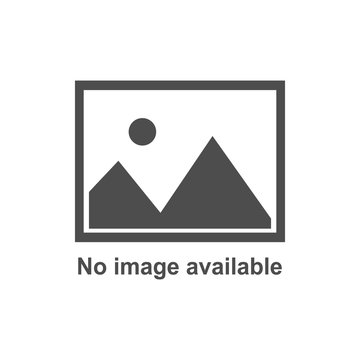
CASE STUDY – To bring consistency to the service provided to customers across their network of workshops, this Brazilian company has turned to Lean Thinking. Along the way, they found in it a different approach to leadership.
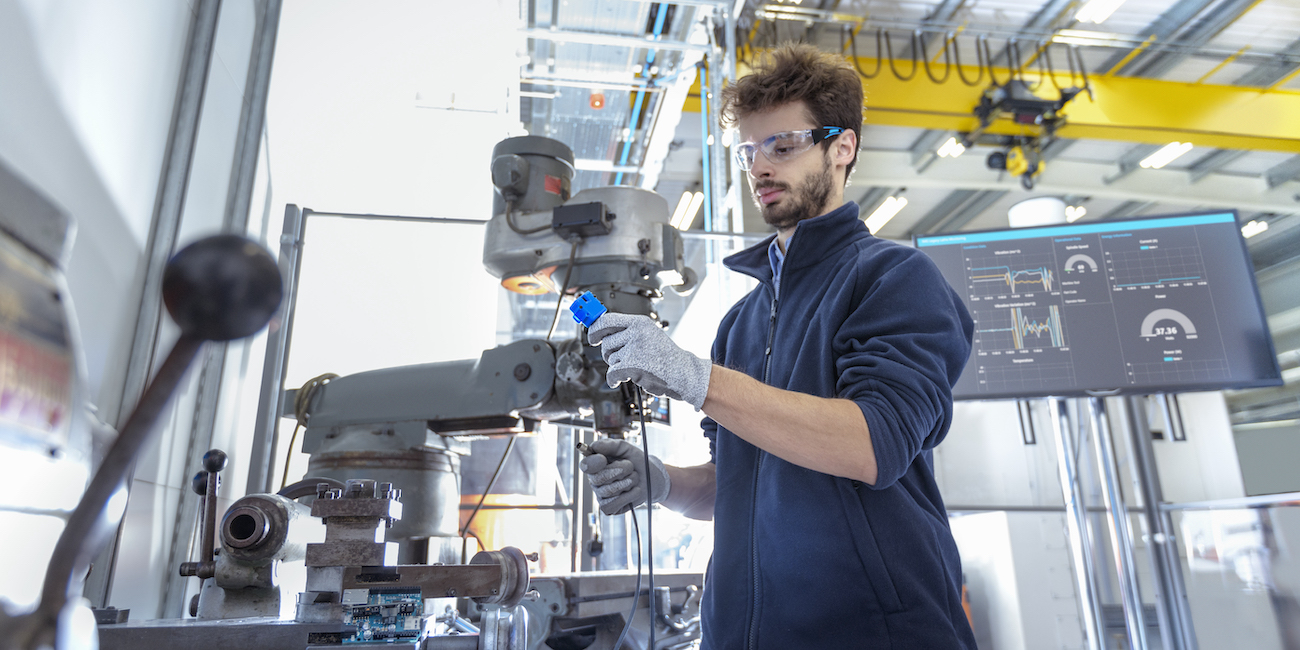
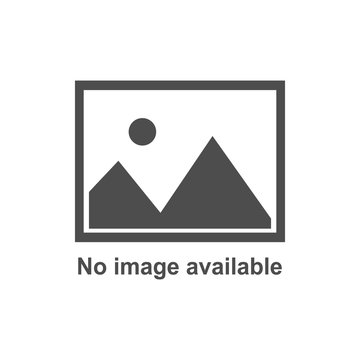
FEATURE – Through kaizen, people can directly participate in the improvement work. But without a manager’s clear responsibility and follow-up, they will left alone with the consequences of the introduced changes.
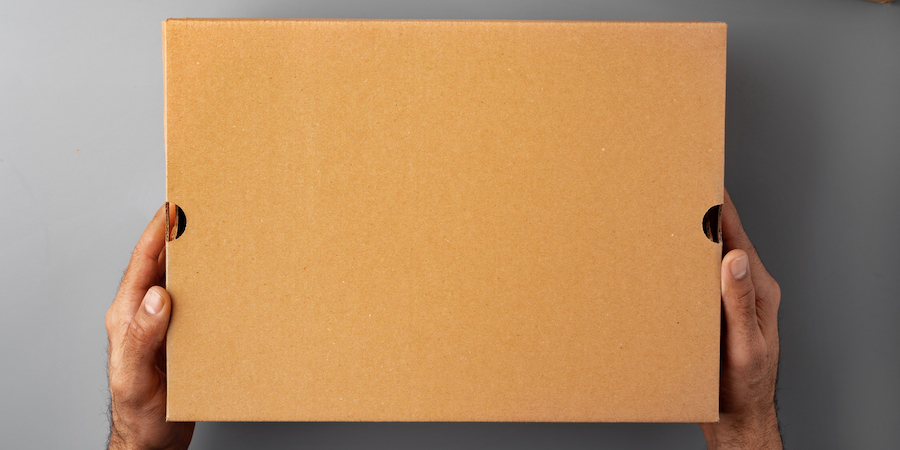
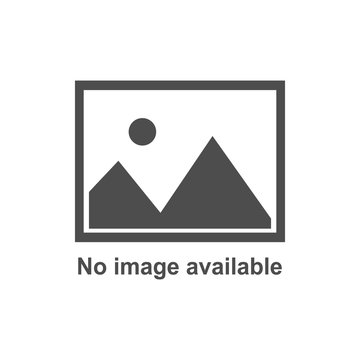
FEATURE – The author shares a story from a training session at the gemba, which contains a couple of important lessons on the Training Within Industry method.
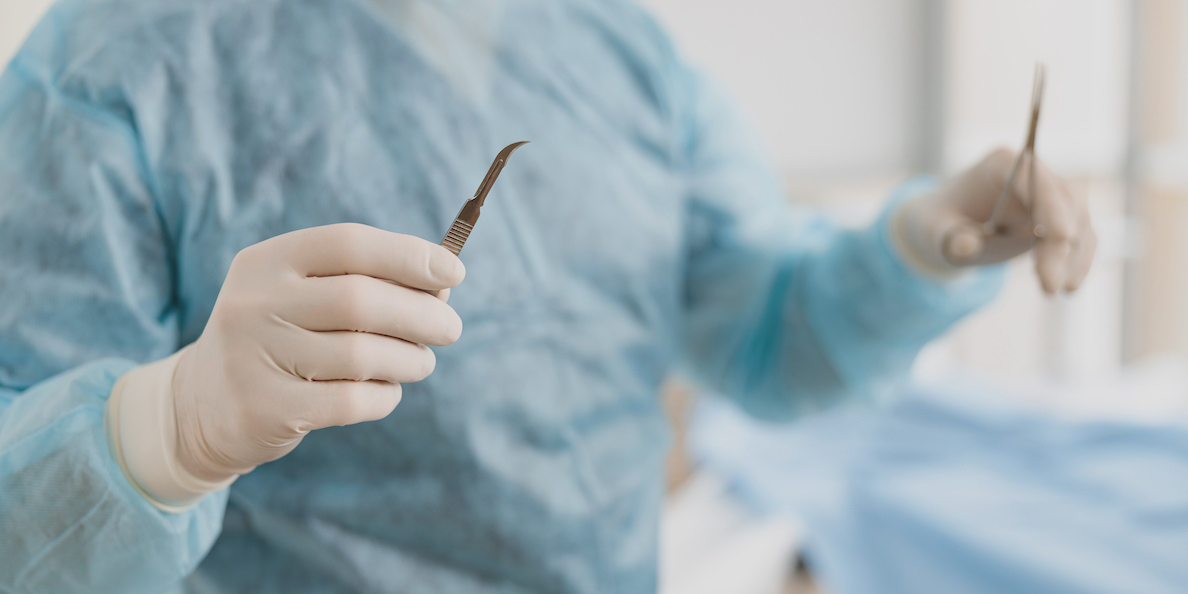
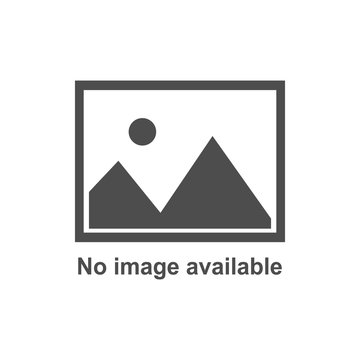
FEATURE - This surgery department was among the first areas in this hospital (maybe in the whole of Spain) to adopt Lean Thinking. Here's what their lean journey is focusing on more than 10 years after they started.
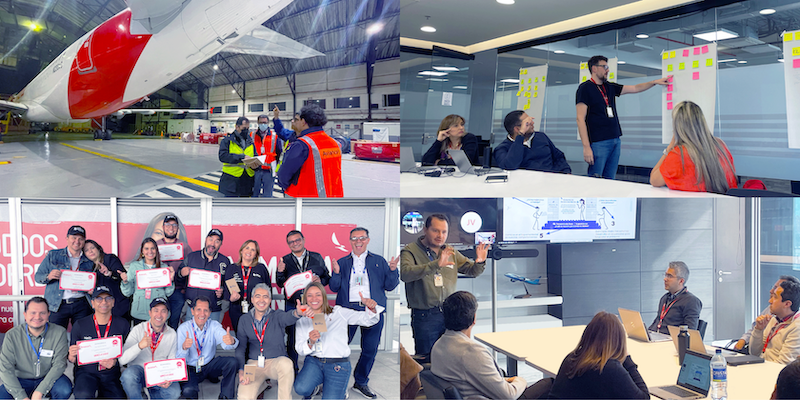
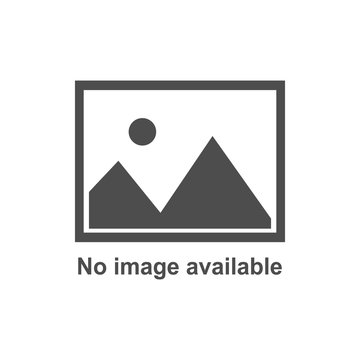
INTERVIEW – The lean journey of the Engineering and Maintenance Department of Colombian airline Avianca proves how important it is for leadership to spearhead change.
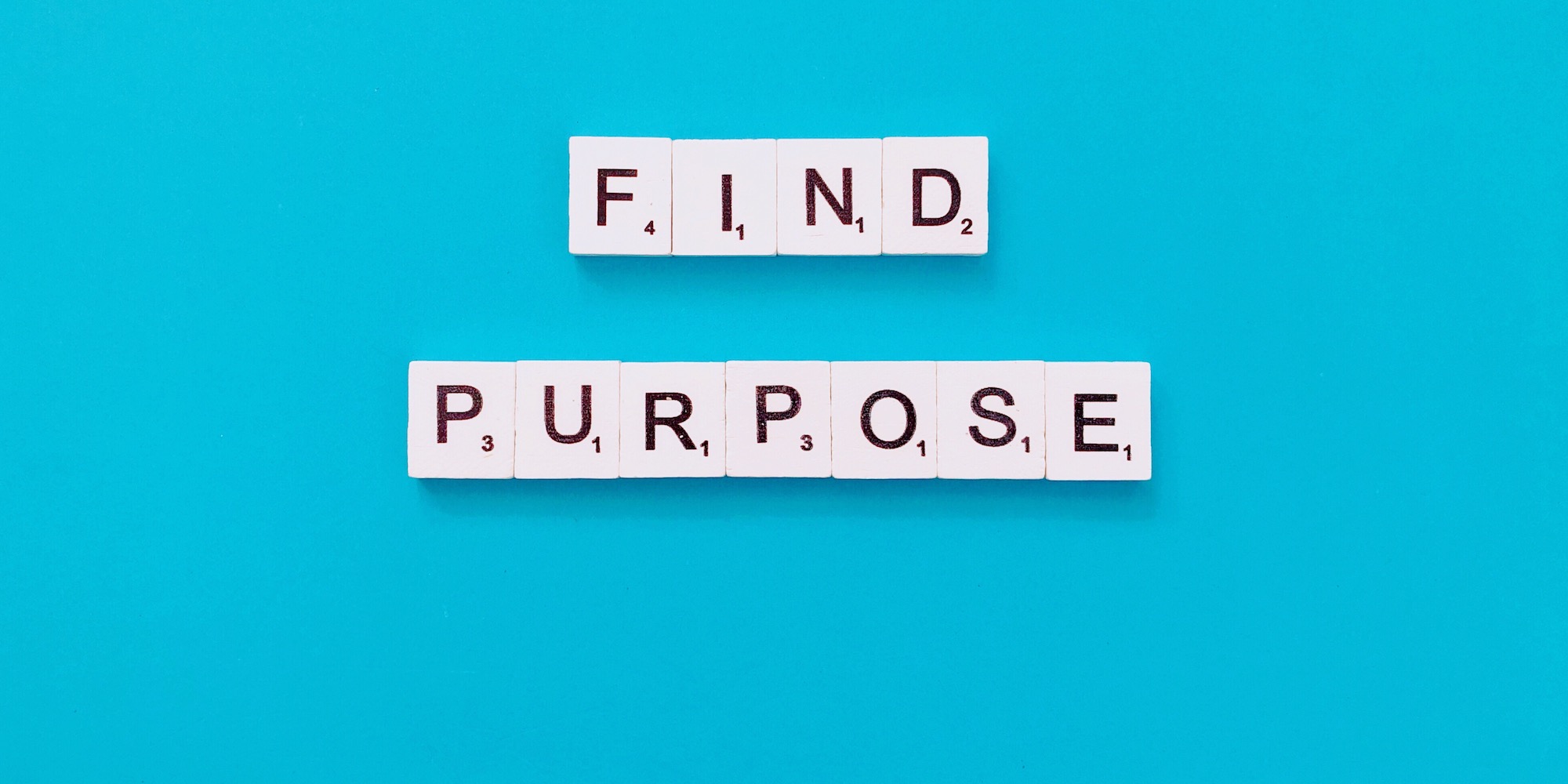
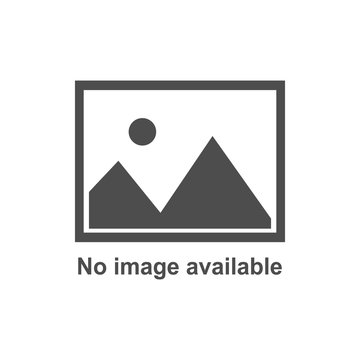
FEATURE – Why is lean change so hard to achieve in times of plenty? And why does it seem to be more attainable when chaos reigns? The author tries to answer these questions.
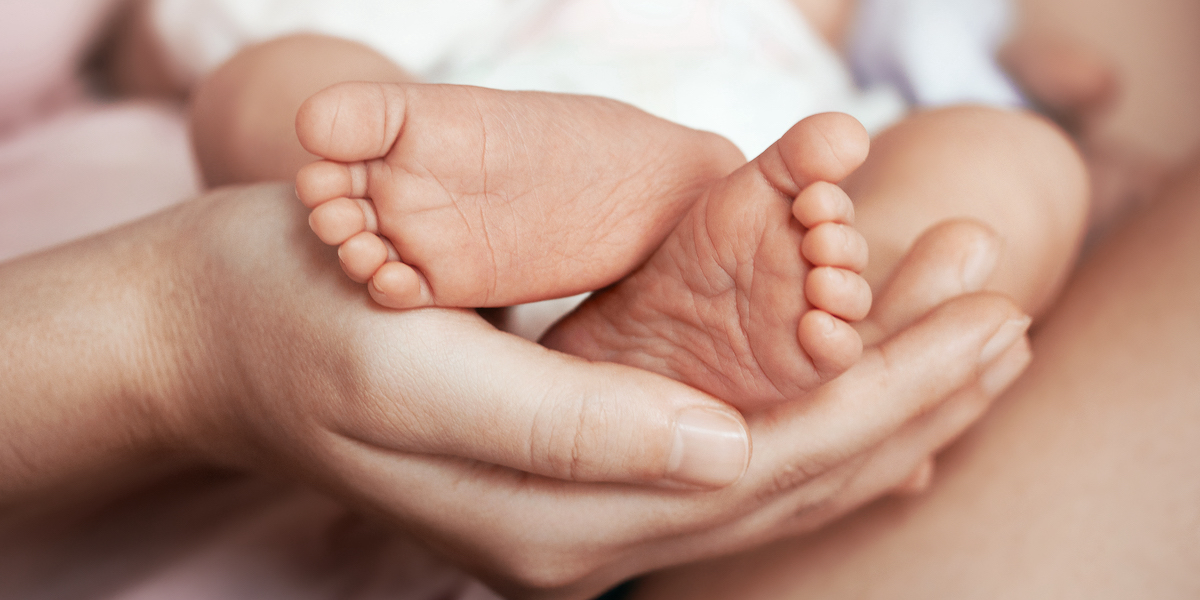
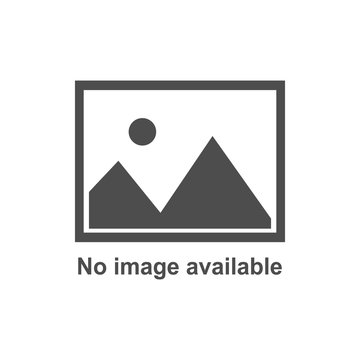
FEATURE - In the second article in his series, the author provides helpful tips for those interesting in bringing some Lean Thinking to their parenting, focusing on the first five years of a child's life.
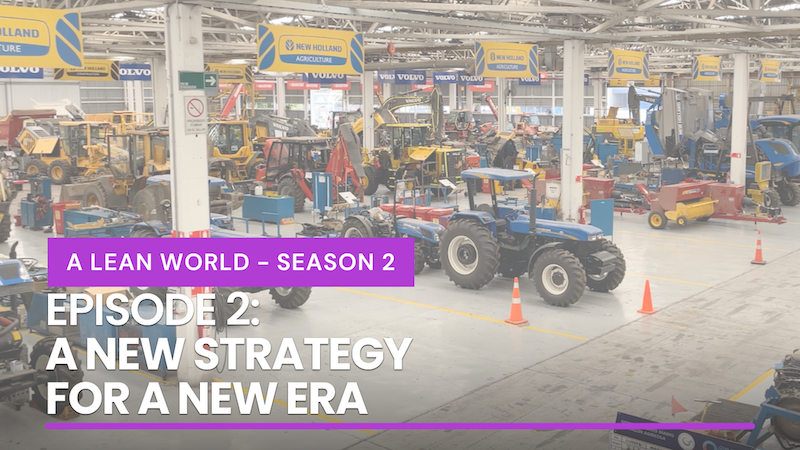
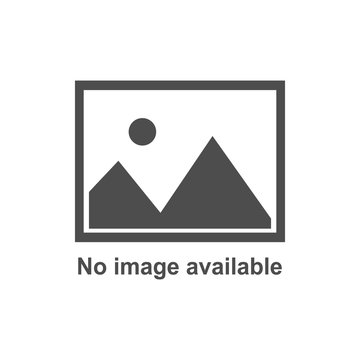
WEB SERIES – In the second episode of our docuseries on lean in Chile, we learn how, with a clear purpose and strong commitment from leadership, SKC is transforming its processes and mindset and building a competitive advantage.
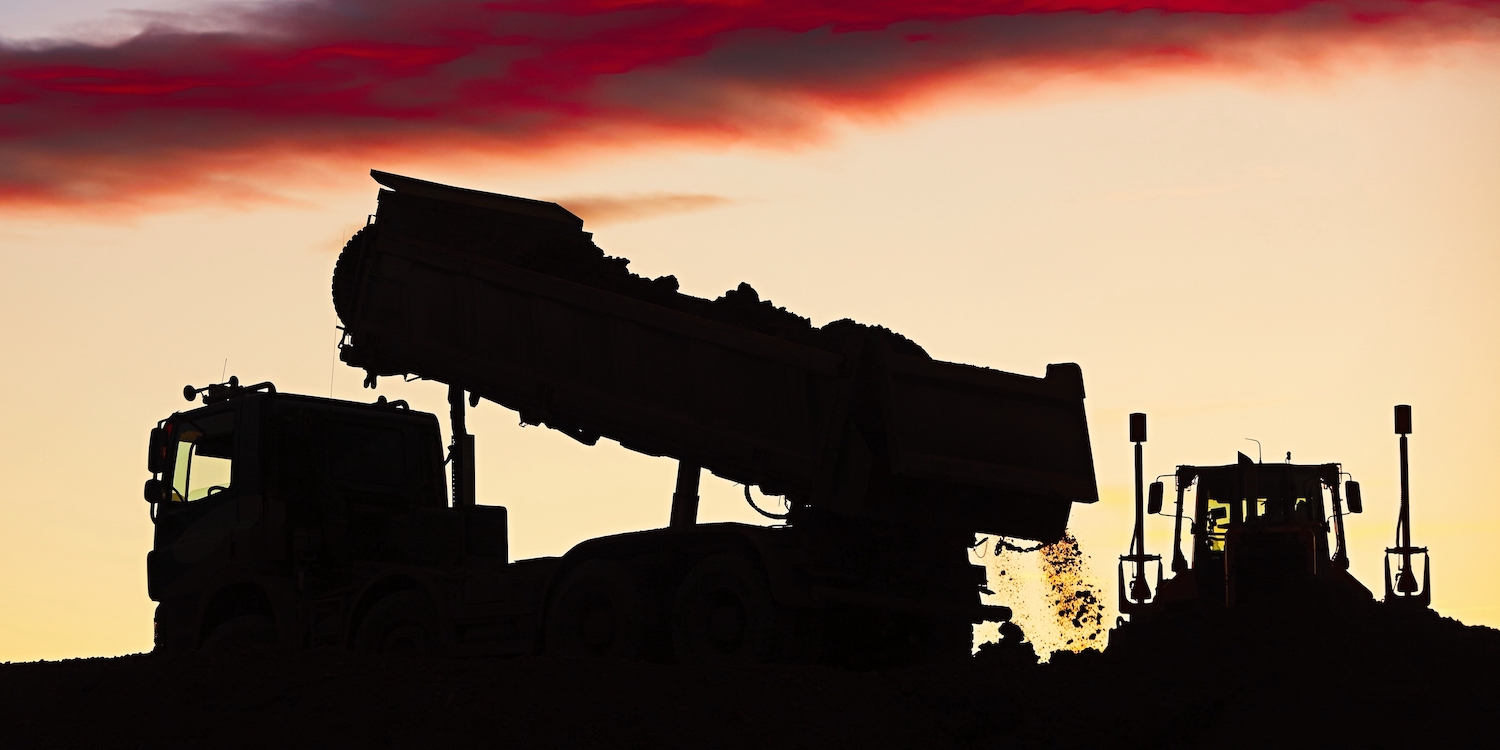
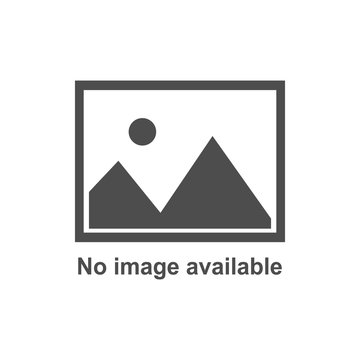
INTERVIEW – Drawing on 33 years of experience working in product development at Caterpillar, the interviewee reflects on lean in engineering.
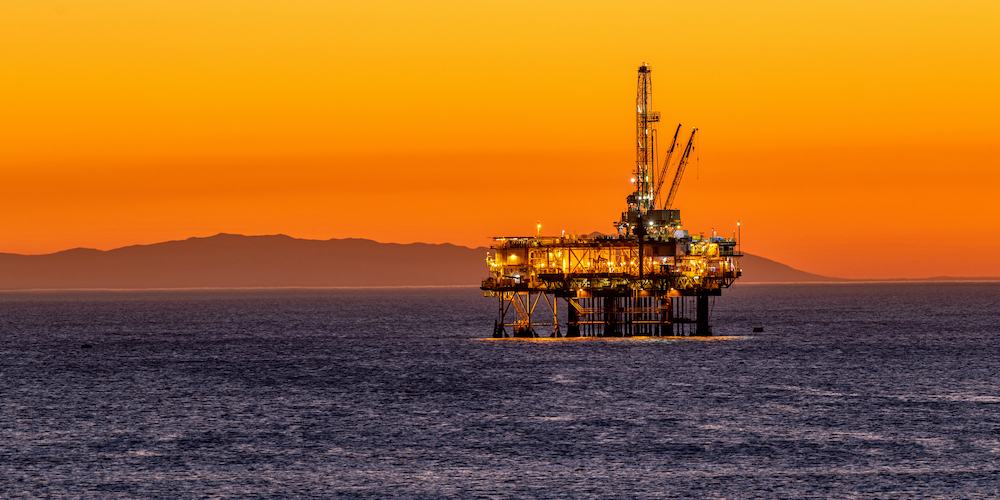
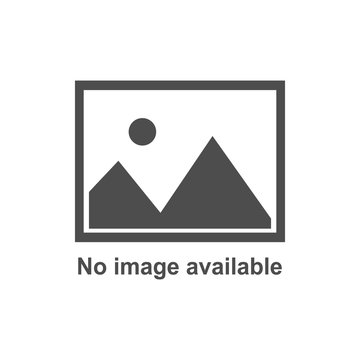
INTERVIEW – In this Q&A, the Chief of Transformation of oil and gas company TechnipFMC tells us about their experience implementing Lean Product and Process Development.
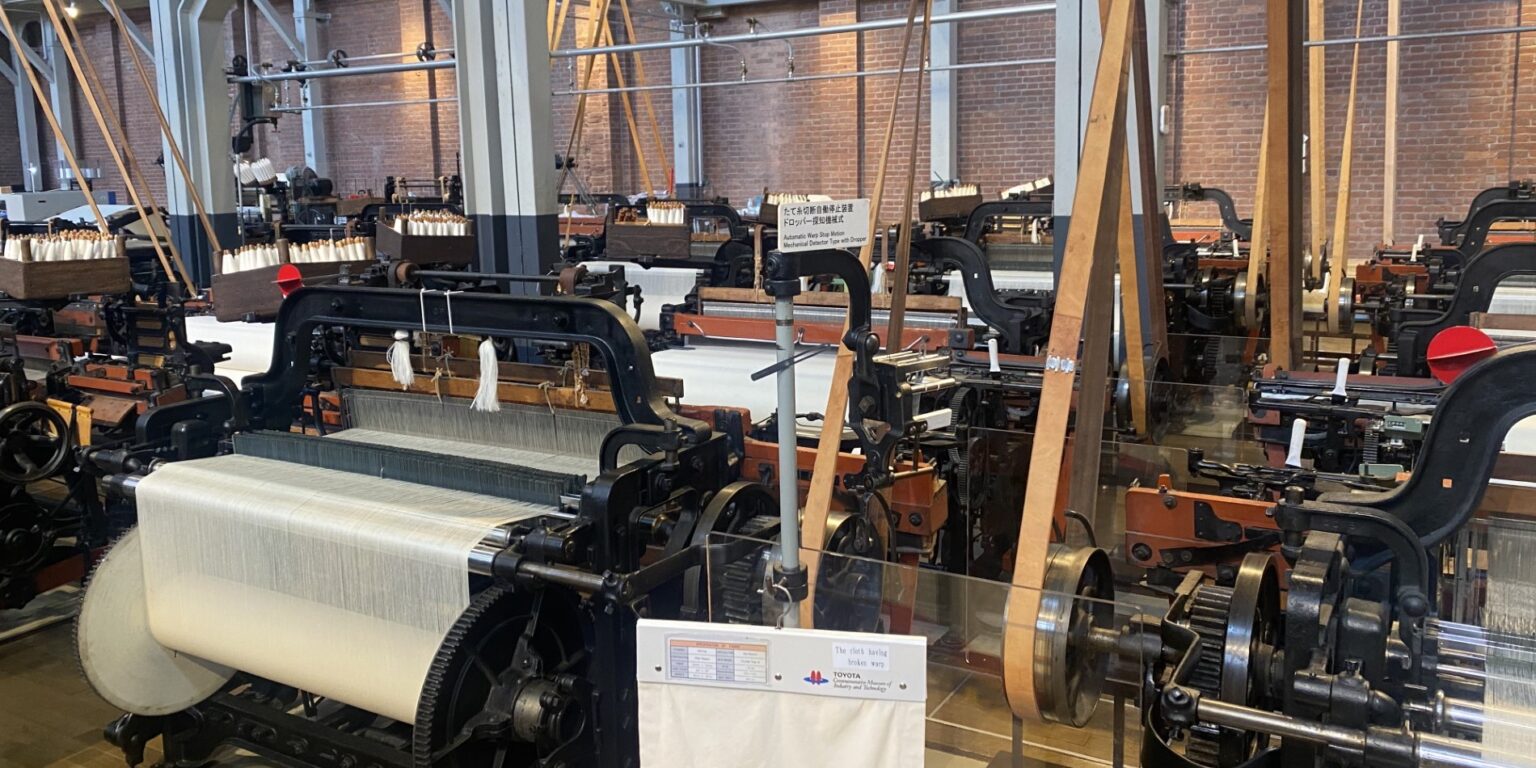
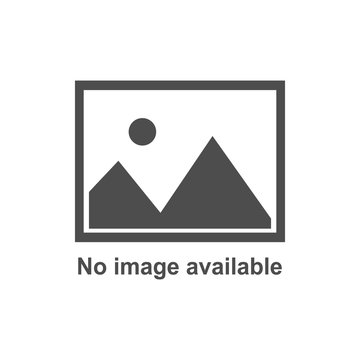
FEATURE – Fresh of a study tour in Japan, the authors wonder if there is anything left to learn from Toyota’s network of suppliers in the age of AI and digital. Hint: it’s a rethorical question.
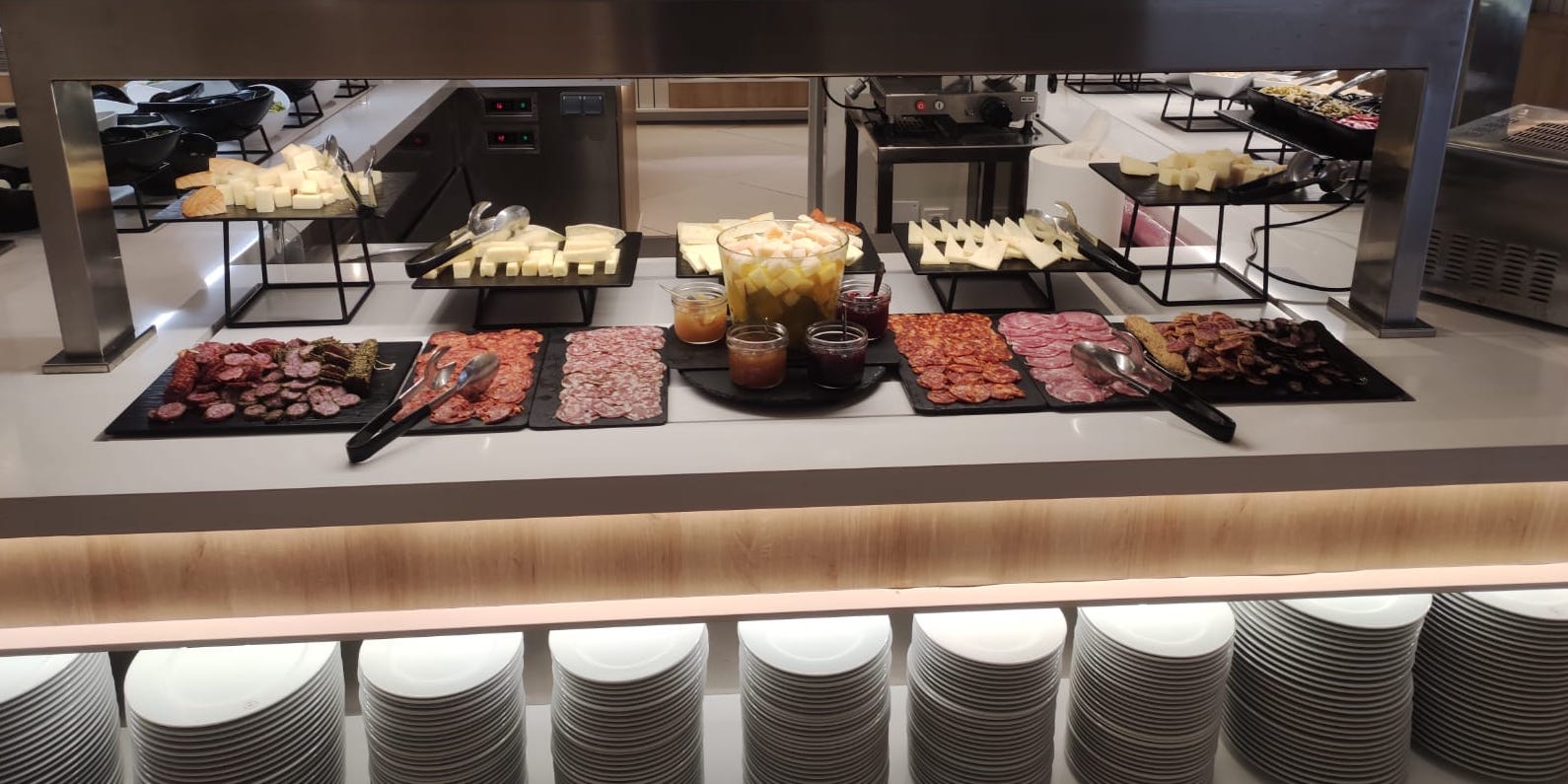
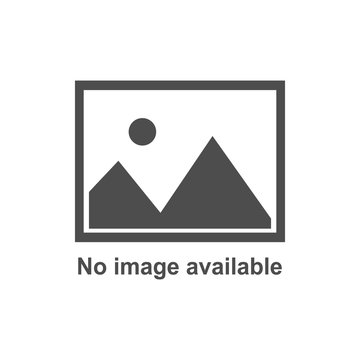
VIDEO INTERVIEW – This hotel in the Canary Islands is bringing lean to its Kitchen Department, hoping to streamline the process and provide a better service to diners.
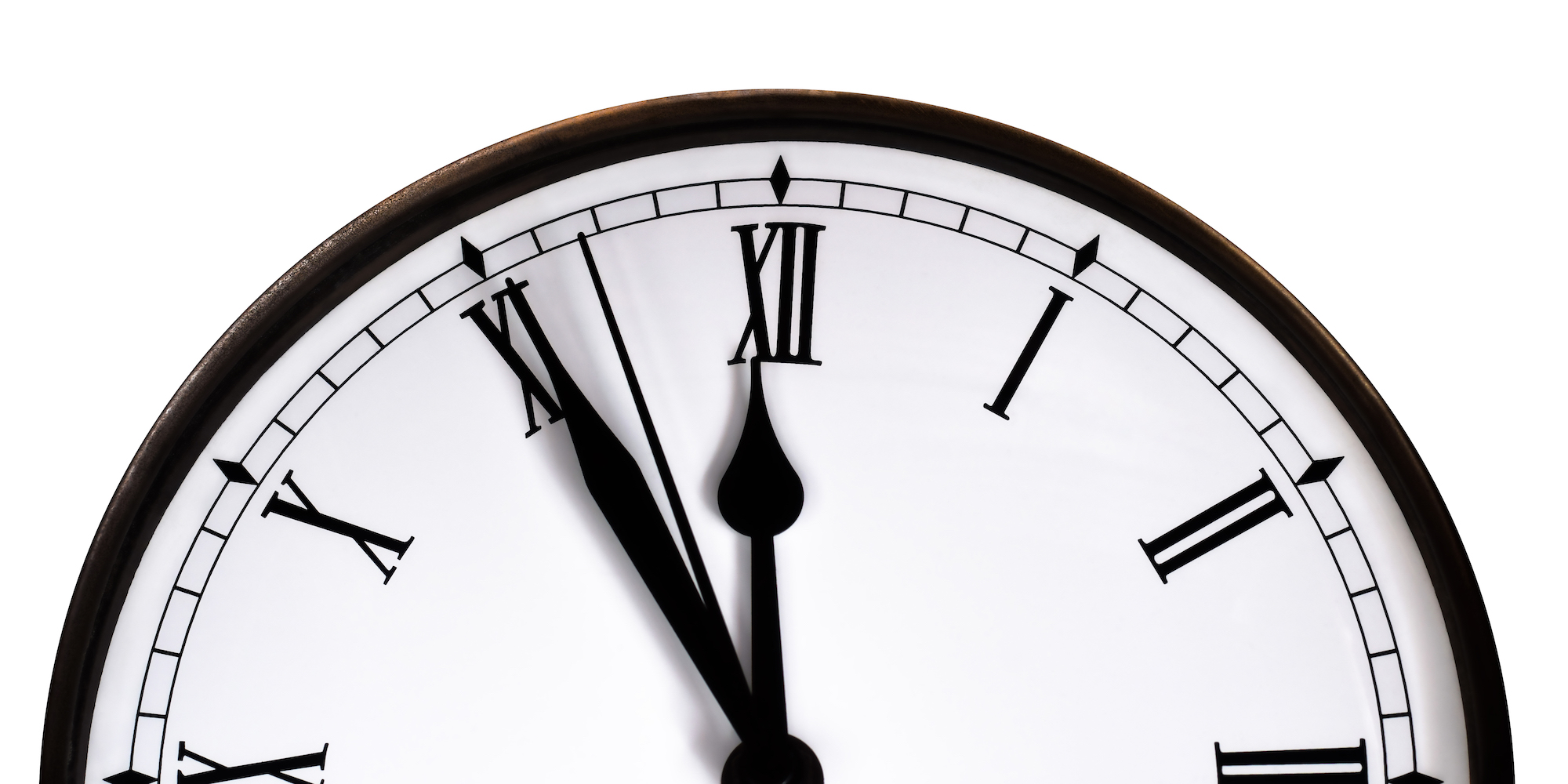
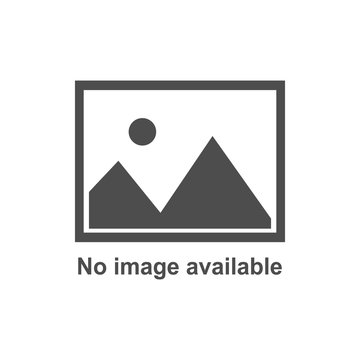
FEATURE – Freeing up beds is an age-old problem for hospitals. The medical area of this Catalan hospital group has found in lean a creative way to solve it.
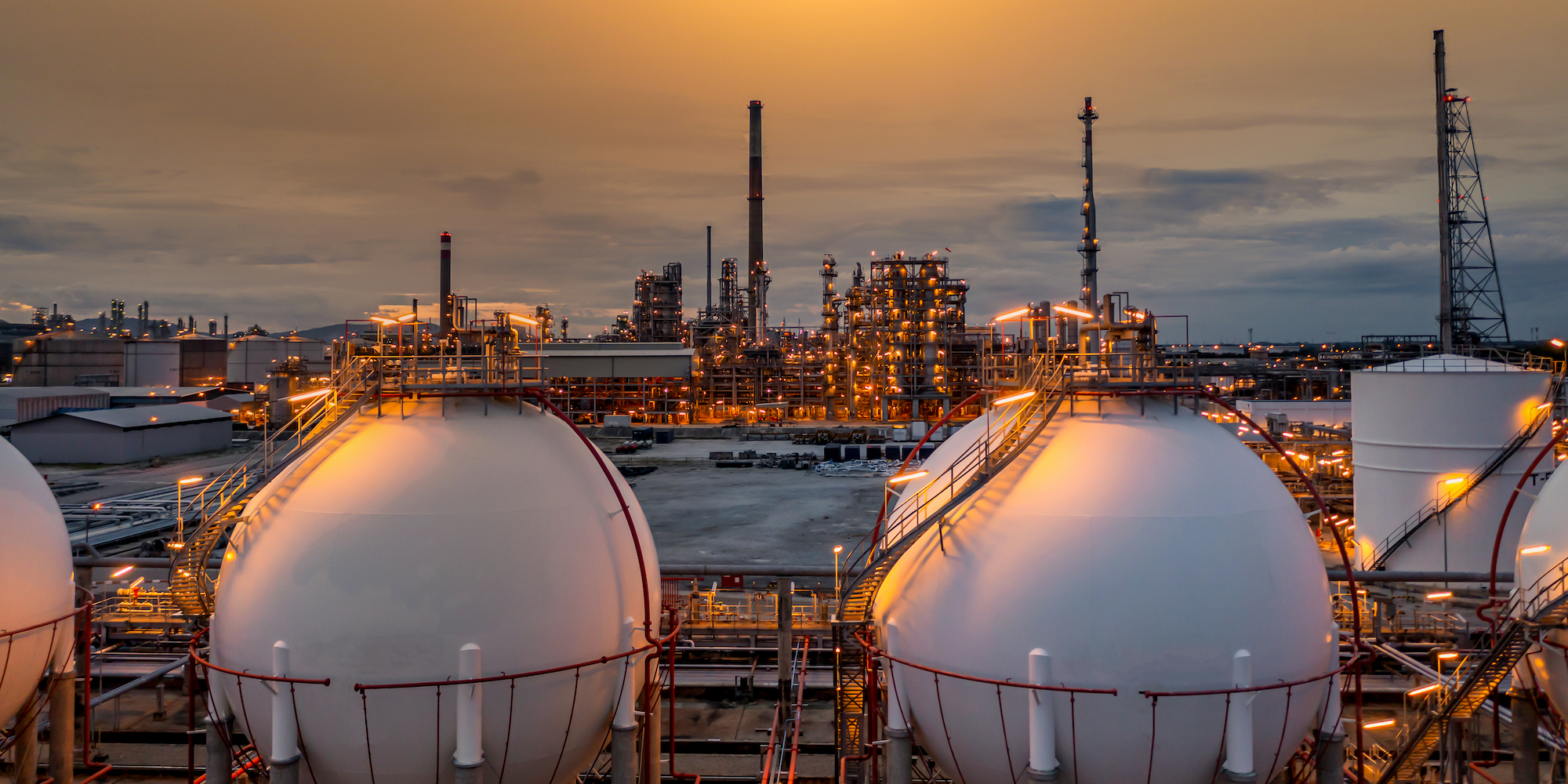
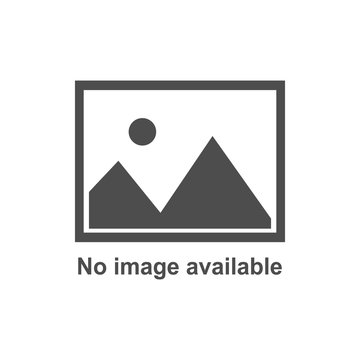
CASE STUDY – By leveraging Daily Management (DM), Supergasbras was able to change its trajectory and add more value to the customer in a critical sector for society.
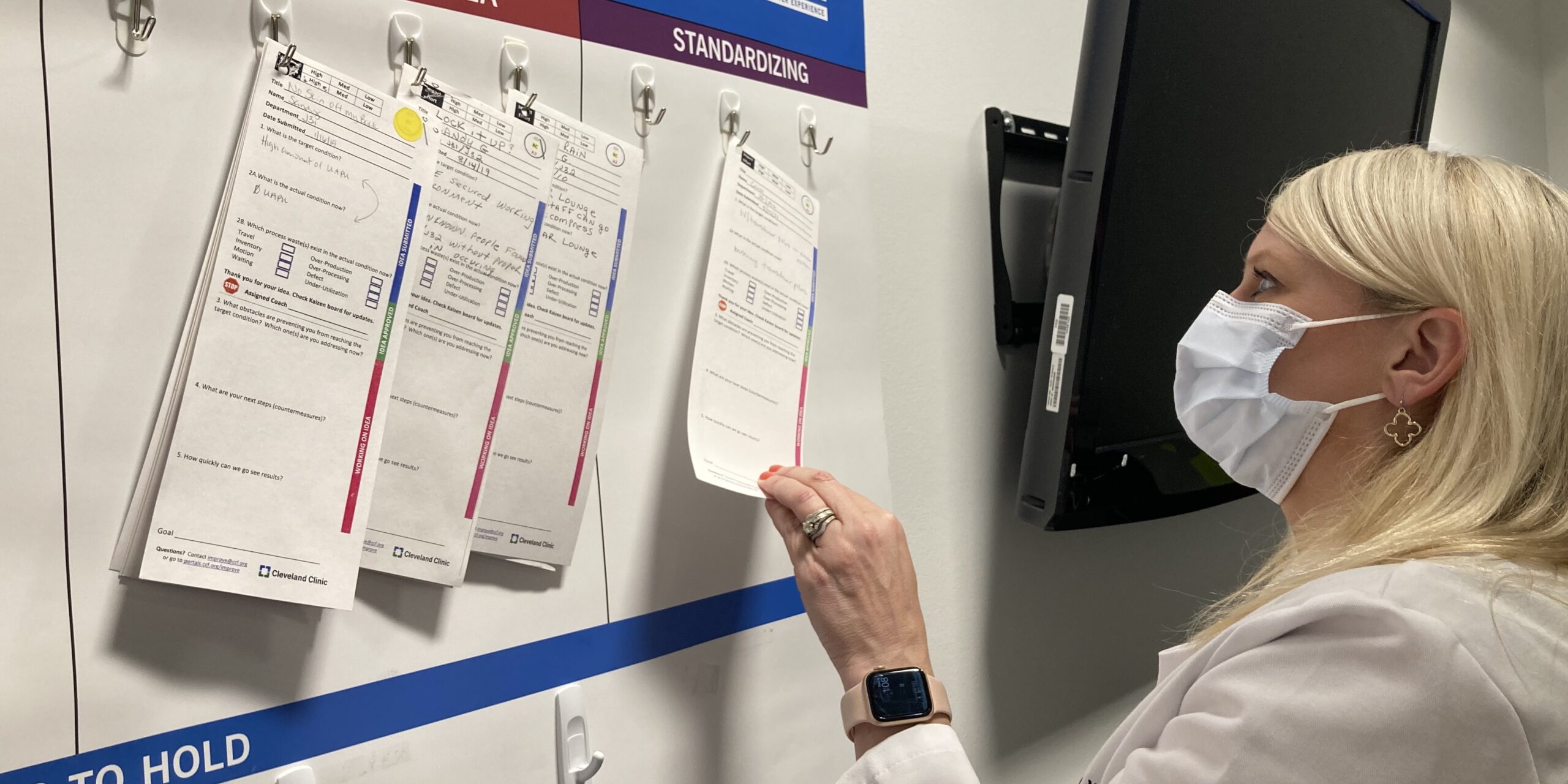
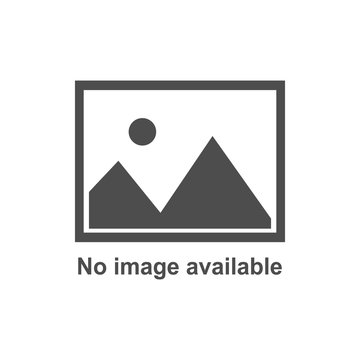
INTERVIEW – Cleveland Clinic has been on a lean journey for a few years now. In this interview, their Chief Improvement Officer and Chief Nursing Officer talk continuous improvement, metrics, and sustaining results.
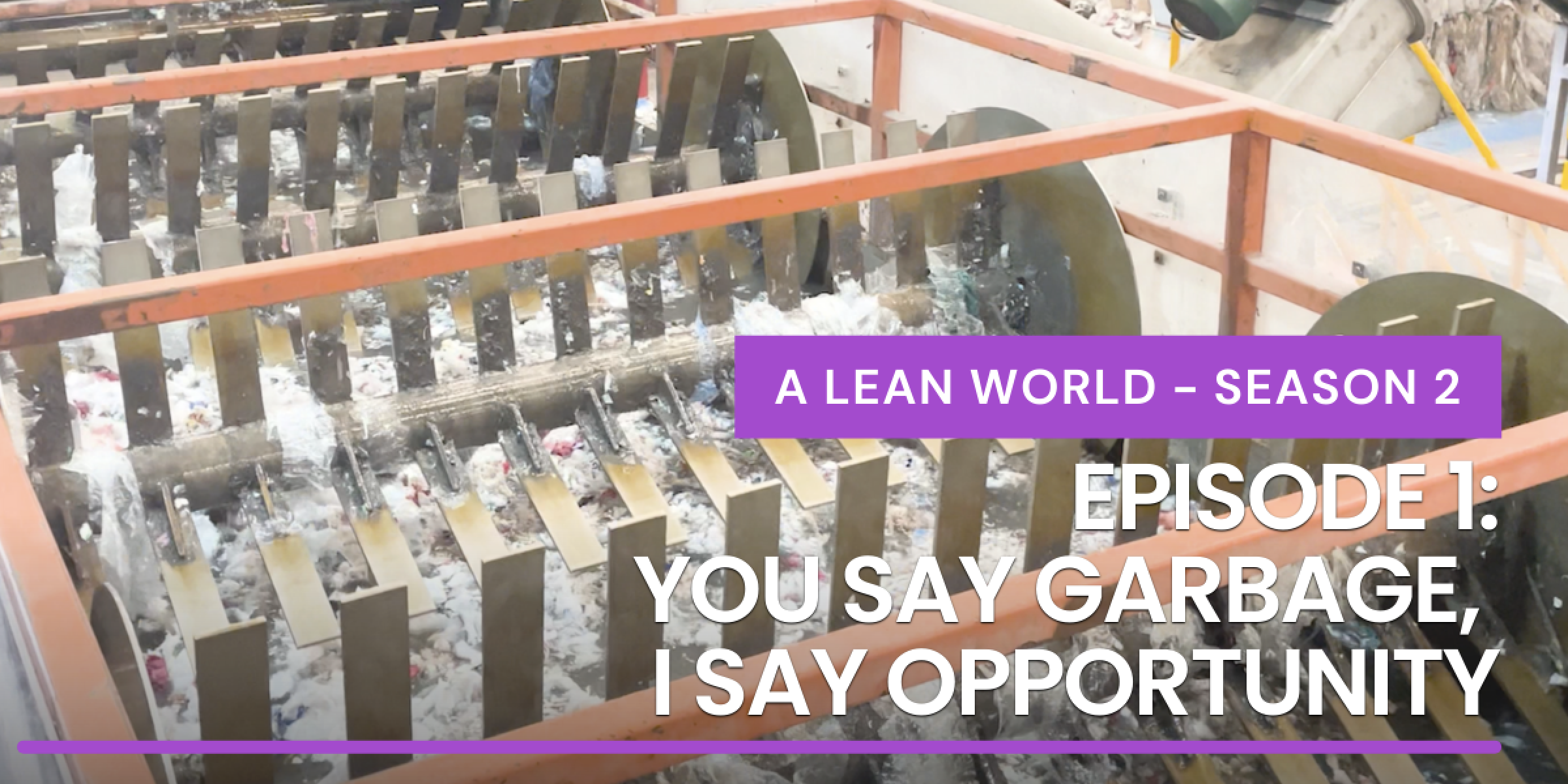
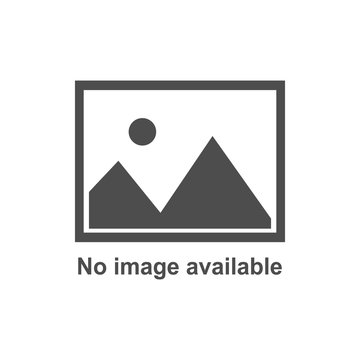
WEB SERIES – Season 2 is here! In the first episode of this season, we visit a company in Chile that shows us how sustainability can be the cornerstone of an improvement project... and not just an afterthought.
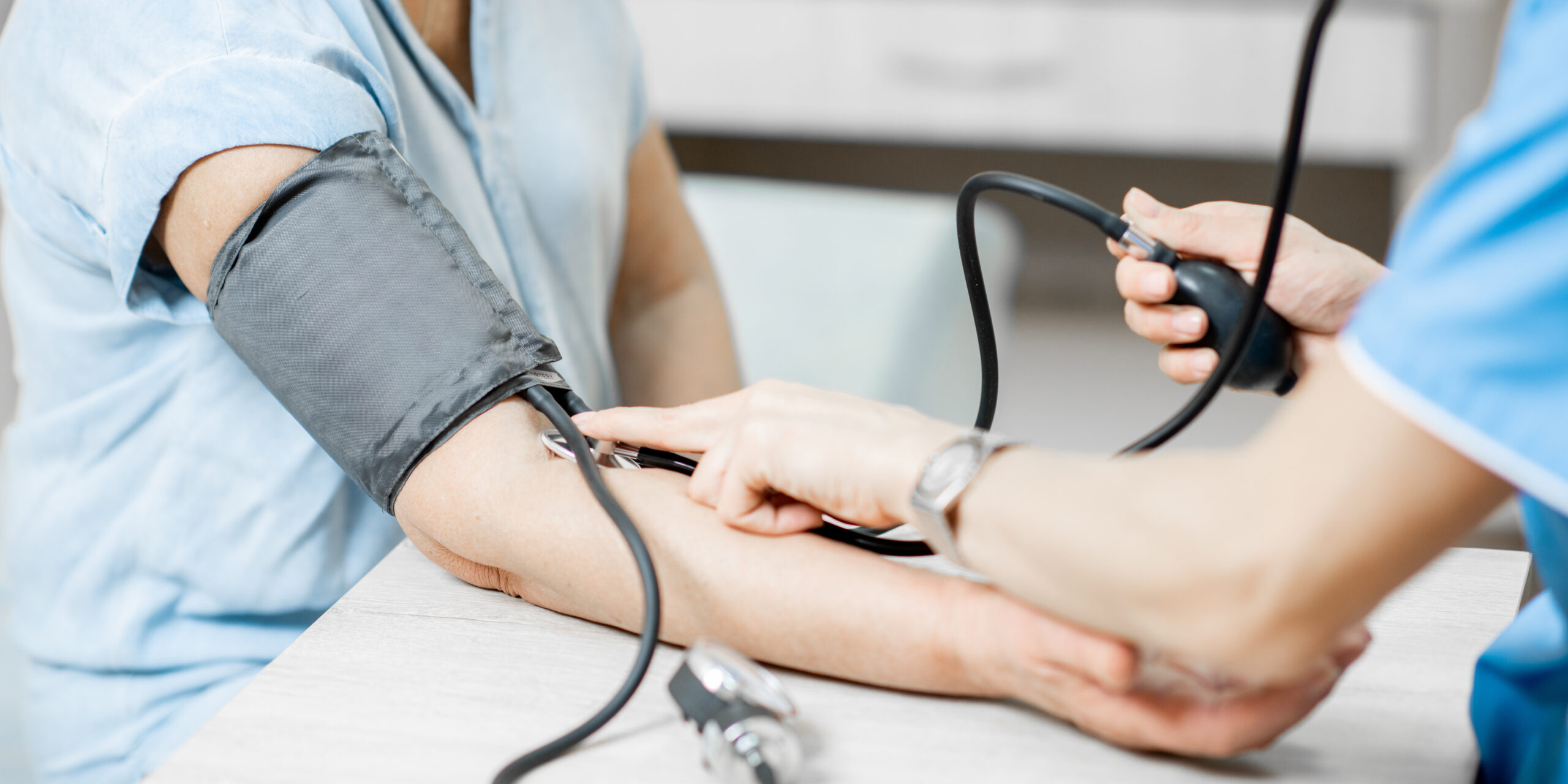
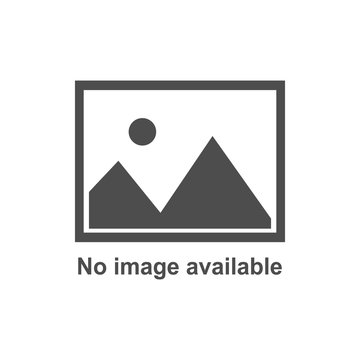
FEATURE – The ER of this Catalan hospital is finding great value in the application of Lean Thinking, which has already led to a dramatic change in its processes and to better care for patients.
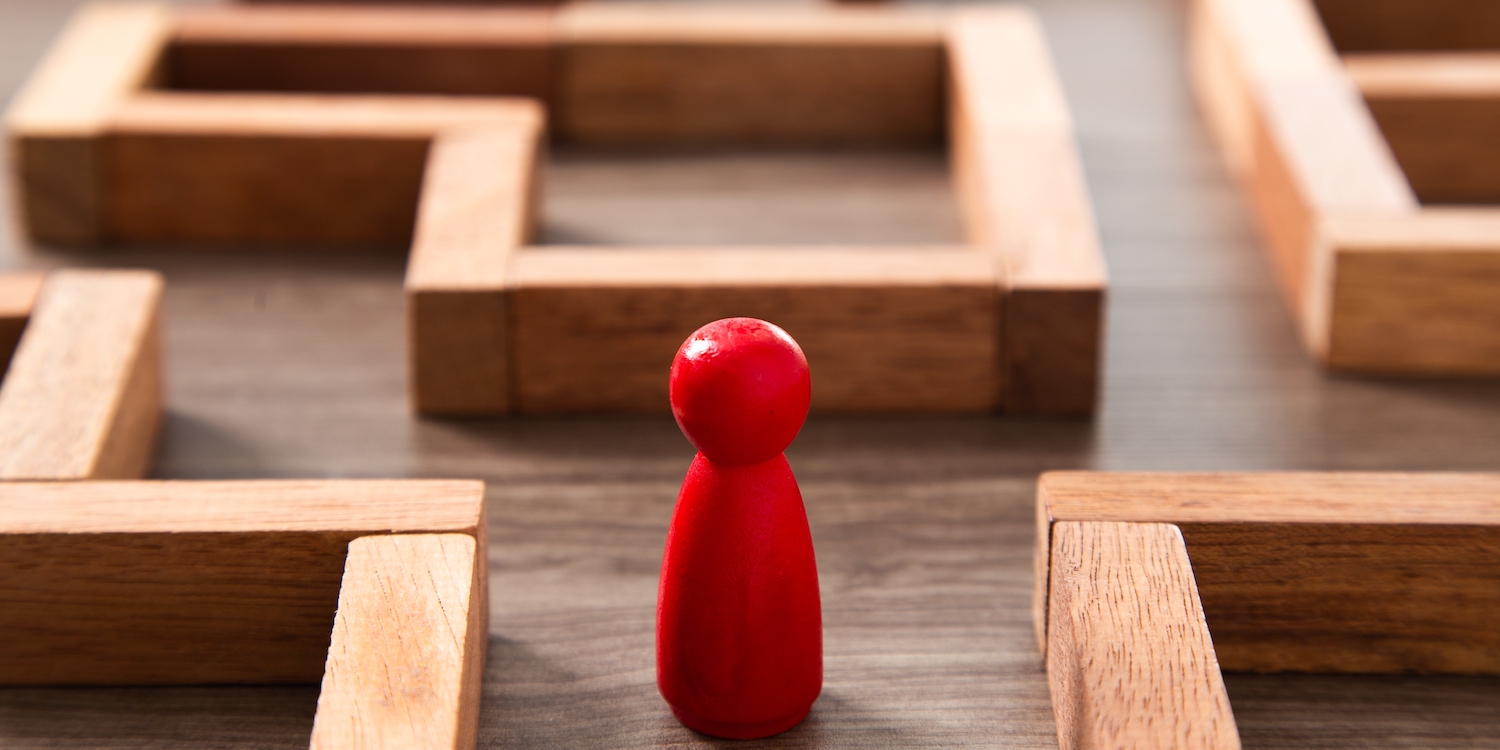
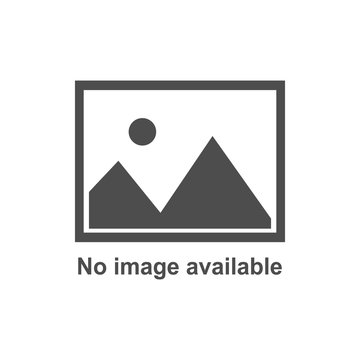
FEATURE – The hardest part of a learning journey is learning to learn and figuring out what we need to learn - as opposed to we want to. The author wonders whether we are drawing the right lessons from TPS and highlights a few things we are underemphasizing.
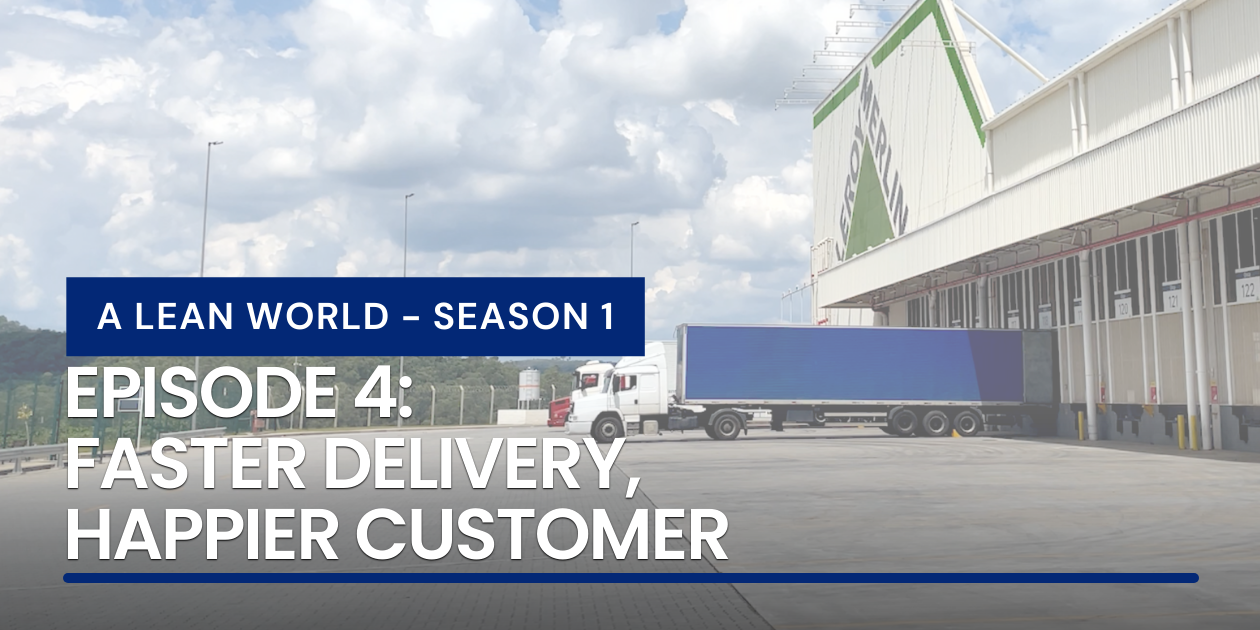
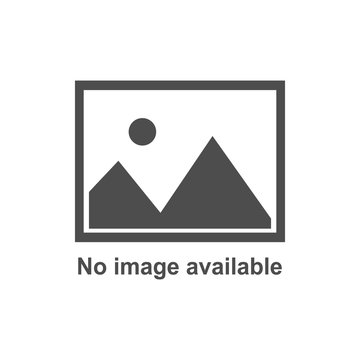
WEB SERIES – In the fourth and final episode of Season 1 of our docuseries, we visit home improvement and gardening retailer Leroy Merlin and learn about their efforts to lean out their supply chain.
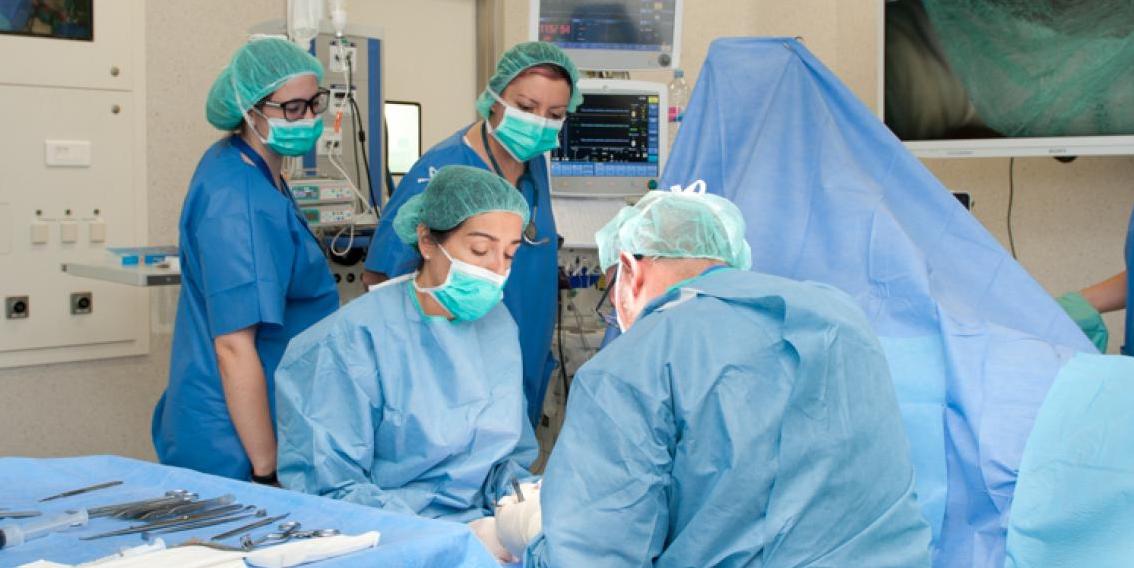
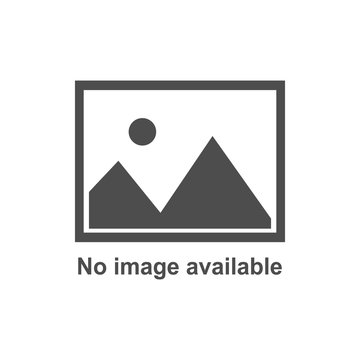
CASE STUDY – The Hospital de Bellvitge in Barcelona is relying heavily on hoshin and Kata to create a working environment based on collaboration and joint problem solving.
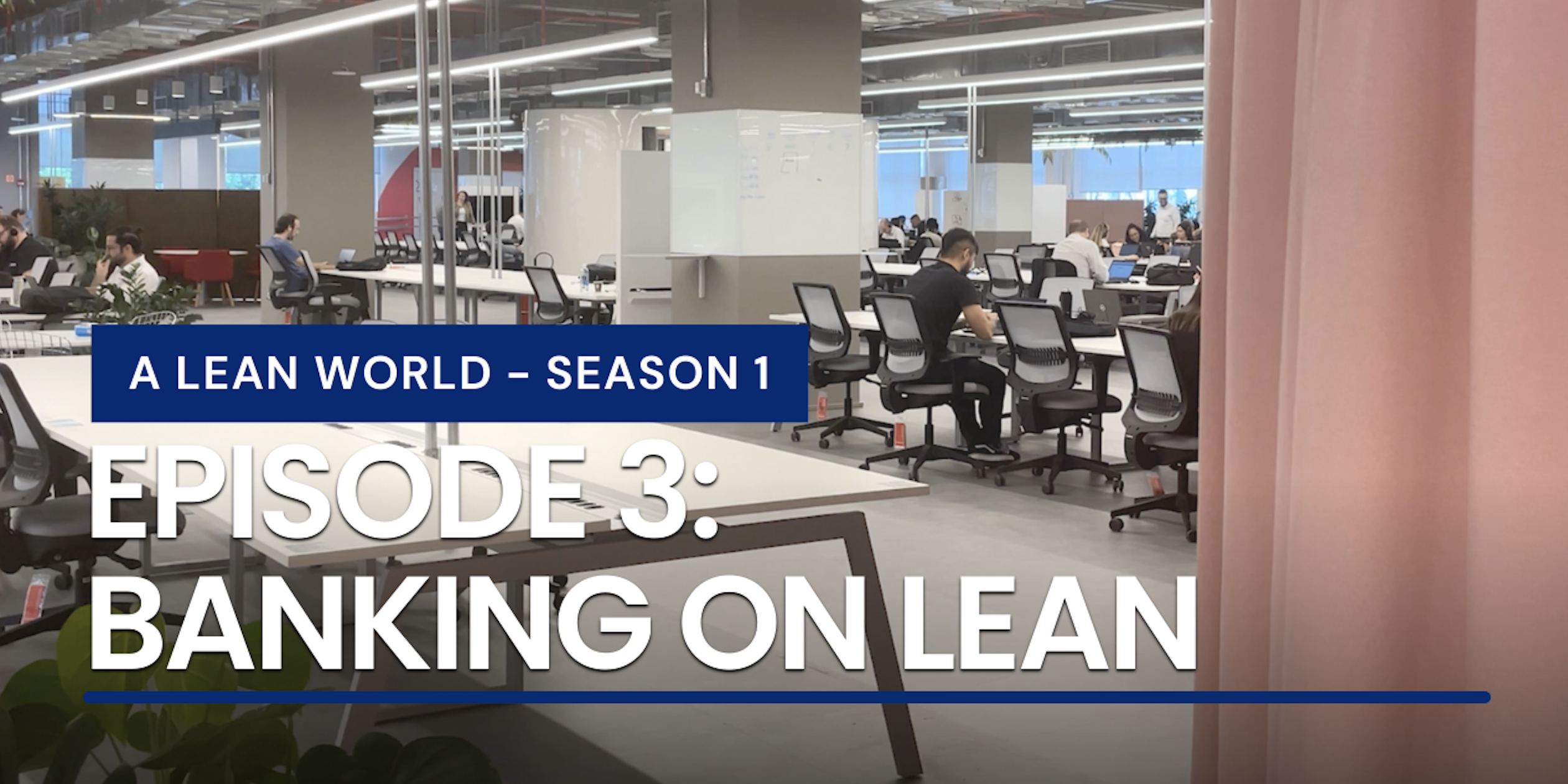
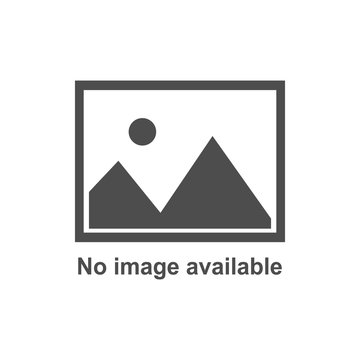
WEB SERIES – Episode 3 of our docuseries on lean in Brazil takes us to the second largest bank in the country. Learn how Bradesco is striving to improve its processes to provide more value to its customers using Lean Thinking.
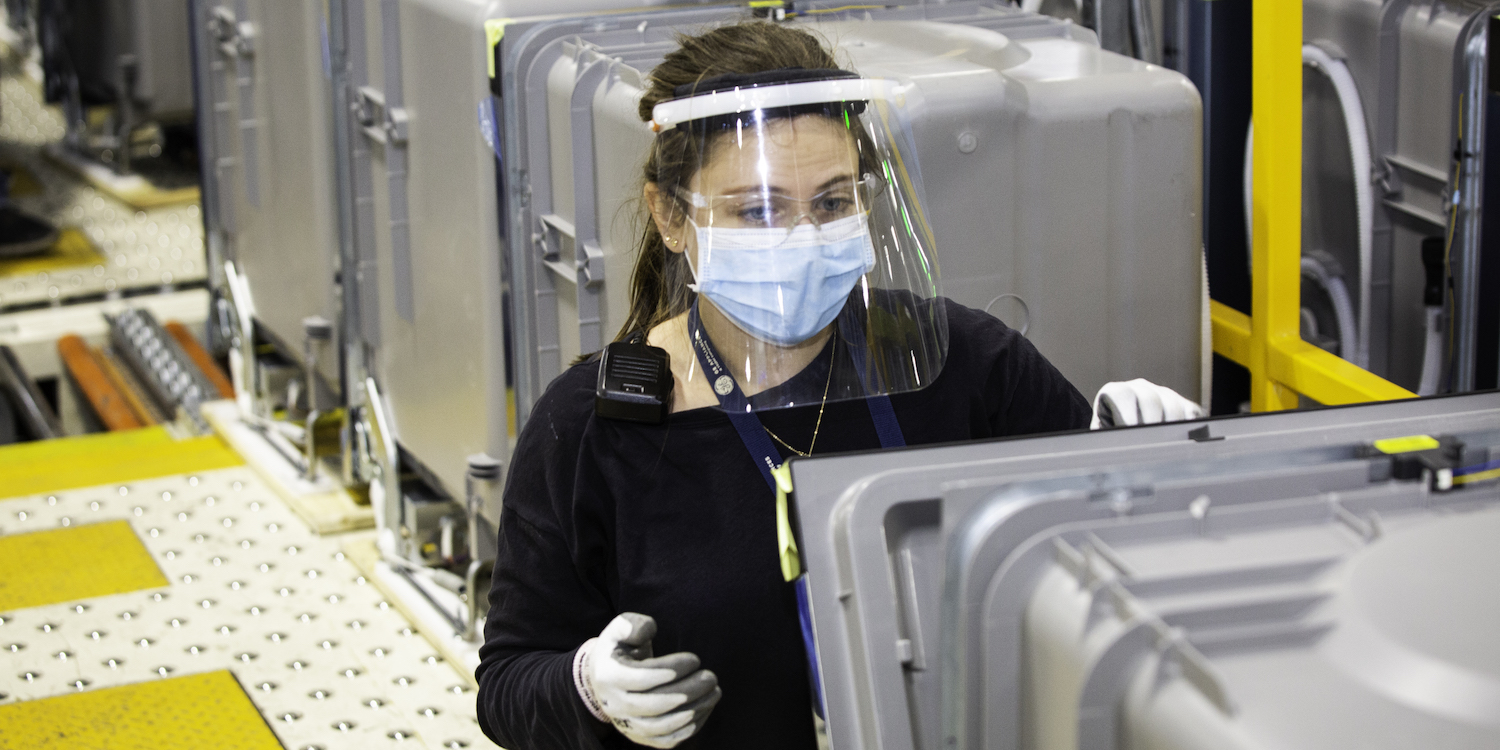
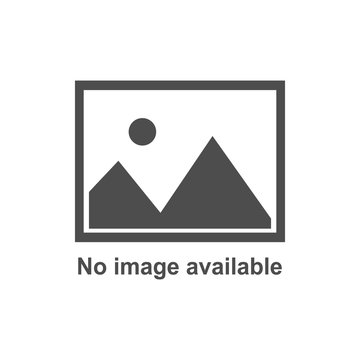
INTERVIEW – In 2020, GE Appliances had to stand up a brand-new assembly process for a new dishwasher. The leader responsible for the program explains how LPPD helped them to get it right.
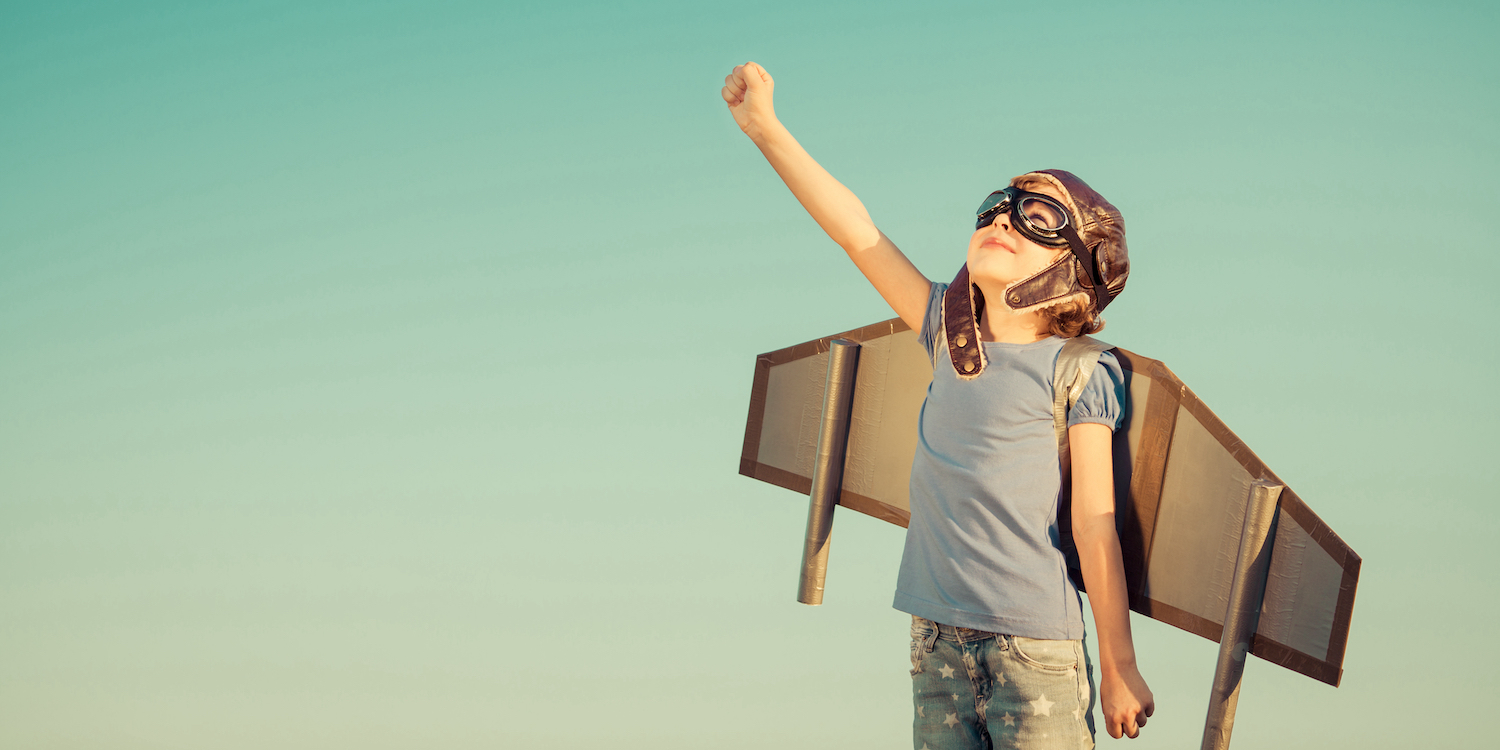
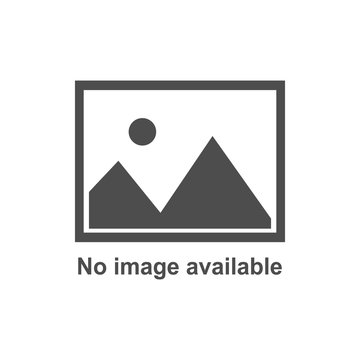
FEATURE – In this new series, the author will walk us through some uncommon ways to apply lean – with a particular focus on establishing productive and enjoyable relationships. In the first instalment, he introduces the concept of lean parenting.
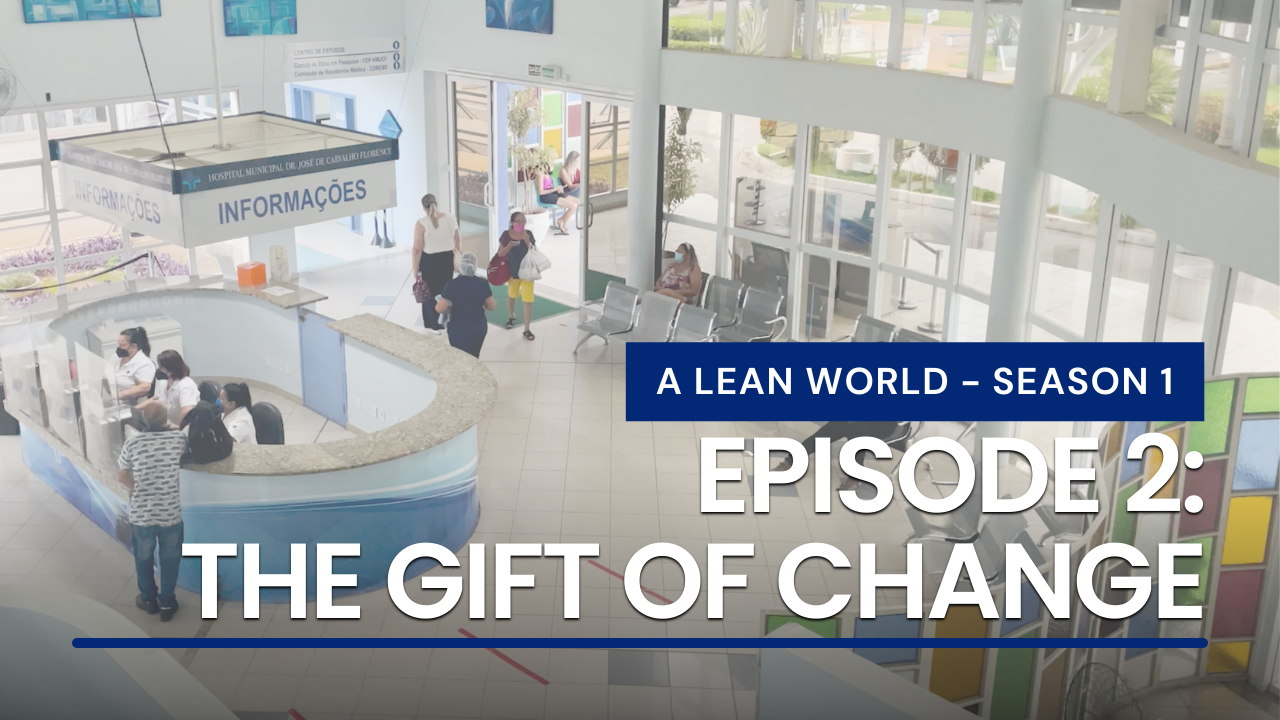
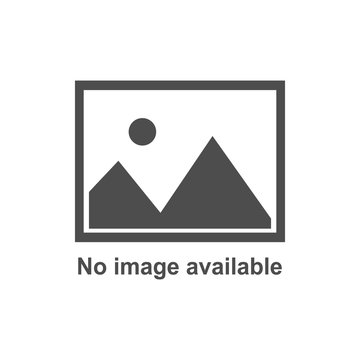
WEB SERIES – In Episode 2 of our docuseries on lean in Brazil, we learn how the pioneering efforts of a cancer clinic have inspired the city of São José dos Campos to transform into a lean healthcare cluster.
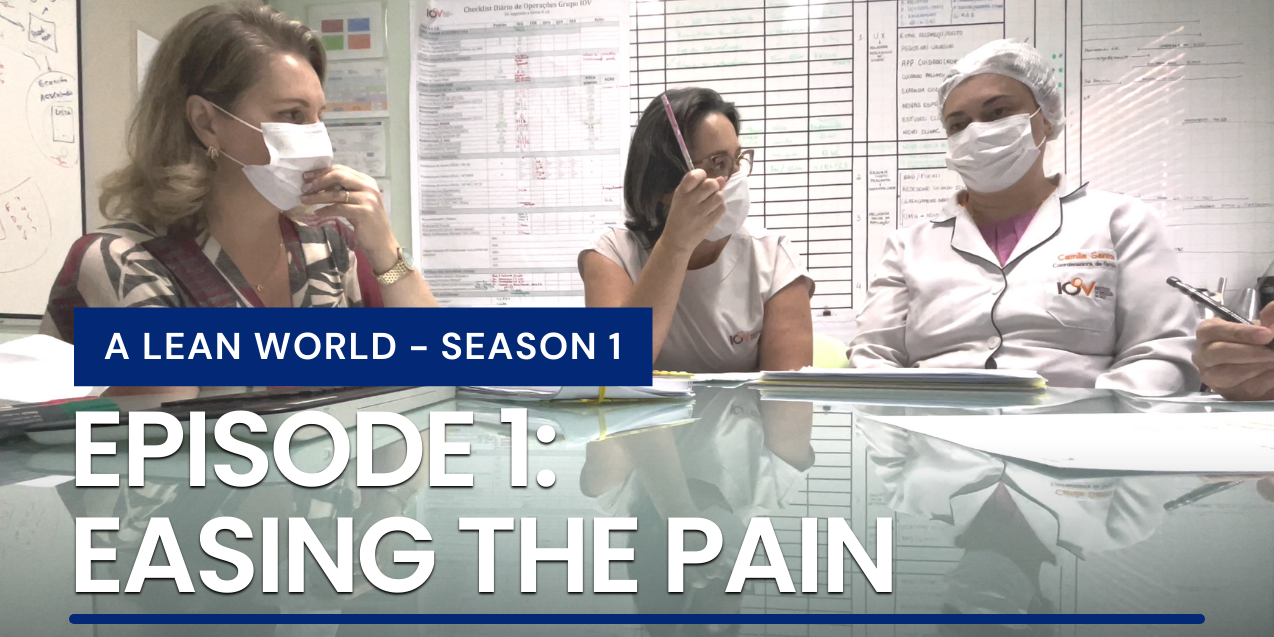
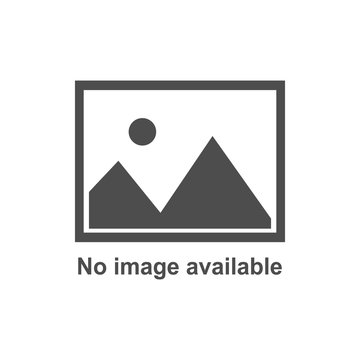
WEB SERIES – Today, we launch a new documentary series on lean around the world, with the first season focusing on lean in Brazil. In the first episode, we visit the lean clinic on a mission to reduce the burden on cancer in our lives.
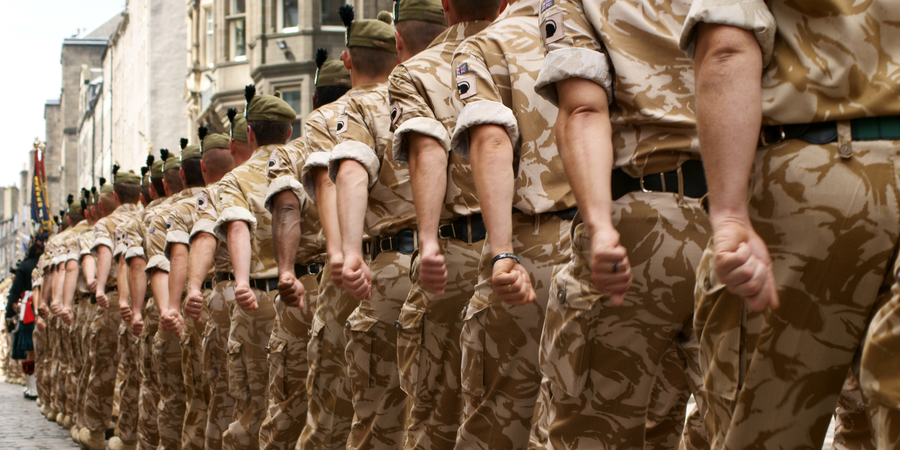
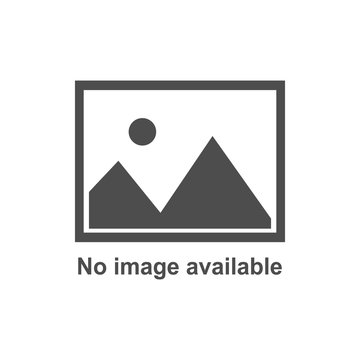
FEATURE – In this in-depth, insightful analysis, the authors explore the essence of bureaucracy and explain why, with Lean Thinking, it can be leveraged as a force for good.
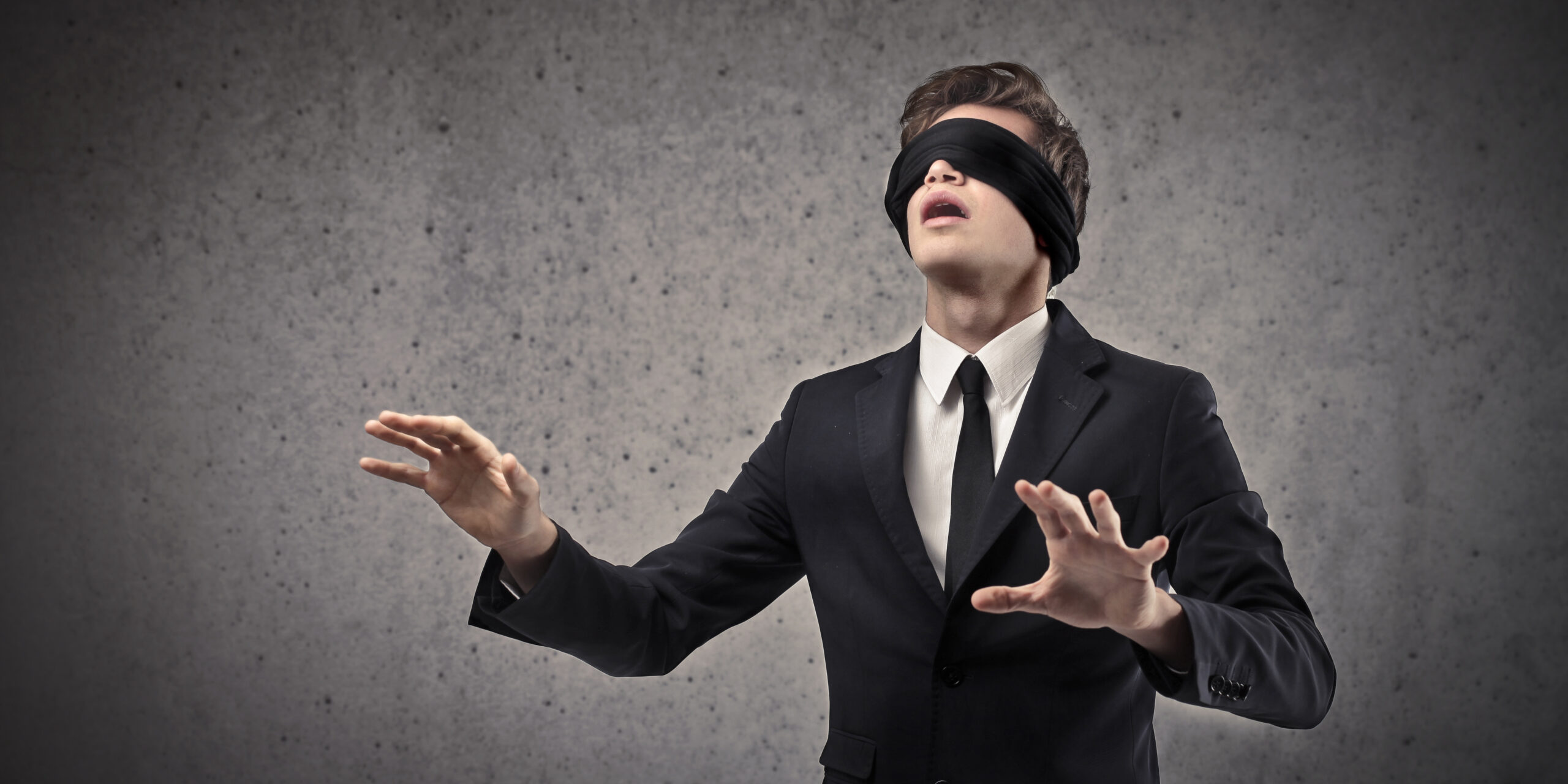
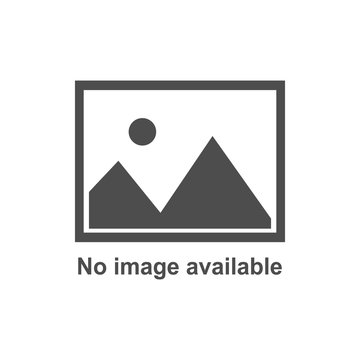
FEATURE - Mental schemas help us to process information, but they often lead us to blindly jump to solutions without understanding the problem. Here, the author explains how Lean Thinking mitigates that risk.
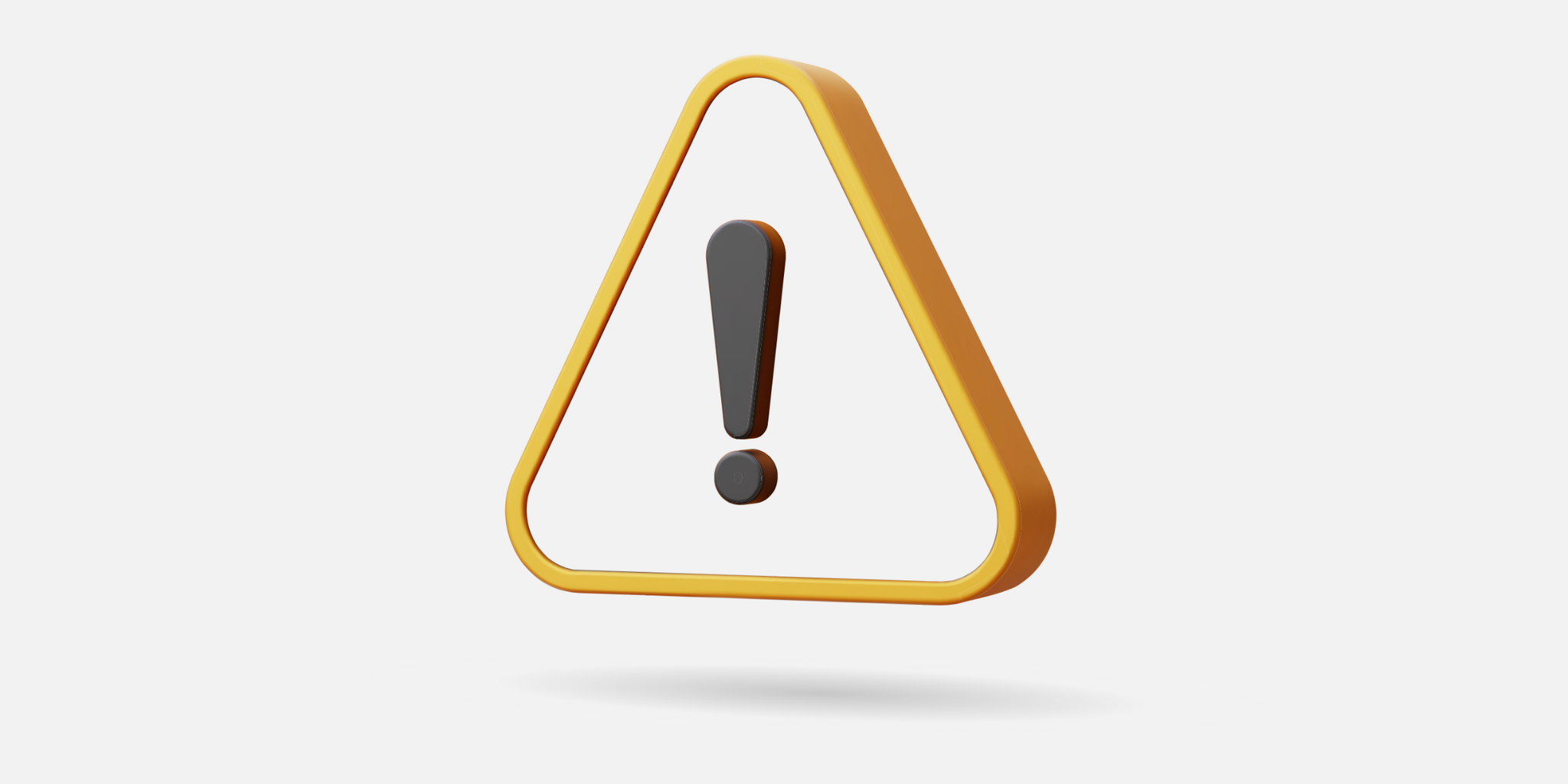
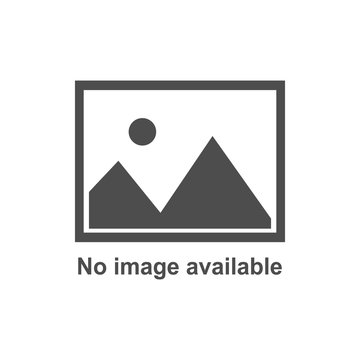
FEATURE – Based on her experience at Lean Institute Colombia, the author lists five common mistakes hindering a lean transformation. Take note!
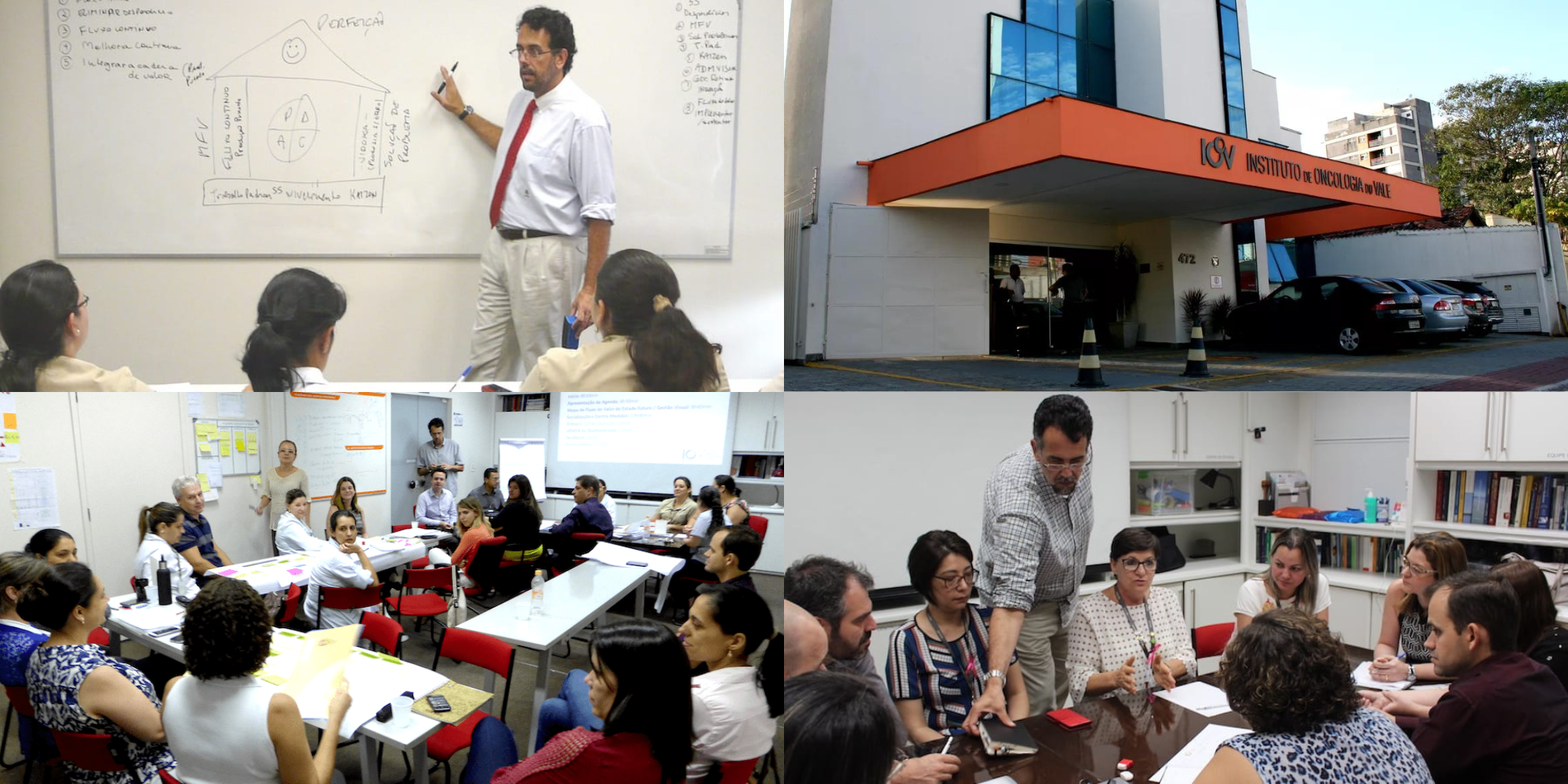
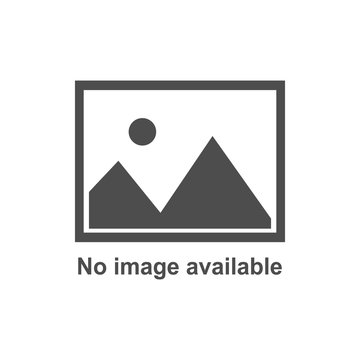
FEATURE – PL readers will likely be familiar with IOV, the cancer clinic in Brazil that’s become a reference for lean healthcare for countless organizations. Here, Dr Fred looks back at IOV’s 15-year journey.
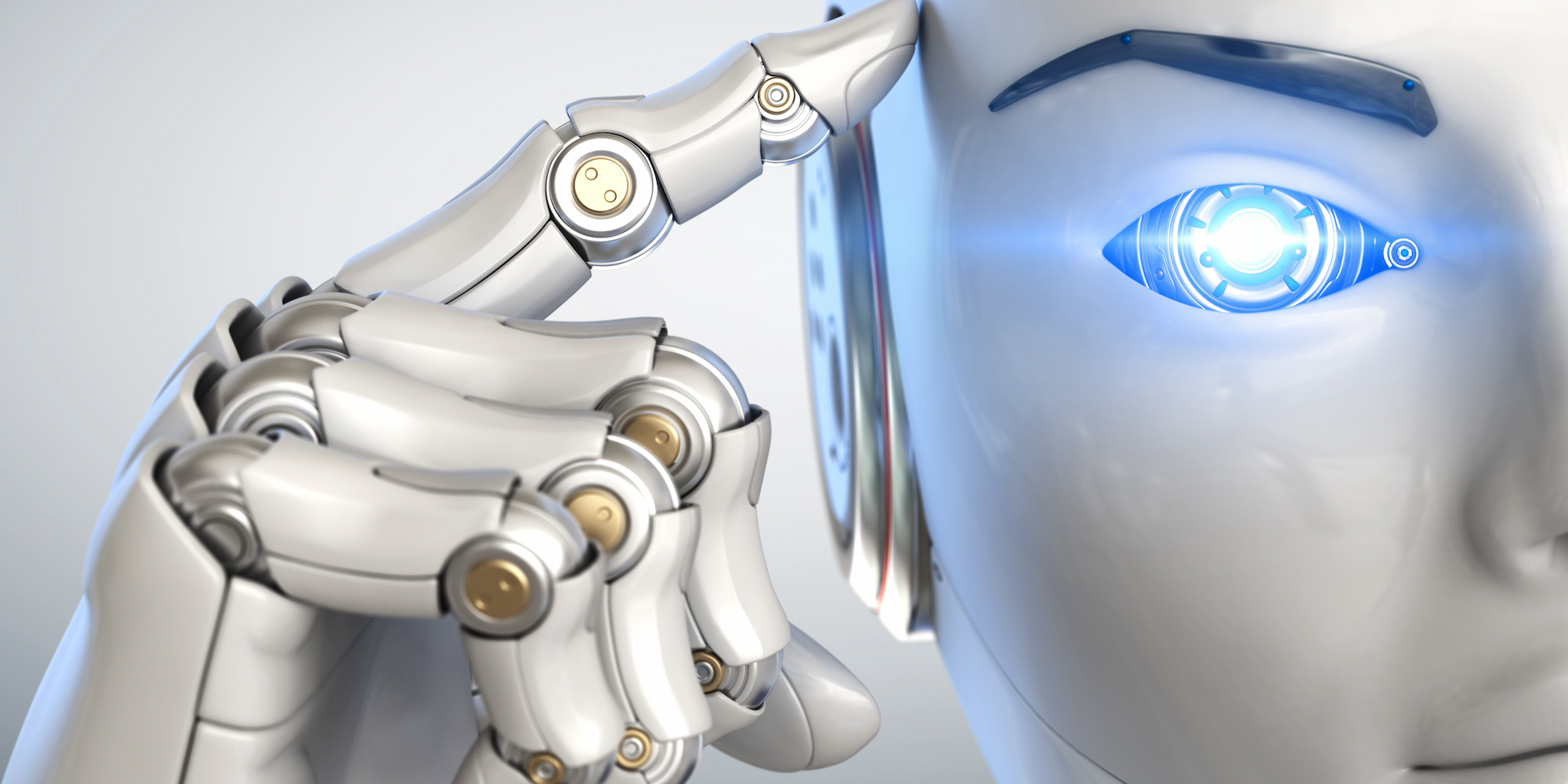
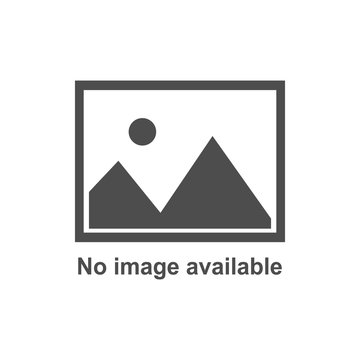
FEATURE – This year, PL will try to understand what the future of work looks like in a world with AI. To kick us off and make us think, we publish an article that is the result of a one-hour conversation between a human and a machine.
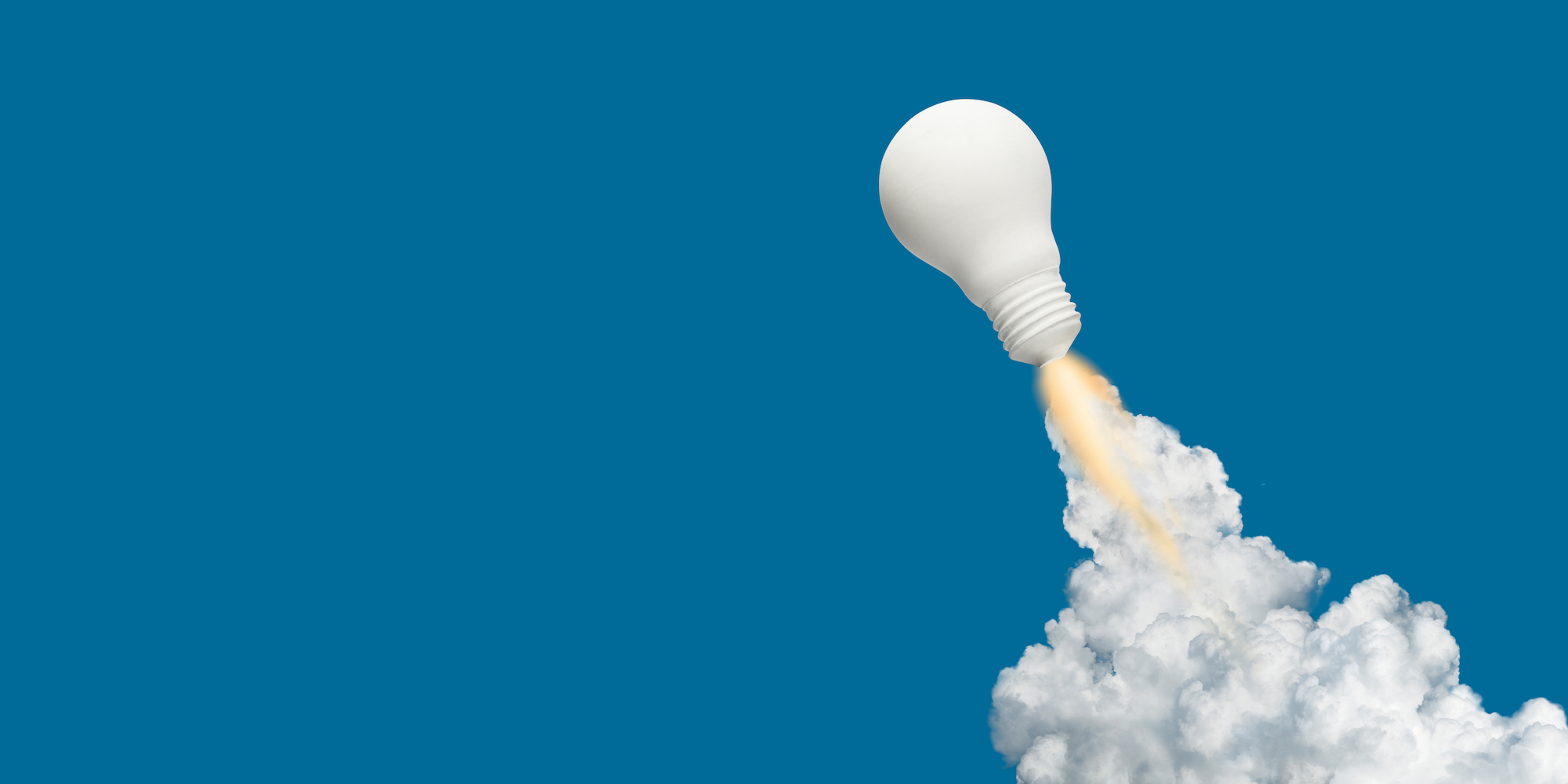
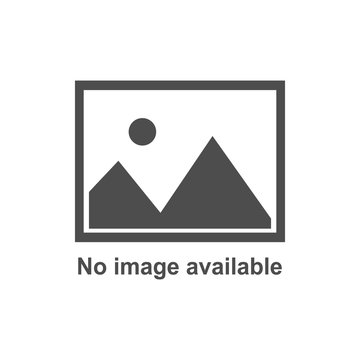
FEATURE – A lean coach from Argentina reflects on the transformations he has supported across Latin America and on why lean can help unlock the potential of the continent.
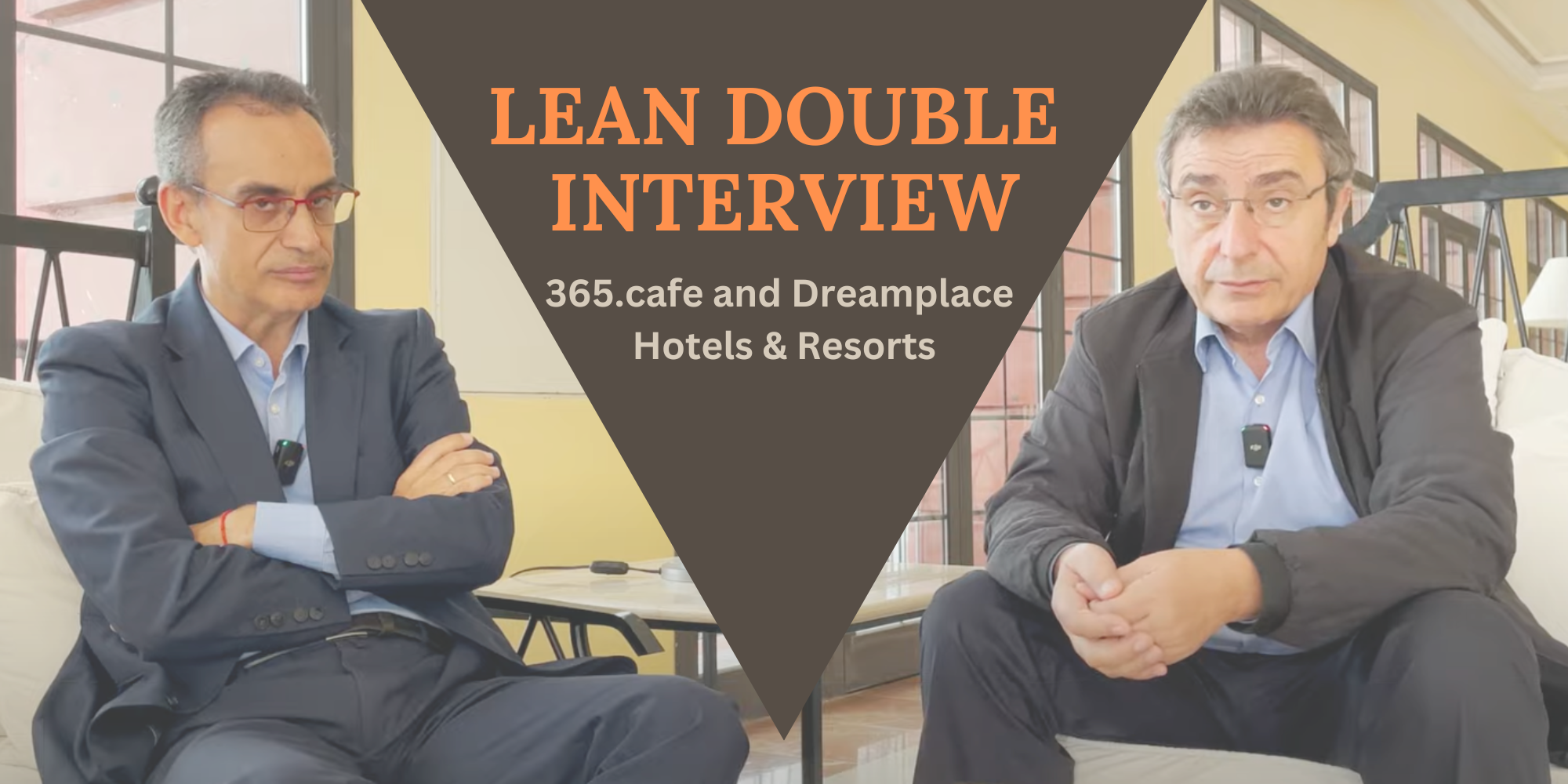
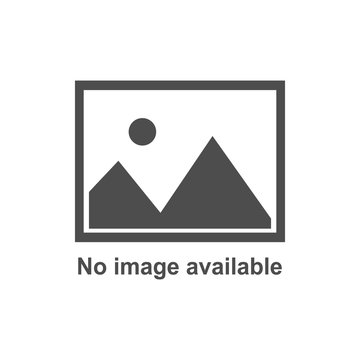
INTERVIEW – Earlier this month, we attended a Lean Day at Dreamplace Hotels and Resorts in the Canary Islands. We sat down with two lean leaders to discuss the transformations of their businesses.
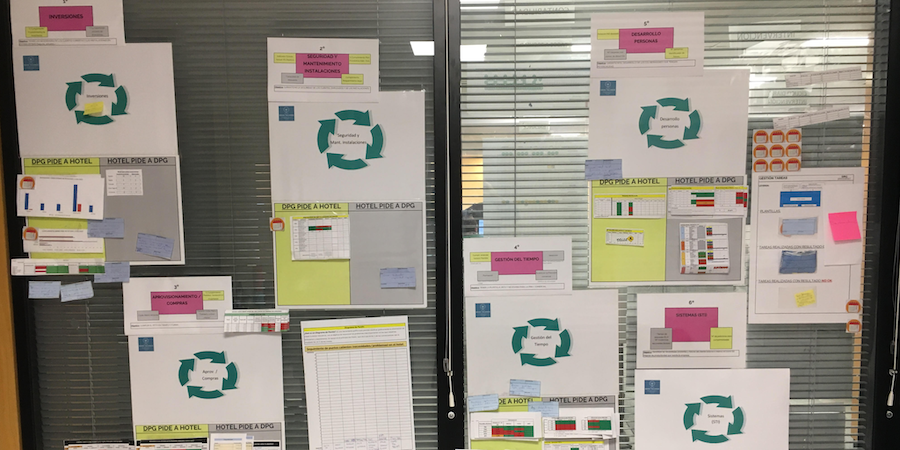
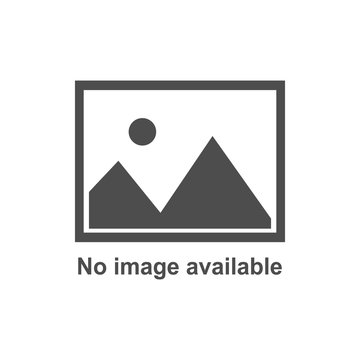
FEATURE – A senior executive of a Spanish hotel chain shares an example of how the organization’s management system and visual tools have changed over time.
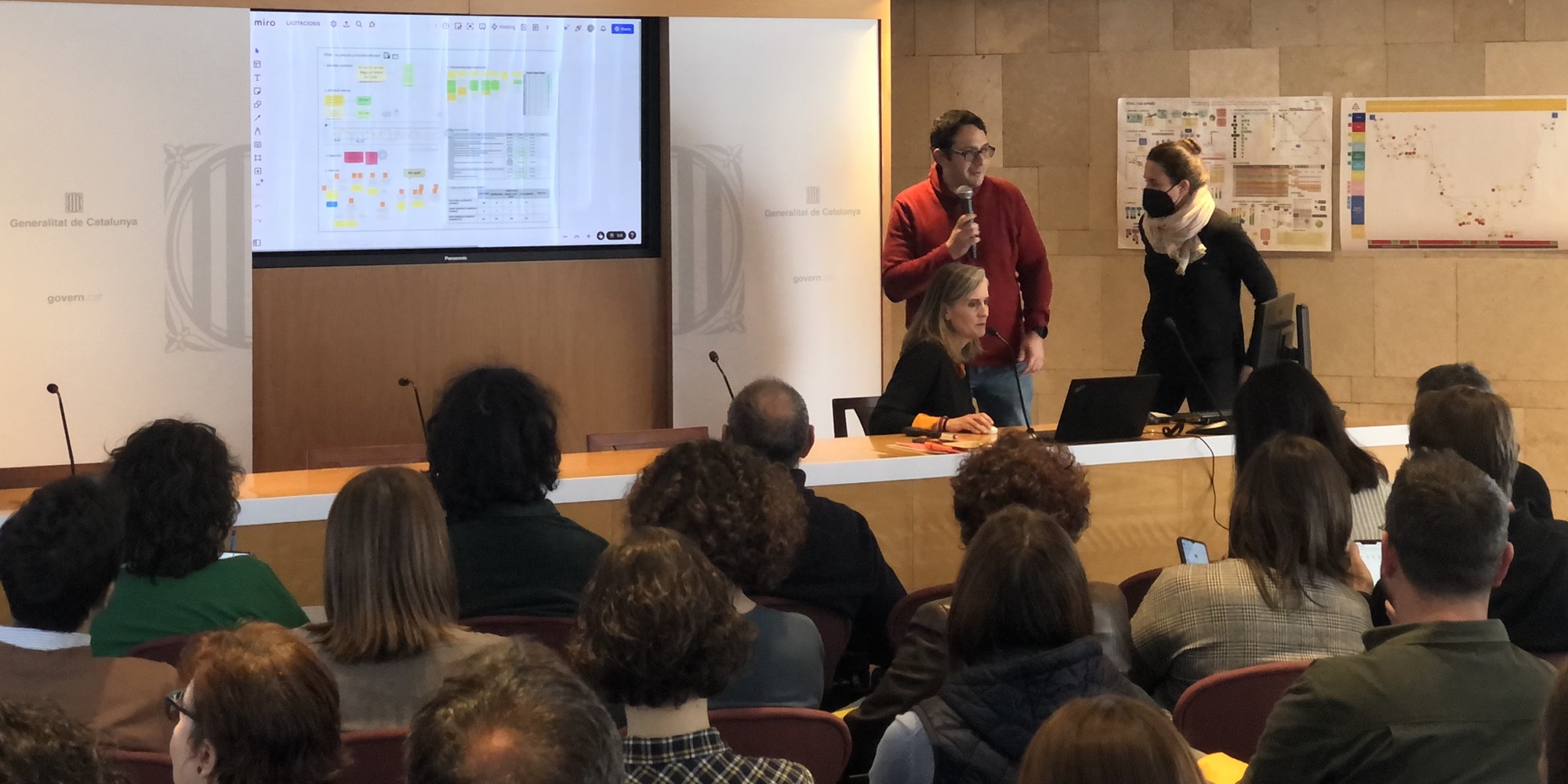
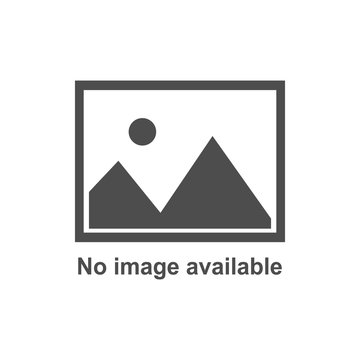
FEATURE – At a recent Lean Day, our editor was reminded of the immense potential of Lean Thinking applied to government. After a few sleepy years, is lean in the public administration having a comeback?

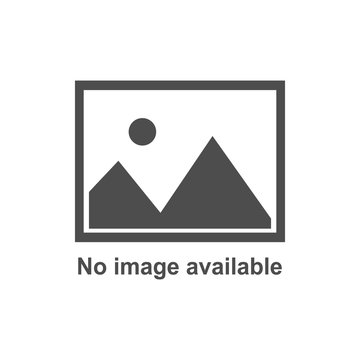
BOOK EXCERPT – The city of Breda in the Netherlands has been on a lean journey for the past six years. Today we share an excerpt from the book The Lean Government, which sets the scene for the transformation.
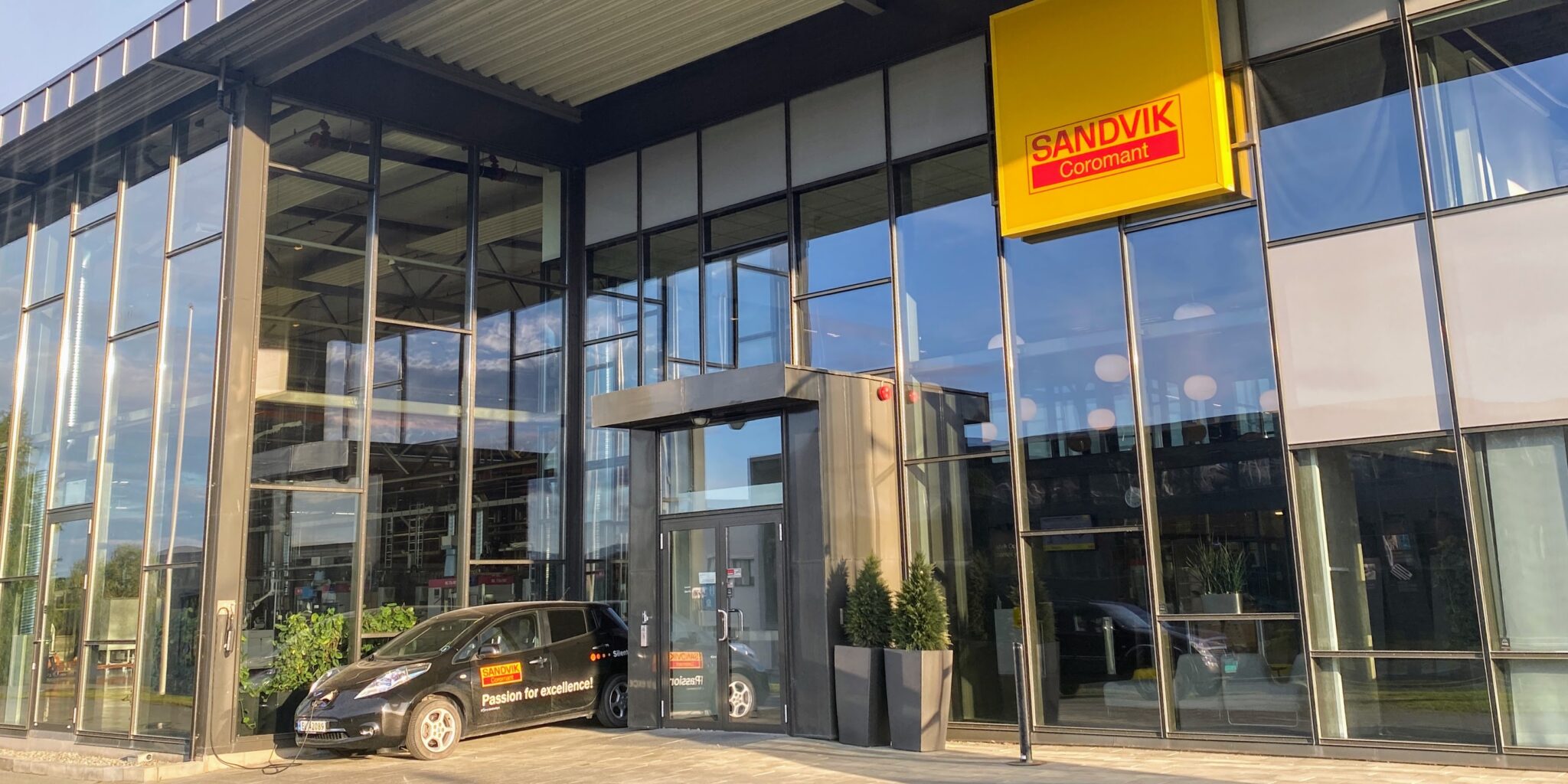
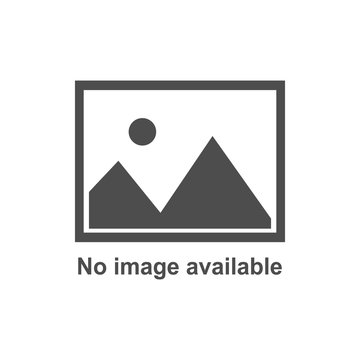
CASE STUDY – A people-centric approach to work, improvement, and the adoption of automation is allowing this Norwegian company to thrive in a changing industry and environment.
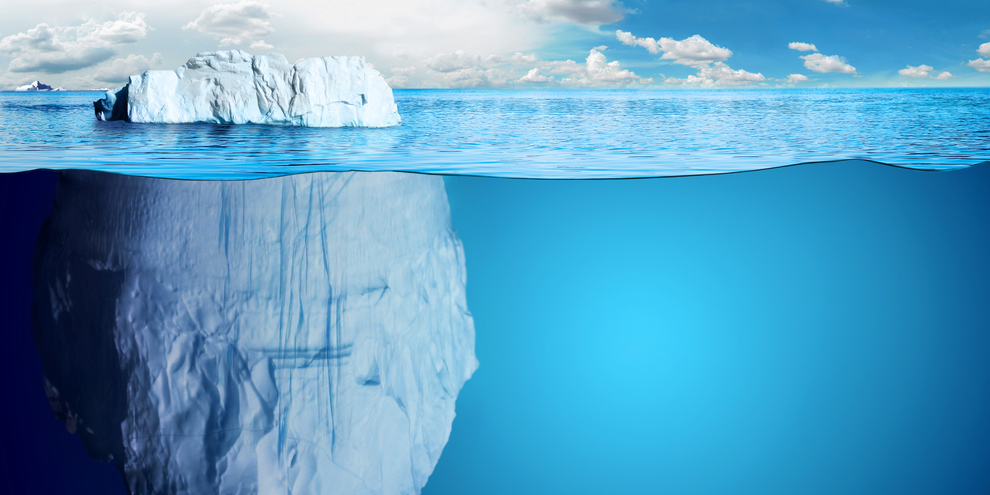
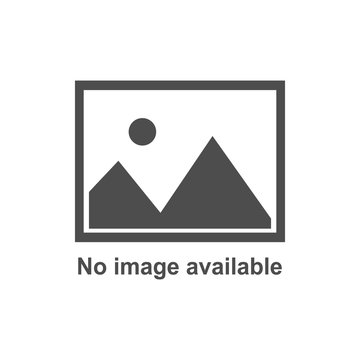
FEATURE – A real understanding of Lean Thinking can only stem from an exploration of its tacit aspects, not just its most explicit, easy-to-grasp elements.
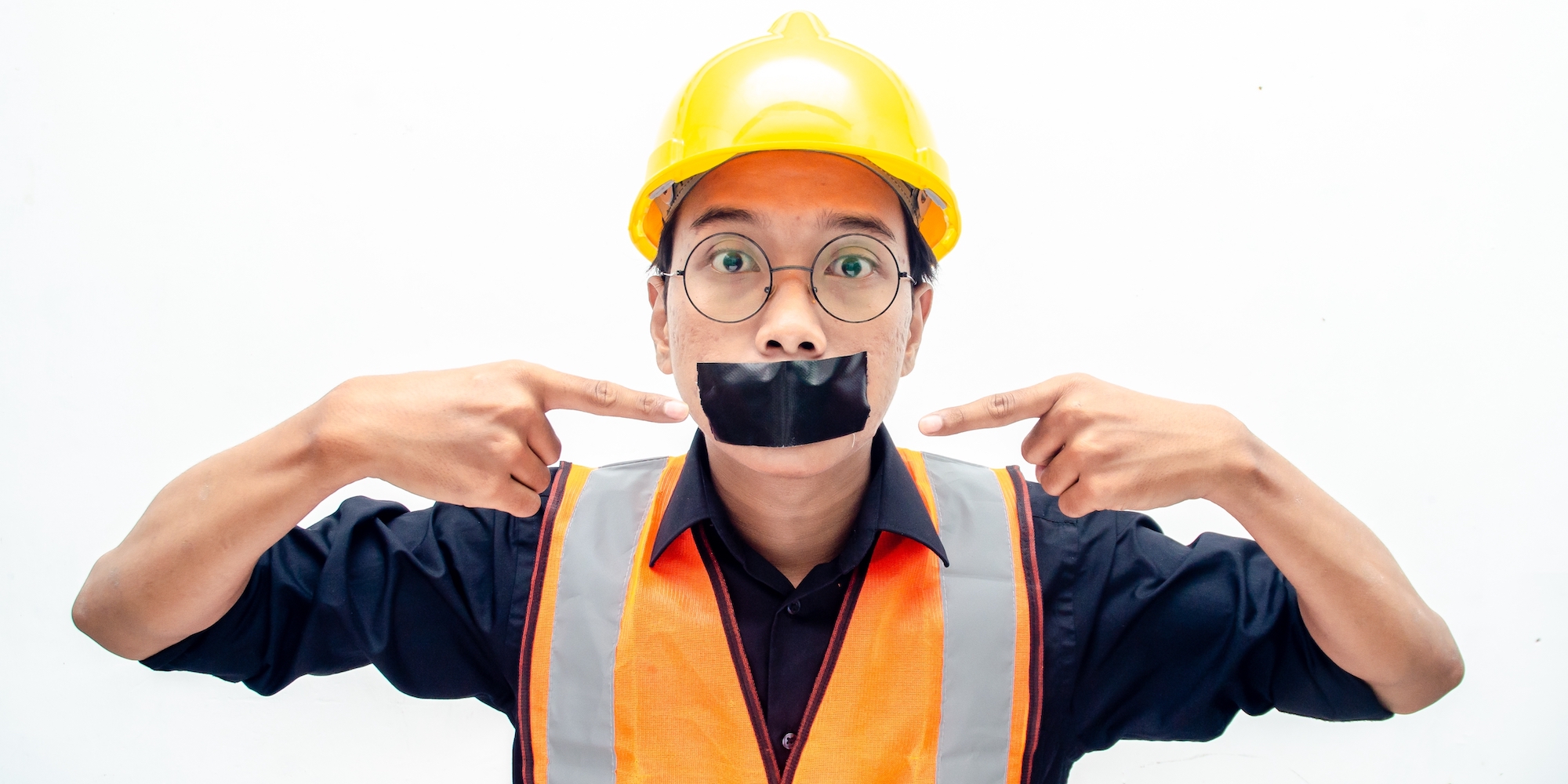
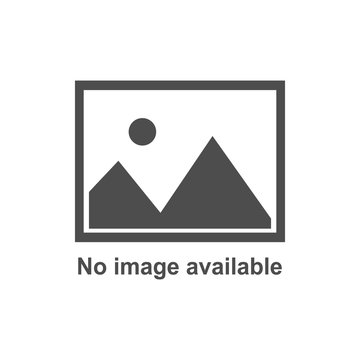
FEATURE – By changing its attitude towards problems and welcoming them as opportunities to learn, this Colombian construction company has turned around its culture.
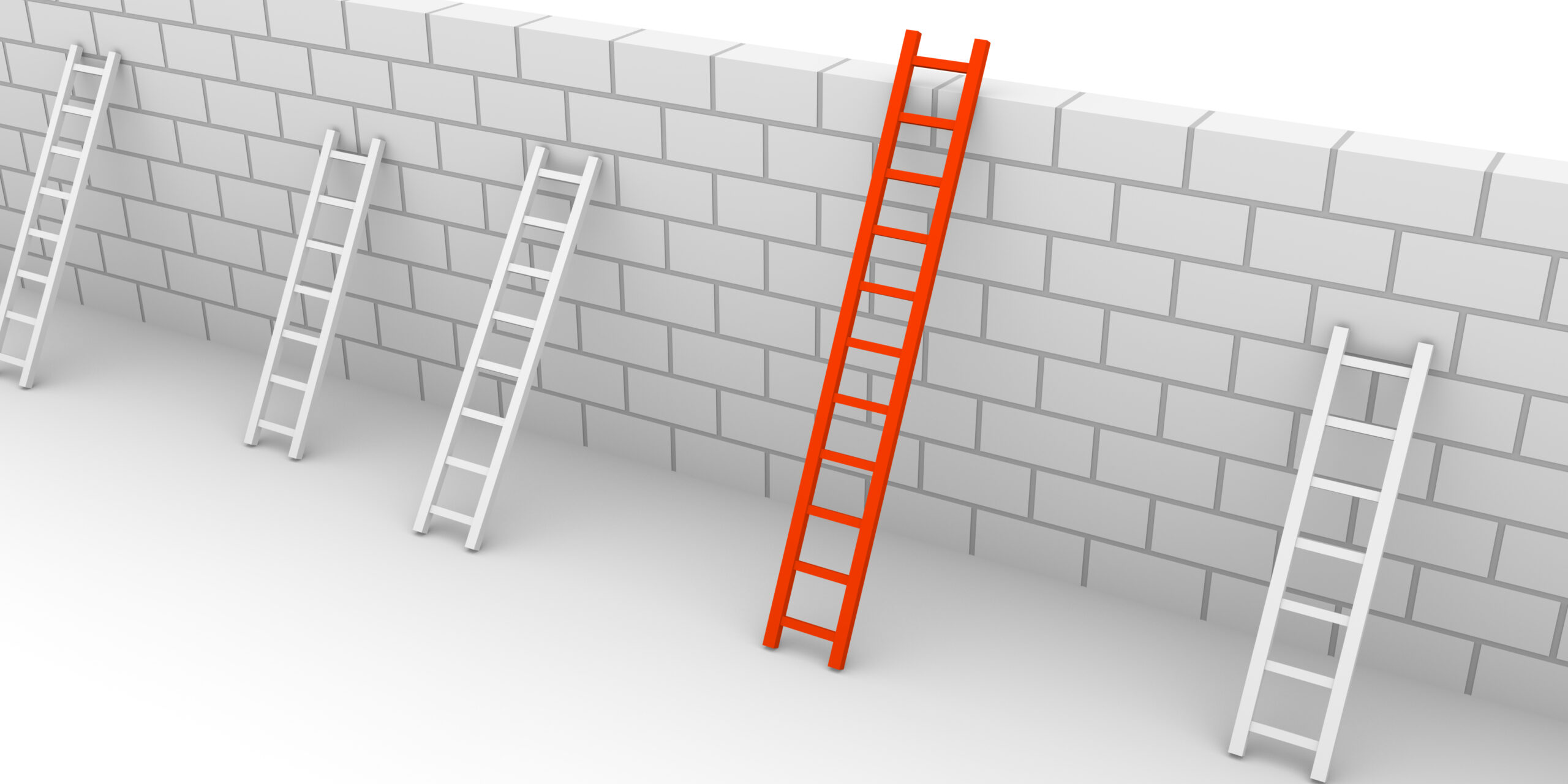
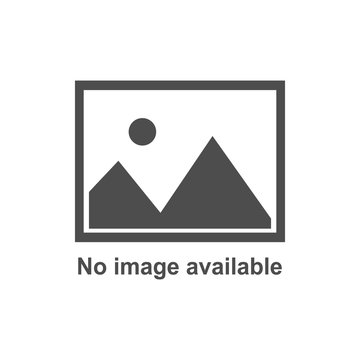
FEATURE – Leading by solving problems is a key trait of any lean leader, but it is important to understand that not all problems are their prerogative.
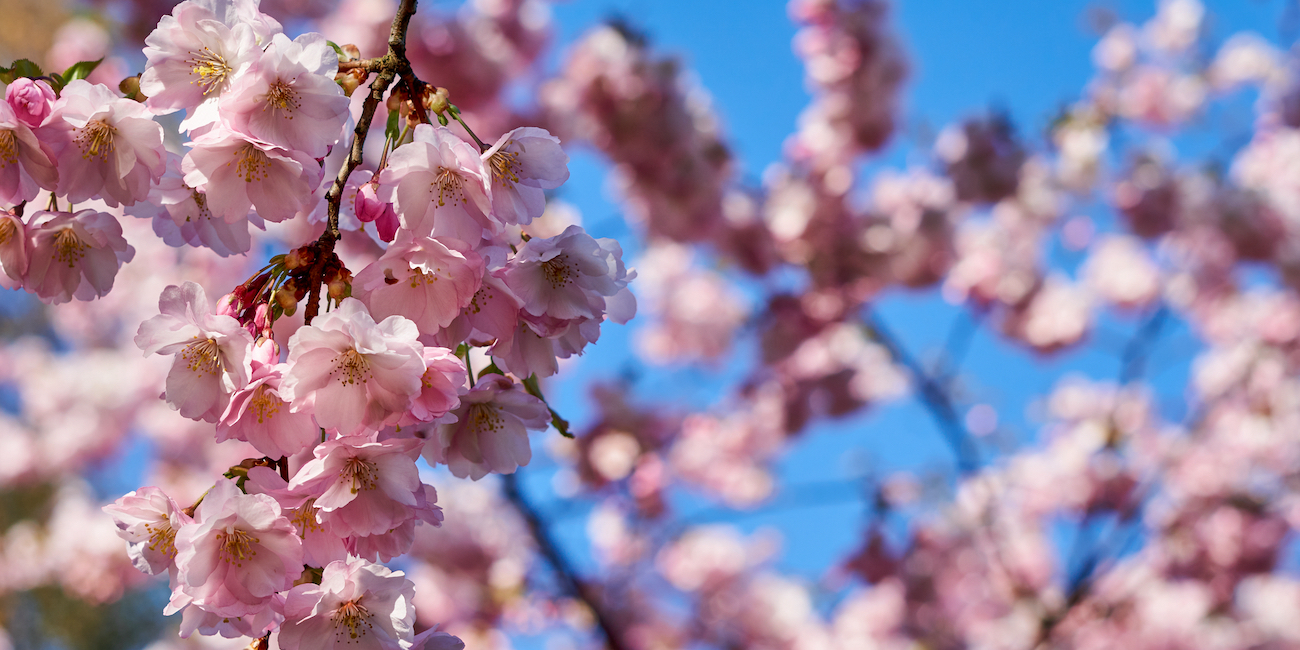
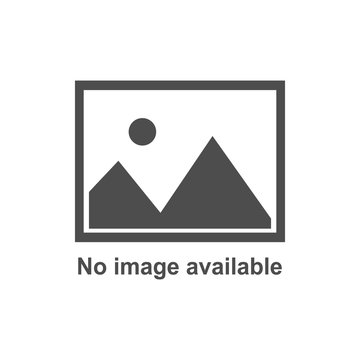
FEATURE – Visuals are a natural way in which human beings learn and teach. The author discusses why visual thinking is part of our DNA and the implications this has on our lives at work.
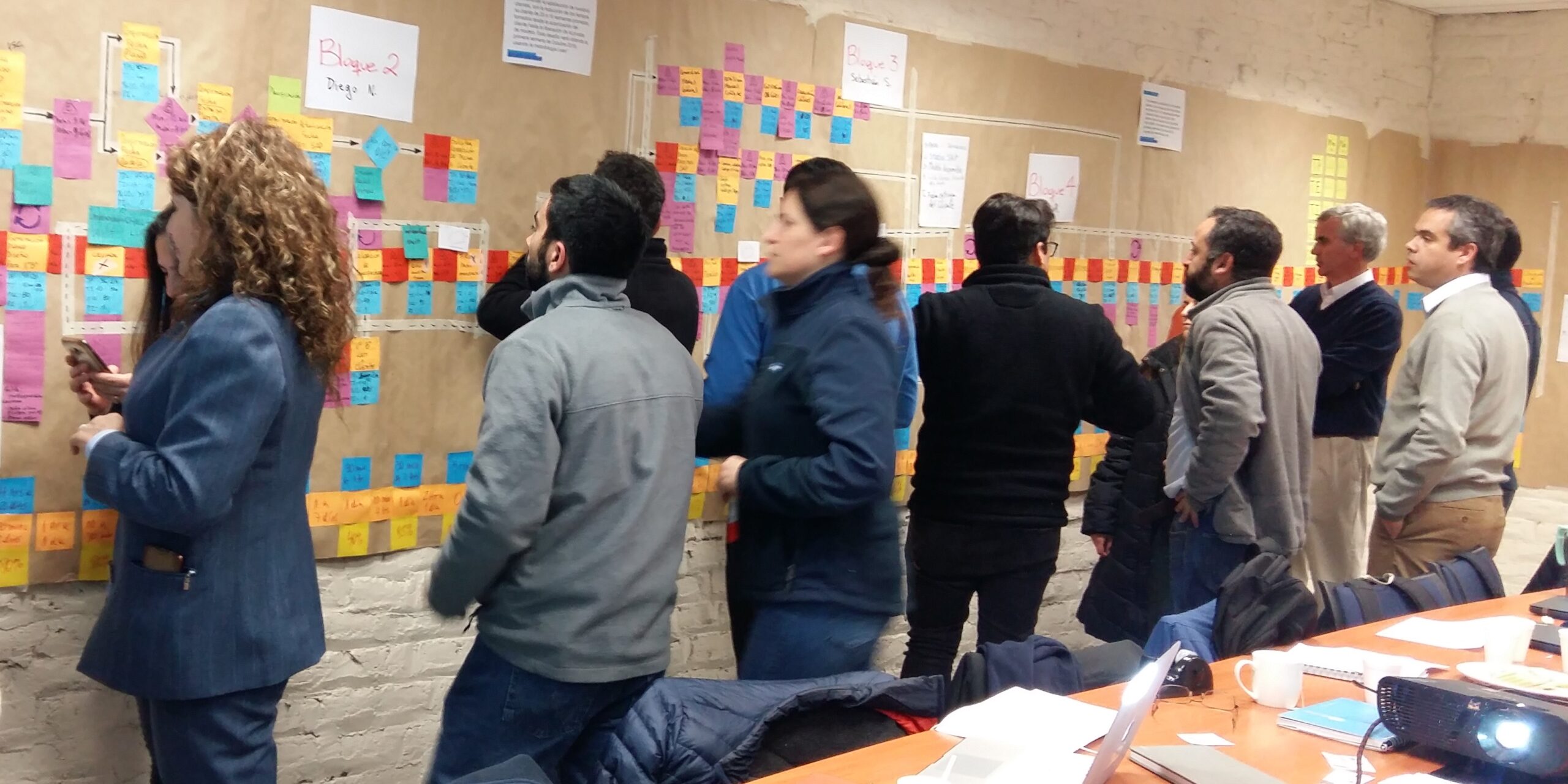
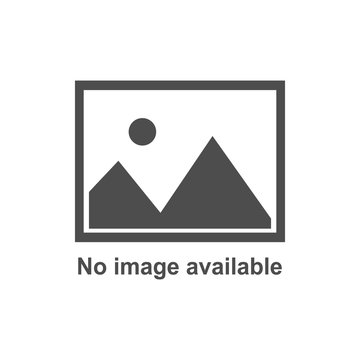
INTERVIEW – Top leaders at Chilean company Elecmetal talk to us about how lean has transformed their role in the organization and how capability development is fuelling change.
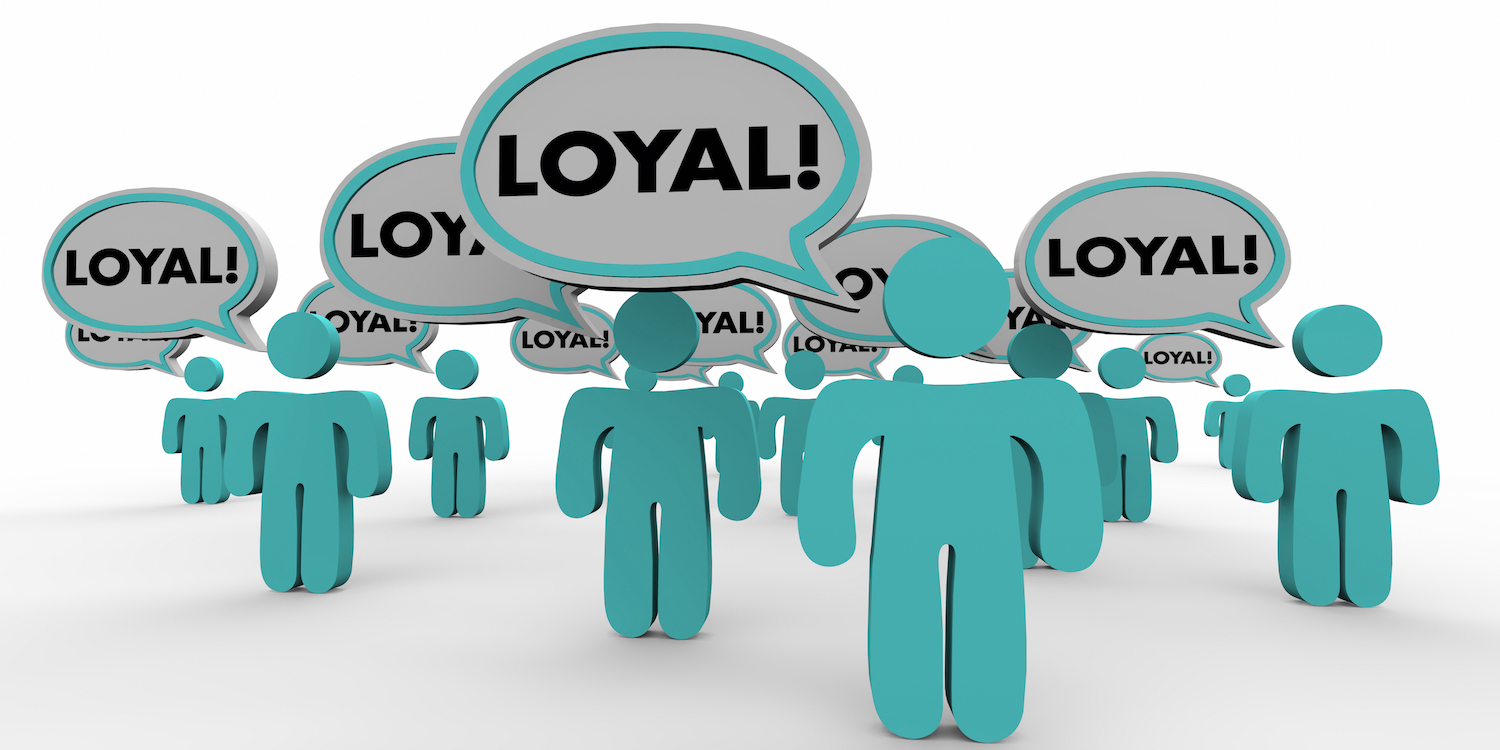
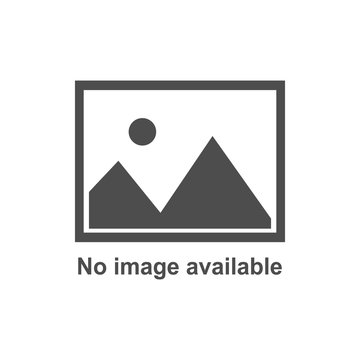
FEATURE – We start the new year with a reminder to put customers first, always. It is they who make our business and keep our lean initiatives true, says the author.
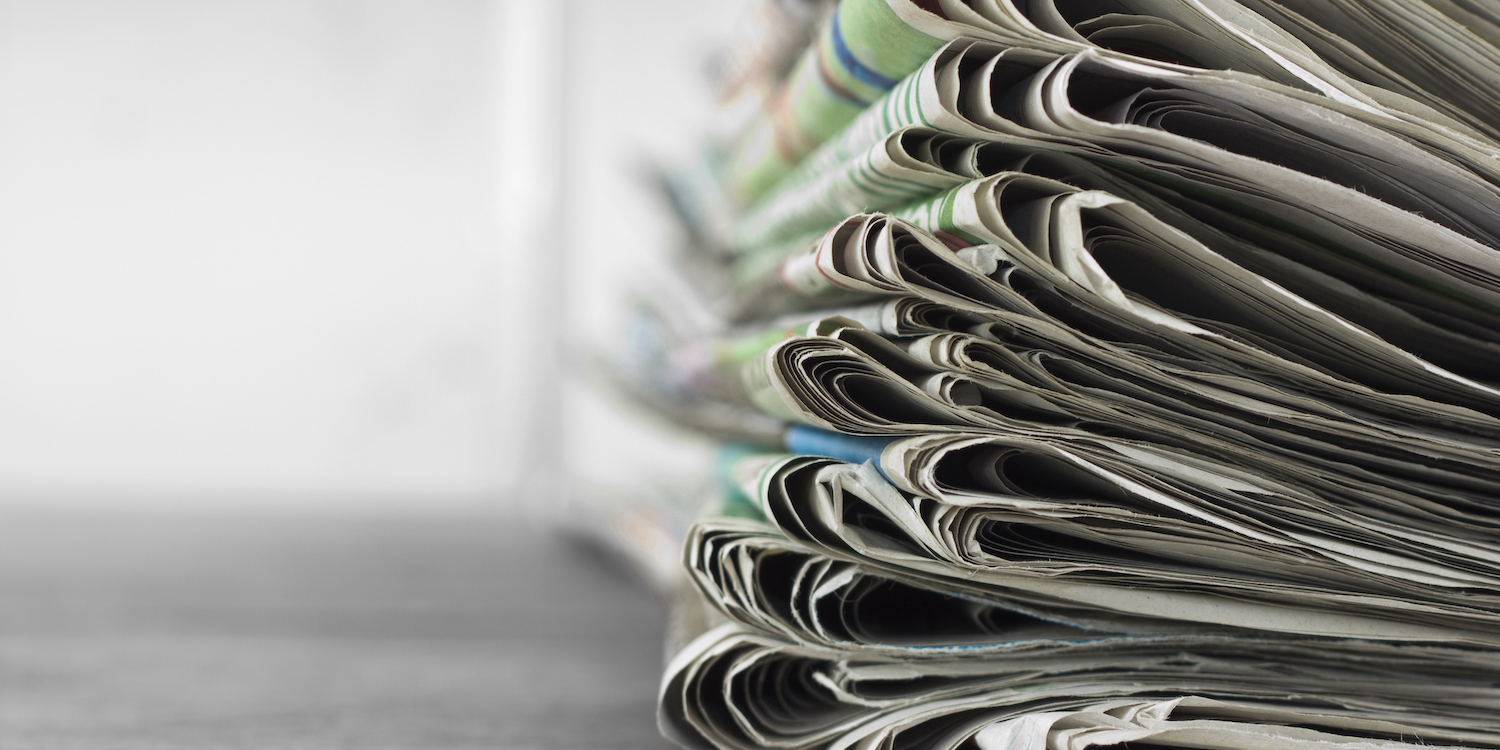
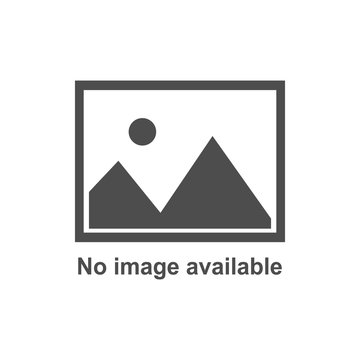
ROUND-UP – In his annual review of the best content we published, our editor looks back at 2022 and what this year was like for the Lean Community.
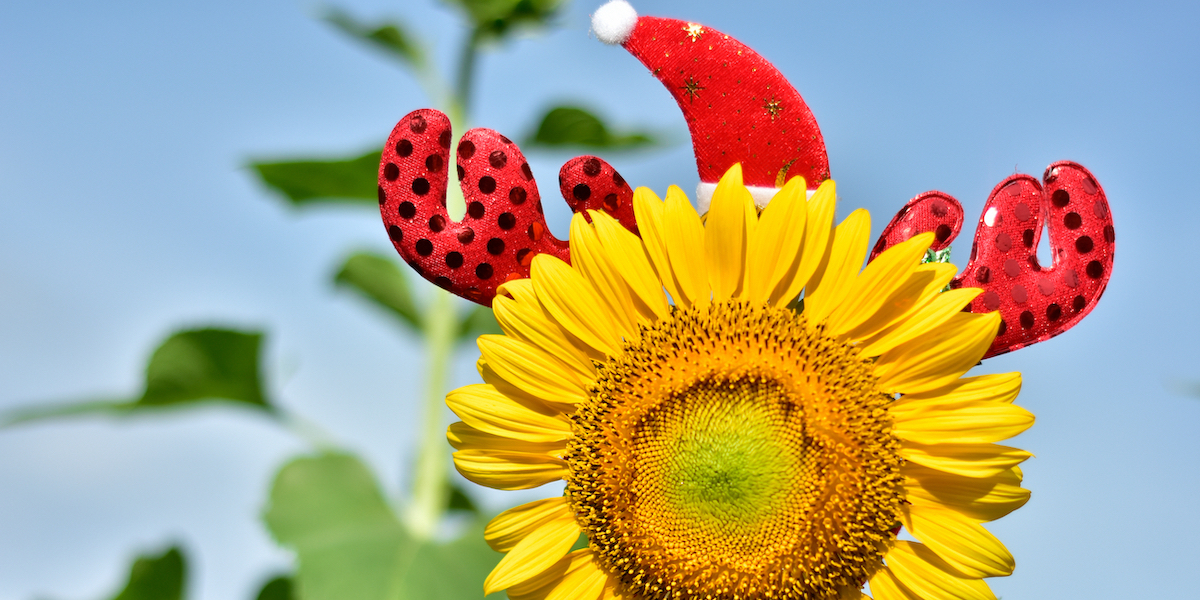
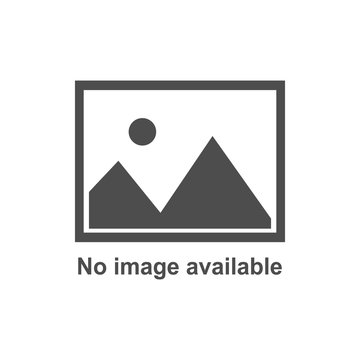
FICTION – Santa is struggling to locate the many children who are hiding from war to deliver them gifts, until the lean Time Benders come to the rescue and help him understand the problem.

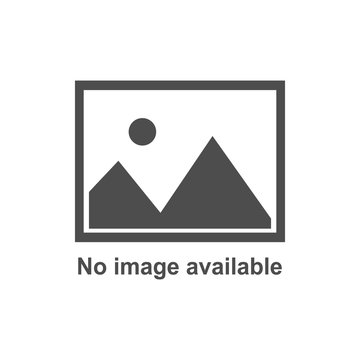
FEATURE – This nurses-led experiment in Barcelona’s Hospital Clinic is proving successful in getting more patients discharged on time and avoiding surgery cancellations.
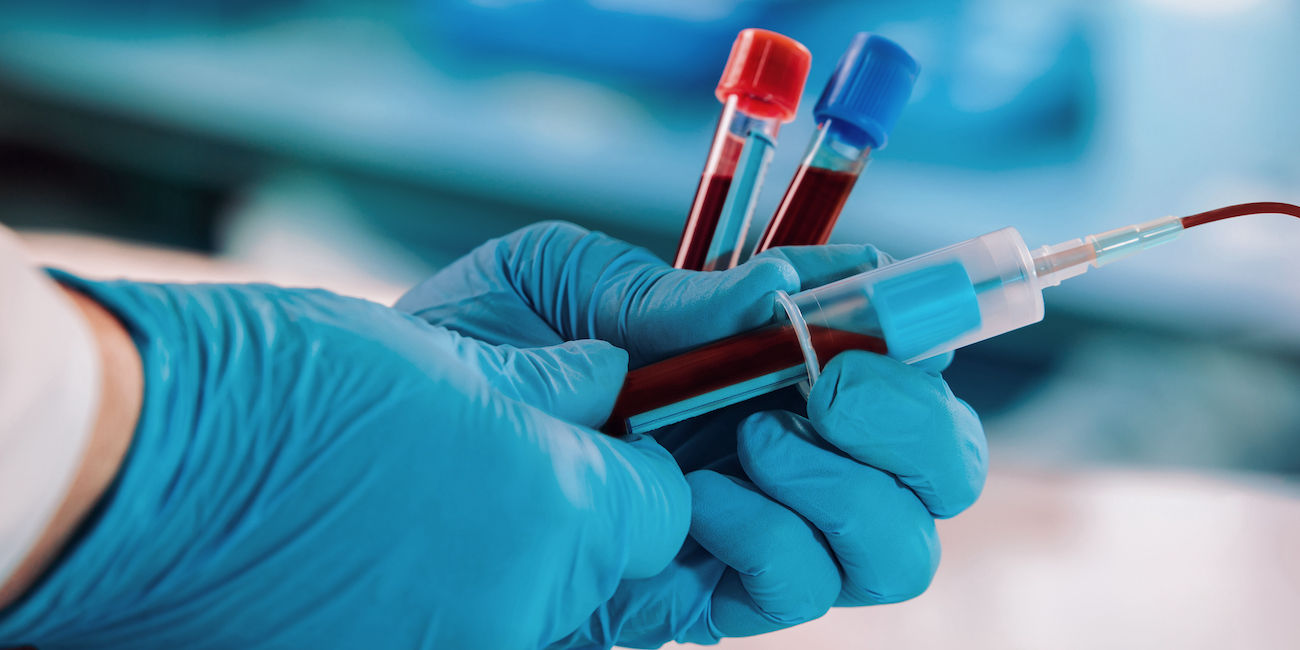
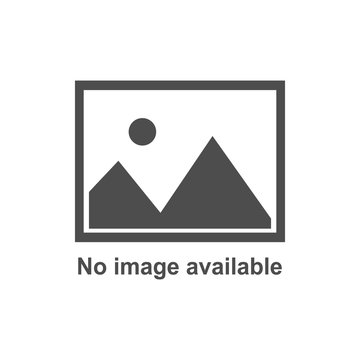
FEATURE – Thanks to lean, a primary care unit in Catalonia has streamlined its blood sampling process, improving the patient experience and the life at work for its staff.
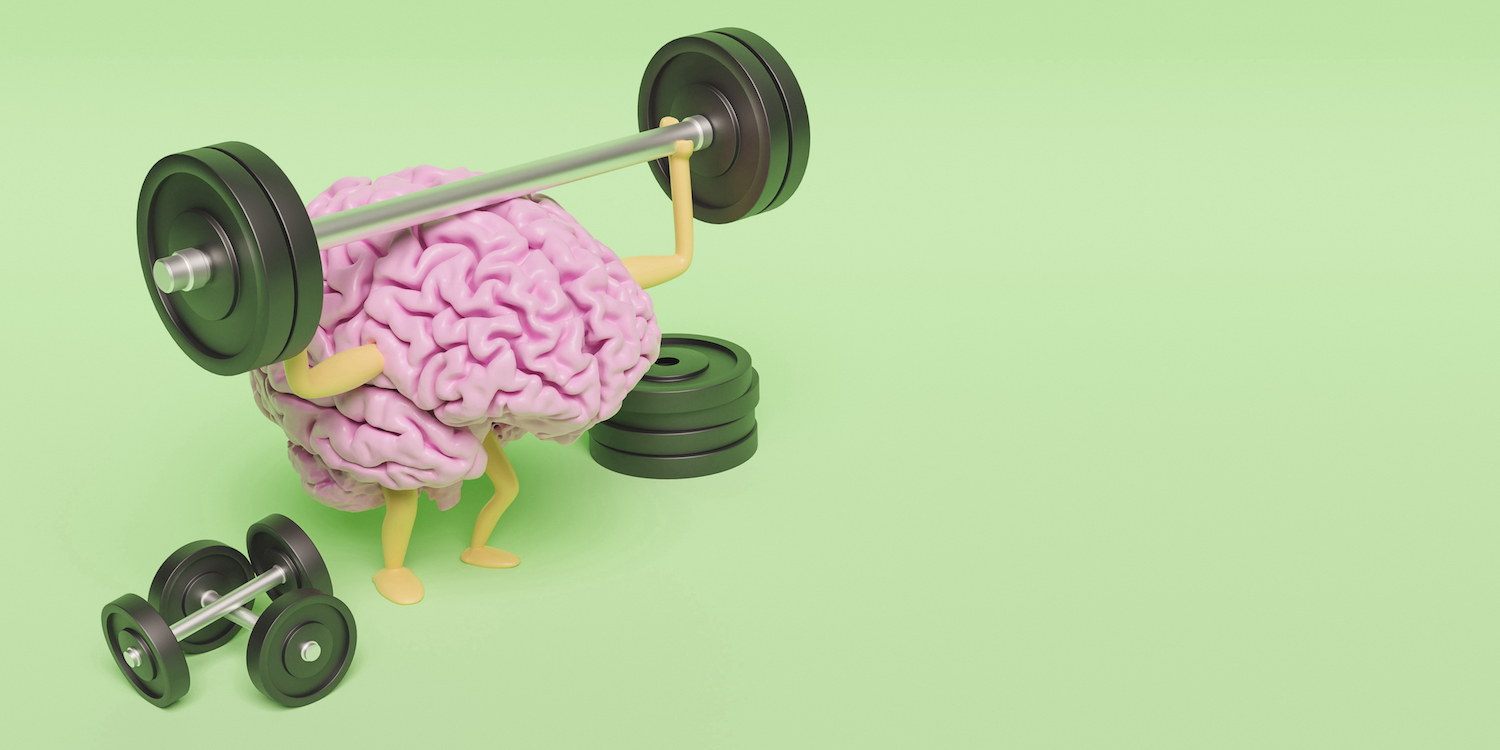
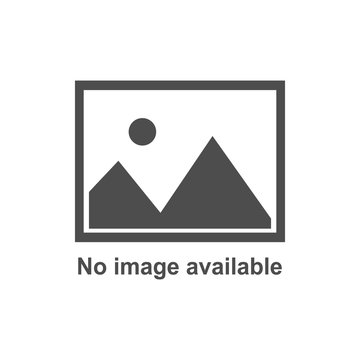
FEATURE – In this interesting piece, the author explains how lean provided everyone, everywhere with a framework to work their intuition muscle and develop insights.
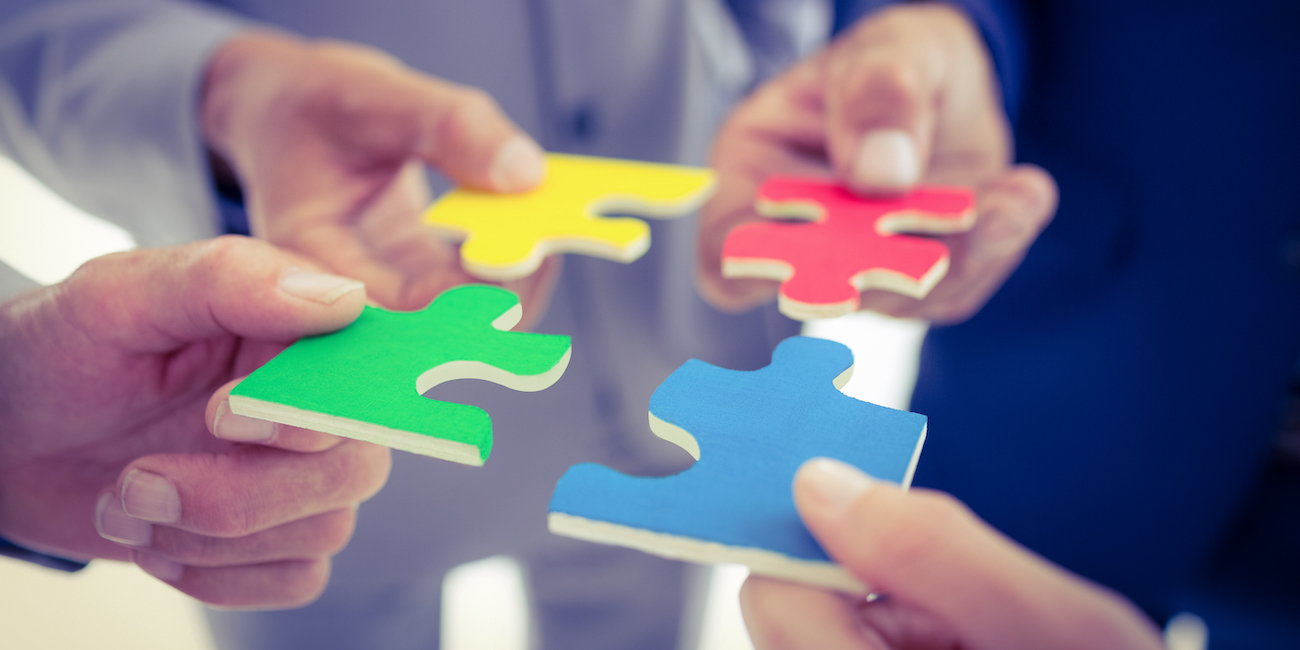
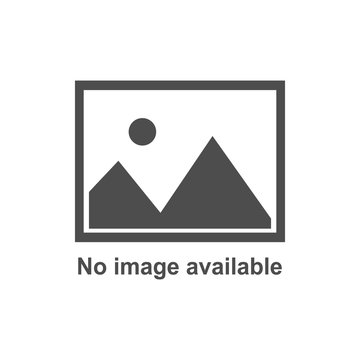
FEATURE – In an excerpt from his new book, the author discusses the importance of building collaboration in your teams and explains why this is the only way to consistently deliver value.
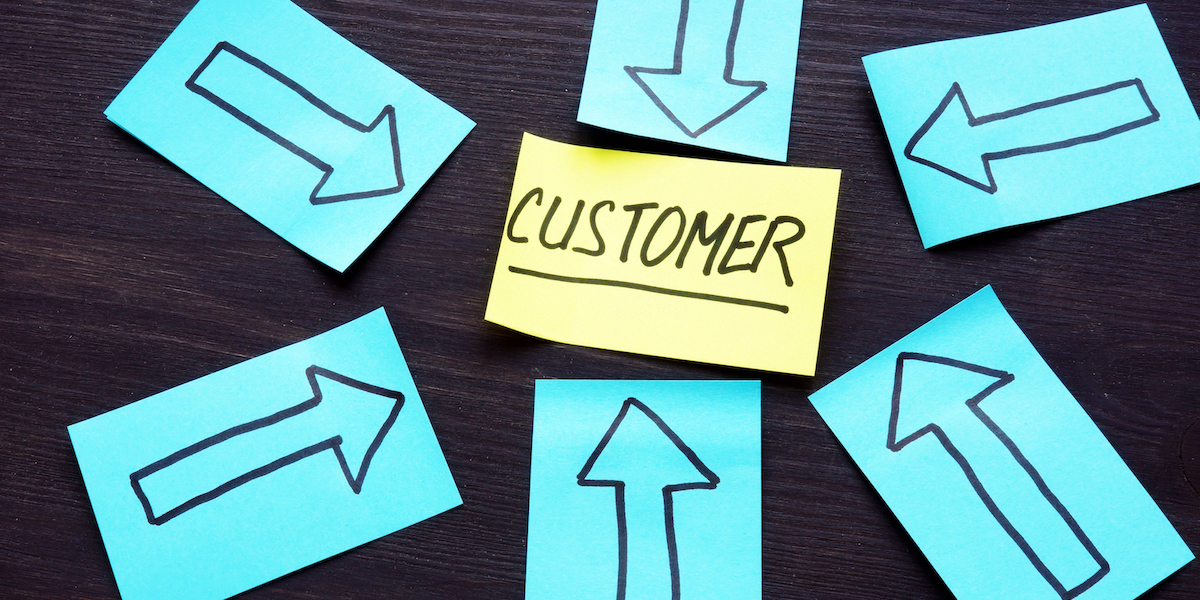
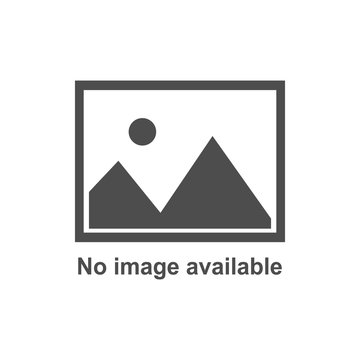
CASE STUDY – This Shared Service Center in Poland has leveraged lean, technology, and automation to completely transform itself and provide an ever-better customer experience.
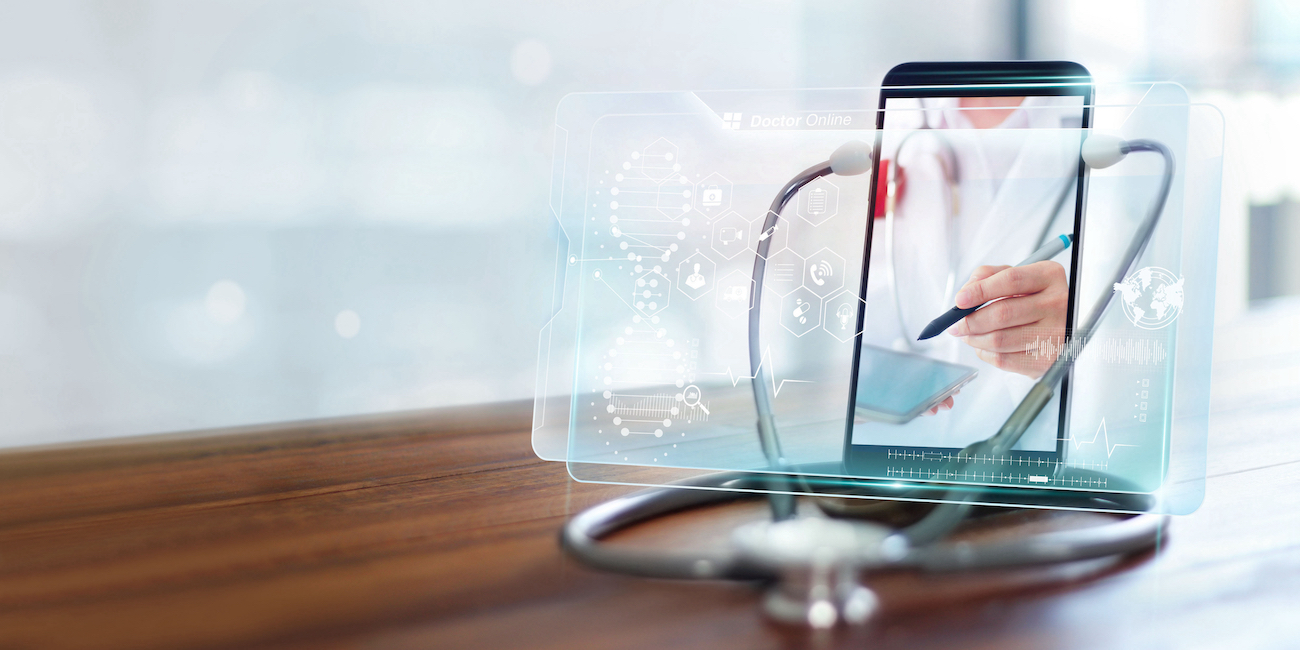
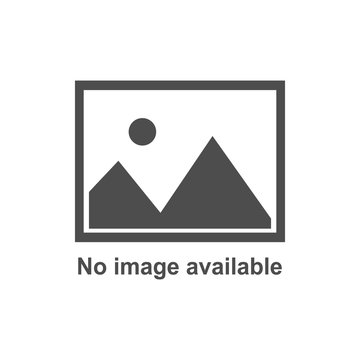
CASE STUDY – The Covid-19 pandemic has accelerated the application of Virtual Healthcare across the world. In South Australia, this has been implemented in urgent care.
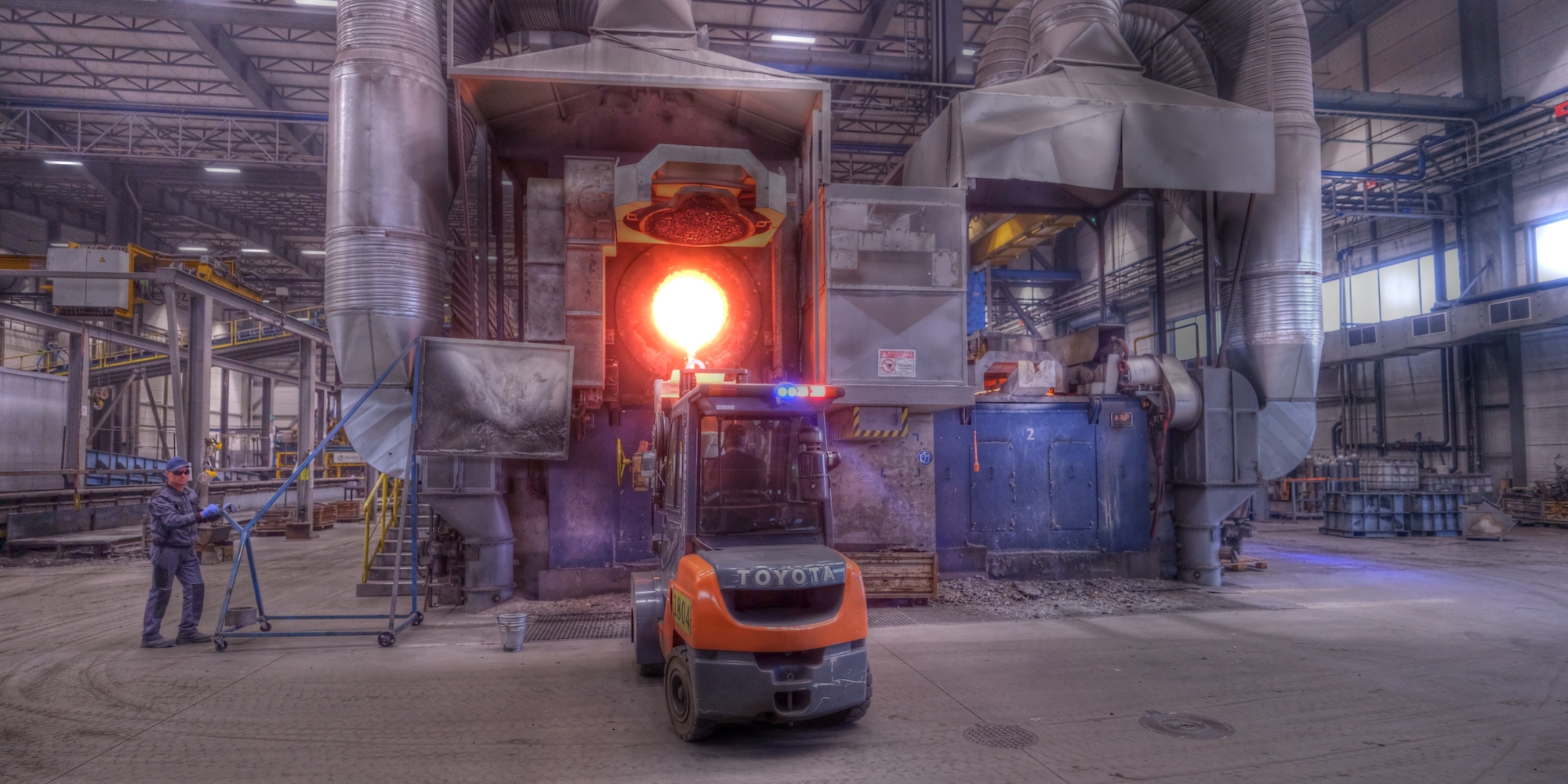
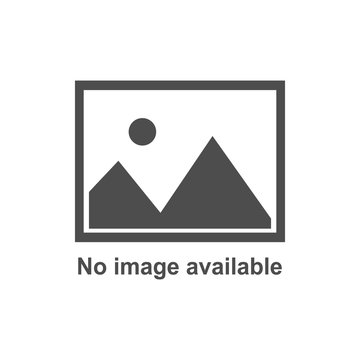
INTERVIEW – Ahead of this week’s Lean Global Connection, we talk to one of the speakers, who is trying to create a foundry that is lean from the start.
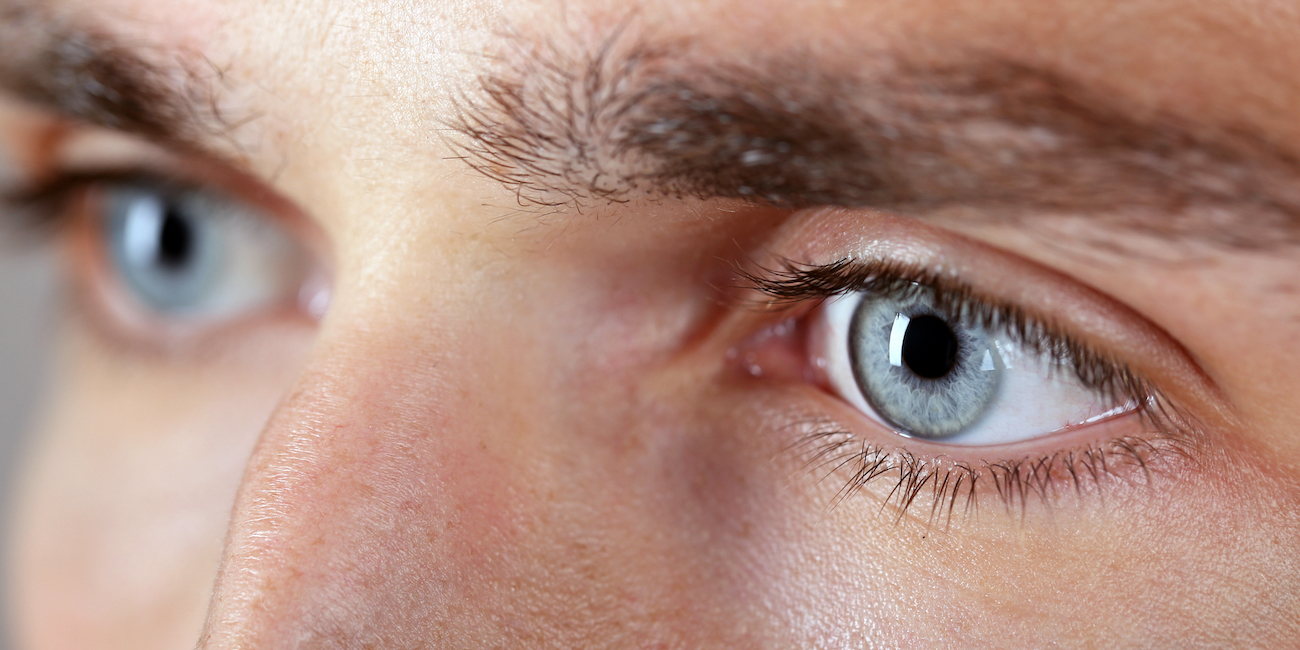
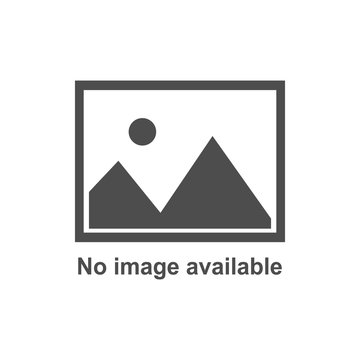
FEATURE – Whether improvement efforts are paying off and people are internalizing a lean way of thinking is a constant worry for many leaders. Here’s a trick to gauge how well – or how poorly – things are going in your transformation.
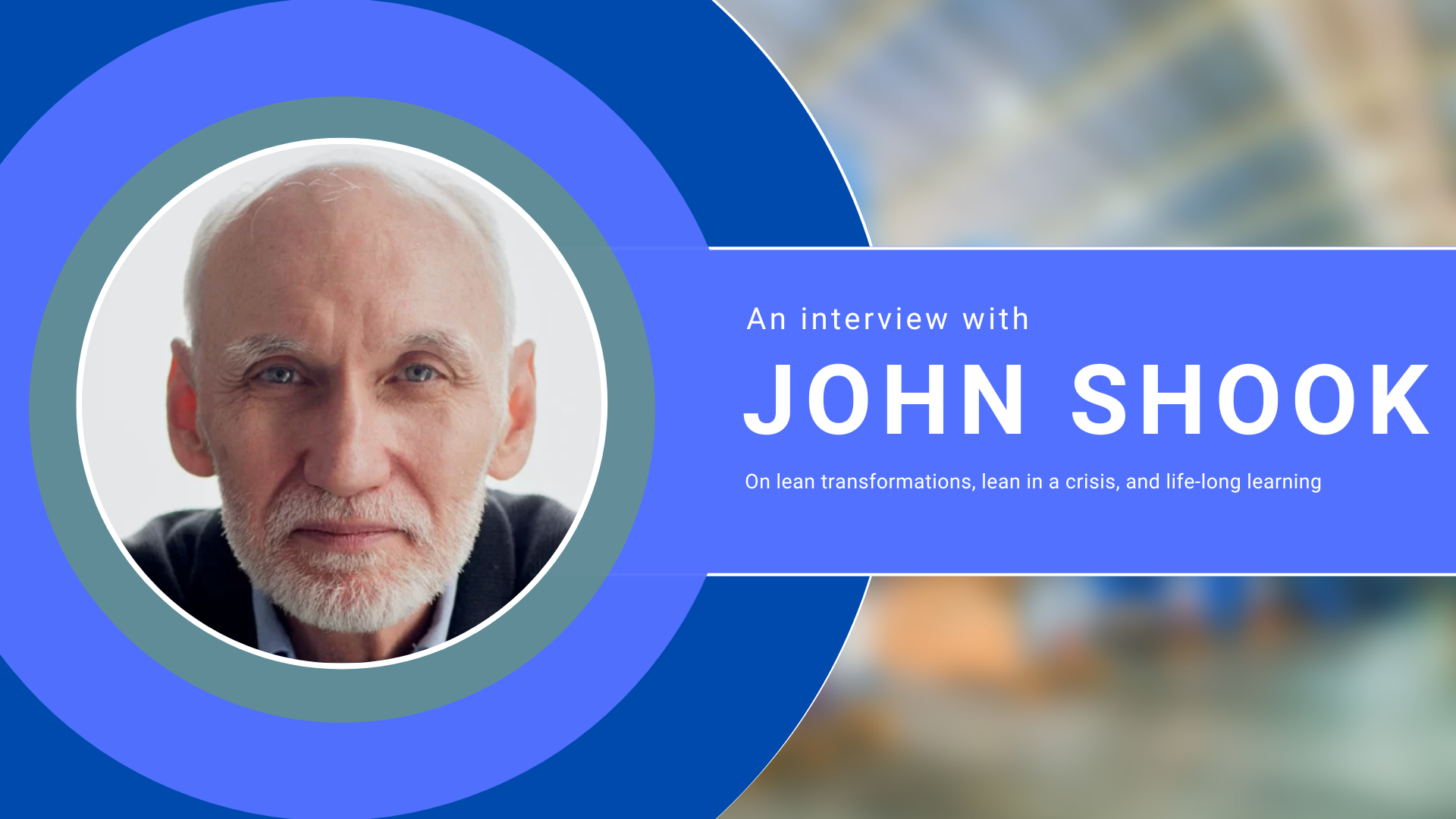
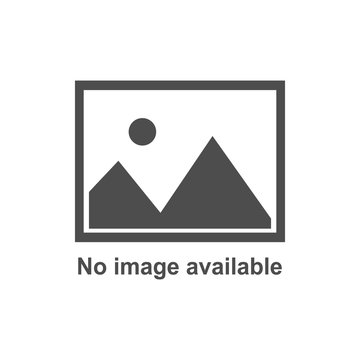
VIDEO INTERVIEW – We recently caught up with John Shook at the Lean Healthcare Academic Conference in Stanford and asked him to share his thought on the questions we need to ask ourselves in a lean journey and on lean in turbulent times.
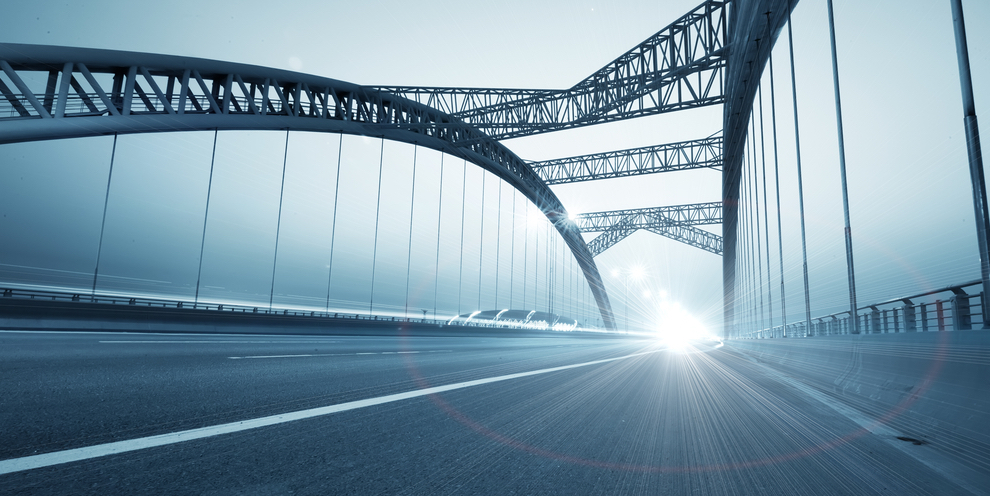
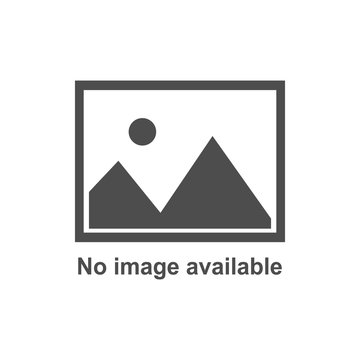
INTERVIEW – This metalworking company based in Poland has leveraged the cultural change brought by Lean Thinking to significantly improve its processes. Ahead of his presentation at the LGC, their lean manager tells us how they did it.
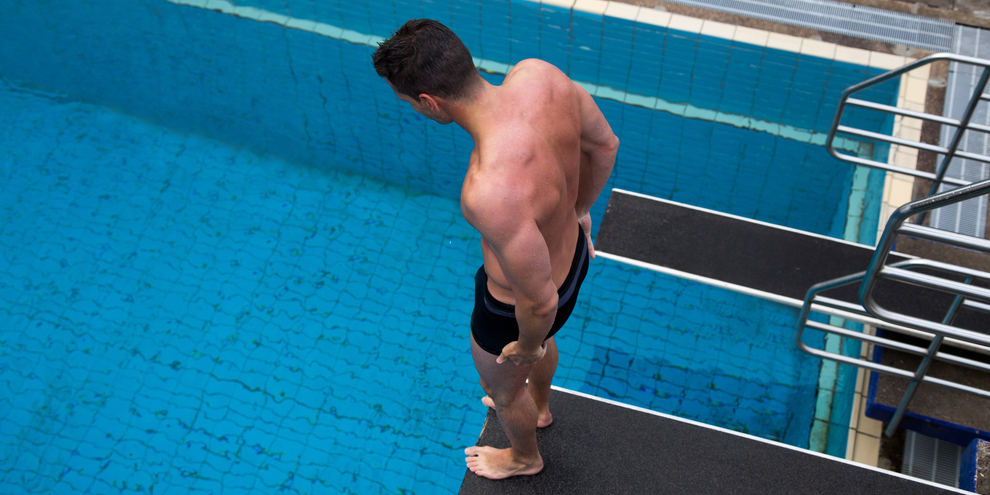
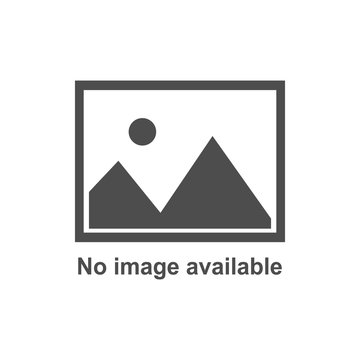
FEATURE – To wholeheartedly embrace lean means to accept changes in our hearts and minds. Understanding this means to finally grasp the reason why lean is only truly taken up by few.
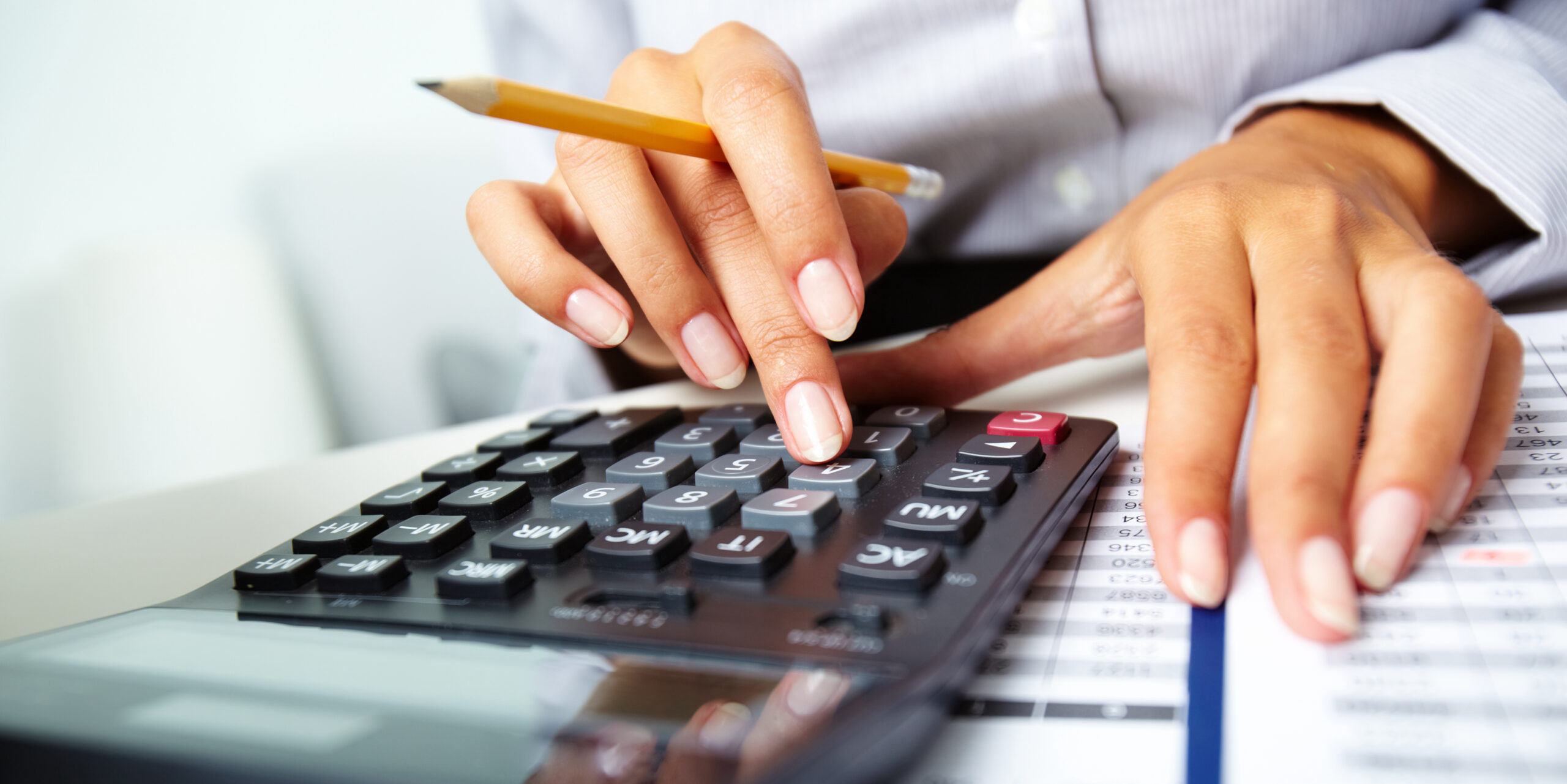
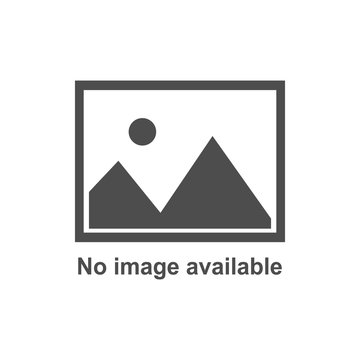
INTERVIEW – General Electric’s Angie Norman talks to our editor about the lean journey of the company’s Finance department and how the area became a driver of GE’s overall transformation.
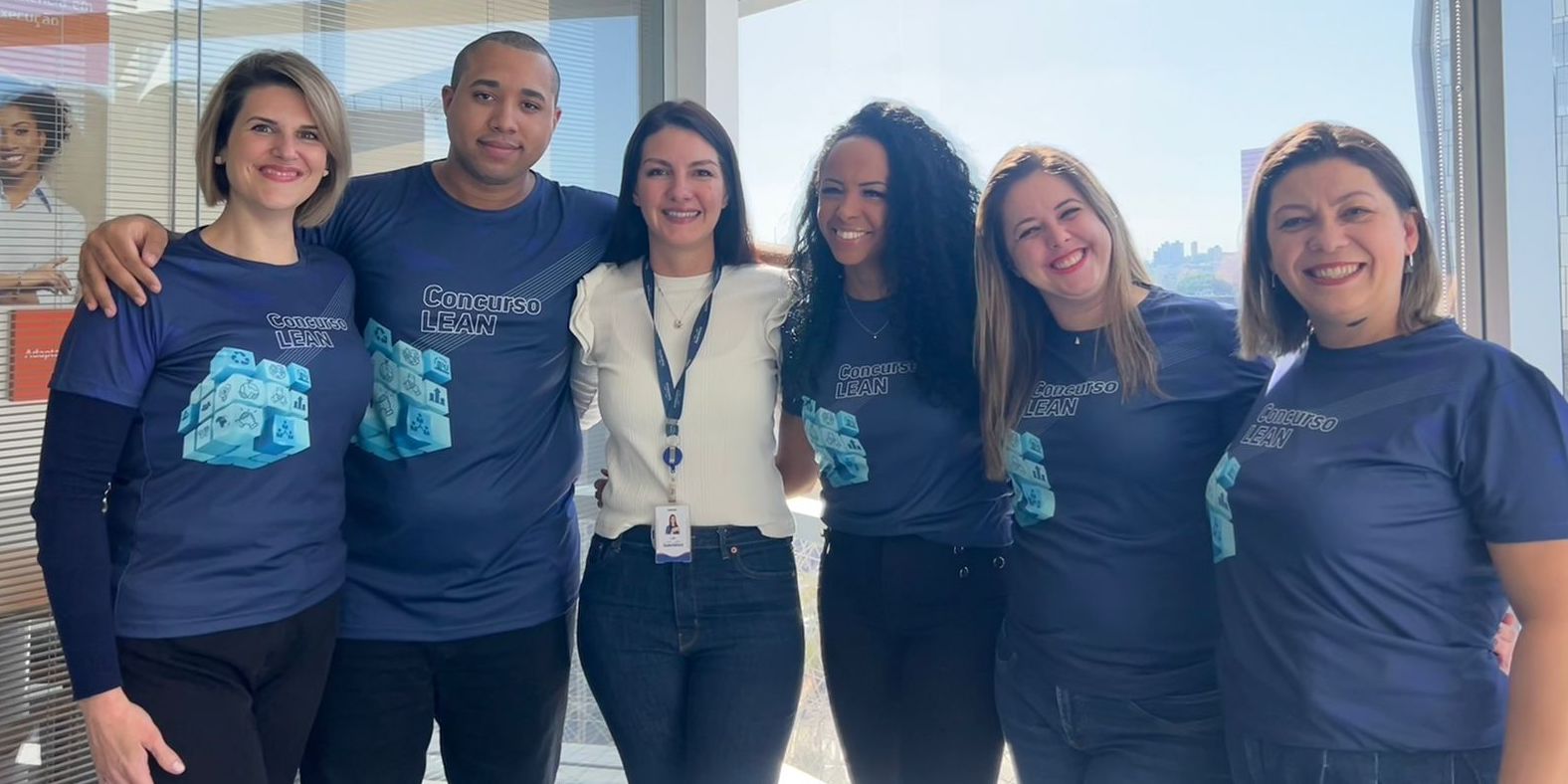
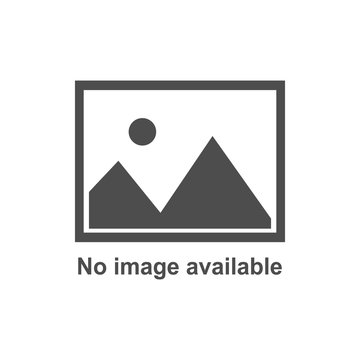
CASE STUDY – The transfer of a patient from one care setting to another is a delicate time. Insurance company SulAmérica has used its extensive lean experience to improve transitional care, and here’s how they did it.
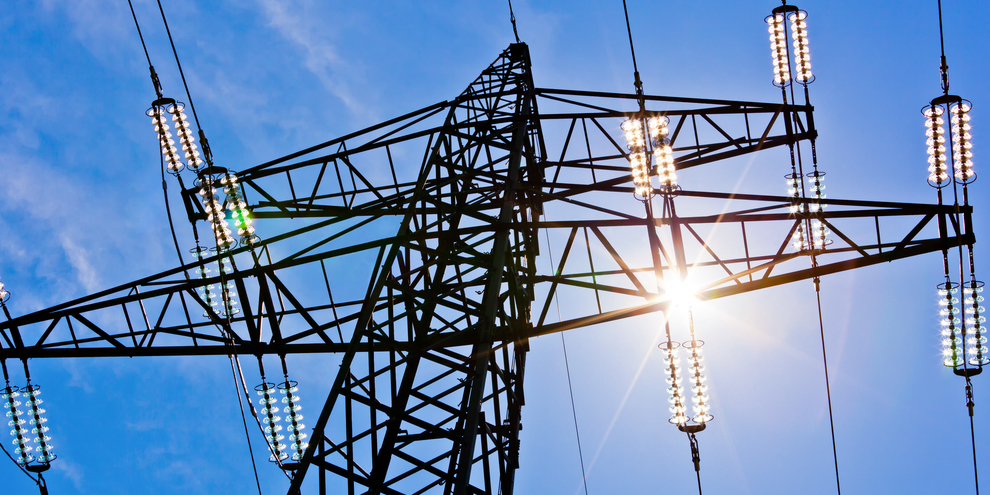
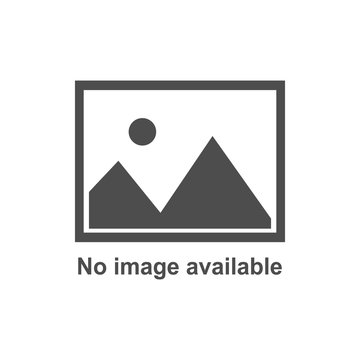
INTERVIEW – A VP at energy company E.ON shares his thoughts on the current energy crisis and discusses how lean is helping them to navigate it.
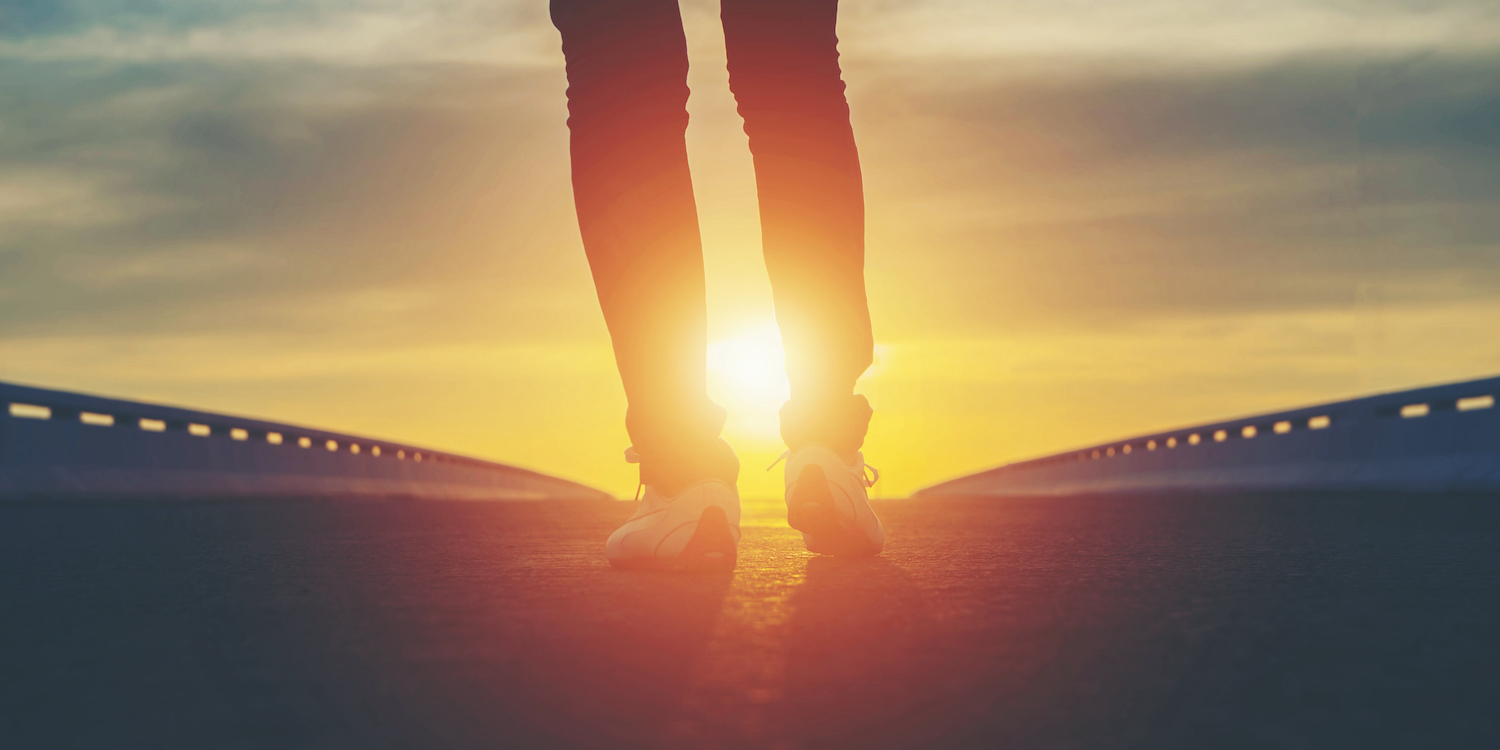
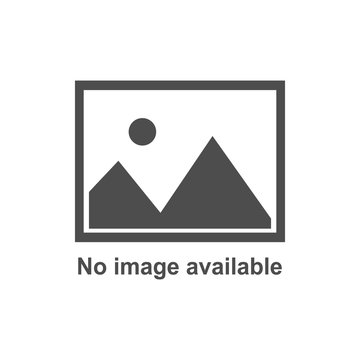
FEATURE – Can lean relieve some of the pain and fear people experience in this crazy world? It can, says the author, because amid so much noise lean carries one truth.
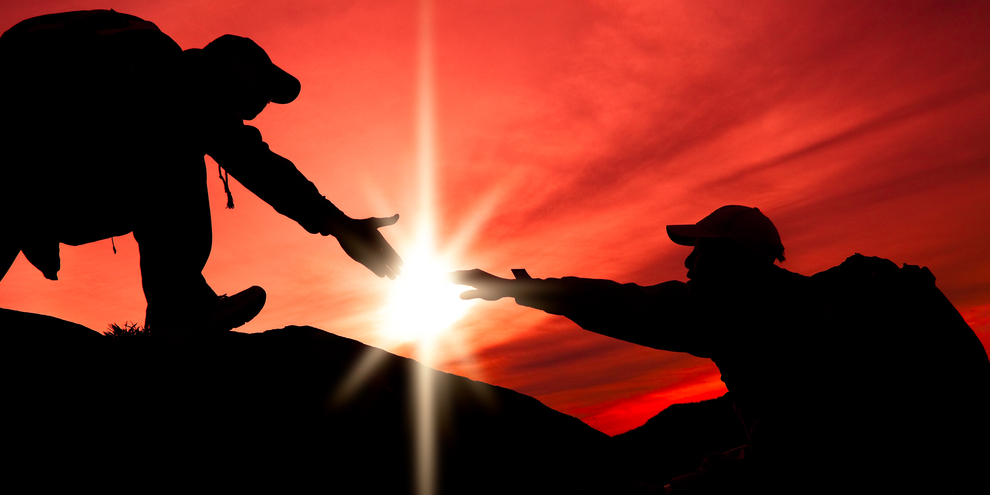
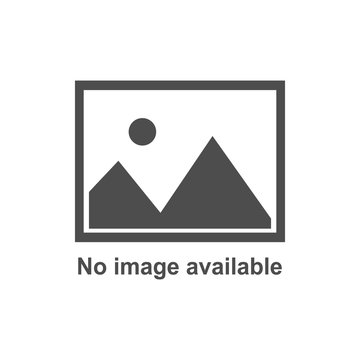
FEATURE – Our disposition towards learning changes depending on the amount of things we don’t know. The author explores this topic and the role of the sensei in enabling learning.
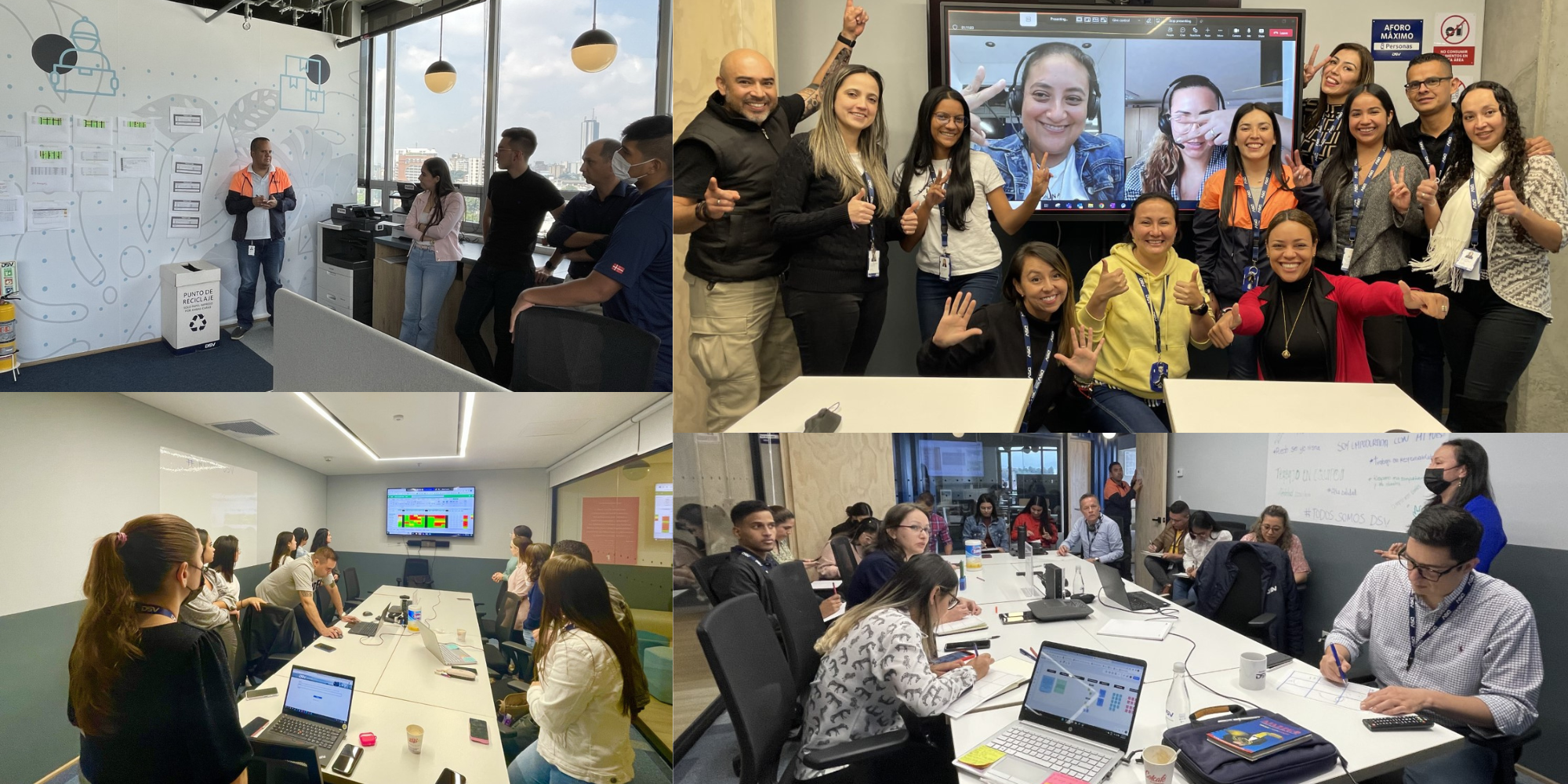
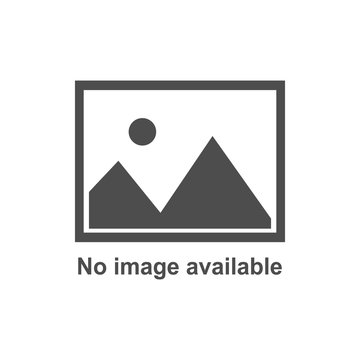
CASE STUDY – This transport and logistics company in Colombia has turned to Lean Thinking to become more adaptive and ensure an easier post-acquisition integration of new cultures.
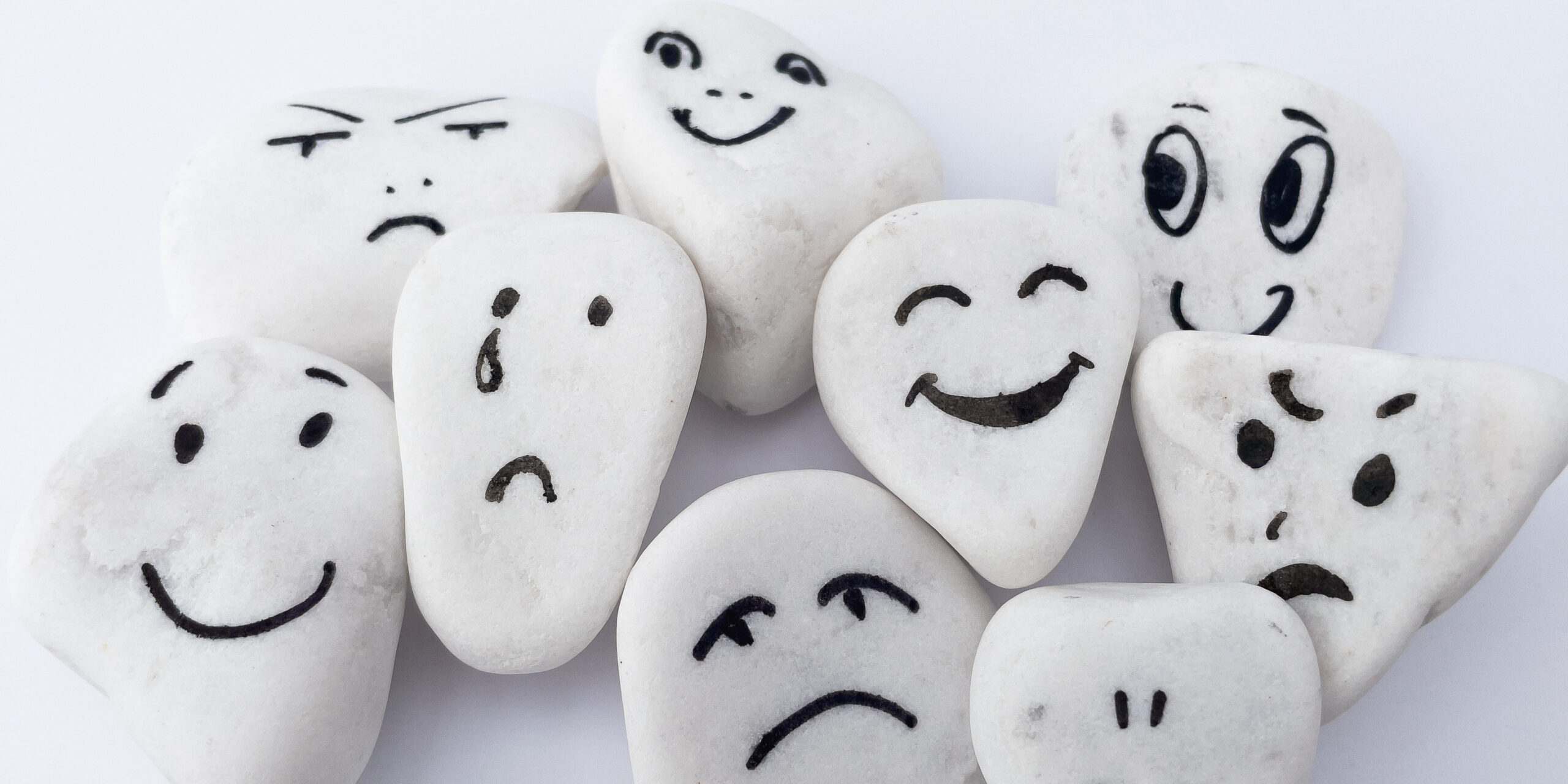
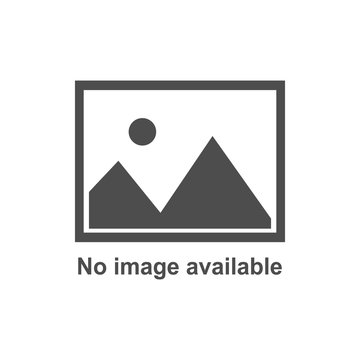
FEATURE – They say lean is all about people, and yet emotions – something we all feel and express daily – are largely absent from the lean discourse. The authors discuss the role they play in a lean transformation.
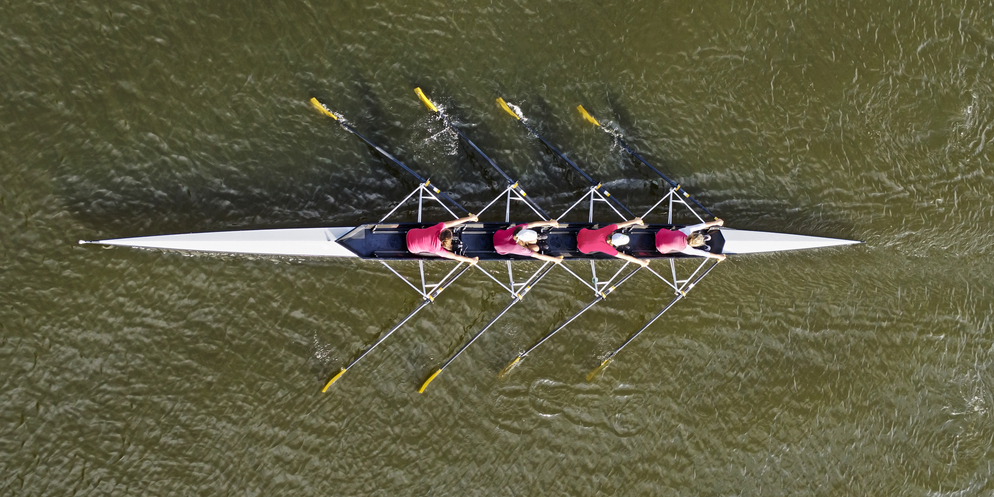
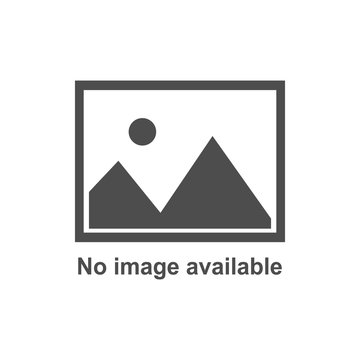
ROUND-UP – Standardized work, which lies at the foundation of the TPS house, is a necessary component of a lean transformation. This article looks at the best content on this topic from our archives.
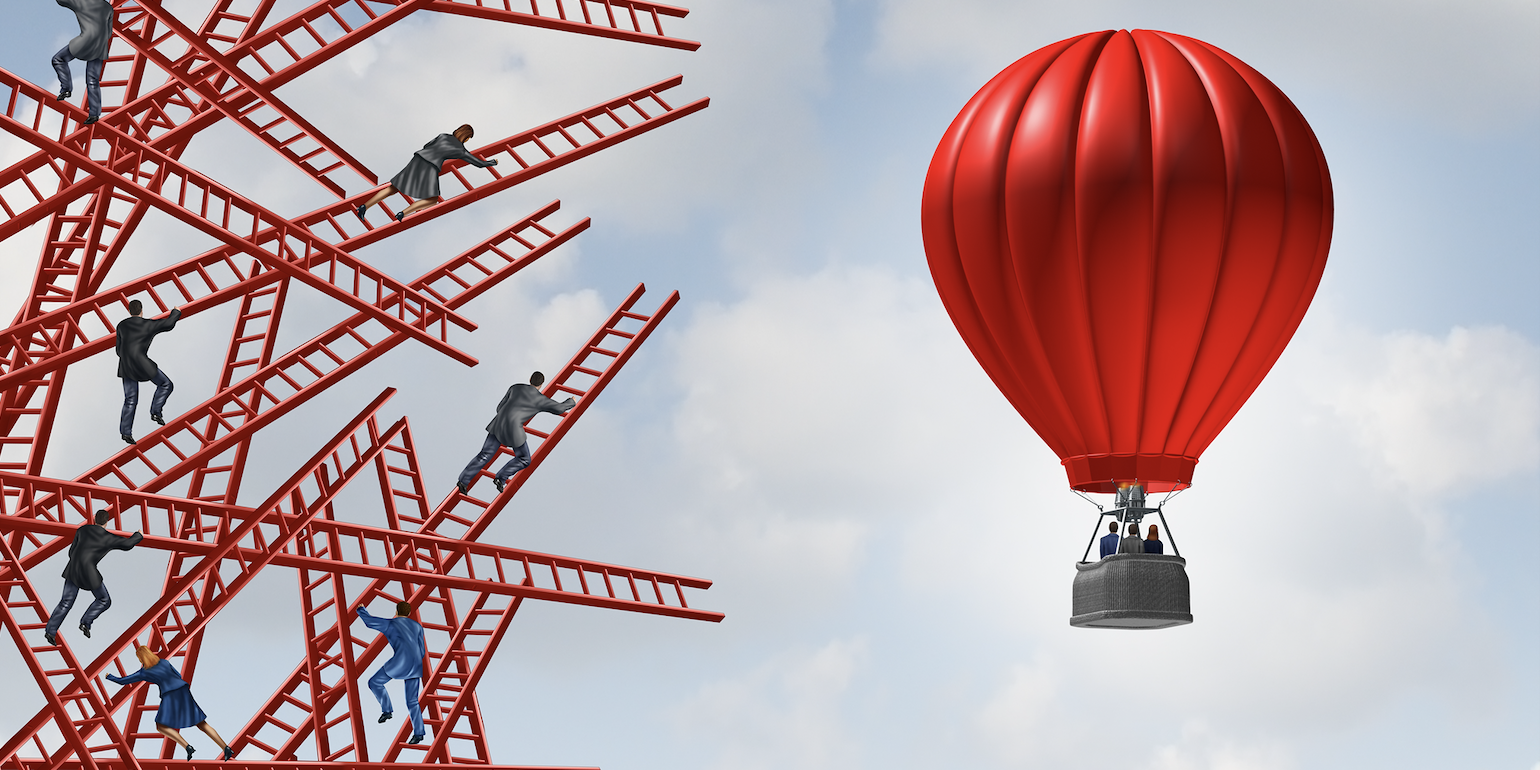
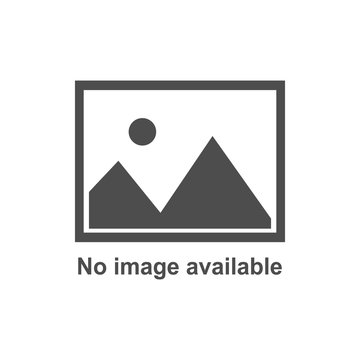
FEATURE – A former plant manager reflects on his experience supporting a team with the implementation of Kata in the daily management system and explains why, when it comes to Kata questions, simple is best.